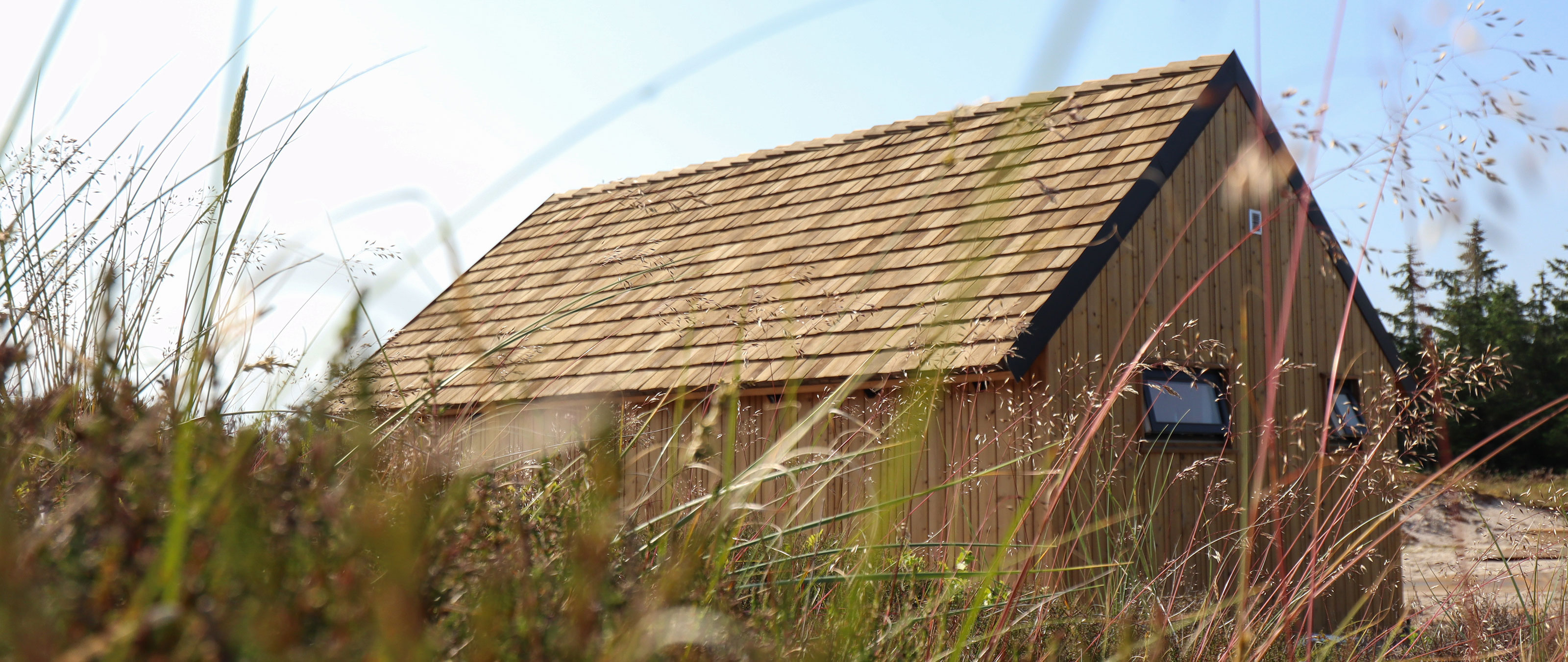
The construction industry—subject to strict energy efficiency regulations—is seen as a key player in this transition. Timber construction in particular, which holds great potential in the country, is gaining increasing importance. This is exemplified by pioneer CM Byg. With its ambitious environmental policy plans, Denmark is once again tightening climate requirements for the construction industry starting in 2025. As of July 1st, new buildings must comply with CO2e limits, which have been reduced to an average of 7.1 kg CO2e/m²/year. These requirements will affect every aspect of the construction process and will also apply to a broader range of building types than before. For example, the regulations will now also cover unheated buildings above a certain size, as well as extensions to residential and office buildings. At the same time, the lowered CO2e threshold makes it more important than ever to use sustainable materials and methods. Notably, the construction process itself—including transport, material waste and on-site energy consumption—is now factored into the building's overall climate impact.
A construction industry rethinking its approach
Unlike other Scandinavian countries such as Norway or Sweden, where timber construction has traditionally accounted for more than 90 percent of buildings, Denmark’s share has historically remained in the single digits. This has been the case in both the private and public sectors. For centuries, clinker brick construction dominated the country’s building tradition, and this influence continues to shape today’s practices. In recent years, public sector projects have also increasingly relied on concrete construction. Both methods are known for their high energy consumption. In recent years, political initiatives have already forced construction companies to increasingly question the use of CO2-intensive building materials. The requirement for developers of hospitals, schools, kindergartens, and administrative buildings to present a full carbon footprint of all materials used has prompted parts of Denmark’s concrete industry to reconsider their approach. Suddenly, due to their poor environmental footprint, many of their traditional business models were no longer viable for the future.
A surge in timber construction forecasted
Several companies that had previously specialized exclusively in concrete elements are now shifting toward hybrid construction methods. While they continue to use concrete for building cores—such as floors, stairwells and elevator shafts—they are now enclosing structures with prefabricated timber elements. The result is buildings that, visually, appear to be made of wood. “I’m convinced that this hybrid construction method will become standard in Denmark, especially for public buildings,” emphasizes Tobias Knölker, Senior Sales Manager at WEINMANN. This trend is reflected in the gradually increasing share of timber construction. “At the moment, the figure stands at 7 percent.” Changes to Danish legislation, set to take effect in 2025, will require private homebuilders to provide a carbon footprint for their projects—a development expected to further boost the growth of timber construction. A drastic reduction in CO2 limits is also anticipated. “Ultimately, the share of timber construction will rise significantly,” says Knölker with confidence. “Market analyses have repeatedly shown that it will increase considerably, driven by new legislation.”
Taking part in the future of timber construction
In response to these developments, WEINMANN is already collaborating with traditional precast concrete manufacturers, and of course, also with timber construction companies of all sizes. Across both the construction industry and the skilled trades, there are now projects being carried out using WEINMANN technology. One example is CM Byg, a timber construction firm based in Ribe, which has been active since 2012 and specializes in row houses and commercial buildings. CM Byg’s Managing Director Jesper Christensen also sees growing interest in timber construction across Denmark: “Many of our clients expect solutions that comply with the new building regulations. Timber is an excellent choice for that. By integrating our timber elements into hybrid buildings, for example, we can help significantly improve the overall environmental footprint of a project.” Based on such developments, he is confident that “timber construction has a bright future.” And the fact that his company is well-positioned to be part of that future is, in his view, directly linked to the investment CM Byg made in WEINMANN solutions in 2023. “These machines have completely optimized our production processes,” says Christensen. “Where we previously relied on manual processes, we can now meet the market’s demands for quality, speed and cost-efficiency far more effectively.”
A thoroughly reliable business partner
CM Byg successfully implemented this transformation using a BEAMTEQ series carpentry machine and a compact wall production setup, configured as a two-table solution consisting of two BUILDTEQ A-300 assembly tables (for longitudinal-crosswise flipping) and a WALLTEQ series multifunction bridge. The BEAMTEQ is designed as a cutting saw with an integrated milling system, tailored for wall cutting, beam processing and the fabrication of nail plate trusses. This allows for the fully automated production of notches, lap joints and mortise-and-tenon connections. Once the elements are laid on the assembly tables, CM Byg can now use the multifunction bridge to automatically fasten sheathing panels and cut any required openings for doors, windows and electrical outlets. “With ten employees in production and another 35 on the construction site, we’re now able to complete up to 400 m² of living space per day, which significantly shortens the construction process compared to conventional methods,” explains Christensen. Such results, he adds, would not have been possible without the partnership with HOMAG Danmark and WEINMANN. “We’ve come to know HOMAG Danmark and WEINMANN as thoroughly reliable business partners who not only provided us with the right machines, but also ensured the systems were seamlessly integrated into our production process. Today, we can respond to customer needs much faster and deliver high-quality products.”
Serving market segments with flexibility
The primary goal for CM Byg is to produce three different element types as cost-effectively as possible in the future. “On a typical day, we aim to manufacture 80 m² of wall elements, plus another 60 to 80 m² of ceiling and floor panels,” says Christensen. In addition to element production, CM Byg’s range of services extends from drafting support for architects to planning, structural calculations and full building construction. For the construction phase, the company will continue to focus on hybrid buildings, as well as row houses and commercial properties. The WEINMANN systems offer the level of flexibility required to support this approach. Christensen views the entire EU as a potential market, although there are differences in execution across regions. For example, in Scandinavian countries including Denmark, timber façades and wood-aluminum windows are commonly used, whereas in Germany, engineered wood products and PVC windows are more typical.
The right technology for the right product
Thanks to the WEINMANN systems, CM Byg has significantly increased both its level of planning and prefabrication. Whereas it was once common for walls to be modified on-site, they are now typically fully finished and ready for installation. This reduces on-site workload and, importantly, shortens the assembly process. At the same time, CNC processing has greatly improved the precision of building components. While manual production used to result in tolerances of 2, 3 or even 5 millimeters, today, “everything fits, and the quality is much better,” emphasizes Christensen. Another major improvement is that CM Byg is now able to manufacture larger elements. “Overall, we’ve increased our production capacity by 40%, which means we build faster, larger and better.” So it’s no surprise that CM Byg is confident they made the right investment. “We’re extremely satisfied—not just with the machines, but also with the installation, training and service. All in all, we’re using the right technology for the right product.”
Taking on a pioneering role
Against the backdrop of the Danish government’s upcoming tightening of CO2e limits in 2025, a stronger shift toward sustainable construction is being actively encouraged. This opens the door for timber to play a pioneering role in the building sector. There is no need for stakeholders to wait for the development of the necessary technologies — they already exist. The next projects can begin now.
An article from the performance customer magazine 2025. Read more.
“These machines have completely optimized our production processes. Where we previously relied on manual processes, we can now meet the market's demands for quality, speed and cost-efficiency far more effectively.”Jesper Christensen, Managing Director CM Byg
CM Byg
CM Byg is a Danish company specializing in timber construction and has been in business since 2012. It specializes particularly in terraced houses and office buildings and uses modern technologies from WEINMANN to optimize its production processes. Using timber elements in hybrid buildings helps to reduce the overall environmental footprint of projects. The company is a pioneer in the increased use of wood in the Danish construction sector and plans to offer its services to the wider EU market, too.
Learn more about the company