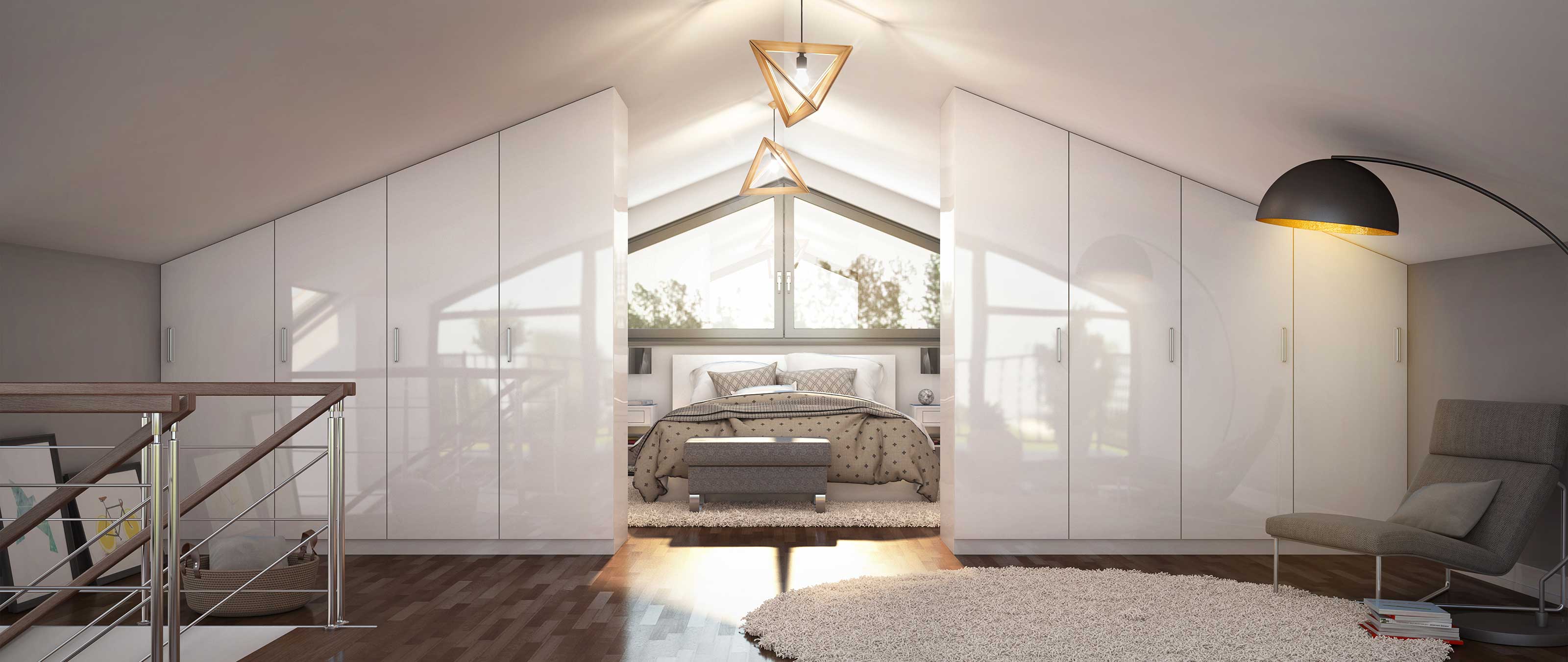
Furniture manufacturer deinSchrank.de is synonymous with high-quality, custom-made furniture that can be configured online by the consumer. Today, the company's production facility combines the TRANSBOT automated guided vehicle system from HOMAG with flexible automated cells, some of which are equipped with robotics. The scalable system opens up brand new possibilities for networking systems and provides the necessary flexibility for further development in the future.
Furniture that is precise down to the millimeter, complete individuality, and an online configurator that is incredibly easy to use: With this business model, deinSchrank.de produces custom-made furniture that is not only unique, but is also a perfect fit — even with a pitched roof.
Usually, you would visit a furniture store or online portal to browse for furniture. The selection is huge, but individuality in every detail is the exception rather than the rule. Anyone wanting to turn all of their ideas into a reality goes to a carpenter, and has furniture custom-made according to their requirements. This is exactly where the solution from deinSchrank.de comes in.
deinSchrank.de is the German e-commerce pioneer for custom-made furniture. The key to the company's success is an online configurator with a 3D view. This configurator allows customers to effortlessly customize their own unique piece of furniture from the comfort of their own home — down to the last millimeter.
Individuality in line with the guiding principles of Industry 4.0
The former start-up has now been around for nine years. For the last three years, deinSchrank.de has been producing its own furniture in Rheinbach—just south of Cologne—and its production has grown steadily from there. Starting with just a group of individual machines, the machinery has gradually expanded. Today, deinSchrank.de is a production company that operates with the highest level of flexibility and produces unique systems and machines in batch size 1 according to the guiding principles of Industry 4.0.
Andreas Heinzmann, Professor at Technischen Hochschule Rosenheim (Rosenheim Technical University of Applied Sciences) and member of the advisory board of deinSchrank.de: "We are a highly flexible production company, and we place a very strong focus on the current market. This also means that, today, we don't know which products we will be producing tomorrow, the day after tomorrow, or in two years' time. Thanks to the flexibility in our production concept, we can easily adapt our production logic to the latest requirements, and we are in a position to satisfy customer-specific requests both today and in the future."
Ample flexibility thanks to a variable production concept
On the road to ensuring flexible production—something that is now consistent throughout the entire production process at deinSchrank.de—the question of an intralogistic link between the operating cells needed to be addressed, since material transport between the automated cells was still carried out manually. It was not uncommon for employees on the machines or downstream operating cells to be waiting for material due to the operator being busy with logistics. It was therefore only logical to look for a solution that enabled independently operating cells to be connected together in such a way that created an automated, variably adjustable production concept.
With the conventional interlinking of the various systems, the intralogistics could also retrospectively take a step towards overall batch size 1 production. As a rule, modifications are then made to existing machines and, if necessary, adjustments are made to position of the machines in relation to one another in order to create space for automation. But this was about much more. Firstly, modifications should be avoided so as not to disrupt production and, on top of that, further changes should also be implemented retrospectively for future operations. The solution for deinSchrank.de was provided by HOMAG and their automated guided vehicle system (AGV), called TRANSBOT.
Maximilian Held, Product Management, HOMAG: "With our driverless transport systems, we are breaking new ground that has not yet been explored in this way. Our aim is to create solutions that make life easier for the industry."
TRANSBOTs connect individual processing machines, automated cells, or even manual workstations together logistically. The self-driving transport robot navigates freely through any space, without the need for mechanical aids such as rails. This is precisely what makes them so flexible when handling logistics tasks. In addition, if changes are made in the production process—due to the implementation of new machines, for example—the TRANSBOT travel paths in fleet management can be effortlessly adapted to the new conditions. The combination of TRANSBOT and fleet management is comparable to the interaction found in self-driving cars that chart your journey with the aid of a navigation system and sensors.
Prof. Andreas Heinzmann: "In production, we use highly flexible, automated cells, some of which are equipped with robotics. We want to think bigger when it comes to cells. We want to think bigger when it comes to units. And the transport robot from HOMAG is the perfect match for our philosophy of flexible production. This is the main reason why we put our faith in HOMAG and opted for this system. To stay flexible, but also to forge ahead with automation in a scalable system."
High level of added value thanks to the right intralogistics
Since July 2018, the TRANSBOTs have been in use at deinSchrank.de, linking the production stages of CNC processing and edging — both in closed, automated operating cells. Once the processing of a material in a production step is finished, the material is stacked on table-like structures known as trays. At deinSchrank.de, these stacking routines are completed by various robots that are integrated in the cells. Once a stack is complete, a TRANSBOT moves underneath the tray, lifts it, and transports the stack out of the machine. It then takes the stack directly to the machine on which the plates are to be processed further or to an automated surface buffer between the processing steps, which is realized by the TRANSBOTs. Even at the next machine, the stack is fed in for further processing—plate by plate—by a robot. The position of the machines or operating cells in relation to one another only plays a secondary role from the perspective of the TRANSBOT. There is no rigid interlinking of plants. As such, it makes no difference where the machines are located in the production hall.
The changes brought about by the new logistics solution are clearly noticeable, Andreas Heinzmann explains: "The machines can now provide real added value, as we are able to separate our logistics from our direct machine operation thanks to the driverless transport system."
Questions such as "How can the various cycle outputs of processing centers be matched?" and "How can the required flexibility for logistics in case of changes to orders be incorporated?" were easily answered. In production at deinSchrank.de, these questions are resolved with a buffer station located in an area between the production steps. With 20 spaces—each accessed individually—empty trays can be set aside and full trays can be stored ready for use until the material is needed. This means that processing centers can be continuously supplied with material whilst operating with a high level of added value, and production planning can be flexibly adjusted in response to order changes.
Modular, scalable, and flexible
As you might expect, when implementing the system of driverless transport vehicles in the production environment at deinSchrank.de, it was necessary to address tasks relating to the software. Travel orders had to be generated, order data had to be managed, and additional data had to be provided. These matters were easily resolved in collaboration with HOMAG Software, as machines are not isolated from one another at HOMAG, but considered as a whole. With the ControllerMES manufacturing execution system, HOMAG has integrated a platform that optimally organizes the production processes and perfects the interaction of machines and manual work stations at deinSchrank.de. The modular system supports the processes at deinSchrank.de — from intelligent configuration and optimization of the production data, to the production planning and ultimately the completeness check after final assembly.
The workflow sounds incredibly simple. Data records are generated via the Internet platform deinSchrank.de and are then adapted to the production requirements in the work preparation. Production orders containing all the required component data are created and then distributed to the production machines.
Prof. Andreas Heinzmann: "Our collaboration with HOMAG has been a huge success — from the outset to the acquisition phase, right through to the service we are currently receiving. When I consider the entire production journey, including the way in which the AGV communicates with the robot cells, how the exchange is, and how the buffer management works—and by that, I mean not only that we maintain our flexibility but are also able to generate a high level of automation—these expectations have absolutely been fulfilled. We are extremely satisfied, and would choose intralogistics from HOMAG again."
The driverless transport system represents automation that is free from rigid interlinking or rigid systems. Thanks to TRANSBOT, deinSchrank.de can now navigate its production path from machine A to machine B, and then proceed to a completely different machine the next day. The scalable system opens up brand new possibilities for networking systems and provides the necessary flexibility for further development in the future.
Videos
Please confirm that when you use YouTube, data such as your IP address, browser identifier and similar may be transmitted to Google.
» Privacy Policy
The TRANSBOT automated guided vehicle system opens up brand new possibilities for networking systems and provides the necessary flexibility for further development in the future.
“The machines can now provide real added value, as we are able to separate our logistics from our direct machine operation thanks to the driverless transport system.”Andreas Heinzmann, Professor at Rosenheim University and member of the advisory board at deinSchrank.de
More about deinSchrank.de
deinSchrank.de is the German e-commerce pioneer for custom-made furniture. The key to the company's success is an online configurator with a 3D view. This configurator allows customers to effortlessly customize their own unique piece of furniture from the comfort of their own home — down to the last millimeter.
deinSchrank.de