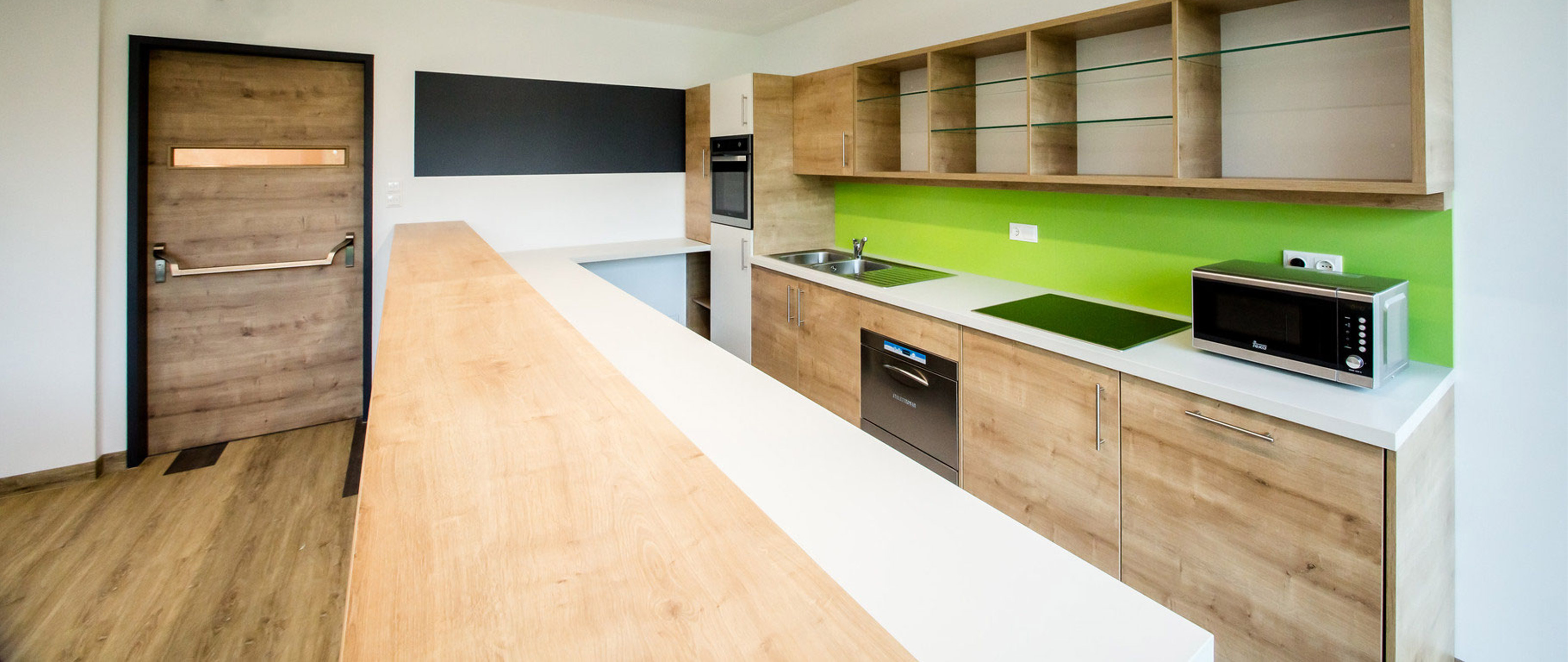
Automated guided vehicles are predestined to flexibly automate material movements within production. However, what must be considered in an AGV factory planning? For example, how do load transfer stations for automated guided vehicles in the furniture industry have to be designed to be capacity-preserving? SCHULER Consulting developed the complete manufacturing concept of Kitzberger Möbel GmbH.
Located in Upper Austria, the family-owned company Kitzberger specializes in furnishing projects. With over 50 years of experience, their main focus is on large-scale projects in the field of interior design of student and senior citizen residences. In order to meet the increasing work demand, the company was looking for flexible, fully automatic solutions and therefore became aware of HOMAG's autonomous cell at the Holz-Handwerk 2018 and thus the automated guided vehicle topic. After an intensive exchange, it quickly became clear that in the already planned production restructuring, intralogistics should also be equipped with new and innovative technologies.
Together with SCHULER Consulting they discussed the exact purpose. Because of the shortage of skilled workers, it was important to Kitzberger to increase the degree of automation and to transform the production into a smart factory. The material flow should therefore be realized by automated guided vehicle's after the fully automatic robot-cutting saw and should also cover all subsequent production processes. From fully automatic loading and unloading of the machines to a semi-automated assembly line with through feed case clamp. The highly innovative project was "born" and in a relatively short period, the experience of the company Kitzberger has created significant momentum for the application of automated guided vehicles in the industry.
The only industry-specific solution on the market today for automated guided vehicle was offered by HOMAG, including a linked stack management system, eliminating the decision-making process that is normally the case with established technology concepts. For the generation of transport orders, as is the case with all modern AGV’s, as well as automated production, a digital sub frame in the form of a manufacturing execution system (MES) is necessary. Since such a system was not yet in place at Kitzberger, SCHULER Consulting developed the required functions so that an optimal system selection and subsequent configuration could be carried out. Often, there is a need for additional clarification in the project due to insufficient knowledge of the process and data quality. Since the company Kitzberger has configured and used the existing ERP and CAD|CAM system very well, this was not an issue.
Also in the choice of part carriers, the current selection in the industry is still relatively limited. Fundamentally it started with the 1x1-stack, which meant that the parts could only be stacked on top of each other (bigger parts on the bottom and smaller parts on top, to maintain stack stability). Here the first number indicates how many parts can be stacked behind each other and the second number indicates how many parts can be stacked beside to each other. A good example can be found in the series production where automatic part infeed can make use of uniform part stacks that are stacked as for example 4x2-stacks (four parts behind each other and two parts beside to each other). However, due to small batches and changing part sizes it made sense to develop chaotic stacking possibilities instead. These chaotic stacks are defined with the help of an algorithm which creates stacking possibilities based on given parameters. After the chaotic stacks the order picking trolleys came into discussion to maintain access of individual parts (instead of stacking them on top of each other).
Since the TRANSBOT is a “pick-up” vehicle, it is required to move so-called trays from place to place. These trays consist of metal racks with for example a pallet in them, the TRANSBOT is then able to drive underneath the tray, pick it up and transport it to the required location. Due to the different characteristics of the load carriers and stack types, it was decided to transport A parts as 1x1-stacks, while C parts from the saw to the edge banding machine were transported as chaotic stacks. Thanks to the stacking algorithm integrated into the robot saw, the creation of transportable stacks was possible without any possible filling parts. An analysis of the production processes showed that C-parts receive different processing steps after edging and thus the further transport ideally takes place in picking trolleys. These picking trolleys will make it easier to pick parts for individual processing without having to relocate other parts and still keep work pieces together throughout the production process.
An essential element in the organization of automated guided vehicles logistics is the batch formation, in most cases it can be seen that these are incompatible with the previously selected stacking systems. At Kitzberger, different cutting optimization concepts were created and simulated for the new batching. This way, after a few runs, the batches could be formed in such a way that the stacks did not become too big. In addition, the efficient cutting results ensured that the existing stacking stations were still sufficient.
The stacking stations necessitated another solution finding for the load transfer from the robot saw. The situation was as follows: The robot mounted on the saw handles both the material handling for cutting and the stacking on the available stations. A lifting table for the stacking stations ensures that the robot can always remove the work pieces at the same height. Since a TRANSBOT was not able to drive on this lift table, due to its chassis, it was therefore necessary to find an alternative solution. Finally, the variant of a system-compatible forklift TRANSBOT proved to be the best choice. This forklift TRANSBOT is located exclusively in the cutting cell and conveys the finished stack including pallet to a transfer station.
After all machines and load transfer stations have been defined and arranged in the layout, it was necessary to design the route network. The design was carried out in accordance with DIN (Deutsches Institut für Normung, German work standard) and VDI (Verein Deutscher Ingenieure, German technical and scientific association) specifications. According to this, automated guided vehicles paths are always based on the largest work piece to be transported plus an additional 50 cm safety distance from the edge. In addition, there needs to be enough space for the automated guided vehicles to make a full rotation. The paths therefore had to be arranged cleverly so that not too much space was assigned to the AGV logistics. Likewise, alternative routes and sufficient number of vehicle charging stations were to be taken into account. Once the required buffer spaces between the machines had been calculated and arranged in the layout, the design of the automated guided vehicle solution for Kitzberger was completed.
As already mentioned, the now planned, fully automated production can only function if a correspondingly innovative manufacturing execution system (MES) supplies it with the right data at the right time. An essential advantage of the selected AGV system TRANSBOT is the integrated stacking management system called “woodStack”.
Due to the connection to the MES an exact part tracking during the production is possible in the future. Search times can this way be reduced to an absolute minimum.
The current implementation of the concept is divided into three sub-steps. At present, the entire production for the new logistics concept is gradually being changed and the infrastructure of the automated guided vehicles installed. Subsequently, the first test drives with the automated vehicles will then be carried out in individual areas and maps for the orientation of the vehicles will be recorded. In the third phase, the AGV can then take up operation throughout the entire production without any problem.
Kitzberger Möbel GmbH and SCHULER Consulting have developed the automated guided vehicles technology for the industry from the cradle within a very short time and the company is on the best way to fully utilize it in its entire production over the next few months. Only by focusing on this goal and the clear ideas of the company Kitzberger regarding their own Smart Factory could such a broad and detailed task be made. This makes the company from Austria an absolute pioneer and can confidently look to the future when it comes to producing project furnishings efficiently and with the latest technology.