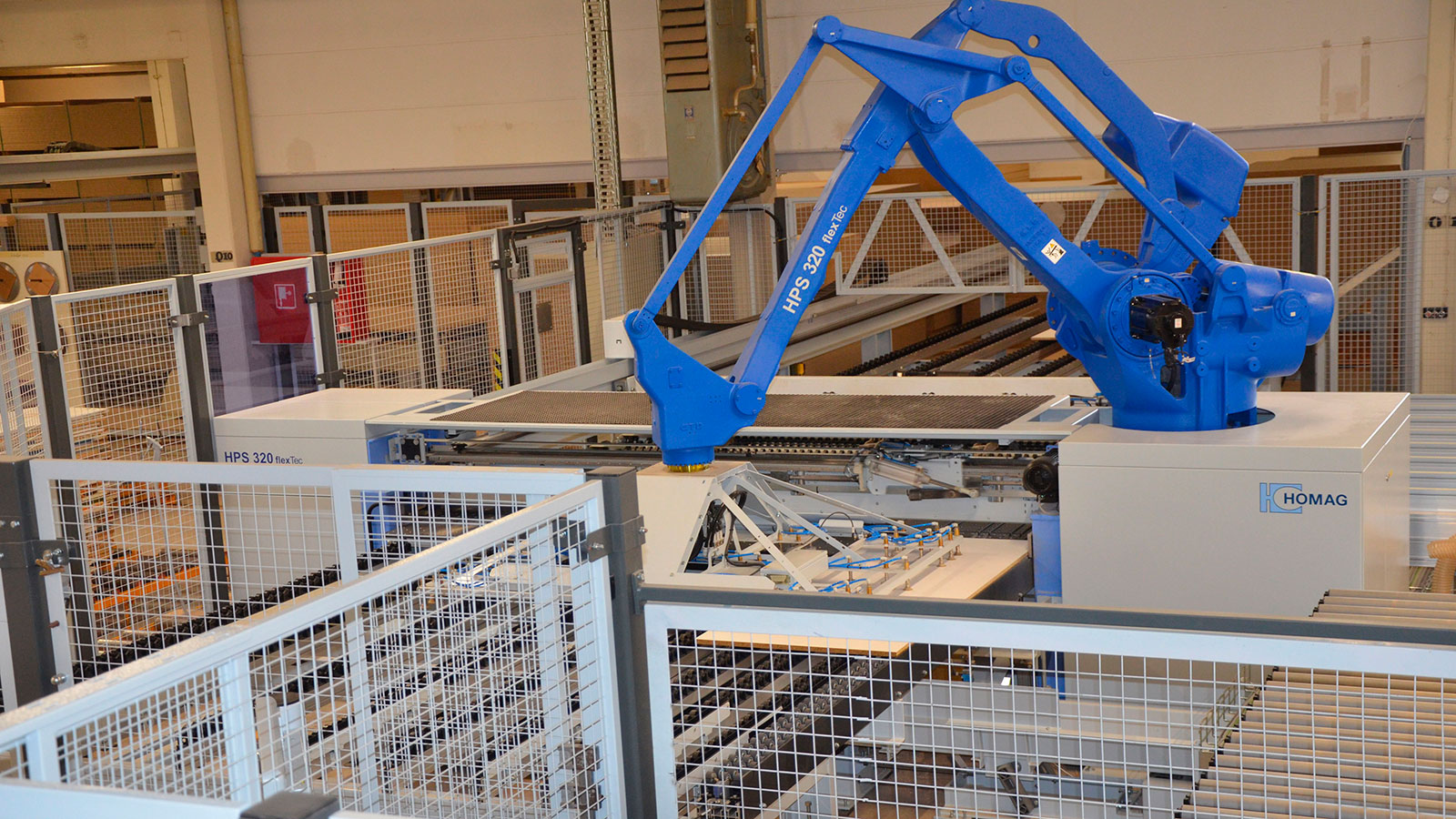
Here's something you don't see every day: The Rudolf furniture factory relies on the latest technology to create an almost perfect flow of materials over an area of 10,000 m². The HOMAG SAWTEQ B-320 flexTec robot-saw cell, which was specially developed for cutting individual panels and boasts highly efficient, fully automatic processes, is a key component in this state-of-the-art system. But this is by no means all that the Hesse-based company's machine pool has to offer.
By Norbert Schmidt
"Our material flow is in no way perfect," admits Karl Friedrich Rudolf, Managing Director of the Rudolf furniture factory. "With the help of external support, we've tried to make sure the hardware – that is, the machines – are positioned optimally according to our objectives. But we'll only have a perfect system once the data flow is also functioning properly." And the company is currently working under high pressure to get this in place. Karl Friedrich Rudolf explains: "We're currently in the practicing phase." He believes they are headed in the right direction, albeit a gradual journey. And he is putting his trust in HOMAG machines to help the company avoid interface problems. But Karl Friedrich Rudolf cannot avoid market demand, which has seen considerable increase: "We used to fulfill 300 individual customer requests. Now we're having to process more than 3000 in order to remain competitive."
The Rudolf furniture factory produces furniture for children's rooms, apartments, home offices and cloakrooms and has become a well-established name in these niche sectors. The company offers several hundred million variants of fold-away beds for apartments. Rudolf produces the 10,000 parts itself in a fully integrated production process, and even has its own paint shop. So it's no wonder that management at Rudolf were looking at batch size 1 production as early as 20 years ago. But the manual effort was significant – there were lots of intermediate storage facilities, and too often parts could not be located and had to be reproduced at great expense. It was also becoming clear that purchasing unprocessed parts in fixed quantities was not economical due to the excess quantity of offcuts that could not be used.
This meant the company needed its own cutting facility. In 2010, the company installed an automatic panel storage system with a downstream HOMAG HKL 380 angular saw unit (now SAWTEQ B-300) for cutting. A HPP 200 pressure beam saw with manual feed (now SAWTEQ B-200) was also installed for batch size 1 cutting. This saw is still being used today for express jobs and is referred to internally as the Ferrari saw. Lignum Consulting was brought in to ensure the company was optimally set up for future requirements, and it quickly became clear that the company needed more automation and greater flexibility. "All parts must be produced in the correct order – from cutting to loading them into the truck," states Karl Friedrich Rudolf, describing the company's requirements. This required hardware and software to be optimally suited to the various processes.
The SAWTEQ B-320 flexTec gave Rudolf a cutting cell specially designed for cutting individual panels, which offered highly efficient, fully automatic processes. Thanks to the use of a robot, panels can be cut longitudinally and transversely with just one saw in a fully automatic process. This also requires less space, since only one saw body, one program fence, one machine table and one waste removal system are required. Extra-thin saw blades increase material yield while reducing energy consumption. A modern suction device with innovative dustEx technology for collecting chips directly at the cutting line is also incredibly beneficial to the company.
The robot moves the panels using gentle vacuum technology. Production stoppages are virtually ruled out thanks to the tried-and-tested industrial robot, achieving almost 100 percent availability. What's more, the error rate is extremely low. The pressure beam printer labels all parts automatically, directly where they are made. The labels contain all the information required for subsequent processing steps. With an output of up to 1500 parts per shift, the unit costs in batch size 1 production are significantly reduced.
Those responsible for production in the furniture factory allowed plenty of time – two and a half years – to comfortably plan and finalize their ideal batch size 1 production system. During this process, in addition to the saw, they decided to invest in a KFR 610 formatting and edge banding machine with automatic part return (now EDGETEQ S-800) with TFU 820 lifting cross rail (now LOOPTEQ C-500), which enables four-sided edging of parts. Today, this edge cell is connected to the robot saw, which supplies parts to the cell. The combination was implemented in fall 2018. In spring 2019, the Rudolf furniture factory took a further important step toward automated batch size 1 production and purchased a DRILLTEQ H-500 drilling unit. This unit drills all the required bore holes on an order-by-order basis.
"These machines form the basis for economical batch size 1 production," states Karl Friedrich Rudolf. "The software really rounds off the project." Here too, Rudolf has remained true to HOMAG and purchased ControllerMES. The company has been using the system since 2018 and it has already proven its worth in cutting and edging. "We are currently in the process of integrating the drilling units and assembly in the MES system."
The digitalization of the Rudolf furniture factory focuses on efficient production processes, optimal data quality and complete transparency. And for Karl Friedrich Rudolf, a perfect production process is not dependent on the size of the business. ControllerMES, the production control system from HOMAG Consulting and Software, enables an integrated information flow within production while offering the option of digitalized production planning and organization. The data is created in an upstream design software such as woodCAD/CAM and transferred to ControllerMES. This guarantees consistent data processing. Labels with barcodes, which are attached in a fully automated process during panel dividing on the saw, enable unique identification of every component, regardless of where it is in production. Furthermore, the machine data required is supplied to the relevant machine through the reading of barcodes. Waste is reduced thanks to flexible grouping of jobs in batch formation and seamless communication with the Cut Rite cutting optimization software.
Job progress can be monitored in ControllerMES throughout the entire production process. This means the operator can see clearly whether the individual furniture components are ready for assembly at a glance. And if a part has to be reproduced quickly, the predetermined logic in ControllerMES helps with this process. For Managing Director Karl Friedrich Rudolf, safety is vital during assembly. His "push-per-light" devices help ensure safety by showing which transport carriage a part supplied by the KFR 610 formatting and edge banding machine (now EDGETEQ S-800) via a spiked buffer must be deposited in.
Rudolf has invested a lot in efficient processes and wants to continue on this path consistently, because he knows that this is the only way to secure the future of his furniture factory.
“We used to fulfill 300 individual customer requests. Now we're having to process more than 3000 in order to remain competitive.”Karl Friedrich Rudolf, Managing Director of the Rudolf furniture factory