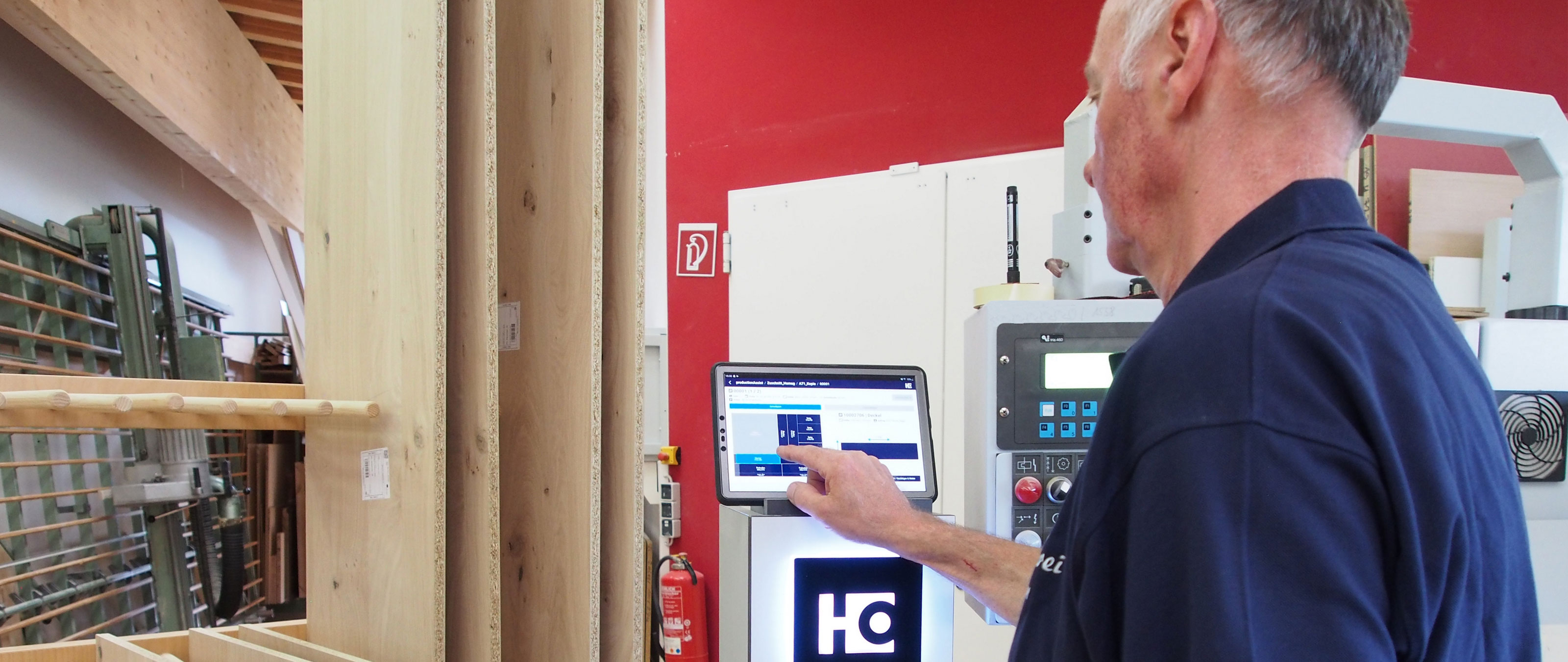
Together with an assistant, master joiner Fritz Strom produces furniture and interior fittings. On site, I discover the usual standard machines. I'm curious about what to expect, as the reason for my visit to the workshop is one that you wouldn't normally expect in such a business: digitalization.
Article from industry magazine BM, 08/2020 edition. Read the article in German on BM Online here.
Fritz Strom (59) tells me that, at its peak, the carpentry business that he founded in 1991 employed four people in the workshop. Today, the team consists of him, his wife Jutta and a carpenter's assistant. As you might imagine, the workshop is small – and has no fancy, high-tech machines. Instead, it contains very robust standard carpentry machines, some of which are even still covered in the green that I know from my days as an apprentice. There is also a compact vertical CNC, procured by Fritz Strom around five years ago, and an edgebanding machine; everything this carpentry business requires for processing panels, solid wood and veneer. The final surfaces are applied to the individual items of furniture and interior fittings in a small paint shop. "Panel processing makes up around two thirds of our work, but solid wood and veneer are still very important to our business," says Fritz Strom. He continues, "We don't participate in public tenders. Nearly all of the items we design and produce are for private customers."
"I'm certainly no PC freak"
We spoke about how his business has entered the world of digitalization. The friendly master joiner admits to me quite openly, "I'm certainly no PC freak. But my wife Jutta organizes the office and uses SketchUp to create very attractive 3D presentations and designs for our customers." Other than this widely known, cost-effective yet high-performance 3D design software, the carpentry business only used standard business programs until recently. The previous workflow was as follows: if the SketchUp presentation resulted in an order, Fritz Strom created the material list with pen and paper – a completely manual process. The necessary material was then ordered using gut instinct. "Using this method makes it so to order too many panels," he says that with a smile, as it doesn't happen to him anymore. The same applies to panel cutting, which is performed on a circular saw and an older, horizontal panel saw: previously Strom used gut instinct, now he uses a more accurate system.
"It piqued my curiosity"
Just over six months ago, Fritz Strom had discussions with HOMAG and his attention was drawn to a "project" that the global market leader from the Black Forest was about to introduce to the market for trade carpenters: digital assistants. The master joiner was so curious about this that he managed to be included in the select group of pilot users. His business matched the target audience that HOMAG wants to reach with these new products: small carpentry businesses that potentially use only standard machines for production but that should still reap the benefits from the possibilities that digitalization brings – fully grounded, with no complicated handling and very effective results. As a pilot user, Fritz Strom received exactly the digital assistant that he was hoping for: the cutting assistant, or to give it its official name, the Cutting Production Set.
Plug-and-play: Ready for operation in no time
Before he could start to use this digital aid, he installed the hardware components himself by connecting the core of the system, the HOMAG CUBE (an intelligent control box for connecting the label printer to the Internet and the apps – or, more simply, a small computer), to the LAN cable and printer – done. In addition to the printer, the starter set also includes two rolls of labels. To house the CUBE and the printer, the master joiner built himself a small, nifty shelf. "It was all very easy," comments Fritz Strom.
The cutting assistant gets the intelligence it requires from the software and the apps: intelliDivide Cutting (optimization software for cutting), productionAssist Cutting (assistant for manual cutting) and materialManager (for material management). The only thing that is required is to get started with these apps is a tapio account. It sounds complicated – but it isn't. The platform is actually quite a cool and clear cockpit for all applications used. Fritz Strom was able to master it too without any problems: The – let's remind ourselves – PC-phobic carpenter now has a good, up-to-date overview of his apps at all times. These are used on the PC in the office and on the tablet in the workshop.
Directly proven in practice
Once the master joiner had successfully got the setup on track without any notable hurdles, work could start. The new workflow is based on starting with the SketchUp planning – just like before. However, instead of pen and paper, Fritz Strom's planning tool is now the cutting optimization software intelliDivide Cutting. He transfers some of the data from SketchUp via a .csv import before entering the remaining data in the cutting optimization software. Once everything has been recorded, Fritz Strom starts the optimization. The system provides several recommendations to choose from – for example, with a focus on minimum waste, the shortest machine running time or the easiest handling. Panel offcuts are also taken into account. A welcome side effect is that Fritz Strom now knows exactly how much panel material he needs to order.
Then the app, which is online rather than PC-based, which saves file space on the computer and allows faster updating, starts working. Within a very short time, the cutting pattern is finished and is transferred to productionAssist Cutting. This supports the cutting process on a tablet in the workshop. There, Fritz Strom or his assistant select the cutting pattern for the first panel and can start work – on the Martin circular saw, for example.
The app intelligently guides the user through the sawing process. Once a part is finished, it is confirmed by touching the screen, the printer creates the label and the color of the part changes on the cutting pattern. The app then indicates which cut makes sense next. Each part therefore has its own individual label that contains all information as well as a barcode for the subsequent processing operations on the BHX and edgebanding machine.
A good start with further potential
Fritz Strom is very happy with the results so far: "Now, I only need half the time for the work preparation and material consumption has fallen significantly. Together, these two factors save us a lot of time and costs. And there are hardly any errors anymore."
However, the master joiner also knows that, although that was a very good "digital start," there is still plenty of scope for further optimization. For example: with an upstream "real" CAD system or cabinet generator, he could supply the cutting optimization software with consistent and complete information with just a click and no further manual entries. That would be a further quantum leap. In fact, I get the impression that the "PC-phobic" Strom finds this approach quite cool. The nice thing about it is that with the Cutting Production Set, he is already ideally equipped for it.
Cutting Production Set from HOMAG at a glance
Optimization and more: what the cutting assistant can do
The Cutting Production Set supports joiners and carpenters in cutting on circular saws as well as horizontal and vertical panel saws of any type and age – from cutting optimization, through the cutting operation on the machine right up to the label printing.
The set includes:
- The following apps: intelliDivide Cutting (optimization software for cutting), productionAssist Cutting (assistant for manual cutting) and materialManager (central material management)
- HOMAG CUBE and label printer
- Commissioning instructions
Here's how it works: First, the intelliDivide Cutting app ensures optimized cutting patterns. After the transfer to productionAssist Cutting, this app helps with the processing in the workshop: a display on the tablet shows which parts have already been sawn and the operator is shown a suggestion for the next part to be sawn. The operator then provides each part sawn with a label. This contains all the relevant information as well as the barcode for the CNC and edge banding machine.
Easy installation: Commissioning instructions show the steps for installing the HOMAG CUBE and the printer. The apps are activated easily via credit voucher codes supplied. All that is needed is access to www.tapio.one. Once the tapio account has been created, it provides the business with an overview of all apps that it uses and can give any number of employees access to the individual applications.
Further assistants: The cutting assistant is one of three digital assistants currently available from HOMAG. The edge assistant (Edgeband Management Set) helps with the organization of the edging strips directly on the edge banding machine. The sorting assistant (Sorting Production Set) can be used to sort components in the workshop.
All sets are available in the online shop: shop.homag.com
Photos: BM magazine/Christian Närdemann
You are interested?
Feel free to send an inquiry via the HOMAG eShop…
...or send an e-mail to DigitalFactory@homag.com