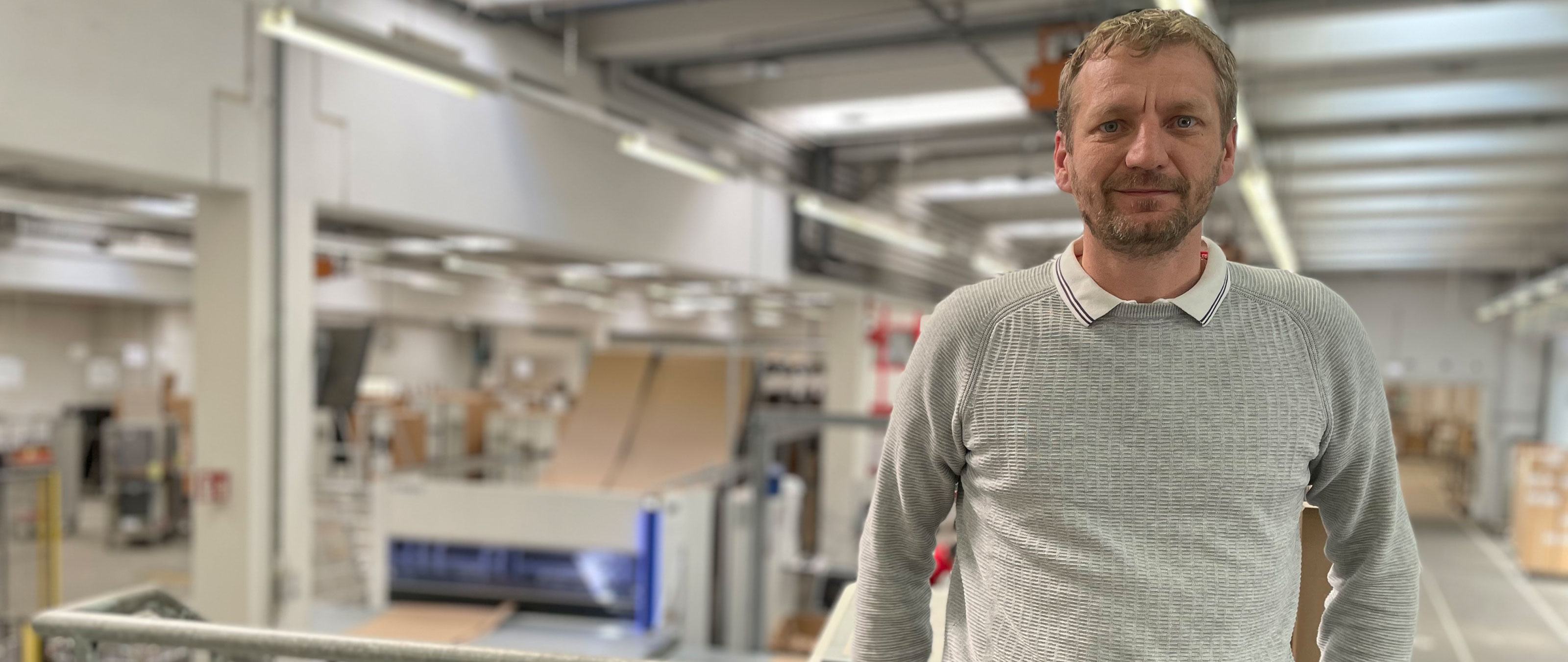
The kitchen is the heart of any home. In the Upper Austrian town of Wels, ewe Küchen manufactures each of these lifelines individually, in high quality and with a love for detail. Since the beginning of the year, ewe has been using a HOMAG cardboard cutting machine to ensure that the fittings reach the customer without any defects.
In 2021, a total of 209,900 kitchens were sold in Austria. That means that, on average, every twentieth Austrian household invested in a new kitchen. The rising demand for kitchens in the Alpine country also demonstrates how dynamic this market is; demand increased by a whopping 7.9% in 2021 compared with the previous year, and by 24% in the case of ewe Küchen. This increase for ewe Küchen was accompanied by a growing market share of 1.3%. In line with the growing demand, 2021 also showed that the quality of kitchens is constantly increasing and that customers are paying great attention to details and fittings.
Made to order, with high production capabilities
As part of the Nobia Group—the largest kitchen manufacturer in Europe—ewe produces high-quality kitchens in batch size 1. The brands in this group include ewe with modern kitchens, FM as a contemporary country house design line and INTUO design kitchens. For example, the "ewe Fina" model is the most popular model from Wels, with the matte surface "ewe nanoo"; "FM Hirschalm," as an example of the newly interpreted country house kitchen, combines traditional influences from the Mühlviertel region with a modern look and feel.
The kitchens are manufactured at the Wels and Freistadt sites. In addition to the batch size 1 principle, the decisive manufacturing principles here are networked, interlinked production in throughfeed with high production capabilities. "Every cabinet is made to order," emphasizes Michael Sterrer, head of engineering at Wels. "Every side, every base, every compartment is produced individually. There is no component that is not connected to an order." Under these framework conditions, a kitchen carcass has a throughfeed time of three days and 1000 cabinets are produced per day.
900 individual parts on line A
Manufacturing in Wels starts with a rack system in which approximately 50 coated panel types are stocked in two thicknesses. "We currently use approximately 25 decorations in the carcass area, each of which has a one-sided and two-sided version," says Sterrer, discussing the range further. Painted and veneered parts are produced in Freistadt and then imported into production at Wels. In principle, half formats run in two carcass part lines, of which the main line A processes all the tall, wall and base cabinets. That's around 900 units per day. Processing starts with two single-axis saws that cut 5,500 parts every day. Here, each part is given a label that contains only data on the type of panel and its dimensions. The subsequent processing steps result in x different components. First of all, however, the part goes via an intermediate buffer into an edge production line, where four systems are connected in series such that the part can pass through in a fixed position. "After the edge line, the part now knows what it is and to what order it belongs," Sterrer emphasizes. The line ends with two outfeed lines, where the components are first pre-sorted and collected in containers, to then run into a picking station.
In manual picking, all parts from the lines in Wels meet with parts from Freistadt in order to be brought into the exact production sequence. ewe performs the subsequent customization as late as possible in the final assembly. In this respect, the maximum batch size, which is currently combined in the carcass area, accounts for one day. "We are even considering reducing this further, because it would simplify the picking process and reduce the amount of logic and expertise required." Ultimately, the individualization of the parts is implemented in a highly automated throughfeed system, where the parts are drilled and dowels are inserted, fixtures are applied, and the parts are assembled and pressed into the carcass.
Another 100 special cabinets
On the second carcass part line, special line C, which produces around 100 cabinets a day, parts that deviate from regular parts are run: particularly small or large parts, but also highly structured parts or those with differences in décor and high-gloss coating. All cabinets that are not cuboid-shaped—for example, corner cabinets—are also processed and assembled here, as well as cabinets that require a high level of effort to assemble that cannot be realized in clocked production. In order to achieve 1,000 parts per day, this line also works with a single-axis saw, but in this case, it is followed by an edge line with return transport.
On both lines, the cabinets run in a colorful order sequence, with commissions produced one after the other. At the end of the two lines, the cabinets then go toward the packaging plant.
Packaging in batch size 1
To sell the kitchens, ewe works mainly with independent dealers who receive the cabinets as carcasses. Since 2009, when ewe put the first packaging plant into operation, the kitchen manufacturer has tailored the packaging exactly to the respective cabinet. "The variety of our products naturally led to a great need for different cardboard box sizes," said Sterrer. "We use three-part or even four-part packaging for glass cabinets alone." In the last twelve or thirteen years, ewe has thus gained extensive experience with batch size 1 packaging. "We have created all designs and processes ourselves, and we continue to run them exclusively to this day. We therefore intend to continue using the associated programming software, which we also purchased in 2009."
All the data required for individual packaging has so far come from an ERP system. ewe uses an interface that it has created itself, via which all relevant information reaches the plant: of course, the carcass width, height and depth, but also, for example, the material thickness of a front. Depending on whether this is 18 or 22 mm thick, different handling processes are ultimately needed for the packaging. "The required data is provided slightly ahead of time. With up to six carcasses as a buffer, we scan the barcode of a cabinet directly in front of the packaging. This creates a variable list in the ERP system, which together with a design, results in the appropriate cut."
Keeping the data structure where possible
Today, ewe has four packaging plants in use at both locations. The individual packaging in batch size 1 is established and extensive expertise is available. So why did the kitchen manufacturer choose a PAQTEQ C-250 from HOMAG for the upcoming replacement investment? There were several reasons. "For example, we liked the fact that we can now print on the cardboard boxes. We have cabinets for which we don't just produce one handling unit, but two or three. A colleague might lose their train of thought and be unsure which design belongs to which cabinet," says Sterrer. "Today, we simply print the five-digit item number on the cardboard boxes, creating a clear connection between the design and the cabinet. The source of error is eliminated."
Another reason was the number of tools. While the previous plant worked with six longitudinal tools, the PAQTEQ now provides eight. "This capacity increase pays off if we need to increase throughput for a certain time," says the head of engineering. "During this time, we simply put another employee on the machine." It was also particularly important for ewe to remain flexible and consistent with the ERP system. The previous data structure of the four packaging machines was to be changed as little as possible. "In order to be able to transfer the data safely to the PAQTEQ, we have adapted the general structure together with HOMAG," reports Sterrer. A process that he thought ran as smoothly as the commissioning of the PAQTEQ, which had been well prepared in all details: "This worked sensationally."
40 seconds
The plant, which was installed at the beginning of the year, is now directly integrated into the line. The entire environment, in particular the conveyor technology for the cabinets and cardboard box designs, remains unchanged. The PAQTEQ is run with six cardboard box shafts. Thus, where three cardboard box widths have been used up to now, ewe now has access to each width twice. "Now we run the machines redundantly and can change the continuous cardboard either during the break or when the cycle on the assembly conveyor belt permits."
There is no longer a backlog on the belt. The 900 to 1,000 cabinets would be packaged in two shifts. "We are talking about a 40-second cycle. For every cabinet that comes from the assembly line, we cut a cardboard box for it and implement the handling in 40 seconds." The operators simply switch the machine on or refill the continuous cardboard. The PAQTEQ takes care of everything else, and the data transfer also runs automatically in the background. The packaged cabinets are then sent order-by-order to the shipping department on a transport carriage to be transported to the dealer by truck the next day.
Good to use
During the preliminary acceptance, the PAQTEQ had already demonstrated that more packaging can be handled in Wels today with a throughput increase of seven percent. An increase that comes in handy for ewe. Just think of the increased market share…
“Today, we simply print the five-digit item number on the cardboard boxes, creating a clear connection between the design and the cabinet. The source of error is eliminated.”Michael Sterrer, Head of engineering at ewe Küchen in Wels