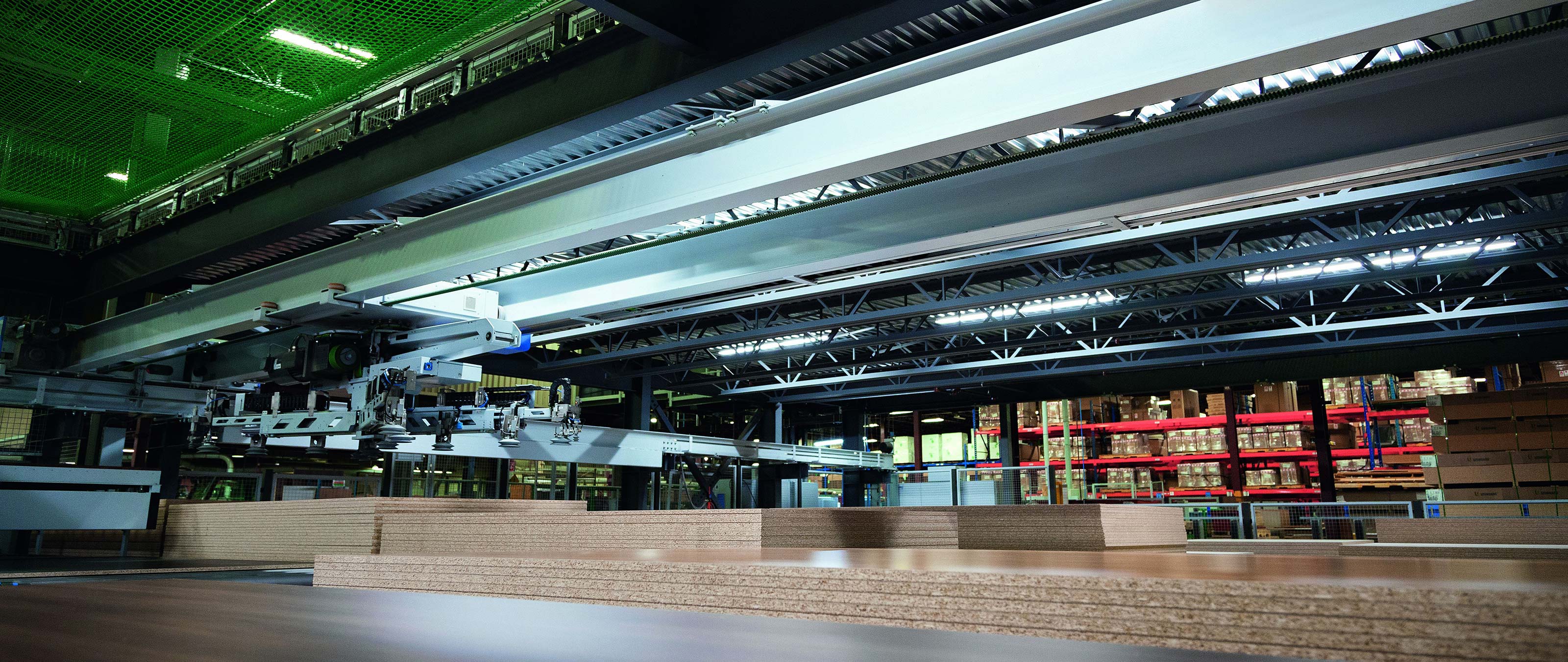
The Canadian office furniture manufacturer Artopex is a fan of the latest trends – and not just for desks, cabinets and chairs.
Stacked up behind the safety fence are hundreds of wooden panels in a variety of colors and finishes. A vacuum gripper whizzes back and forth across the storage area. It knows exactly where to find the right panel, lowers down onto it, and then picks it up and places it on the conveyor belt. Shortly afterwards, the saw bites into the wood and cuts the panel into several pieces. The pieces will be used to make furniture that will be used just days later in an office somewhere in North America. The state-of-the-art two-tier storage system and the fully automated robotic saws represent the first successful stage of a major replacement and expansion investment for which Canadian office furniture manufacturer Artopex has commissioned the HOMAG Group. Over a two-year period, the old production systems at the site in Granby near Montreal will be gradually replaced with a fully automated production system.
Help from a digital twin
Between now and 2019, the experts from Germany will deliver and assemble all the machines in such a sequence that production is not interrupted. This process is as complex as performing open heart surgery. Under no circumstances must there be unexpected production downtimes. This would be both disastrous and costly. The HOMAG Group is well-versed in projects such as this. “Perfect planning and a lot of experience are essential,” says Wolfgang Kläger from the technical sales team within the Business Unit “Systems”. Each individual delivery within the staggered implementation process is finalized way in advance and is rehearsed until everything runs smoothly. The setup is achieved in part through the help of a 3D simulation model that creates a virtual map of the production line. This digital twin is used to run various tests. The most important of these relates to the controllerMES production control system. This HOMAG Group software platform pulls together all aspects of the networked production process in a real operation environment. It issues commands to each machine relating to what it must do and allow, and the integrated reporting functions mean it can monitor whether the instructions have been followed.
Faith in the HOMAG Group
Given the meticulous preparations, Denis Bergeron remains relaxed about the situation. He has worked in collaboration with the HOMAG Group for many years now. “I know I can rely on them to take care of the implementation,” says the Artopex Vice President. He works closely with businessman Daniel Pelletier, who took over the 38-year-old FrenchCanadian family business in 1993. Today, Artopex employs 650 people across five different locations. The company designs and builds high-quality office furniture: desks, storage furniture, industrial chairs, soft seating, acoustic panel systems and partition walls. The furniture has its own unique style. Simple shapes, bright colors and individuality are the key features of the product range. “Our aim is to meet the needs of our customers in every respect,” says Bergeron. It is often the case in contemporary companies that designers create strict parameters in order to give the office landscapes a definitive look. This is why Artopex is set up to manufacture each piece individually, yet with an assembly line approach.
From tradition to pioneering spirit
At the end of the 1990s, Artopex purchased a storage system with two integrated saws from the HOMAG Group – this was almost unheard of at the time in North America. A few years later, Artopex switched to small-scale production in batch size 1. Since then all machines have been electronically controlled and know how to process each individual part. Quite early on, Artopex purchased a processing center for this purpose, as well as an edge banding machine that was interlinked with the drilling technology . “We were always keen to lead the way on technology,” says Bergeron.
By 2014, the systems had served their time. Bergeron was now considering a new production system. He was spurred on by a technology tour that he took with the HOMAG Group in Europe. A week of visits to various factories – always displaying the latest technology. The representatives from Artopex were excited by what they saw. As a result, Founding President Daniel Pelletier gave the go-ahead to build a fully automated production system. The main aim was to create a system that was faster than the previous one. His requirement was that the system should be able to cut up to 4,000 parts per day, complete with formatting, edging and drilling or trimming. At full capacity, this equates to up to four parts per minute. A sizable figure.
Not for the faint of heart
Planning began as soon as the trip ended. Local sales company HOMAG Canada and technical salesman Kläger worked with Artopex to get the project off the ground. The idea was for the five implementation stages to be spread over two years – with no production downtime. The first step was to create the new, fully automated storage system and connect it to the saws. “We walked around the factory with the customer and discussed which parts of the system to move during implementation, and where to, so that the running machines could continue with production,” says Kläger. Not for the faint of heart. The new material must be stored, and sorted in such a way that each part is available immediately as soon as it is needed. Steel, cables, tools – it all adds up to tons in weight. While walking around the factory, Kläger came upon a panel storage area that was no longer in use. This is where the new storage system would be set up and interlinked with the saws. “This first stage was relatively easy to implement,” says Kläger. The storage system and saws have been in operation since the end of 2017. Now for the next steps.
A new factory, step by step
A decoupling buffer is scheduled for incorporation in the system by fall 2018. It is an important part of the production line – the cut pieces “rest” here, so to speak. If there are no supplies in the warehouse, production can still continue. The edge processing system is also scheduled for completion by the fall. Edges are the hallmark of good furniture. No dirt should gather in the joints. The machines from the HOMAG Group position the edges on the correct part, in the appropriate color. A laser beam brings the edging strip to melting point and the strip is then pressed against the panel.
Edge processing systems are able to process unusual shapes, but there are limits. If a customer wants a completely non-standard furniture design, Artopex uses a HOMAG Group electronic processing center to take care of edging; this center is designed for more complex jobs and will be positioned alongside the production line.
Networked right to the customer
The drilling technology will be added from fall 2018, followed in spring 2019 by the sorting buffer. The sorting buffer puts the processed parts in the correct order for the available assembly conveyor belts. The fifth stage of the process will see another saw and a second edge processing system added. This will double production capacity again and the cutting and edge processing areas will be kept as redundant areas. Artopex already has plans for after the conversion: The company is considering extending the production line. In the future networked machines will also pack the parts. Then all that remains is to load them onto the trucks and assemble them at the customer’s premises. “The fully automated production line will then be complete,” says Denis Bergeron. “And Artopex will remain a technology leader into the future.”
The digital twin
The use of digital twins is becoming increasingly common in the mechanical engineering sector. What we mean by this is a virtual machine that is mapped on the basis of a real machine before the real machine is assembled. The twin is created as a real-time-enabled, hardware-in-theloop simulation. The simulation makes it possible to test all the machine functions on the digital twin even before the real machine is assembled.
Other benefits of the twin: Mapping complex material flows within a realistic framework makes it possible to optimize systems and also to carry out risk-free testing of new software. Using the system throughout the entire life cycle of a machine could, in the future, lead to problems being replicated in service cases and thus being solved more quickly.
“I know I can rely on the HOMAG Group to take care of the implementation.”Denis Bergeron, Vice President, Artopex Inc.