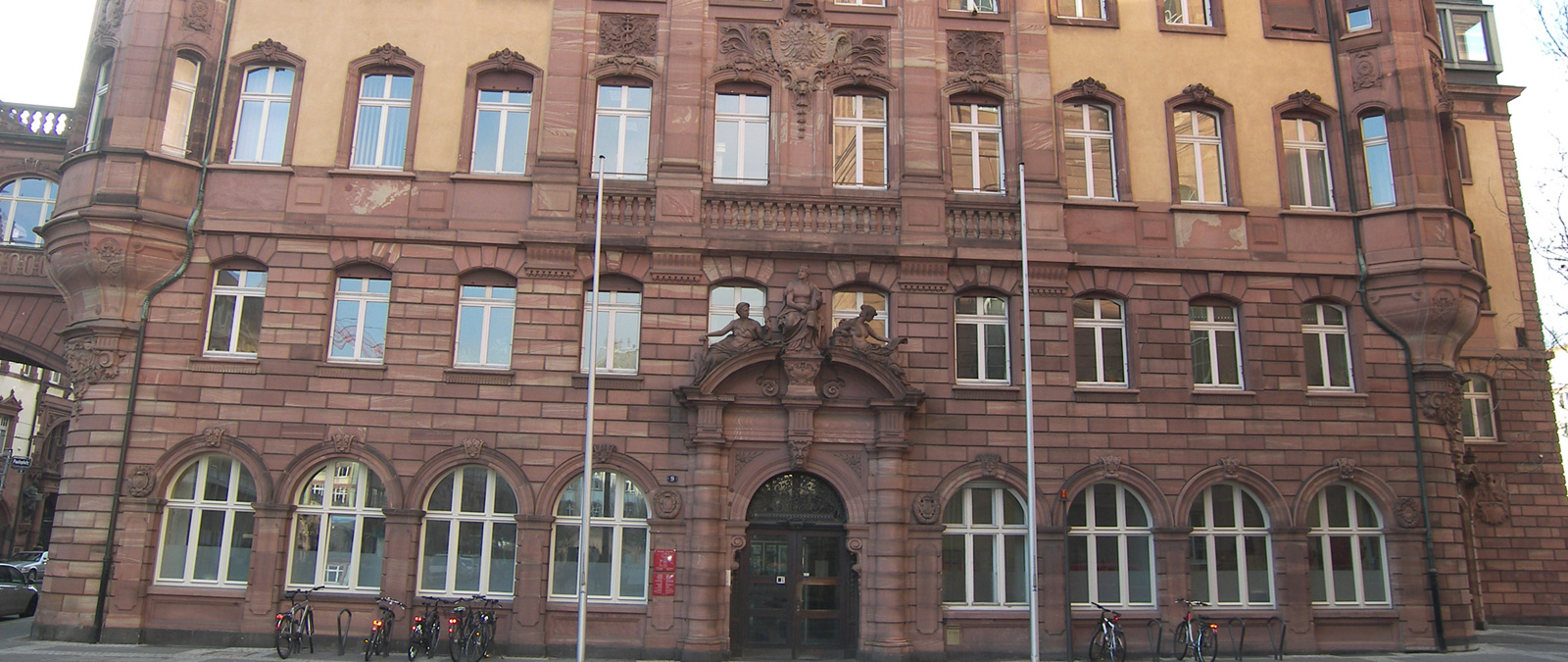
The joinery Koch in Otzberg produced 60 arched windows to be fitted in the northern wing of the famous Römer town hall building on the Paulsplatz in Frankfurt. The flexibility and efficiency of this traditional joinery business improved practically overnight once it had installed the new HOMAG BOF 211 processing center. Koch is now able to tackle commissions it would previously have considered too ambitious.
Asked to sum up the main attributes of their customers, Managing Directors Herbert and Jan Koch come back with a very confident answer: “A healthy respect for tradition, a receptive attitude to new ideas and vision for the future”. What makes this assessment all the more convincing is that these same attributes could just as easily be used to describe the Koch joinery business itself. Modernization and change were the key strategic pillars propounded by founder Georg Koch back in 1959, and have been embraced with equal enthusiasm by his son and grandson who are continuing to breathe new life into the business as Managing Directors. Continuous adjustment and adaptation of the company to the demands of the future have always been fundamental to the Koch family philosophy.
Instant leap forward in efficiency
The latest step in the company’s continuous drive toward modernization was to invest in a BOF 211 processing center from HOMAG in July 2011. The new machine not only resulted in changes to the production process but also helped to boost the order situation, as the economic processing of large-scale contracts is now firmly on the agenda. “Our lead and set-up times have been reduced, and we only need one operator to be in charge of the machine. This type of order has now become viable”, explains Herbert Koch. “What impressed us the most is the machine’s enormous flexibility. We are now able to tackle orders we would never have been able to take on before.”
Previously, Schreinerei Koch worked with a smaller HOMAG processing center and a conventional angular plant for its window production. Together, these machines only achieved capacity utilization of around 30%. Jan Koch explains: “Because of the enormous flexibility of the machine and our limited space availability with a production area of just 3,00 sq.m., we decided to replace these two machines by a single larger processing center. Although the BOF 211 is longer and wider than its predecessor, it allows us to carry out all processing operations on one and the same machine, making us far more effective, and ensuring our continued success as a contender in the marketplace.”
60 windows – each one different to the next
Alongside individual requests from private customers, the company Koch also takes part in all kinds of invitations to tender – most recently clinching a contract for work on the listed Römer Town Hall building in Frankfurt. The north wing of this landmark town hall building, constructed in 1908 in the neo-baroque style, is located in the direct vicinity of the Paulskirche. All the arched windows on the ground floor – 60 in total – had to be renewed. Production on the new HOMAG processing center started in December, with assembly of the windows taking place in January. The windows were required to comply with resistance class 2 and came in a wide range of different dimensions, with no two windows the same. The Koch team produced four complete Römer windows every day, comprising around 150 individual components. If producing single sash windows, this would be around the equivalent of 20 window units per day. A perfect link to the Klaes trade-specific software is particularly advantageous for this type of application. Koch also benefits from the machine’s easy-to-operate, highly flexible clamping technology. Depending on the size of the parts, several workpieces can be positioned for processing simultaneously, saving time and money. The glazing bars for the whole window including miter cut are finish recessed during the first pass. Where a number of intermediate steps used to be required, the operator is now able to remove the parts form the machine finished to a perfect standard of quality and surface finish.
“Standard is commonplace”
“The contract to work on the Frankfurt Römer building is the first major order we have completed entirely on the new machine. Without the new HOMAG processing center we would never have even considered undertaking the order to replace the windows in the Römer building. Using our previous machine outfit, it would have been unrealistic to even attempt economic production of an order like this. And what’s more, we are blown away by the surface and the finish quality. The results are amazing“, confirms Herbert Koch. “Our special field of expertise is not churning out mass volume: our focus is on non-standard and special designs. We particularly relish the challenge of unusual orders, call it cherry picking from the joinery cake”, Koch continued. “And as far as materials are concerned we can process practically anything.” As regards order scope, since the new machine has been in place the Kochs are now broadening their horizons on every dimension – whether individual one-off orders or large-scale projects. “The machine has the capability to achieve still more, we are only beginning to explore the possibilities”, says Jan Koch.
Convincing overall package
With five decades of experience, a 15-strong production team and additional teams specifically for assembly, Schreinerei Koch customers are impressed first and foremost by the overall package. Anyone entrusting their project to Koch benefits from all-round support and a complete project processing service from A to Z: always with the premise that top quality and flexibility are underlying standards embraced by the firm. With its broad-based product spectrum, Koch does not aspire to establish a broad market basis, but rather to cover niche demands – including the field of high-end interior fixtures and fittings. This is why, supported by HOMAG Sales Partner Dr. Keller, the Kochs have placed their trust not only in the BOF 211 but also other machines from the HOMAG Group portfolio. These include an Optimat SBC 213 sanding machine from BÜTFERING, a KDF 30 C from BRANDT and a HOMAG saw to address the most stringent expectations of quality and precision.
Extreme material diversity
Window production in wood and wood / aluminum constructions accounts for over half the total production output of Schreinerei Koch. The fields of furniture production and interior fittings account for around 30%. Also part of the company’s portfolio are front doors, lift and slide doors and internal doors in all kinds of wood.
One element of the overall Schreinerei Koch package is the “Door configurator”, which can be accessed on the company’s website. This affords customers the facility to put together their own individual door, choosing freely between a variety of designs, side elements, wood types and colors. Additional available options for all the doors and also windows include inward or output opening, resistance classes 1 – 3, with or without assembly.
“We are committed to quality”
“In the search for an optimum solution for our company, the focus was primarily on flexible machine application and our high quality aspiration. We compared a number of machine engineering firms, but the one which stood out for us was HOMAG Holzbearbeitungssysteme GmbH. We are committed to quality and we strive to address the ever growing expectations of our customers. We were also able to draw on the excellent results we experienced with the previous HOMAG processing center”, recalls business administration graduate Jan Koch. His father adds: “When the new machine arrived, we changed our production sequence and oriented the material flow directly to the machine. Although this was a steep learning curve and took some getting used to, during the period up to the launch of production and complete integration of the machine into our production sequence, we were already able to categorically state that the adjustment process had paid dividends”. A particularly valuable bonus for the company Koch was the one-stop link up with a single contact partner who assumed equal responsibility for everything during the set-up process, including hardware, tooling and software.
As far as the future is concerned, although the Koch joinery may enjoy the luxury of several months’ planning security ahead, it is now also able to respond flexibly to all kinds of other orders. Asked whether they would opt for the HOMAG processing center again, both were in perfect agreement: “We most certainly would”.