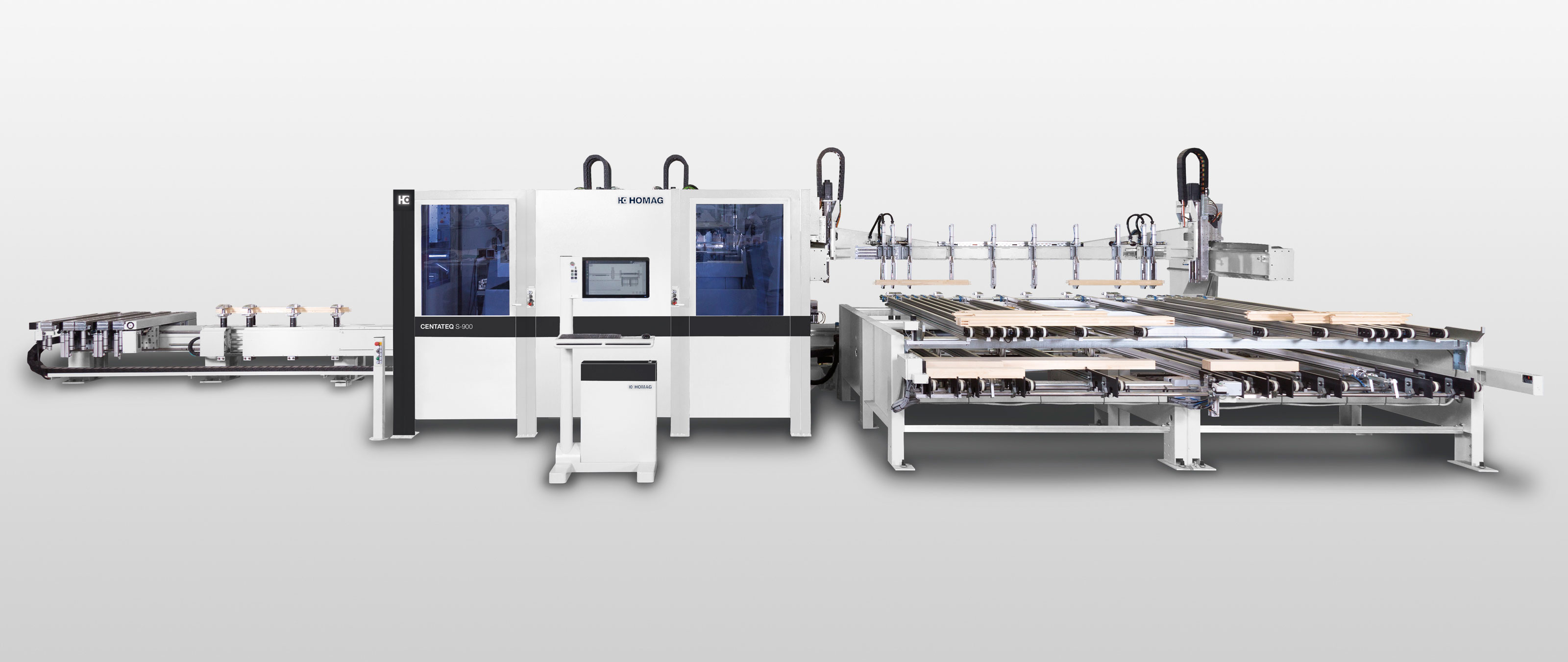
To keep ahead of the rapidly changing UK market for windows, Essex based Mumford & Wood recently invested in the state-of-the-art HOMAG CENTATEQ S-800 CNC machining centre. This windows CNC is the latest addition to the plant list of HOMAG machinery operated by the company. This advanced CNC is designed to increase output and productivity whilst maintaining Mumford & Wood’s reputation for quality and service to core customer groups including architects, developers, designers and owners of aspirational homes.
“Over the last 10 to 15 years, the UK market for windows has changed dramatically,” explains Mumford & Wood managing director, Dion Panting. He continues, “The design of windows and the components used to make them have become far more complex, while batch sizes have become smaller, more bespoke and with much lower volume requirements.
“Compounding these issues, is a lack of skilled labour throughout the construction and manufacturing industries. This means that house builders are reluctant to use just primed and unglazed windows onsite; they want fully finished windows ready to simply fit into the building.
The latest CNC windows machining centres
HOMAG has led the way in advanced CNC window machinery for many years and the company’s latest iterations, the CENTATEQ S- 800 and S-900 have raised the bar even higher. Phil Pitchford, HOMAG UK’s CNC specialist takes up the story, “When it comes to windows CNC machines, we view every sale as a project. We start the process with an initial meeting in Germany where we involve the tool and software suppliers to discuss the parameters with the customer.
"We discuss all of the individual window profiles the customer wants to make and we evaluate all the tooling suggested by the tooling supplier to ensure suitability.
“The next step is to make certain that the software team can program what’s required. This might sound obvious, but very few CAD|CAM systems on the market can drive a CNC windows machine because of the complexity of the process.
“We use our own woodWOP parametric software which has become recognised as the industry standard and, together with the tooling manufacturer and the customer, we prepare and test each window system on the customer’s machine, using their timber, tools and ERP output. Mumford have invested heavily in KLAES software over the years and it represents the backbone of their company.
“When Mumford & Wood go out and see a customer, they design the windows, cost them and the KLAES software provides all the timber, glass and ironmongery requirements etc., effectively creating a bill of materials for the job. Then, using the HOMAG interface, we merge the details into the woodWOP software to generate the individual component programmes to yield a fully finished workpiece.
“Before we deliver a CNC windows machine to the customer we carry out one or two weeks commissioning at the factory using their tooling systems. Then we do the same when it’s delivered to the customer’s facility. It’s a lengthy process, but it pays in spades.”
Limited competition in the marketplace
There are few manufacturers on the market that can offer this type of CNC machine or the level of service that HOMAG provides. Dion Panting again, “A major attraction to us was the extremely compact footprint of the CENTATEQ machine, the HOMAG service and the benefits of the proven woodWOP software.
“Add to this the flexibility of the machine, the output speed and quality, and the value for money, and it becomes clear why the decision to invest in this machine was relatively straightforward.
“As part of our due diligence, we visited a factory in Germany which was operating a similar windows CNC and this gave us confidence that the machine would deliver exactly what we were looking for.”
Powerful and versatile production
To improve the versatility of the CNC and increase the productivity, we specified both and 5-axis heads for our CENTATEQ S-800. This enables us to use the power of the 4- axis spindle for the heavy operations such as counter profiling and rebaiting. The 5-axis then available as a second head that can spin over off the vertical and do any operation using the full power and spindle.
“The results we’ve achieved with this new machine have been outstanding. We even managed to process 270 components (pieces of wood) in one nine hour shift which is unheard of in complex window manufacturing. This is partly due to the rapid load cycle of the machine.
“Once we’ve loaded one table, that will start processing the work and at the same time we can load up the second table ready to run as soon as the first table finishes. This re-clamping in cycle eliminates a huge amount of the downtime you get with other machines and is why our throughput is so high.”
First class training and support
The training and support HOMAG provides prior to and after the machine has been installed is first class. Once they’d trained our operators on the basics, they remained onsite for a further two or three weeks to make sure everything was working as it should and we were running at full production.
“There are horror stories out there of manufacturers installing a machine and giving only basic training – with HOMAG you get real peace of mind, they are on your team from day one and that’s something we really appreciate.
“The benefits the CENTATEQ S-800 has delivered for us are many. Perhaps the most important is that every part comes off correct and finished to the premium quality standards we demand. Basically re-working is a thing of the past and because components are fully finished in one clamping, the risk of damaging each piece of timber during the manufacturing process is much less.” concludes Dion Panting.
If you would like a demonstration or further information on HOMAG’s CNC windows machining centres or woodWOP software, please contact HOMAG UK on 01332 856424 or email: info-uk@homag.com
“The results we’ve achieved with this new machine have been outstanding. We even managed to process 270 components (pieces of wood) in one nine hour shift which is unheard of in complex window manufacturing. This is partly due to the rapid load cycle of the machine.”Dion Panting, Managing Director