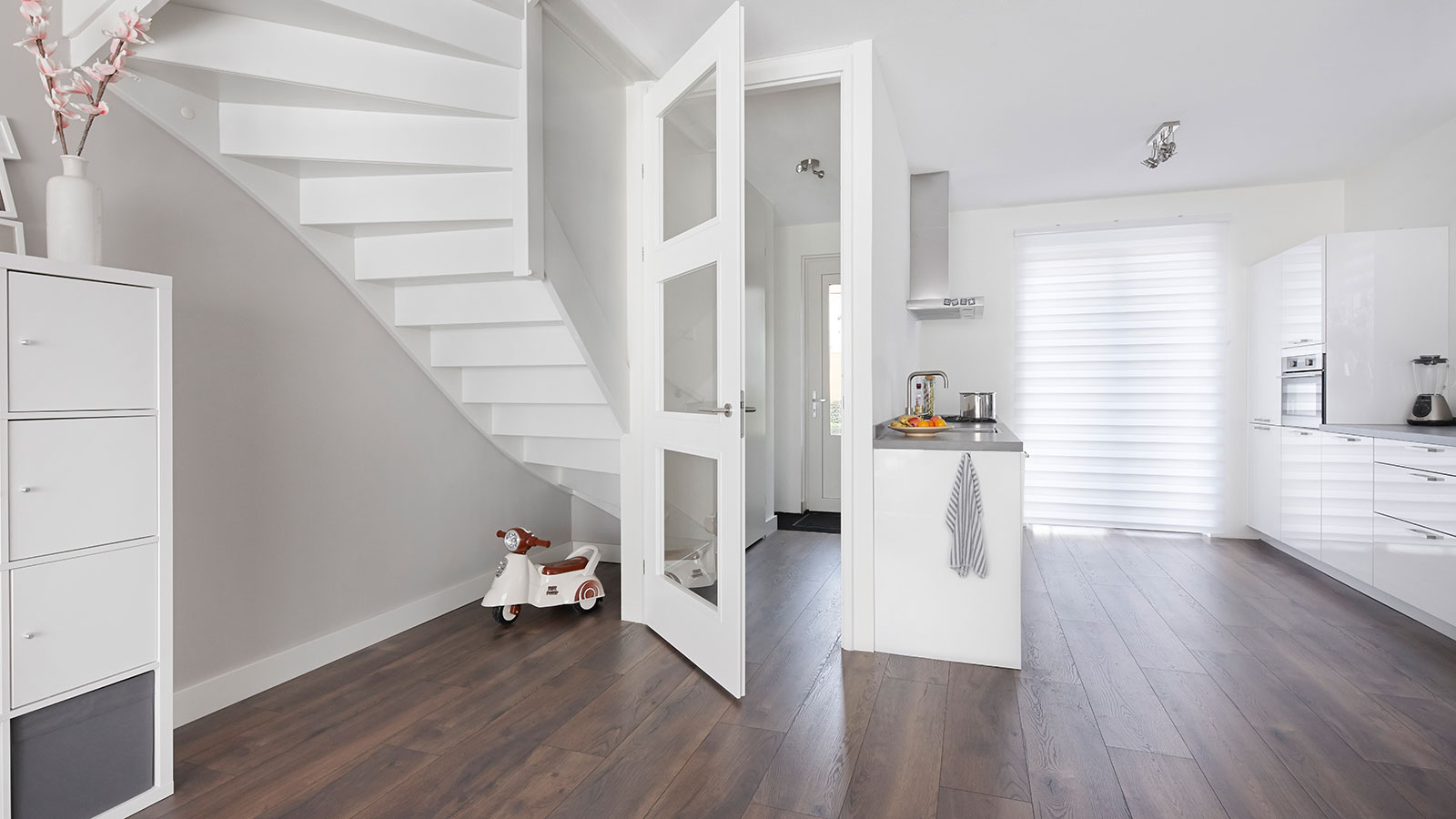
Practically speaking, doors connect or separate rooms— that is their purpose. But a door is much more than this, as nothing is shaped more by our individual personality than our own four walls. HOMAG has designed a processing cell that supplements a classic system for producing door leaves and offers particularly impressive flexibility. The Dutch door manufacturer BERKVENS TUR SYSTEMEN BV has been using the system successfully for six months and is producing doors with much more customization, thereby contributing significantly to designing indoor spaces.
The most important thing for people in Germany is their own four walls. This is shown repeatedly by surveys and statistics that place classic investment goods such as cars or electronic/entertainment devices lower down in the rankings. It's easy to see why. Within our own four walls we find peace; they give us a feeling of wellbeing and we recharge our batteries there. There are no limits to individuality in furnishings and design when it comes to getting the right feel-good atmosphere.
When designing rooms, the furniture and the color of the walls are not the only things to consider. The overall concept must be harmonious and the design of the doors is also very important. Doors enrich the comfort, functionality and atmosphere of rooms. They have different surfaces, different types of edges; cut-outs for glass panes or grooves; all of which allow them to be adapted excellently to suit individual tastes and the space within the room.
Automated CNC processing on two processing tables
To allow for individuality but still enable industrial production, as an addition to the finishing processing in door production, HOMAG has developed a CNC stationary cell for finalizing door leaves. At the core of this cell is a CENTATEQ P-500. It is fed automatically by a robot that moves in the X and Y axes.
The cell is connected directly to the classic throughfeed line and offers fully comprehensive processing of door leaves for fixtures, cut-outs for glass panes or decorative grooves.
The production sequence is as follows: The prefabricated door leaves are fed into the machine via a roller conveyor. Here they form a stack of unprocessed parts that the robot uses as the starting point for feeding the CENTATEQ. In the next step, the individual door leaf can be turned using an alignment table. It is placed in the correct position and simultaneously identified by a barcode scanner. The barcode gives the CNC processing center information about the properties of the door and the processing steps to be performed. The actual trimming of the door is the main part of production. The door is produced and processed according to the specifications.
The automatic processing means that the following actions are performed simultaneously: the robot places new door leaves on the alignment station, the robot disposes of offcuts and a new door leaf is placed on the other side of the processing table of the CENTATEQ. Finally, the robot unloads the processed door leaves onto the finished part stack. All feeding and handling processes can be executed independently of one another. The machine can be run in 100% shuttle operation with no waiting times.
Efficient production with no idle or lost time
The robotic feeding of the cell is the key to a smooth production flow without any idle time. Analog to the processing of a door on the CENTATEQ P-500, post-processing and preparatory steps also take place with robotic support. As part of the offcut picking process, the robot removes and disposes of the panels that have been trimmed out to create the cut-outs for glass panes. This is faster and more efficient than cutting the parts up into smaller pieces. The finished door is removed from the production table and placed on the finished part stack. The alignment table can then be used to place the next door in the correct position for feeding to the CNC processing center, which, after processing the current door, is ready for the next door immediately. The barcodes located on the threshold sides, which provide information about the properties of the door and the processing steps to be performed, allow the robot to sort the doors individually after production. This means that from one stack of unprocessed parts, by adding protection boards, multiple finished part stacks can be formed, dividing a quantity of 20 doors, for example, into stacks with quantities of 2 x 5 and 1 x 10. The robot moves in the X and Y axes to ensure maximum flexibility and to reach and feed all stations efficiently, such as the alignment station or the waste box. The automated, fully automatic parts handling guarantees not only efficient production but also consistent quality, full reproducibility and reduced waste.
High-performance configuration for processing doors quickly
It is not only the feed that is optimally aligned to the requirements of door processing. The tool selection and spindle configuration are also optimally configured. Here, HOMAG uses a DRIVE5C+ five-axis head with a pre-tensioned crossed roller bearing and spindle with encoder return. The spindle is distinguished by high and constant performance over the entire speed range and by highly precise movements. The 28 kW high-performance trimming spindle can rotate at up to 30,000 rpm. It represents high performance, a high level of removal and efficient processing with small tools. The spindle also has a high-performance C axis with strong dynamics. This is particularly important for processing with small radii or corners, when the C axis also has to swivel. Both spindles have a sensor for load control with visualization software and a program-controlled, infinitely variable extraction hood.
Each spindle has its own piggyback 10-slot tool changer, which means that one spindle can always be working while the other is changing for the subsequent processing. The complete system is equipped with a central 18-slot tool storage at the bottom that can be accessed by both spindles.
The machine receives the travel paths and specifications for trimming or drilling from the HOMAG project manager, who imports programming modules into the control system. The programs are put together automatically via a description of the dimensions, the design of edges or cut-outs for glass panes. However, customized and spontaneous adjustments are also possible. Measuring devices can be used to determine the contours of doors to record the reference edges. The offsetting takes place in the program automatically, even for a program position correction.
Customers and the market have a growing desire for individuality in the field of cut-out processing for fillers or glass, decorative grooves and application processing. Door manufacturers are faced with the challenge of meeting this desire. Combined with the robot, the CENTATEQ P-500 represents efficient production in finishing processing for doors. The automated processes and the fully automated parts handling guarantee productive and highly efficient execution.
Toon Snoeijen, technical project manager at the Dutch door manufacturer BERKVENS TUR SYSTEMEN BV, describes his experiences after the first six months with the CENTATEQ from HOMAG.
1. Why did BERKVENS decide on this type of solution?
"The new CENTATQ with robotic feeding replaced a HOMAG machine that had to be fed manually. We want to increase production capacity and decided on this solution."
2. What were the important factors in the design for you?
"That the system meets our demands precisely in terms of capacity and performance. We also had limited space therefore this cell was ideal for the final processing of the doors."
3. What conclusion can you draw after six months of production? Have the requirements that you set out for the machine in advance been fulfilled and what is the effect on production?
"Yes, the system was delivered according to our wishes and the agreed requirements. Thanks to the autonomous cell, we have become more flexible and we will optimize our processes further."
4. Can the machine also produce autonomously, without any personnel?
"Our production needs were taken into account fully when putting the system together and we can therefore produce autonomously, with less personnel."
5. How happy are you with the software and the control system?
"We had a list of requirements in advance and we were able to integrate these into the existing software and control system when designing the system with HOMAG. I can also say that we are very happy with the control system."
An article from "Türen" magazine in 2020. More information is available here.
“The new CENTATQ with robotic feeding replaced a HOMAG machine that had to be fed manually. We want to increase production capacity and decided on this solution.”Toon Snoeijen, technical project manager at the Dutch door manufacturer BERKVENS TUR SYSTEMEN BV