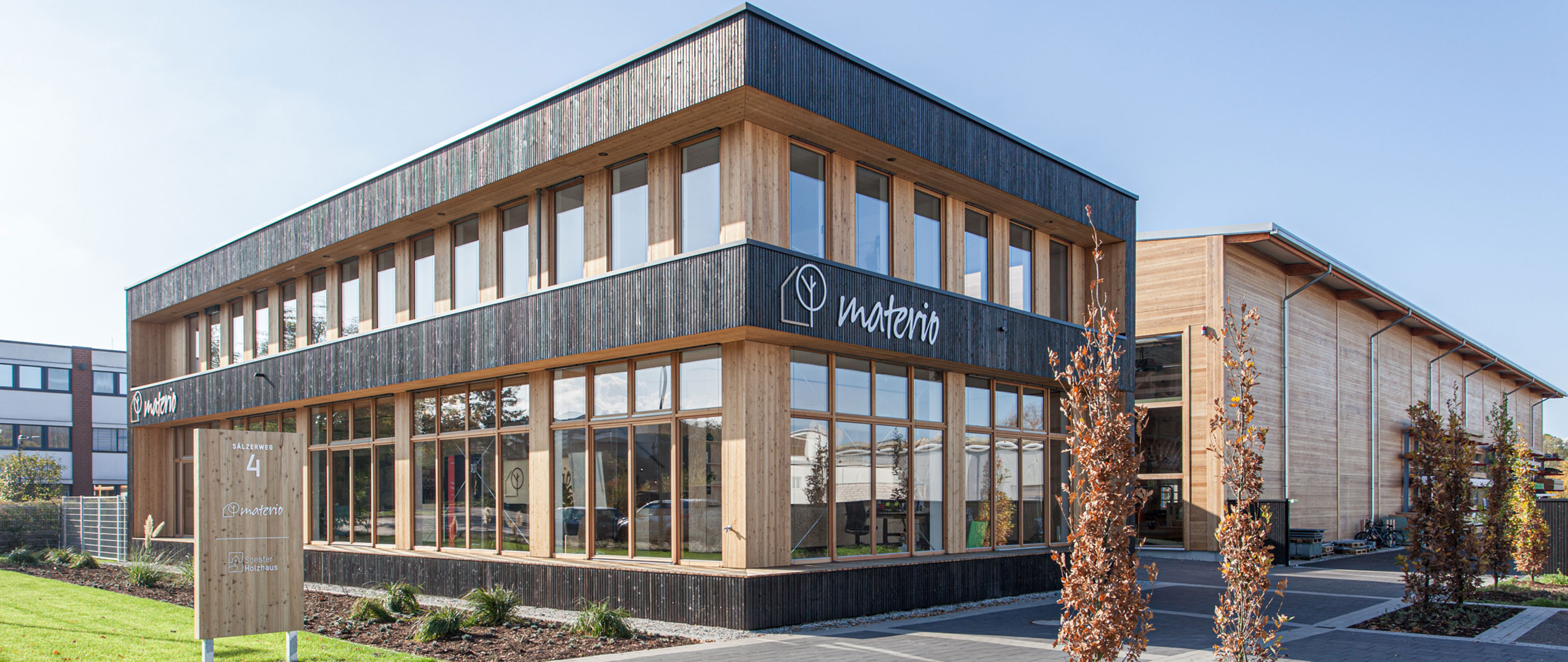
This is also the case in the "Auf dem Rode" construction area, where the company has built 18 detached houses in standardized construction. In doing so, the company took advantage of the benefits of serial construction and automated production. One of the key factors currently influencing timber construction is the development of the labor market. In view of an exorbitantly good order situation, it is the shortage of skilled workers in particular that is limiting the scope of timber construction companies. One of the first steps to mitigating the impact of this shortage of skilled workers is a comprehensive digitalization and automation of companies. However, this too is reaching its limits due to a lack of construction managers or assembly personnel on the construction site. This is a situation in which the imagination and creativity of company management are much in demand.
Serial construction with ecological materials
One person who has found an answer to the pressing issue of personnel is Rolf Schottmüller, managing director of Materio GmbH in Soest, in North-Rhine Westphalia. Active in timber construction since the 1990s, Schottmüller, who was born in the Black Forest region, founded the company in 2014 with his business partner Johannes Berger. In subsequent years, he has increasingly specialized in large-scale projects: "We were already active in the detached house sector, but today we have neither the construction managers nor the consultants to provide these clients with the kind of intensive support that we want to give them and that they are entitled to." This is one of the reasons why the company, with its 40 employees, is now focusing increasingly on buildings. The company does this preferably as a general contractor and investor in the commercial and municipal sectors: "If we are already responsible for project development, we can increase our impact immensely," explains Rolf Schottmüller. "We can then build in series and deliver at a fixed price within a tight time frame — with cost benefits through synergy effects, proven subcontractors and a mature system of ecological building materials for which all details have been checked in advance."
The focus here is on day care centers or office buildings; at present, the construction of residential complexes and multiple dwelling units is emerging as a future business area.
Competition for architects and investors
Even though the company is increasingly withdrawing from the detached house sector, it is still active in the development and construction of residential complexes. Detached houses are also being built here, but according to a completely dif-ferent business model. At present, for example, Materio GmbH is building 16 detached houses and two semi-detached houses in the "Auf dem Rode" construction area in Lippstadt. This is a former agricultural area that the city converted into land for construction in 2017 to counteract the housing shortage in the industrially well-developed region. In 2020, the non-profit-making housing association in Lippstadt advertised an architect and investor competition for a small parcel of land in this area, and Materio GmbH and its partner Rinsdorf Ströcker Architekten (RSA) took part in the competition. The aim of the competition was to cover this part of the development plan with space-saving and energy-saving buildings built by regional companies. The targets also included the design of sustainable, cost-effective and flexible buildings that provide a high quality of life, are attractive and have open spaces on the plots.
Intelligent and flexible living concept
Rinsdorf Ströcker Architekten solved these challenges with a concept for a residential com-plex that makes good use of the option of construction abutting property lines and places the residential units at the edge of the plot. The road space in the middle will be used as a community and interaction area. Although the line between public and private outdoor space was deliberately blurred in this concept to strengthen community life in the complex, each of the houses, built in the Bauhaus tradition, has a private outdoor area. The latter is created thanks to a playful shift of structure levels on the rear of the houses. Depending on the variant, this area is designed either as a covered terrace or as a balcony on the upper floor. The structural offset also livens up the facade setting in the residential complex because the houses facing the street alternately present a terrace under the projecting upper floor or a recess of the upper level with a balcony. The architectural appearance is made even more attractive by large glass surfaces and a facade blend of dark gray wooden strip paneling (upper stories) and white plaster (first floor). Thanks to a well-insulated outer shell and a heating system with geothermal heat pumps, the timber frame constructions achieve the KfW 40 standard in terms of energy, and residents are offered the option of retrofitting a PV system. The fact that the geothermal heat pump can be used for cooling in the summer fulfills a further requirement of the competition and enables individual temperature control of the houses even in the hot season.
Standardized in high quality
The fact that RSA and Materio won the competition was due not only to the impressive ideas of the architectural firm, but also to the sustainable timber frame construction of the timber construction company. Wooden windows, cellulose insulation and healthy interior materials are standard at Materio GmbH. In Lippstadt, the following were used: 435 mm thick timber frame walls with 260 cm of cellulose and 60 mm of fiber-board, solid wooden ceiling panels and 280 mm roof elements plus gradient insulation. Ultimately, this all leads to high-quality construction that does not sacrifice quality of life or ecological orientation. In addition to the construction itself, the flexible living concept was also impressive: each house can be divided into two living units on top of each other by separating the staircase – for example, a residence for a senior citizen on the first floor and a carer apartment on the upper floor. Further individualization options are limited to the option of dividing the open living space on the first floor with partition walls. The central walls of the bathroom, the plant room and the staircase, like the outer shell, are used to reduce vertical loads, meaning that they cannot be changed. The houses were designed according to a standard design and were sold to the future residents with the land included, whereby Materio GmbH acted as an investor and developer within the cooperation. After the first press release, most of the houses were sold in a very short time; during the first week, there were already twice as many inquiries as houses. Rolf Schottmüller sees this business model as "a huge advantage. If we build detached houses, then this is how to do it. Thanks to the serial design, we were able to use many synergies. For example, we only needed one system static – we were able to copy wall, ceiling and roof elements and therefore drastically reduce the effort involved in planning.
On the construction site, we saw how the assembly was smoother and faster with each repetition." Thanks to automation, the synergy effects could also be used optimally in production. Since 2019, the company in Soest has been using a WALLTEQ M-120 from WEINMANN for production. If required, this machine is also suitable for ceiling elements, and a special hall was built for it at the new company location. The insulation has been blown in by a subcontractor on the construction site for 20 years.
Wanted: More capacity and precision
The company invested in the automated production line due to the impact of a strongly increasing demand, which is fostered by politics: "As far as the day care centers are concerned, we had such a good name back then that we always received new orders by word of mouth. In Ennepetal alone, we have built four day care centers to date, and two more are already being prepared." In addition to the increase in capacity, when thinking about the automation, the company was also interested in increasing precision: "We have always set ourselves high targets and we were good even when producing manually – but today we are better," explains Rolf Schottmüller. "And you also have to acknowledge that with manual production, as the rate increases, the precision drops: anyone producing large quantities doesn't constantly have a yardstick in their hands." The personnel situation was also an important argument for automation. Today, with one employee and one apprentice, the company has a much faster workflow than before with more manpower and manual production. "With the WALLTEQ M-120, we produce the walls for a house within a week. However, in our experience, we do have to employ dedicated employees on such a machine. That way, we can achieve quantities that are even higher than WEINMANN's forecasts." When the company was searching for the right technology, there was no real alternative to the machine manufacturer in Lonsingen: "Even after a first introduction to the topic, for us, WEINMANN was far out in front. When we were then advised by friendly carpenters from another company to use this technology, the decision was perfect." The period that followed showed that the decision was right. This was not only because automated production started smoothly upon the installation of the new technology and, with increasing experience, brought ever improving results — it also became clear that the choice of the "small" WALLTEQ M-120 had been excellent foresight. "We use the machine a lot and it is ideal for our purposes, as we prefer to produce buildings with wooden facades."
Plans for the future
If, contrary to expectations, the demand for EIFS increases significantly, an upgrade to a larger WALLTEQ could be on the agenda in Soest: "If a lot of EIFS greater than 40 mm is to be processed, an additional sawing unit is recommended and therefore a change to a larger multifunction bridge, for example to the WALLTEQ M-380." But perhaps there will also be a shift to the next innovative business model. From today's perspective at least, managing director Rolf Schottmüller can imagine expanding existing collaborations with associated carpentry companies in this event: "Our partners would then produce some of the walls, while the majority of the work would continue to run along our production line. The carpenters could also help us with assembly during the strained personnel situation, while we continue to develop our activities in the direction of project development, planning, general contractor activity and investor activity."
Text: Dr. Joachim Mohr
An article from the customer magazine performance issue 21 | 2022. More information is available here.
“We have always set ourselves high targets and we were good even when producing manually — but today we are better.”Rolf Schottmüller, Managing Director of Materio GmbH.
Materio GmbH
Materio GmbH is based in Soest, North Rhine-Westphalia, and has been active in timber construction since the 1990s. Today, the company employs 40 people and focuses on large-scale projects, acting as general contractor in the commercial and municipal sectors.
More information is available here.