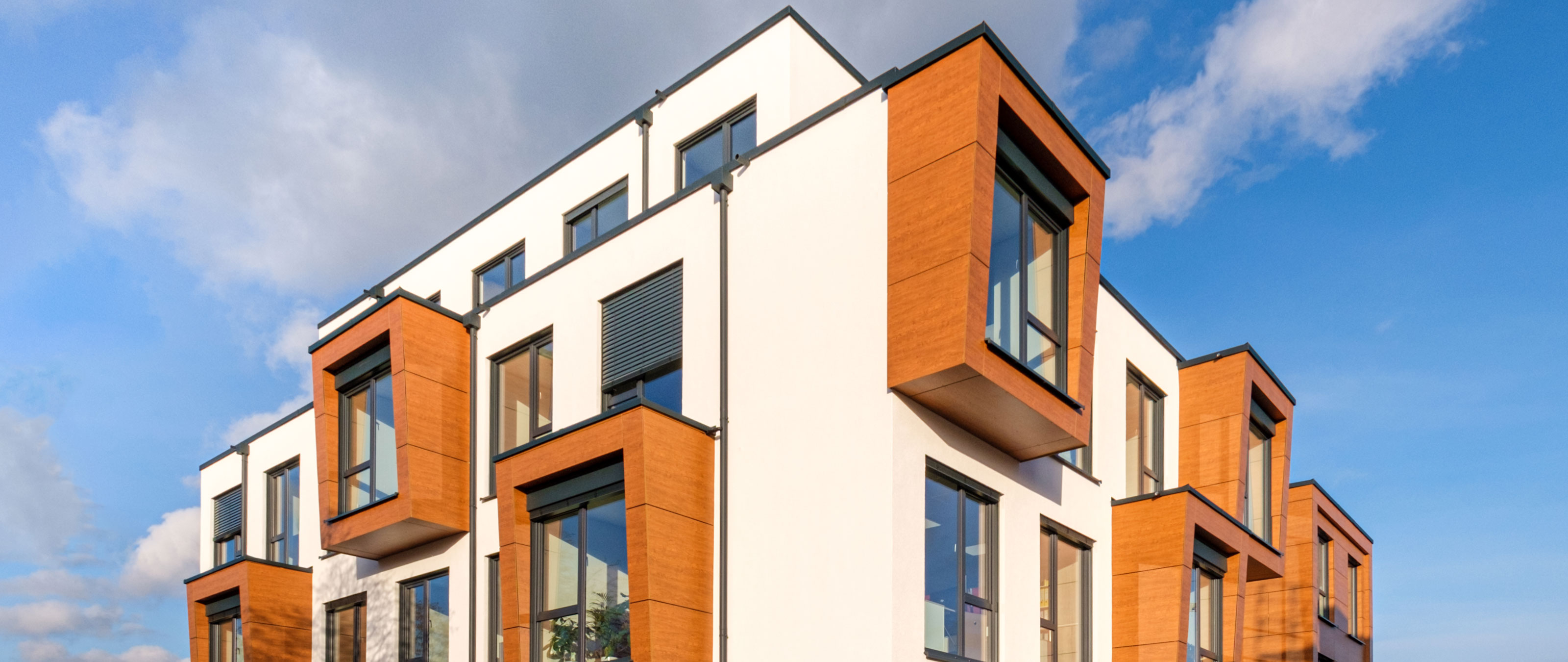
Stefan Höötmann doesn't like to be held up in his work. When he decided to automate element production in his company SH Holz & Modulbau GmbH, he would therefore not accept any delays due to delivery times: "We had the WEINMANN self-assembly tables right from the start, and we can wait a little for our multifunction bridge — a WALLTEQ M-380 — because we've been running production manually so far anyway." However, the businessman wanted his carpentry machine immediately: "My attitude was: If I can't get a Mercedes, I can get by with a VW. That's why I had already looked at a second-hand carpentry machine in Italy and was about to buy it. However, this remained purely an intention because Weinmann made Stefan Höötmann an offer that he couldn't refuse: "I was loaned another carpentry machine for the hall — for me, this was a great solution that was also handled in the best possible way: when my BEAMTEQ B-660 arrives, the loan machine will be collected and sold on. I love this kind of thing: when people look for solutions, instead of just reciting the problems. And this solution was perfect."
Starting out as a ridiculed exotic timber construction business
This was another chapter in a company history throughout which Stefan Höötmann had proved to be just as dynamic as when he is purchasing machines — founded in 1998 as a classic carpentry firm, his company, based in Lingen near the river Ems, began wood frame construction in 2004: "That was what we wanted, it allowed us to take the reins on our own orders much better." Although considered rather exotic in the region as a timber construction business, the company showed the astonished public "what can be done with wood." Following this motto, the company developed an excellent reputation — initially among private builders. Due to its proximity to the Netherlands, the company also "slipped" into modular construction for Dutch clients, as this construction method was already well developed over the border. "We enjoyed this even more," remembers Stefan Höötmann today: "There was an even higher level of prefabrication and we were even more independent of external tradespeople — for example, we weren't dependent on when window manufacturers or tilers could come to the construction site. This allowed us to do more and do it more quickly." This was reason enough to import the modular construction method into northern Germany, which was still largely clueless about the method at the time: "As timber and module manufacturers, we were laughed at in the region back then" — which may also have had something to do with the poor quality of the Dutch modular buildings. This was also noted in Lingen, which is why the modular construction was subsequently adapted to the higher German quality requirements.
Established as a modular construction company since 2015
In 2008, the breakthrough came with a commercial property for BP: "The company wanted a temporary office building for 120 employees for four years. We were awarded the contract and delivered a three-story modular building with 3500 m2 of usable space, the quality of which was so high that BP still uses it today." In Lingen, the experience gained from this project was "how much time and money we can save on a large-scale project. It's crazy!" Stefan Höötmann therefore decided to develop his company further in the direction of commercial construction. Although the financial crisis meant that the company initially had to set its sights somewhat lower, the time was used constructively to optimize the company's own modular construction system. In 2015, the company entered into serial modular construction of refugee shelters, and in 2016, it entered into a partnership with Vonovia, which wanted to purchase modular residential buildings from Lingen. "This was the starting point for rapid growth," says Stefan Höötmann in retrospect. We rented halls for module production—which requires a lot of space—and today we have a hall capacity of 13,000 m2 over four locations." The partnership with Vonovia came to an end and framework agreements with the major cities of Cologne and Hamburg replaced it, which the company regularly supplies with residential buildings at a fixed price. In addition, SH Holz & Modulbau GmbH now builds office buildings, schools, daycare centers, nursing homes and, hopefully, hotels again in the near future. In 2021, the company moved into its new representative office building, which it had constructed in modular design. In Lingen, the company is currently in the process of reorganizing the production processes in the halls. Stefan Höötmann has moved away completely from business with private builders: today, he only takes orders from a project size of at least 700 m2 of usable space.
Small team, big impact
The businessman focuses particularly on profitability: "The effort involved in a single-family home is not much less than that for a large building — for example, samples have to be provided for both. However, the turnover for a commercial construction is much higher. So I wouldn't have enough staff to make the same profit with single-family homes." This is not because of the general shortage of skilled workers, but because it is part of Stefan Höötmann's company philosophy to make a great deal of difference with a lean team: "We currently have 35 employees, about half in the office and the others in the hall." Stefan Höötmann uses subcontractors to manage large volumes with such a small team: "Our employees do just the element production and module assembly. If we don't have enough capacity, we also buy elements. We outsource the construction to tried-and-tested partners from the trade sector. This enables us to adapt our capacities quickly and flexibly, and to commission additional tradespeople for large orders if necessary, which is no problem for their companies given a lead time of six months." This is even more the case because modular construction provides tradespeople with a number of advantages: they work — in shifts, if necessary — under controlled and ergonomic conditions at a fixed, weather-protected location with short journey times. They can easily drive their materials to the workplace instead of spreading it over several floors on the construction site. These are advantages that the employees of SH Modulbau also benefit from: "No one wants to work on construction sites any more. At our company, field operations are reduced to 14 days two or three times a year, everyone likes to get out now and again. So we've never had any trouble finding new people. If we have a bottleneck, it's not the staff, it's the capacity of the hall."
Planning with affinity for the system
Stefan Höötmann also likes to work with external parties when planning — in the well-staffed office of SH Holz & Modulbau GmbH, only work preparation is completed and work plans created. It is important for the company to be able to start the project as early as possible: "This is absolutely essential for modular construction. This allows you to build chic, high-quality buildings — even tailored according to customer requirements. However, you still need a certain affinity for the system in the planning. We have just seen how important this is at a nursing home that was modified by an architect until it was no longer a modular building and we had to reject the order." This is despite the fact that the in-house modular system allows for very flexible construction of up to five stories. The modules have variable sizes up to 13.50 x 4.70 m, with the preferred width dimension being 3.40 m. "We can play within this framework, for example, we are currently building a school with large, open room modules and a ceiling span of 8.00 m. If modules don't work, we also use steel and concrete. For example, we would never build an auditorium from modules. We therefore have few restrictions on our orders — but there are also limits to flexibility." In Lingen, therefore, the planning is usually assigned to three planning offices that the company has been cooperating with for a long time. This is a process that was initially only accepted with a gnashing of teeth, but that has become established with increasing familiarity with the company. "Today, our customers plan with our planning offices without any problems — even though they know that the price will only be calculated at the end of the module planning and that at this point in time, from a practical perspective, they are no longer able to implement our plans with a conventional company."
Modular construction as a problem solver
Where does this leap of faith come from? "Because today we have our finger on the pulse, because it has become known that the construction method works excellently and that, in addition to a number of advantages, it also brings the customers greater security. It's like a car: It's planned and produced by a manufacturer, and if the manufacturer does this well, the customer knows exactly what they will get, when and at what price." Of course, that's not all. Another thing that customers appreciate from the module manufacturer from Lingen is that he acts as a problem solver. For example, when it comes to adding a story to a building in the city within an extremely short construction time and with minimal impact on the environment. In this case, modular construction means two weeks of large-scale construction, after which only small vehicles stop by now and then. You can spend a bit more money, especially since the customer, all things considered, is often saving money if you include potential problems in the price. As an example, Stefan Höötmann cites the addition of a story to a hospital: "A solid construction company was chosen there because their offer was 20 percent cheaper than ours. In the end, the hospital had to shut for several months due to noise, dirt and moisture, but the wages and salaries for the hospital staff still had to be paid. We would have been almost finished in two weeks. You can easily calculate which variant was cheaper in the end." A second example of the advantages of this problem solver mentality is an enclosed, 250 m long connecting walkway between two hospital buildings. It runs on pillars across a hospital site with heavy vehicle and pedestrian traffic. SH Holz & Modulbau quoted for 20 modules with 19 pillars for the project. After the pillar foundations have been prepared with small construction sites, the modules are to be installed on the site in 20 days — one pillar and one module per day. "A competing solid construction company quoted 80 pillars and a six-month construction period," remembers Stefan Höötmann. "Even though it was half the price, we got the contract without any problems." A further advantage of modular construction is the building contractor resources required. While, for example, the site manager of a city has to turn up regularly to the construction site for conventional residential construction projects, for a module project, he only needs to be available in the planning process and during handover. During the production phase, he has free capacity and can take care of other projects, which is why with modular construction, a city or residential property company can handle around four times as many projects with the same level of personnel.
Industrial construction
A key prerequisite for all these advantages is a consistent industrialization of the construction activity. Once it has been implemented, a modular building becomes a product that is manufactured under controlled conditions and delivered as a complete service to its destination. The construction activity on site is reduced to a short timeframe for assembly; the effect of external influences such as weather or negative interactions between the individual trades is reduced toward zero. In addition to planning and work preparation, the construction project focuses on the production of the modules in the hall, which should be largely automated and streamlined in line with the example of the automotive industry. Industrial construction then also makes it possible to use the synergy effects of standardization and series production consistently. It is not without reason that in the production of 13 identical refugee shelters, Stefan Höötmann experienced "that we were less prone to errors due to repeating the same processes and that we saved up to 30 percent in working time. That's what we measured, and that's the way we must go. With automated production, we will be able to exploit these synergy effects even more thoroughly in the future." Contacting WEINMANN, a machine manufacturer that represents automation in timber construction as part of the HOMAG Group, was a further step in the right direction from this point of view. For Stefan Höötmann, it is part of his efforts to "have all processes around the construction in his own hands and to consistently optimize them. In the production area, this means a faster workflow thanks to automated production, as well as higher quantities and a rapid response to peaks in demand. Not to mention the higher quality — we still made too many mistakes when we were producing manually." The carpenter also wants to make use of further streamlining potential in the field of module assembly in the future: "At the moment, we put the modules down in the hall, assemble them, construct them, package them and transport them away. This means that we only get the modules out of the hall when they are all finished — if there is a problem with one module, the entire hall is blocked."
This is a system that has worked for a long time but is reaching its limits with today's volumes. Therefore, the company wants to establish a slide system from 2023 onwards, which they can use to transport the modules through the hall. "They then come to the craftsperson who has a fixed station in the hall. This allows us to complete a module every day and store it outside." With this, SH Holz & Modulbau GmbH seems to have done its homework. However, Stefan Höötmann still thinks they have some catching up to do in the area of external trades: "The subcontractors also make savings due to the streamlined work in our hall. However, they have not yet recognized that at least part of these savings could be incorporated into an improvement of the cost structure." In addition, electricians and installers could also prefabricate cable or wiring harnesses and install them in the hall. "This would allow them to use additional cost potential, but unfortunately, many tradespeople still lack the understanding for this. Nevertheless, I am convinced that if we take further steps in the right direction in terms of module expansion and make intensive use of the possibilities of large-volume discounts, conventional solid construction will be less and less able to keep up with us." The rise of his company proves that the carpenter's visions must be taken seriously. He has contributed a lot to the conversation around modular construction now in northern Germany — everyone is talking about it and it is no longer considered a low-quality method of construction. He has secured a market position for SH Holz & Modulbau GmbH in which the company, as one of the very few suppliers, can concentrate exclusively on modular construction. Since the word has spread, the first imitators have started to appear in the region.
An article from the customer magazine performance 22 | 2023. Find more information here!
“In the production area, this means a faster workflow thanks to automated production, as well as higher quantities and a rapid response to peaks in demand. Not to mention the higher quality — we still made too many mistakes when we were producing manually.”
SH Holz & Modulbau
SH Holz & Modulbau GmbH started out as a traditional carpentry business, but has developed into an innovative modular room manufacturer over the course of recent years. For more than 25 years, the company has been specializing in using wood as a construction material. SH Holz & Modulbau GmbH was founded in 2009 as a specialist supplier of modular constructions. Since then, the company has implemented more than 100 projects. The company works closely with its customers to create residential buildings, offices and business premises, educational institutions and administrative buildings using advanced modular construction.
Learn more