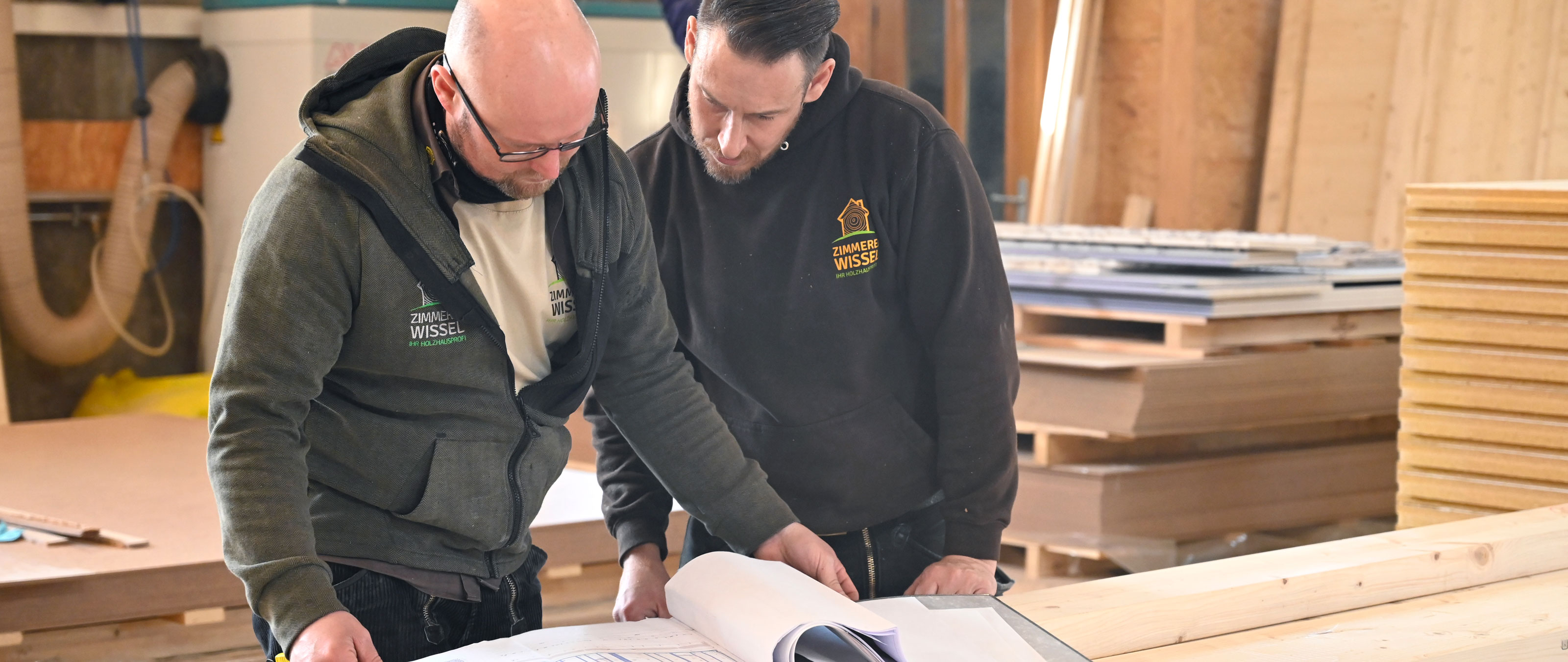
When visiting Zimmerei Wissel GmbH in Mömbris, a town in lower Franconia, you can expect to find a typical carpentry shop. Building on his father's timber construction business, master carpenter Florian Wissel founded Zimmerei Wissel GmbH two years ago and now employs two multifunction bridges, six journeymen and three apprentices. It doesn't look much from the outside, but this small facility houses modern machine technology and innovative timber construction. Two employees and two machines work hand in hand. While all of the beam processing for the roof and wall elements is performed on the carpentry machine, the elements are finished on the multifunction bridge.
The team at Zimmerei Wissel exclusively designs and builds unique products that are precisely tailored to customers' requirements, placing great importance on the use of ecological materials in the process. With six houses and one or two upward extensions to build in 2019, the carpentry firm already had more than enough to do that year. And demand continued to rise. It was this development that prompted Florian to replace his aging carpentry machine. He decided to contact a company he had not worked with before: WEINMANN, a manufacturer of timber construction technologies and long-standing expert in the field of prefabrication. This contact then brought Zimmerei Wissel into direct contact with a fellow carpenter whose used carpentry machine the firm could acquire. The advice and support provided throughout the purchasing and installation process was fantastic and, shortly afterward, the "new-old" WEINMANN carpentry machine stood in Florian's facility.
First the carpentry machine, then the multifunction bridge
The next step followed just three months later. Florian saw the WALLTEQ M-120 multifunction bridge for the first time when visiting the Dach+Holz trade show in Stuttgart: "It won me over immediately and I said to my wife that it was exactly what we needed. We did our sums and drew up some estimates over the next few days, and the logical conclusion quickly became clear." No sooner said than done, Florian decided to invest in the multifunction bridge. Stefan Rach, responsible for WEINMANN sales in southern Germany, visited Zimmerei Wissel to assess the premises and possible solutions. The part of the facility where panelization takes place is 11 meters wide and 25 meters long. With its compact design – the multifunction bridge is just 6 meters wide – the new machine found its current place in the carpentry shop. The machine technology was designed to make it possible to install a larger bridge later on. The solution therefore allows the carpentry firm to be flexible.
The WALLTEQ M-120 arrived just in time for Florian's 40th birthday and his employees, together with WEINMANN colleague Stefan Rach, immediately set about making him a birthday sign to mark the occasion.
The WALLTEQ M-120 is based on an 8-meter-long carpentry table. The frame work is created here as well as the elements. The table can also be tilted, making it much easier to remove and turn the elements. This is all the more important for the carpentry firm since there is no overhead crane. During day-to-day work, this makes the workplace considerably more ergonomic for employees. An example of this is post-processing of the finished element. Thanks to the tilt function, the panel joints are glued to the finished wall whilst upright. Many of the tasks that employees previously had to carry out while kneeling are now much easier. Creating good working conditions for employees was a particular for concern master carpenter Florian Wissel when he chose the new technology: "Another reason for purchasing these machines was to retain our employees into the future – not only our younger employees but our older ones too, who have an incredible wealth of experience. This is the right step to take to allow for our senior journeymen to stay with us until they retire."
Time saving of 35%
The carpentry machine and multifunction bridge complement each other perfectly during the production process. The carpentry machine cuts the pockets into the top and bottom plates, marking the positions for the individual studs and making them quick and easy to insert. Before investing in the WALLTEQ M-120, two people worked in wall production creating the frame work, laying the panels and attaching them. Today, most of the elements are manufactured by just one person. If a second person is ever needed – to put on the top and bottom plates, for example – the colleague responsible for beam processing will help. Thanks to the integrated vacuum lift, laying the panels onto the machine is no longer a problem: the required panels are simply removed from the material stack and placed on the element. The panels are then pre-mounted in place and the machine takes over the remaining work, such as attaching the sheathing and trimming the outer contour, window and door cutouts. Insulation is carried out using a blow-in system. The blow-in holes required for this are likewise made using the WALLTEQ M-120. Florian is delighted with the new work process: "The entire element production process is carried out to an incredibly high quality and at unbelievable speed. We've claimed about 35% of our time back and increased our productivity from six homes a year to eleven – with the very same team."
The multifunction bridge uses the CAD data to establish which edge and clamp distances it must adhere to. "The nails are positioned exactly where we want them. The nail is inserted exactly according to specifications and the edge and nail distances are observed precisely, which is almost impossible by hand. This process means that the elements' fitting accuracy is incredibly high. The construction sites have been running even more smoothly since we got the machines. Everything that's been prefabricated in the shop is taken to the construction site and set up there — it simply slots together. This saves us an enormous amount of time on the construction site and our employees are now much more relaxed at work."
Visible elements with wooden nails
Individual customer specifications with high quality requirements are the order of the day at Zimmerei Wissel. This makes quality an even more decisive factor for Florian Wissel in addition to time savings when working with the multifunction bridge: "It's a matter not just of getting a few extra minutes for each element, but also of maintaining our exacting quality standards. When you look now at everything we can produce with the two machines, it simply wouldn't be possible to make these by hand to this level of quality in this amount of time."
Visible wooden elements are a particular feature of the projects. Visible three-layer panels are installed in load-bearing elements, for example as an inner wall, roof or ceiling element. To do this, Florian has equipped the multifunction bridge with a wooden nail unit: "When working with exposed wood, we only use wooden nails. We're able to achieve a really nice finish with the multifunction bridge. The wooden nails are pushed in cleanly at defined intervals down to the exact millimeter." The multifunction bridge with integrated wood nailer is currently the only one of its kind in Germany.
As mentioned earlier, Zimmerei Wissel uses purely ecological building materials. For example, its outer walls are made of bio-fiberboard panels that are completely free of glue. As this material is extremely hard, the nails are very difficult to insert and processing is likewise heavy going. "With the WALLTEQ M-120, we've been able to solve these problems completely. The bridge fastens and processes this material with ease and with the same good result every time, no matter whether the panels are made of bio-fiberboard, OSB or Fermacell."
New ideas and projects
Florian Wissel is a master carpenter with a passion for what he does and is always open to new ideas and projects. "I'm always looking to try new things. Thinking up and developing new ideas, working out the fine details together with our customers and the architects – I love all that, it's so much fun. The two machines have opened up even more possibilities for me and resulted in some extremely interesting projects." A self-supporting staircase is one example of this. "That staircase is the centerpiece of a beautiful showcase project." The recesses for the stairs were cut into the interior wall precisely with the multifunction bridge and the recesses in the beams were made using the carpentry machine. "This project provides yet another perfect example of the multifunction bridge and carpentry machine working in harmony."
An article from the magazine der Zimmermann, issue 5/2020. You can find more information here.
Videos
Please confirm that when you use YouTube, data such as your IP address, browser identifier and similar may be transmitted to Google.
» Privacy Policy
Carpenter Florian Wissel of Zimmerei Wissel GmbH gives insights into his company, where he works with machinery of WEINMANN.
“The entire element production process is carried out to an incredibly high quality and at unbelievable speed. We've claimed about 35% of our time back and increased our productivity from six homes a year to eleven – with the very same team.”Florian Wissel, managing director Zimmerei Wissel
Zimmerei Wissel GmbH
Zimmerei Wissel GmbH in Mömbris, a town in lower Franconia was founded 1983. The team at Zimmerei Wissel exclusively designs and builds unique products that are precisely tailored to customers' requirements, placing great importance on the use of ecological materials in the process.
Website