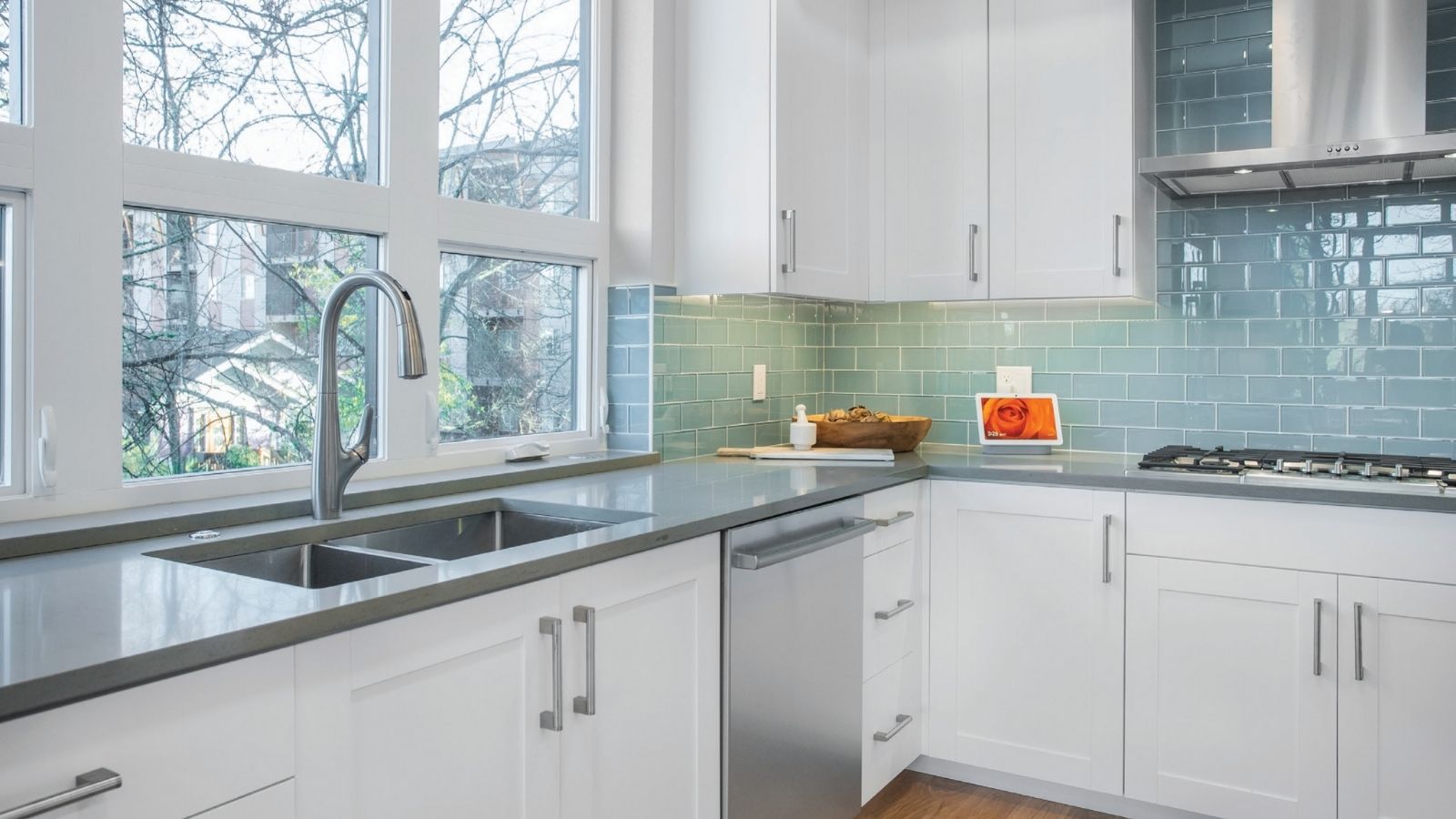
Established 50 years ago in Eugene, Oregon, Lanz grew from a handcrafted custom cabinetry to a progressive cabinet manufacturing company oriented in the western US multifamily housing market. With SCHULER Consulting the company has now found a partner to guide it through the next stage of development to find solutions that would enable it to grow with market demands.
Streamlined production – How it’s done so far
Lanz produces face frame and frameless kitchen packages as well as quartz and granite countertops. Within three factories on over 160 thousand sqft, the company manufacturers up to 7,500 cabinets per week with 280 production employees. Each cabinet is produced for a specific reason, meaning for a specific order and has his own requirements. With a lean manufacturing process parts flow continuously through the different process steps. An MES (Manufacturing Execution System) is controlling components running through the factory. Today the linear flow in production ensures a solid process stream. Leading from cell to cell, connected via roller conveyors it goes over material storage, cutting or nesting, drilling, assembly, and shipping. A code is scanned at each machine for accuracy of processing.
In the multifamily housing segment, Lanz Cabinets strives to be the supplier of choice in the western US market but without automation there is no possibility to be competitive in the next few decades. Therefore, the current way of production had to be optimized in favor of enlarging production capacity without increasing production space and labor. “We needed help with taking our manufacturing to the next level and we knew involving the team at Schuler Consulting would be the only way to accomplish this” explains Kyle Bressler, president of Lanz cabinets.
Reaching for the automated future – How to get there
"We used data driven optimization processes to develop specific solutions for Lanz", explains Martin Kintscher, Regional Manager at Schuler Consulting. Within the first phase of the project as much data as possible needed to be gathered, sorted by each relevant production area. Next, big data was transformed into smart data. "Meaning, we filtered and analyzed the collected data in the context of previous set goals. The main goals were to increase the overall automation level, raise production capacity and lower manufacturing costs. After collecting and analyzing data, we worked out different options to achieve the project goals and presented it to the project team at Lanz. The company decided to invest in three new automated storages, which allowed the production processes to be spatially reorganized and certain work steps to be brought closer together (e.g. integrating the saw within the automated storage system)."
Making automation a reality – How it works
With the solution worked out by the Schuler Consulting team, Lanz is now taking the next step into the future. The company already produces with a high-tech machine such as the Homag CNC processing center "CENTATEQ", providing the modern way of cutting highly flexible and individual cutting patterns. Integrating the cutting process into the material storage now brings more flexibility into the production: The automated storage system stocks the panel material, feeds the machines, and sorts its stock to the most efficient production way. Combining two process steps like storage and cutting leads to an increase of productivity and at the same time offers the possibility to deploy employees elsewhere. It reduces production costs by saving time and boosts the performance of the connected machines by feeding them just in time. The total output of production will increase about 33%, allowing Lanz to hit a new benchmark by producing 10,000 cabinets per week. Lanz is expecting to begin implementing these changes in mid-2022. The newly gained production flow increased production capacity while also reducing production costs.
Even more to come? – How it could continue
"With Schuler Consulting's customized solution developed for Lanz, we saw the opportunity to increase capacity even further in the future", says René Hanuscheck, Consultant in Schuler's Team America. Maintaining the entire production flow, we can generate a cell production where each process step is seen as its own production cell with an input and output. Here it is a question of two different methods to automate even more. Keeping the cells itself with manual material infeed but automated roller conveyors ensure a straightforward process flow. To bridge the path from one machine to the other, AGVs are more flexible and individual in their transportation ways. Automate the whole process line is not common yet but may be standard soon. Therefore, jumping right into future, the second method could be a further step for Lanz to automate its production even more. A fully automated solution where almost everything moves, loads, and unloads without manual labor at all. Robotics and KI are state of the art, we should not forget them in our industry.
Authors: Martin Kintscher (Regional Manager America, SCHULER Consulting) and René Hanuscheck (Team USA, SCHULER Consulting)