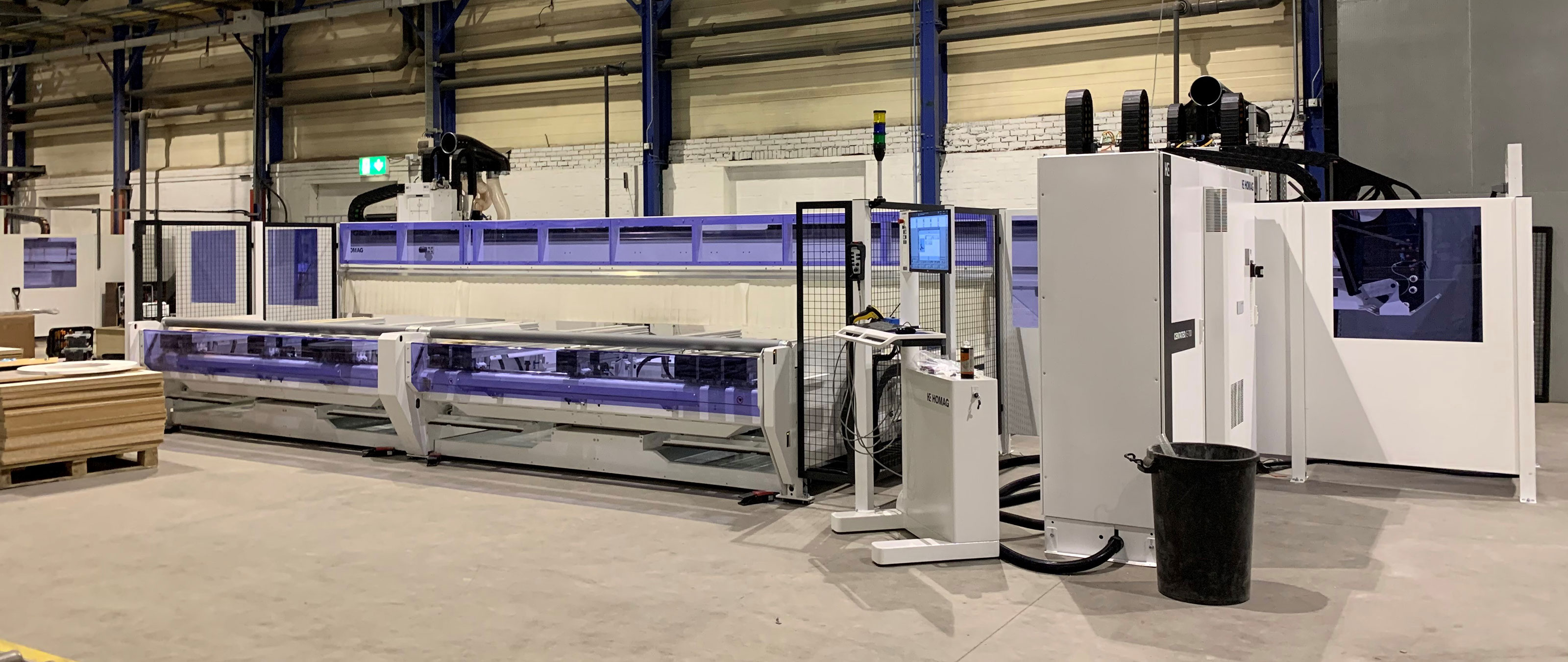
Established in 1976, Starbank Panel Products is a laminate and wood-based panel fabricator for the interior fit-out industry. Based in Newton-le-Willows on the borders of Lancashire and Merseyside, this family-run business specialises in manufacturing a wide variety of finished and semi-finished products for projects that span multiple industries.
When it comes to product mix at Starbank, no two weeks are the same and they can range from intricate healthcare and educational furniture to large scale fire door and case goods manufacture for the construction industry.
HOMAG technology has been a vital necessity for business growth
Since its incorporation, Starbank has invested in 22 high-performance HOMAG machines. These have been crucial for the production of its high-quality products and paramount for the success and growth of the business.
The company’s management has always taken a forward-thinking, latest technology approach when purchasing new equipment, focusing purely on high-specification solutions.
This tactic has delivered tremendous flexibility to the company, enabling it to produce a wide variety of panel types to a very high quality. Starbank’s most recent CNC machining centre investments, a HOMAG CENTATEQ T-700 and a CENTATEQ E-700, are no exception.
Keeping one step ahead of the market
John McCaffrey, Business Development Manager at Starbank Panel Products explains: “Previously, we had invested in a multi spindle BOF 700 series, a one off in the UK, which served us well for processing large batch volumes, but over the years market demand gradually moved to smaller batch production. As a result, we needed a machine that was more flexible and efficient in handling batch size one, hence our decision to opt for the HOMAG CENTATEQ T-700 CNC.
“With regard to the CENTATEQ E-700, this is a direct replacement for one of our older HOMAG BAZ 723 CNC’s, a machine that believe it or not we bought way back in 2004. This machine had put in a lot of production hours for us on often on two shifts per day. These gantry machining centres with their edgebanding units, multiple tool changers and flexible beds are huge investments, but they allow us control from batch size 1 to batch size 10,000 if needed. It really is a testament to how robust these CNC’s are.”
HOMAG CNC processing center CENTATEQ T-700 and CENTATEQ E-700
“One of the reasons for selecting the CENTATEQ T-700 was the growth of compact laminate components we are now producing each week. To successfully manufacture high end detailed components and large volume work surfaces, with this material, it requires a large, robust and technically advanced machining centre.
You only get this performance with the big gantry CNCs and the T-700 is perfect for us. We specified a 4-axis model with extra tooling carousels for bespoke applications to give us the capacity, flexibility and edge we wanted.
“The CENTATEQ E-700 is another powerful gantry CNC machine, but with the benefit of adding an EVA/PO edge banding unit. This gives us the ability to run a multitude of materials including the challenging 3D acrylic edging, setting us apart from our competition. As with the T-700 we opted again for a 4-axis model as this enables both synchronous or independent processing of panels depending on configuration.
“Quality is always a critical driver for Starbank and a source of continuous improvement. The power of the spindle heads is paramount to the performance of the machines when running a multi shift operation. This, coupled with the large bed size of both models, gives us a unique advantage in the market.
“Naturally, we did consider other CNC machinery manufacturers. However, as all our CNC machinery operates on the same HOMAG software platform, it made sense to stick with HOMAG and their latest technological advances. It means our operators can easily switch between machines without having to learn new programming or machine skills.
“Our people really like the latest powerTouch and woodWOP 7.2 software. The tool databases are a lot more efficient when adding and changing tooling and the upgraded graphical user interface is a real bonus. The majority of our HOMAG machines have been networked for many years and in the future we’ll be looking to take advantage of the Homag ‘Tapio’ platform to maximise our Industry 4.0 approach to running a smart factory which really is becoming a reality for Starbank.”
A forward-thinking company
“The Darbyshire family who own Starbank are always looking to future production trends, and as a business this gives our team an advantage whilst researching and procuring the latest technology. Phil Darbyshire, Starbank’s Managing Director and Paul Atkinson, Production Director, have a very close working relationship with Jon Lawman their HOMAG account manager and often visit other facilities to learn more about the capabilities and benefits of new machine technology.
“The relationship we have with Jon enables him to have an in-depth understanding of Starbank and the types and variety of panels we produce. There is genuine trust between the two parties, and Jon would never push us down a road that didn’t work for us”, explains Phil.
A skilled production team and efficient machinery delivers high-quality finishes
“Starbank operate both a day and a permanent night shift meaning machines are potentially running for 16 hours a day. Sometimes during the summer months, we need to be operational 24 hours a day. The excellent extraction and cooling systems on these CNC machines enable us to run for longer periods without any issues.
“We believe the finish of our products is second to none which is partly down to the machines and a reflection of the vast knowledge and skills of our programmers and operators. We are extremely proud of the work our team produces week on week, without fail.
“The new CENTATEQ CNCs have given us much more flexibility. A normal day might see us processing several types of materials with varying panel lengths and thickness. We’re not set up for example as a kitchen manufacturer would be where they have machines that are in the main producing the same thing day in and day out. The ability to switch and change panel type is a vital requirement for both our sales and production team considering the variety of industries we serve.
“Our multi-million euro investment in these two new machines will firmly place Starbank at the heart of panel outsourcing in the UK for many years to come as we strive to continuously improve for our customers' benefit.
There’s no doubt we would not be where we are today without the right machinery and team driving our investments” concludes John McCaffrey.
If you would like a demonstration or more information on HOMAG’s range of CENTATEQ CNC processing centres, please contact HOMAG UK
“Our multi-million euro investment in these two new machines will firmly place Starbank at the heart of panel outsourcing in the UK for many years to come as we strive to continuously improve for our customers' benefit.”John McCaffrey, Business Development Manager, Starbank Panel Products