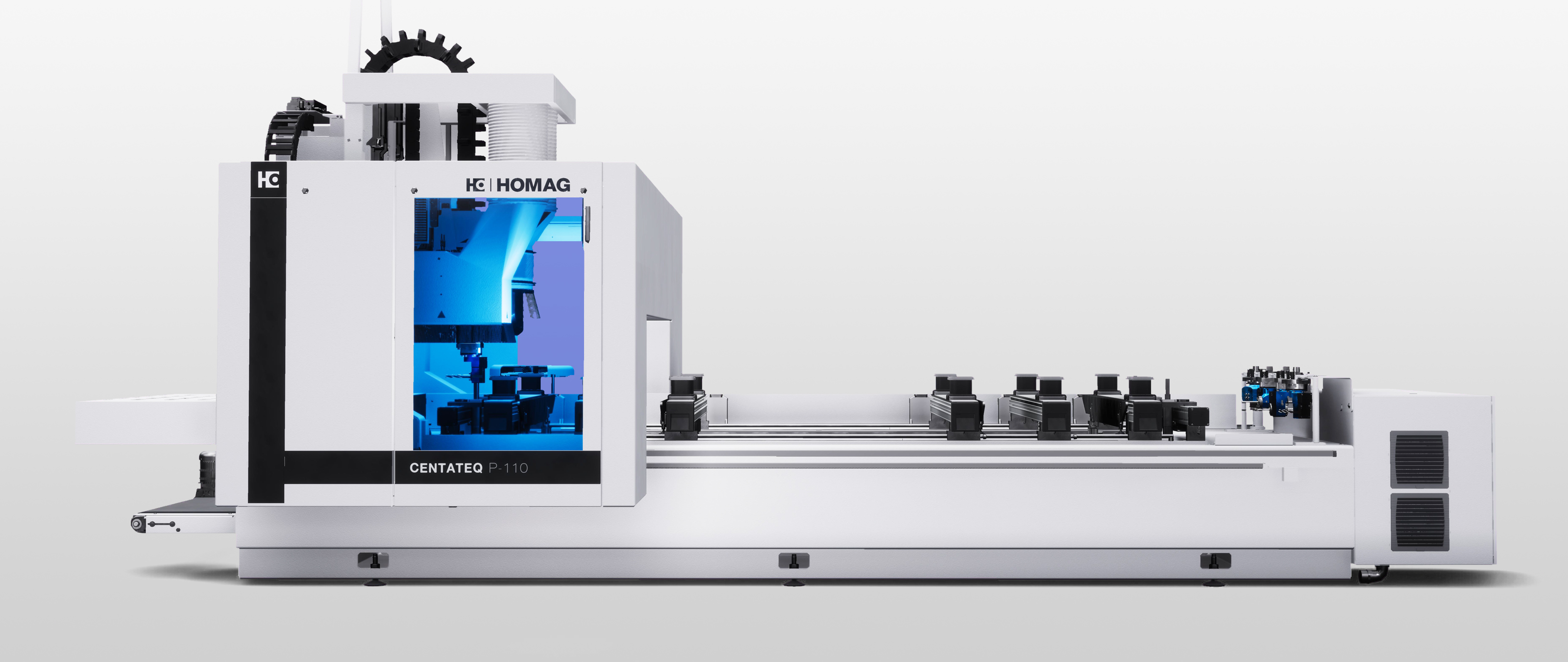
An increase in workload and orders, however, saw the company need to expand its workforce and production facility to keep up with demand.
“It has always been in our business plan to invest in a CNC and the need for expansion meant we decided to automate production processes ahead of our original timeline”, explains Allan Jackson, production director at Quest Joinery. “Once we agreed it was time to invest in new machinery, we spent a couple of months researching the market thoroughly.”
Making the right choice with HOMAG
“Of the brands we evaluated, HOMAG was the most accommodating. They arranged for us to visit another of their customers, East Coast Fittings. There we were able to experience the HOMAG Venture 109M CNC in a working environment. In addition, we received a full CNC machine demonstration at HOMAG UK’s Castle Donington showroom.
“The concept of having a CNC machine was new to us, so it was essential that we picked the right model for our facility. With our prior knowledge and experience of CNC technology being limited, it was fantastic to be able to speak to the machine operator and ask any questions we had. This all helped to give us the confidence we needed to make the right decision.
“The HOMAG team were very professional and had a lot of time for all our questions. They displayed the same caring approach to business as we give to our customers. This was very reassuring and made the decision to purchase a HOMAG BMG 114 CNC machine easy.
“The confidence we had in HOMAG and its machinery meant we were excited, rather than nervous, to be the first company in the UK to install the new Venture BMG 114. Naturally, we thought we might experience some teething troubles, but actually we didn’t encounter any issues at all. The BMG is proving to be a fantastic addition to our facility.”
The BMG 114 CNC – superior technology
“HOMAG has a reputation within the market for being a step ahead of the competition. This was clearly evident as the BMG 114 has no limitations compared to some of the other CNCs we viewed. Although it wasn’t the cheapest machine we looked at, the BMG 114 was a much higher specification than we were originally looking for and the additional features have been a welcome bonus, more than justifying the investment.
“As a bespoke joinery company, the versatility of the machine was really important to us. On a daily basis we produce a mix of work including doors, wall panelling, reception desks and units. So, we chose the pod and rail system because we do a lot of solid work as well as bespoke intricate projects which require high levels of precision.
“In terms of tools, we started with a basic set, the idea being to add more tools as we progressed. We initially invested in cutting tools and an aggregate head; this gave us the ability to cut shapes and carry out complex work, such as cutting locks out of door sets and producing intricate joint details. Our products use a wide variety of materials including leather and brass, and the BMG 114 ensures accurate cut outs for these inserts.
“What really impressed us about the BMG 114 is the ability to operate it from all four sides. It means you don’t need to worry about where you place the machine, as it’s accessible from every side. This is great for a smaller factory, especially as the machine itself already has a 15% reduction in footprint size. So even placing the CNC in a corner space is no longer an issue.
“In addition to this, the ‘Bumper Safety Rail’ technology means the machine automatically stops itself if the moving gantry is about to come into contact with operators or any other obstruction. If the machine does come too close and it stops, there are no delays in production. Once the obstruction has cleared, it instantly restarts itself after a couple of seconds without the need for any re-programming. The technology removes the need for any fencing or matting which means you can work all round the machine.
“The BMG 114 is running HOMAG’s woodWOP software. Our operators visited HOMAG UK at Castle Donington for software training and thought the training course was comprehensive. Despite having a few weeks gap between completing the training course and the installation of the machine, the operators were still able to get to grips with it really quick. It is very clear that the software has been designed with the user in mind and has been kept simple and intuitive.”
A 35% increase in production for Quest Joinery
The CNC has not only increased production output by 35 per cent, but it has also allowed us to expand our product offering. It has enabled us to be able to take on larger projects and we are now completing work in-house, such as sign writing and engraving which we previously outsourced. Without this new machine, we simply would not be able to turnover what we are doing today.
“Previously, parts of our production were carried out by hand, but the CNC has reduced manual labour levels for us. As a result, our repeatable accuracy and quality has increased which in-turn has led to a lower volume of waste. We are producing the same items before in a fraction of the time and the quality is in a totally different league from where we were.
“In terms of paying for the machine, we used HOMAG finance to arrange a five-year payment plan. They came highly recommended within the industry and the terms were simple and easy to understand. Now the BMG is operational, we predict it will pay for itself within 30 months.
“As part of our expansion, we also invested in a Ambition 1650 edgebander with both hotmelt and PU glue options. This was to replace our smaller and older existing edgebander. It will provide us with the capabilities to further expand our product range to include fire rated doors,” concludes Allan Jackson.
If you would like more information or a demonstration of any of the HOMAG range of CNC routers and machining centres, please contact HOMAG UK on 01332 856424.
“What really impressed us about the BMG 114 is the ability to operate it from all four sides. It means you don’t need to worry about where you place the machine, as it’s accessible from every side. This is great for a smaller factory, especially as the machine itself already has a 15% reduction in footprint size.”Allan Jackson, production director at Quest Joinery