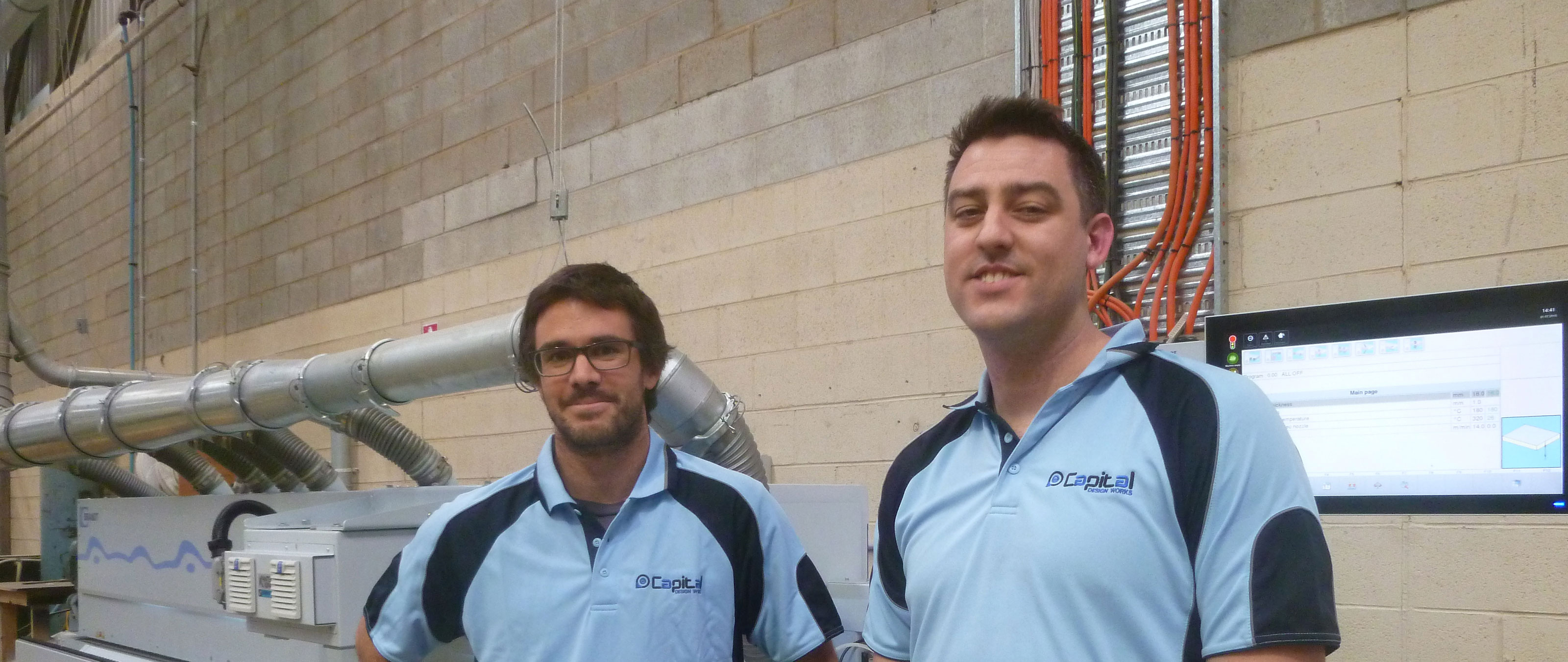
The article was first published in the AWISA Magazine, Spring edition 2016.
www.awisa.com
With 12 staff, the number of employees has been constant for years even though they doubled their capacity. Thanks to smart investments, they were able to move their labour more and more into the office where they can spend more time with programming work.
Having moved to the new premises in Revesby early this year, they grew from 300 square metres to now 1,700 square metres. Company owner Matthew Kitchin, shopfitter by trade, has gained work experiences in another joinery before he started the business in 2011.
Since then, Capital Design Works supplies joinery work for pubs and clubs. While the majority of their clients are in NSW, they also deliver to the market in VIC and QLD. From consultation and design to construction and installation, they are using the best available methods of production.
Growing big
Looking back at the beginnings when they started with just a panel saw, an old pod machine and an edgebanding machine seems so far away as Matthew remembers.
The latest purchase includes a Brandt Ambition 1440 FC edgebander with airTec, HOMAG’s hot air technology. It was just the right time for an upgrade as the old edger caused problems. “We had other ones before and always had issues. This time I wanted to get the best, a machine that works and is reliable. The panels come off the machine without the need for further processing”, Matthew says. “I wouldn’t buy a machine without premilling anymore. We eliminate laminate chipping, chatter marks from machining and material swelling.”
The Ambition 1440 FC basic machine also features a joint trimming unit, an EVA gluing unit, an end trimming unit and a two-motor corner rounding unit. The perfect finish is obtained by a radius scraper, a glue joint scraper and a buffing unit.
Capital Design Works were able to speed up their production processes massively. “We now have improved from 3 minutes per metre to 5 metres per minute,” Matthew says.
The competitive edge
For even better results, they decided to invest in the hot air unit airTec. Hot air systems, such as Brandt’s airTec, are simple techniques where the edge and work piece are joined together by using hot air. Special edge materials which consist of a hard décor layer and a meltable functional layer need to be used. The functional layer is melted by the airTec activation unit and the edge is pressed onto the work piece. “With airTec, there’s no glue line on white gloss boards. This gives you the competitive edge which was the reason for the purchase,” Matthew says.
If the airTec unit is not needed, it can be easily switched off. The way the airTec reactivation unit is installed makes it possible to either work with the standard glue application unit or with the airTec system.
Not to mention the powerTouch controller which allows users to swipe, tap, zoom and scroll. Production supervisor Jason Wilson says, “The touchscreen user face is great; I can control the whole production line.” The powerTouch operating concept from the HOMAG Group combines design with function to create a totally new generation of control that feels like the tablets and smart phones we use every day.
The system centres on a large multitouch monitor which allows operation of the machine functions by direct touch. New on-screen help and assistant functions significantly simplify working – while standardised operating elements and software modules ensure a uniform operating experience at any of the HOMAG Group machines.
Precise nesting
In 2014, Capital Design Works upgraded to a WEEKE Vantage 100 nesting machine with additional auto loading and unloading and label printing. Matthew appreciates the new capabilities the machine brings to the business, “Previously, we had to load the sheets manually, now everything works automatically. We now cut everything on the nester and it’s more accurate. We can use bigger sheets as well. In summary, we achieve more capacity and a better end product.”
Jason values the ease of handling the operating software and the alerts that come up if something needs attention. “The machine tells you exactly what to do and, at the same time, we have the ability to control the suction zones. This is all a massive improvement.”
After the success of the Vantage 100 model, HOMAG now offers a similar nesting machine at an even more competitive price, the WEEKE Vantech. “This is the perfect time to purchase a CNC,” says HOMAG sales rep Ryan Slater, “we offer ex stock machines for prompt delivery.”
Service makes the difference
When Matthew started considering HOMAG machines he not only looked at the machine alone. “Service plays an important role as well, and HOMAG’s service is pretty good. They have very good service technicians.”
With the right set up, Capital Design Works looks positively into the future. “We’ve been growing every year. With the software and the right people and a quality product that comes off the machine we are right on track,” Matthews says. “We constantly look internally to improve ourselves, which makes the product better. This is our way to differentiate ourselves from the competition.”
“This time I wanted to get the best, a machine that works and is reliable.”Matthew Kitchin, Owner, Capital Design Works