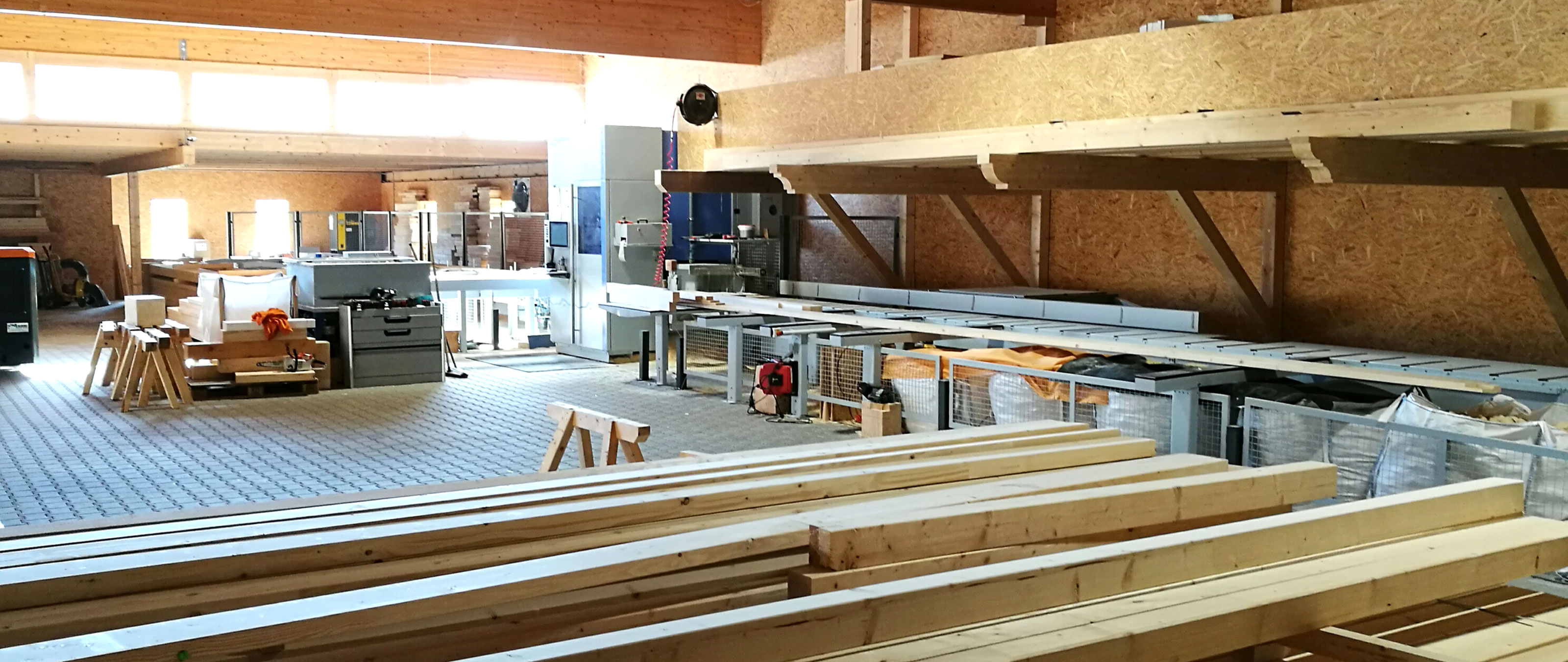
Even a small company with eight employees can achieve great things. It may return the same sales as a competitor with 15 employees; it may even make a slightly larger profit in comparison. At least this is how Marco Büsing, who used to have significantly more employees in his carpentry firm, sees things: "And back then, the sales weren't any higher and we didn't earn any more money."
From manual to automated
Between then and now there has been a change from manual to automated production, which is reflected in the addition of a WEINMANN WBS 140 in the beam processing facility. The successor to this carpentry machine, a WBZ 160 powerSIX, has already been ordered from Lonsingen.
One of the reasons that Marco Büsing decided on these two carpentry machine was due to the required footprint: "They simply fit better in our facilities than the machines provided by competitors, and they also require less preparation."
Another factor was the processing quality. In this regard, the WEINMANN machines made an excellent impression on Marco Büsing. "Although we can 'only' process formats of up to 200 x 455 mm here, larger beam crosssections are only requested every few years anyway. And then there are alternative solutions."
Before his company, situated in Barssel in Lower Saxony, purchased the WBS 140 two and a half years ago, the roof trusses were produced in the traditional way with a manual circular saw and drilling machine.
High level of prefabrication, quality & reliability
However, even back then, Marco Büsing planned all roof trusses with a CAD program from Weto, which he has been using intensively for 15 years. "In those days, the planning wasn't as detailed as it is today because in manual beam processing, you can correct a lot of things during processing or even on the construction site. By contrast, today I have to plan precisely as part of the work preparation. Alterations should no longer be necessary after the beam has been processed."
This is because, amongst other reasons, the Büsing firm does not join in with the general price war in a region with a high density of beam processing suppliers and strong competition. Instead, it relies on higher quality compared to competitors: "Therefore, we're perhaps EUR 0.20/m more expensive, but we offer our customers services that a competitor cannot provide or charges extra for."
Customers are generally construction companies from the conventional solid timber construction field, and Büsing supplies them with around 100 roof trusses for residential houses each year. In this business, besides quality, it is primarily reliability that counts, which is why Büsing has to be able to rely on his production system: "On one hand, it's important to know that the order going through the WBS 140 today can be delivered tomorrow.
On the other hand, clearly defined production times make our medium-term order planning easier. However, we rely less on the software calculations and more on our experience in this regard. Ultimately, the software cannot predict that a truck has to be unloaded in-between and that the machine is therefore at a standstill for a while."
The special "services" that Büsing refers to are primarily a high level of prefabrication with equally high precision: "When our customers can see how well our components are prepared, how fast and easy everything can be assembled, and that there is practically no post-processing involved, then we create a correspondingly good image."
Perfect interaction between software and machine
The first step towards creating this image is the CAD planning of the entire roof using Weto Viscon V10. Büsing generally performs this task himself but does have two employees who have experience in running this program and can deputize if required.
What is surprising is that none of the three have attended any training on the program: "When I first started to use this software 15 years ago, it was called 'Easy Abbund', and this name was very appropriate: the software really is 'easy'. Over the years I learned how to use the program via the 'learning by doing' method.
As a complement to this, the wupWorks software from WEINMANN is excellent. It converts the BTL data from all common CAD programs into CNC programs fully automatically." The transfer and conversion of the data is automatic and therefore no further postprocessing is required.
If required, the user can of course adjust details to the individual requirements of his company during processing. For example, in the automatic tool assignment he can replace a saw with a trimmer and define this as standard for future processing. For this purpose, the tools, processing steps, and workpiece are shown in the program's graphical display, which means that the user can check the result on the user interface before starting the machine.
With little effort, Marco Büsing can specify individual roofs in Viscon V10 based on various predefined standard forms and then transfer them to the WBS 140. The same applies for gables and dormers in various forms. This allows a wide range of forms of dormers up to shed dormers to be entered and executed easily, as can valley rafters, roofs, thick board roofs etc. He can also define standard details, such as a form of dormer common in a particular region, as a default setting in the CAD program.
Büsing admits that other CAD programs may be able to do more, but that "they would require extensive training. The deciding factor for us is that with our CAD program, we almost never reach our limits. Of course, we don't plan any complicated hall roofs but rather roofs for detached houses where the demand is for standard architectural and design solutions."
Solving a personnel problem
Nevertheless, Büsing does not see the company as a supplier of standard components because the level of prefabrication usually provided by the company is significantly in excess of the regional standard and extends to prefabrication of the roof battens. "When our roof truss arrives at the construction site, the fascia boards are also ready and the roof tile spacing has already been allocated accordingly. This means that our customer doesn't have to do a lot of calculations — provided that they give us enough time in the startup phase and notify us if there are any changes in the roof tiles during the planning."
The fact that the company earns more money with this level of prefabrication despite the greater effort involved in the work preparation is something that Marco Büsing notices regularly in the final costing: "The better prepared we are and the more precise we are in loading, the more we have left at the end."
Loading is performed by the two employees who are responsible for operating and supplying material for the WBS 140 in the production facility. Because the WEINMANN carpentry machine is equipped with a fully automatic transport system, these two employees have free capacity. They can even screw the roof components together to a certain extent to significantly reduce the assembly time at the construction site.
This saves both time and money and also solves a massive workforce problem for Marco Büsing: "If we had enough qualified craftsmen for assembly at the construction site, we might not have got to this point. As it was, we were forced to continually increase the level of prefabrication in order to minimize the error rate and the risk of accidents at the construction site."
Problemfree data transfer
Today, despite the low volume of personnel in peak times, a truck leaves the company's yard every day and the truck from the previous day returns and is loaded again straight away. This is a cycle that does not leave any room for malfunctions in the interplay between the CAD software and the machine.
But what happens when something does go wrong? "We generally don't have many problems in that regard," explains Marco Büsing. "For one, this is because we think through every detail of what we want to produce on the WBS 140 in the peace and quiet of the office.
Secondly, wupWorks is very reliable because in the event of any issue, it issues an error message at a very early stage and stops the processing if there is an impending collision or a component cannot be produced completely."
Greater capacity & new work opportunities
So everything works well? "In principle, yes. We are very satisfied with the quality of our WBS 140 and other companies who we supply with processed beams now also share this opinion. However, we have now reached our limits in terms of sawing capacity.
This is why we are buying the WBZ 160 powerSIX, which significantly reduces the processing times even further. This gives the employees in the production facility more time for preassembly and loading. At peak times, that means much less stress."
The additional processing opportunities provided by the underfloor unit are also very welcome. In the processing of beams for roof trusses, this leads to a significant time saving. Equipped with a 6.6-kW side milling cutter and a 7.5-kW drive unit for finger trimmers, dovetail trimmers, and drills, this unit allows six-sided processing of components without any tilting and thus makes material handling easier.
The WBZ 160 powerSIX also has a main spindle, a 12-slot tool changer, a five-axis saw, and a high-resolution positioning system, thereby enabling almost unlimited high-precision component processing.
Marco Büsing is also very happy with the cut optimization — according to the manufacturer, the degree of usage is up to 98 percent. To minimize the time lost when changing tools, the carpenter generally works with 13-m lengths of unprocessed material: "So if we need three components that are each four meters in length, we perform each process step three times for this type of beam before we change the tool. At the end, we then separate the beam into the individual components.
Of course, with this working method we have to make sure that our remaining wood is used in a prudent manner." This is a problem that his new machine may possibly eliminate.
Published in Bauen mit Holz 11 / 2016
Many thanks to the editor Markus Langenbach and Dr. Joachim Mohr
Many thanks also to our customer Zimmerei Büsing
Pictures: Zimmerei Büsing and WEINMANN Holzbausystemtechnik GmbH
“On one hand, it's important to know that the order going through the WBS 140 today can be delivered tomorrow.
On the other hand, clearly defined production times make our medium-term order planning easier.”Marco Büsing, Büsing Zimmerei GmbH
Internal growth
Marco Büsing founded the Büsing Zimmerei GmbH on the 01.09.2008. Eight employees work for Büsing in the fields of timber framing, building refurbishment and interior constructions. The main area is the region of Barßel. In addition to traditional carpentry works Zimmerei Büsing offers individual solutions for new constructions and refurbishments.
Webiste of Zimmerei Büsing