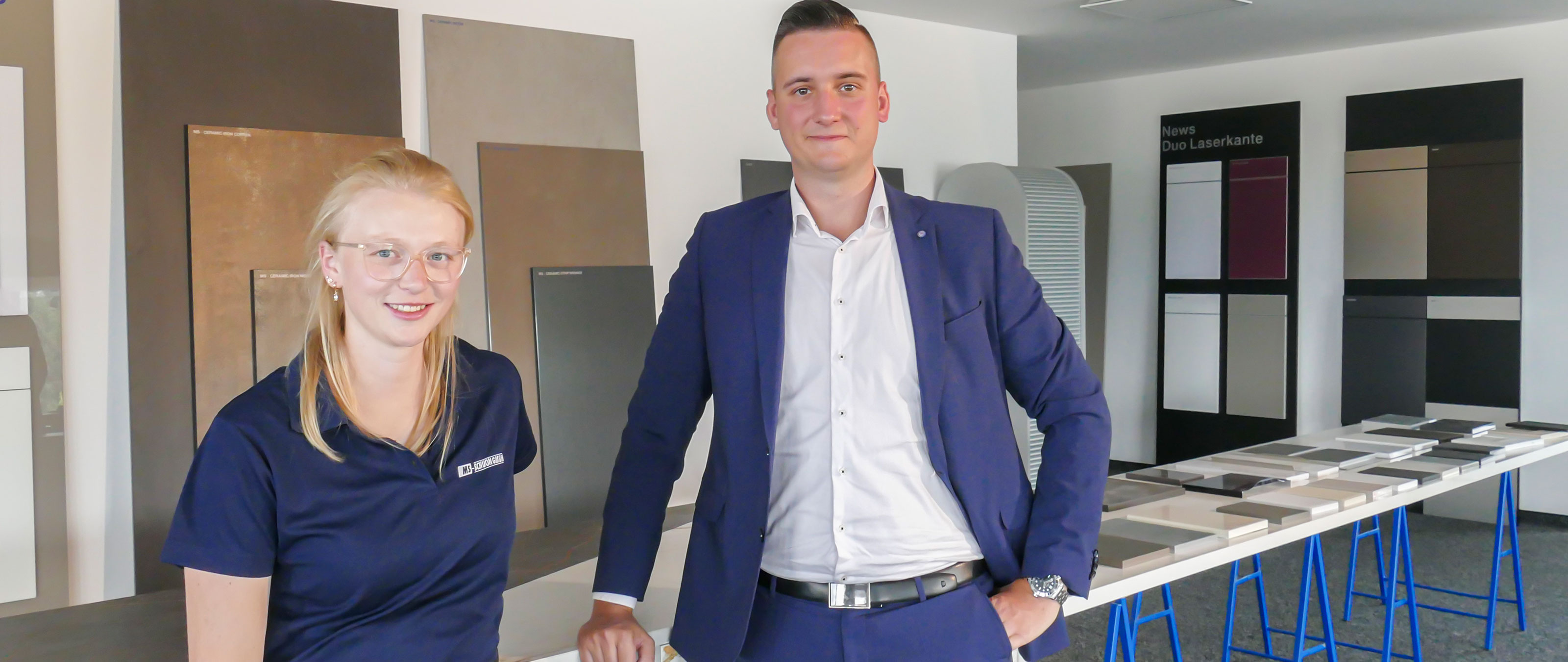
Bei einem kontinuierlichen Betriebswachstum, einer vielseitigen Produktpalette und einer hohen Anzahl an zu produzierenden Teilen kommt es schnell zu unübersichtlichen Strukturen. Dieser Meinung ist auch die MS-Schuon GmbH aus dem Schwarzwald. Die Lösung? Der Schritt in Richtung digitale Zukunft. Mit der Einführung des productionManagers – der digitalen Auftragsmappe von HOMAG – wurde in den Abläufen in der AV und Produktion der Grundstein für einen Wandel gelegt, der kurze Wege und die vollständige Transparenz über die Aufträge in der Produktion mit sich bringt.
Nach der Gründung 1983 startete die MS-Schuon GmbH als Hersteller für Leimholzmöbel und legte zügig an Volumen zu. Aus dem innovativen Möbelbereich ist ein sehr starker Zweig als Zulieferer für verschiedene Industriebranchen entstanden. Mit rund 120 Mitarbeitern ist das Schuon-Gespann heute auf die Produktion von Möbeln und Möbelteilen in der Caravan-, Küchen- und Möbelindustrie spezialisiert und bedient mit einem modernen und vielfältigen Produktspektrum Kunden weltweit.
„Inhouse“- Produktion ermöglicht hohe Fertigungstiefe
„Wir steuern die Qualität unserer Produkte von Anfang bis Ende selbst. Im Caravan-Bereich beispielsweise kaufen wir Rohprofile ein, die dann bei uns direkt weiterverarbeitet und fertiggestellt werden. Bis zur Spritzgussfertigung produzieren wir alles bei uns im Haus.“, berichtet der 29-jährige Geschäftsführer Phillip Schuon. Durch die daraus resultierende Fertigungstiefe wird den Schuon-Kunden eine durchgängige und detaillierte Beratung von A bis Z geboten.
Durchdacht und lösungsorientiert mit HOMAG
Umfassendes Know-how und zuverlässige Lieferanten tragen ihren Teil zu einer hohen Fertigungstiefe bei, aber auch die richtige Maschinen- und Softwaretechnik gehört dazu. Dabei setzt das Schuon-Team nun in der dritten Generation zu großen Teilen auf HOMAG: „Die Zusammenarbeit mit HOMAG besteht schon lange. Wir haben einige Maschinen-Prototypen bei uns im Einsatz, deshalb gab es schon immer eine enge Verbindung. Hinzu kommt, dass die Maschinenkonzepte und digitalen Produkte durchgängig miteinander agieren – durchdachte Lösungen und alles aus einer Hand. Deshalb war für uns sofort klar: Wir möchten bei den Maschinen- und Softwarelösungen von HOMAG bleiben, da es für uns einfach Stand der Technik ist.“
Der Wunsch: Eine transparente Teilenachverfolgung – aber wie?
Das stetige Betriebs- und Produktwachstum machte es immer herausfordernder, den Überblick über Aufträge und Teile zu behalten, den Bearbeitungsstatus eines Auftrags in Erfahrung zu bringen oder kurzfristig Aussagen zur Termintreue in der Auslieferung geben zu können. Die Rückverfolgbarkeit der Teile wurde immer undurchsichtiger – und gleichzeitig nahm die „Zettelwirtschaft“ in der Produktion zu. Dokumentiert und abgearbeitet wurde nahezu alles mit Hilfe von Unterlagen in Papierform. Die Lösung: Ein bedeutender Schritt in Richtung Digitalisierung. „Für uns ist es wichtig, dass wir vereinfacht und transparent darstellen können, an welchen Bearbeitungsorten sich die Bauteile zu einem Auftrag befinden. Ich habe mir das Produktvideo zum productionManager auf YouTube angeschaut und mich gemeinsam mit Frau Fischer, unserer Mitarbeiterin aus der Arbeitsvorbereitung, selbständig informiert und letztendlich in das Produkt eingearbeitet, da alle benötigten Informationen bereits dokumentiert auf den HOMAG Kanälen zur Verfügung standen“, berichtet Schuon.
Der Familienbetrieb entschloss sich dazu die digitale Lösung einfach auszuprobieren: „Der productionManager bietet einen großen Funktionsumfang, dafür, dass das Produkt in der Basisversion kostenlos ist. Das hat mich überrascht. Der Invest war also keine Hürde für uns, somit hatten wir nichts zu verlieren. Einfach die App installieren, online buchen und loslegen, ohne sofort ein kostenpflichtiges Jahresabo abschließen zu müssen! Einfacher geht’s kaum. Kosten kamen erst hinzu, als wir die Anzahl der Arbeitsplätze in der Produktion, an denen der productionManager genutzt werden soll, angepasst haben.“ Die Testphase und Implementierung des productionManagers übernahm Rebecca Fischer, verantwortlich für die Auftragserfassung und bereits seit fünf Jahren bei MS-Schuon tätig: „In der Arbeitsvorbereitung war die Teilenachverfolgung davor ein großes schwarzes Loch, da wir nie sagen konnten, wo sich welches Bauteil zu welchem Auftrag aktuell befindet. Das löst jetzt die digitale Auftragsmappe für uns, da wir seither den Bearbeitungsfortschritt problemlos nachverfolgen können.“ Bei Frau Fischer kommen die Aufträge der Kunden in Form einer Excel an. Diese importiert sie einfach in den productionManager. Aber auch ein Import aus anderen Dateisystemen – bspw. einem CAD/CAM-System – wäre möglich. Anschließend gibt Frau Fischer jeden Auftrag für die Produktion frei. Ab diesem Moment hat jeder Mitarbeiter in der Fertigung per Tablet Zugriff auf den Auftrag und kann die Bauteileliste und den Auftragsfortschritt in Echtzeit einsehen.
Egal wo, egal wann: Alle Mitarbeiter haben alles im Blick
Nicht nur in der Arbeitsvorbereitung, sondern auch in der Produktion hat sich seit der Einführung des productionManagers einiges verändert. Für die transparente Teilenachverfolgung wurden individuell gewählte Arbeitsplätze definiert, die den Bearbeitungsfortschritt direkt in die Arbeitsvorbereitung zurückmelden. An der Plattenaufteilsäge kommt der freigegebene Auftrag zuerst an. Dort wird das Bauteil während des Zuschnitts etikettiert. Die Maschine meldet automatisch den Fertigungsfortschritt des Bauteils an den productionManager zurück - ganz ohne manuelle Zwischenschritte des Maschinenbedieners. Mit Hilfe des productionManagers besitzt jedes Bauteil seine eigene und individuelle ID und trägt alle notwendigen Bearbeitungsinformationen auf dem Etikett bei sich. Das ermöglicht die anschließende Rückmeldung an der Kantenanleimmaschine. Dort werden die Teile mit einem Handscanner gescannt. Die Anzahl der fertig bekanteten Teile wird in Echtzeit im Auftragsfortschritt des productionManagers sichtbar. In der letzten Station vor der Auslieferung - in der Kommissionierung - scannt eine Mitarbeiterin die Teile per Tablet. Sobald alle Teile kommissioniert wurden, wird der Auftrag als abgeschlossen markiert und für den Versand vorbereitet. In der Arbeitsvorbereitung erscheint der Auftragsstatus „Abgeschlossen“. „Wir stellen die Rückverfolgbarkeit sicher und auch die Mitarbeiter im Büro wissen zu jeder Zeit, wie weit der Auftrag vorangeschritten ist und wie viele Aufträge im Umlauf sind.“, berichtet Rebecca Fischer.
Das Gesamtpaket stimmt
Für das gesamte Team von MS-Schuon stellt die digitale Unterstützung eine Arbeitserleichterung dar. Auch die Vertriebsmitarbeiter können den Auftragsstatus einfach einsehen und gezielte Rückfragen zu einem Auftrag stellen, da im productionManager direkt angezeigt wird, wo sich jedes Bauteil aktuell befindet. Allgemeine Anfragen an den gesamten Produktionskreis, lange Nachforschungen und die Suche nach Bauteilen gehören ab jetzt der Vergangenheit an. „Der productionManager erleichtert unsere tägliche Arbeit, da auch unsere Kunden benötigte Informationen viel schneller erhalten. Was früher mehrere Stunden gedauert hat, wird heute in ein paar Minuten geklärt. Die Arbeit mit dem productionManager macht einfach Spaß“, betont Frau Fischer. Auch der Geschäftsführer Phillip Schuon ist begeistert: „Durch die transparente Arbeitsweise haben wir in jeden Auftrag einen schnellen Einblick und können bei Rückfragen zügig Abhilfe schaffen. Alle Mitarbeiter arbeiten selbstständig, ohne auf Rückmeldungen warten zu müssen.“
Hier bleibt kein Wunsch offen
Auch wenn der productionManager zunächst alle Anforderungen erfüllt, die für MS-Schuon relevant sind, gibt es auch Verbesserungspotenzial. Vor allem Frau Fischer, die sich mittlerweile bestens mit der Applikation auskennt, steht im engen Austausch mit HOMAG und unterstützt mit Optimierungsvorschlägen: „Während des letzten Besuchs von HOMAG hatte ich den Wunsch geäußert eine Kommentarfunktion zu implementieren, damit wir defekte oder beschädigte Teile direkt digital in der App erfassen können und uns so den Weg von der Produktion in das Büro sparen. Außerdem wollten wir Zeit sparen, da wir bisher mit „roten Zetteln“ Informationen zu beschädigten Teilen gesammelt haben und dies meistens einige Zeit in Anspruch genommen hat, bis der Zettel letztendlich auf meinem Schreibtisch gelandet ist.“ Der Wunsch von Frau Fischer wurde innerhalb kurzer Zeit umgesetzt und die bisherigen „roten Zettel“ durch die digitale Kommentarfunktion ersetzt: „Wenn wir Feedback geben, wird das schnell von HOMAG umgesetzt. Es ist spannend, wenn man eigene Vorschläge einbringen kann und wir die Weiterentwicklung des Produkts hautnah mitverfolgen. Das macht dann umso mehr Spaß!“
Mit Blick in eine digitale Zukunft
Phillip Schuon blickt positiv in die Zukunft und möchte den Einsatz des productionManagers im Betrieb ausweiten. Aktuell wird die digitale Lösung in der Holzfrontenproduktion eingesetzt, im nächsten Schritt wird die Glas- und Keramikfrontenproduktion mit dem productionManager ausgestattet. Auch an weiteren digitalen Produkten ist der Geschäftsführer bereits dran: „In der Kommissionier-Abteilung möchten wir demnächst den Sortier-Assistenten von HOMAG implementieren. Um weiterhin stetig wachsen zu können, brauchen wir ein funktionierendes Rückgrat für unsere Prozesse. Der Einsatz von digitalen Bausteinen nimmt hier für uns eine bedeutende Rolle ein.“
Videos
Bitte bestätigen Sie, dass bei der Nutzung von YouTube Daten wie Ihre IP-Adresse, Browser-Kennung und ähnliches an Google übermittelt werden können.
» Datenschutzerklärung
Digitale Auftragsmappe im Einsatz bei der MS-Schuon GmbH
„Unser Hauptinteresse galt der Nachverfolgung in der Produktion, damit wir zu jeder Zeit wissen, wo sich unsere Bauteile aktuell befinden. Der productionManager erfüllt mit seinem Funktionsumfang genau das, wonach wir gesucht haben!“Phillip Schuon, Geschäftsführer MS-Schuon GmbH