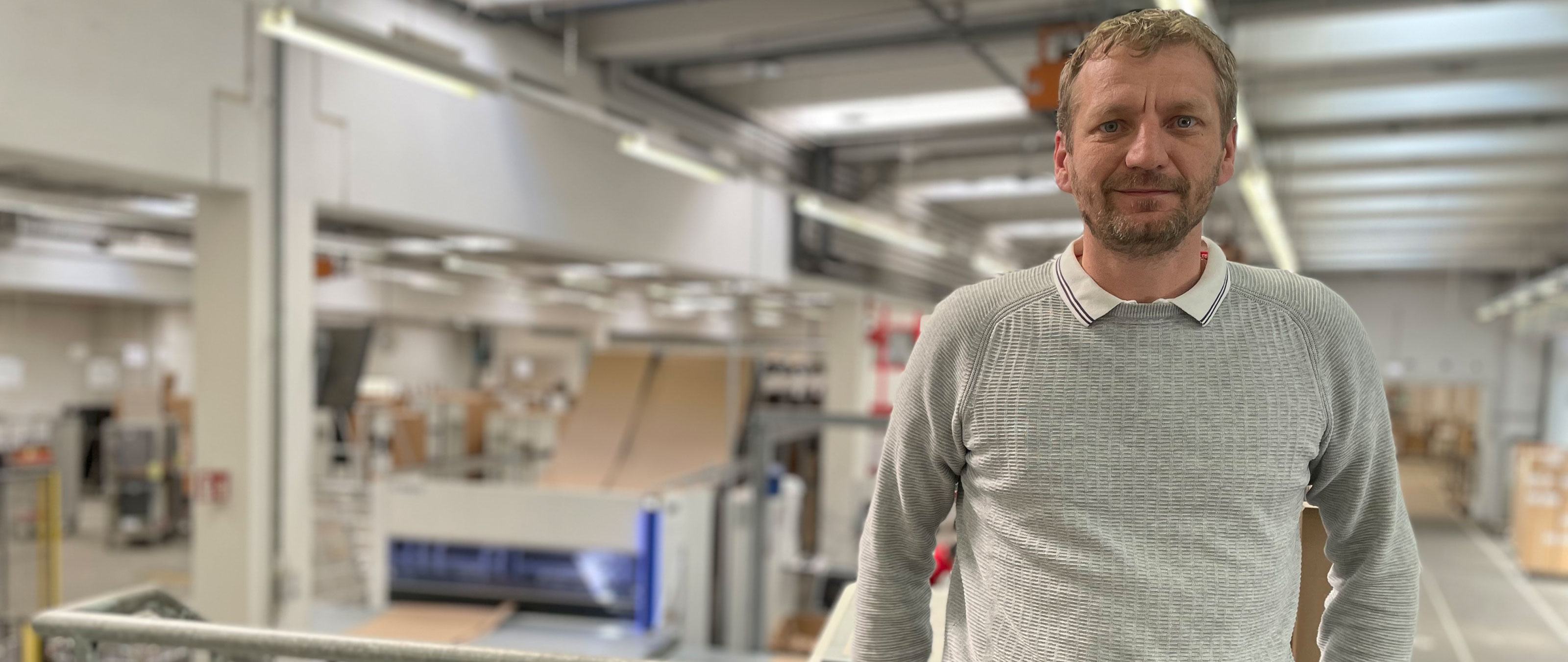
Die Küche ist der Dreh- und Angelpunkt einer Wohnung. Im oberösterreichischen Wels fertigt ewe Küchen jede dieser Lebensadern individuell in hoher Qualität und mit Liebe zum Detail. Damit die Einrichtung mängelfrei zum Abnehmer gelangt, setzt ewe bei der Verpackung seit Anfang des Jahres auf eine Kartonschneidemaschine von HOMAG.
2021 wurden in Österreich insgesamt 209.900 Küchen verkauft. Damit investierte durchschnittlich jeder zwanzigste österreichische Haushalt in eine neue Küche. Dass der Küchenmarkt in der Alpenrepublik von Dynamik geprägt ist, zeigt auch der Anstieg der Nachfrage, die sich 2021 zum Vorjahr um satte 7,9 % erhöhte, bei ewe Küchen sogar um 24 %. Begleitet wurde dieser Anstieg für ewe Küchen von einem wachsenden Marktanteil um 1,3 %. Im Gleichklang mit der wachsenden Nachfrage zeigte das Jahr 2021 zudem, dass Küchen immer hochwertiger werden und die Kunden großes Augenmerk auf Details und Ausstattung legen.
Auftragsbezogen mit hoher Fertigungstiefe
Als Teil der Nobia-Gruppe, dem größten Küchenhersteller Europas, produziert ewe hochwertige Küchen in Losgröße 1. Zu den Marken gehören ewe mit modernen Küchen, FM als zeitgemäße Landhausdesignlinie und INTUO Designküchen. So ist etwa das Modell „ewe Fina“ die Küche mit der matten Oberfläche „ewe nanoo“ das beliebteste Modell aus Wels; „FM Hirschalm“ als Beispiel der neu interpretierten Landhausküche hingegen kombiniert sowohl traditionelle Einflüsse aus dem Mühlviertel als auch moderne Anmutung.
Gefertigt werden die Küchen an den Standorten Wels und Freistadt. Maßgebliche Fertigungsprinzipien sind hier neben dem Losgröße-1-Prinzip die vernetzte, verkettete Produktion im Durchlauf mit hoher Fertigungstiefe. „Jeder Schrank ist auftragsbezogen“, unterstreicht Michael Sterrer, Leiter Engineering in Wels. „Jede Seite, jeder Boden, jedes Fach ist individuell produziert. Es gibt kein Bauteil, das nicht einen Bezug zu einem Auftrag hat.“ Rahmenbedingungen, unter denen ein Korpus eine Durchlaufzeit von drei Tagen hat und 1.000 Schränke pro Tag produziert werden.
900 Individualisten auf Linie A
Die Fertigung in Wels startet mit einem Regalsystem, in dem circa 50 beschichtete Plattentypen in zwei Stärken bevorratet werden. „Im Korpusbereich verwenden wir aktuell circa 25 Dekore, jedes davon ein- und beidseitig“, geht Sterrer weiter auf das Spektrum ein. Lackierte und furnierte Teile werden in Freistadt gefertigt und dann in die Welser Produktion eingespielt. Hier laufen grundsätzlich Halbformate in zwei Korpusteilelinien, von denen die Hauptlinie A alle Hoch-, Ober- und Unterschränke bearbeitet. Täglich sind das etwa 900 Stück. Die Bearbeitung beginnt mit zwei 1-Achs-Sägen, die Tag für Tag 5.500 Teile schneiden. Jedes Teil erhält hier ein Etikett, das erst einmal nur Daten zur Art der Platte und ihren Dimensionen beinhaltet.
Mit den nachfolgenden Bearbeitungen entstehen daraus x verschiedene Komponenten. Zunächst einmal geht das Teil aber über einen Zwischenpuffer in eine Kantenstraße, wo vier Anlagen so in Reihe geschaltet sind, dass es lagekonstant durchlaufen kann. „Nach der Kantenlinie weiß das Teil nun auch, was es ist und zu welchem Auftrag es gehört“, betont Sterrer. Die Straße endet mit zwei Auslaufstrecken, wo die Bauteile erst vorsortiert und in Containern gesammelt werden, um anschließend in eine Kommissionierstation zu laufen.
In der manuellen Kommissionierung treffen sich dann alle Teile aus den Welser Linien mit den Teilen aus Freistadt, um in die exakte Produktionsreihenfolge gebracht zu werden. Die nun folgende Individualisierung in der Endmontage nimmt ewe so spät wie möglich vor. Insofern beläuft sich die maximale Losgröße, die derzeit im Korpusbereich zusammengefasst wird, auf einen Tag. „Selbst da überlegen wir, weiter zu reduzieren, weil es den Kommissioniervorgang vereinfachen und den Aufwand an Logik und Know-how reduzieren würde.“ Umgesetzt wird die Individualisierung der Teile schließlich in einer hoch automatisierten Durchlaufanlage, wo die Teile gebohrt und gedübelt, mit Beschlägen versehen, montiert und zum Korpus verpresst werden.
Noch einmal 100 der besonderen Art
Auf der zweiten Korpusteilelinie, der Sonderlinie C, die täglich etwa 100 Schränke durchsetzt, laufen die Teile, die vom Üblichen abweichen: besonders kleine oder große, aber auch stark strukturierte oder solche mit Unterscheidungen in Dekor und Hochglanzbeschichtung. Bearbeitet und montiert werden hier auch alle Schränke, die keine kubische Form aufweisen, Eckschränke zum Beispiel, sowie Schränke mit hohem Montageaufwand, der sich in der Taktfertigung nicht realisieren lässt. Um täglich 1.000 Teile durchsetzen zu können, arbeitet auch diese Linie mit einer 1-Achs-Säge, nun aber gefolgt von einer Kantenlinie mit Rücktransport.
Auf beiden Linien laufen die Schränke in bunter Auftragsreihenfolge, wobei eine Kommission nach der anderen produziert wird. Am Ende der beiden Linien gehen die Schränke dann in Richtung Verpackung.
Verpacken in Losgröße 1
Beim Vertrieb der Küchen arbeitet ewe zum Großteil mit unabhängigen Fachhändlern zusammen, die die Schränke als Korpusse erhalten. Schon seit 2009, als ewe die erste Verpackungsanlage in Betrieb nahm, schneidet der Küchenhersteller die Verpackung exakt auf den jeweiligen Schrank zu. „Die Vielfalt unserer Produkte zog natürlich einen großen Bedarf an unterschiedlichen Kartonzuschnitten nach sich“, so Sterrer. „Allein für Glasschränke nutzen wir drei- oder gar vierteilige Verpackungen.“ In den letzten zwölf, dreizehn Jahren hat ewe somit umfangreiche Erfahrungen mit der Losgröße-1-Verpackung gesammelt. „Alle Designs und Abwicklungen haben wir selbst kreiert und fahren diese bis heute auch ausschließlich. Die zugehörige Programmiersoftware, die wir ebenfalls 2009 gekauft haben, wollen wir daher auch künftig weiterverwenden.“
Alle nötigen Daten für die individuellen Verpackungen kommen bis dato aus einem ERP-System. Genutzt wird eine Schnittstelle, die ewe selbst erstellt hat und über die alle relevanten Informationen an die Anlage gelangen: natürlich die Korpusbreite, -höhe und -tiefe, aber beispielsweise auch die Materialstärke einer Front. Je nachdem, ob diese 18 oder 22 mm stark ist, entstehen schließlich verschiedene Abwicklungen für die Verpackung. „Die erforderlichen Daten werden mit einem geringen Vorlauf bereitgestellt. Mit bis zu sechs Korpussen als Puffer scannen wir den Barcode eines Schrankes direkt vor der Verpackung. Im ERP-System wird so eine Variablenliste erstellt, die zusammen mit einem Design den passenden Zuschnitt ergibt.“
Datenstruktur möglichst beibehalten
Vier Verpackungsanlagen hat ewe heute an beiden Standorten im Einsatz. Die individuelle Verpackung in Losgröße 1 ist etabliert, umfangreiches Know-how ist vorhanden. Was also war der Grund, dass sich der Küchenhersteller bei der anstehenden Ersatzinvestition für eine Kartonschneidemaschine PAQTEQ C-250 von HOMAG entschieden hat? Es gab mehrere. „Gefallen hat uns zum Beispiel, dass wir die Kartons nun bedrucken können. Wir haben Schränke, für die wir nicht nur eine Abwicklung produzieren, sondern zwei oder drei. Da verliert ein Kollege schon mal den Faden und ist unsicher, welches Design zu welchem Schrank gehört“, so Sterrer. „Heute drucken wir einfach die fünfstellige Elementnummer auf die Kartons und stellen so die Verbindung zwischen Design und Schrank her. Fehlerquelle eliminiert.“
Ein weiterer Grund war die Anzahl der Werkzeuge. Während die vorherige Anlage mit sechs Längswerkzeugen arbeitete, stellt die PAQTEQ nun acht zur Verfügung. „Diese Kapazitätserhöhung zahlt sich aus, wenn wir für eine gewisse Zeit den Durchsatz erhöhen müssen“, sagt der Leiter Engineering. „Für diese Zeit stellen wir einfach einen weiteren Mitarbeiter an die Maschine.“ Besonders wichtig war es ewe zudem, aus dem ERP-System heraus flexibel und durchgängig zu bleiben. Die bisherige Datenstruktur der vier Verpackungsmaschinen sollte möglichst wenig geändert werden. „Um die Daten sicher auf die PAQTEQ transferieren zu können, haben wir zusammen mit HOMAG die generelle Struktur etwas angepasst“, berichtet Sterrer. Was nach seiner Ansicht ebenso problemlos lief wie die Inbetriebnahme der PAQTEQ, die in allen Details gut vorbereitet worden war: „Das hat sensationell funktioniert.“
40 Sekunden
Die Anlage, die Anfang des Jahres installiert wurde, ist heute direkt in die Linie eingebunden. Das gesamte Umfeld, insbesondere die Fördertechnik für die Schränke und Kartondesigns, konnte unverändert bleiben. Gefahren wird die PAQTEQ mit sechs Kartonschächten. Damit hat ewe, wo bislang drei Kartonbreiten genutzt wurden, jede Breite nun zweimal im Zugriff. „Jetzt fahren wir redundant und können die Endloskartonage entweder in der Pause wechseln oder wenn es der Takt am Montageband erlaubt.“
Einen Rückstau am Band gebe es nicht mehr. Verpackt würden die 900 bis 1.000 Schränke in zwei Schichten. „Wir sprechen somit von einem 40-Sekunden-Takt. Für jeden Schrank, der von der Montagelinie kommt, schneiden wir in diesen 40 Sekunden einen Karton zu und realisieren das Handling.“ Die Bediener schalten dafür die Maschine nur ein oder füllen die Endloskartonage nach. Alles andere übernimmt die PAQTEQ, auch die Datenübernahme läuft automatisch im Hintergrund. Kommissionsweise gehen die verpackten Schränke dann auf Wagen in den Versand, um am nächsten Tag per Lkw zum Händler transportiert zu werden.
Gut zu gebrauchen
Dass heute in Wels die ein oder andere Verpackung mehr bewältigt werden kann, hatte die PAQTEQ bereits bei der Vorabnahme mit einer Durchsatzsteigerung von sieben Prozent gezeigt. Eine Steigerung, die ewe sehr gelegen kommt. Man denke nur an den gestiegenen Marktanteil …
„Heute drucken wir einfach die fünfstellige Elementnummer auf die Kartons und stellen so die Verbindung zwischen Design und Schrank her. Fehlerquelle eliminiert.“Michael Sterrer, Leiter Engineering bei ewe Küchen in Wels