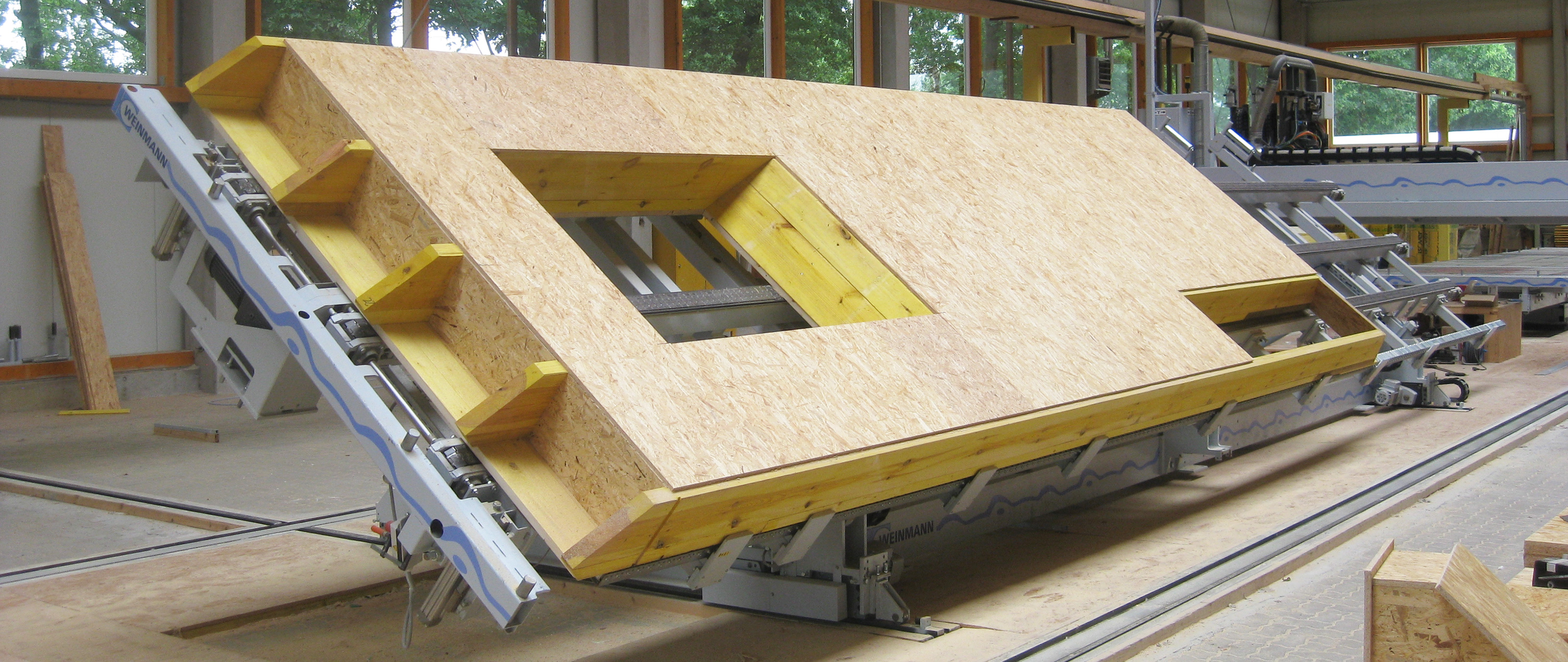
Ein Artikel des HOLZBAU-MAGAZIN, 2/2017. Hier lesen Sie das HOLZBAU-MAGAZIN Online.
Redakteuer: Dr. Joachim Mohr, Tübingen
Als 2008 die Produktion von Holzrahmenelementen an ihre Kapazitätsgrenze stoß, entschied sich Zimmermeister Daniel Hamdorf für eine umfassende Umstrukturierung seines Unternehmens. Seine Umsätze im Holzrahmenbau hat er seither bei gleichem Mitarbeiterstamm glatt verzehnfacht.
Die Zimmerei Hamdorf im schleswigholsteinischen Fahrenkrug kann als Beispiel dafür gelten, dass viele Holzbauunternehmen gut durch die Finanzkrise gekommen sind. 2009 hat Geschäftsführer Daniel Hamdorf 2,3 Mio. in sein Unternehmen investiert und dabei den Umsatz im betreffenden Geschäftsfeld verzehnfacht. Ein Schritt, zu dem er sich nur entschlossen hat, weil auch in der Krise eine hohe Nachfrage nach seinen Produkten vorhanden war.
2008 an die Kapazitätsgrenze gestoßen
Es war der Holztafelbau, dem Daniel Harmdorf mitten in Krisenzeiten ein Upgrade spendierte. In weiteren Geschäftsfeldern übernimmt seine Zimmerei mit insgesamt 50 Mitarbeitern traditionelle Zimmereigewerke wie Dachstühle, produziert und montiert Nagelbinder, deckt Dächer und ist auch im Fassadenbau aktiv. Darüber hinaus liefert sie Bauteile an Zimmererkollegen. Derzeit liegt der Anteil solcher Zulieferprodukte am Umsatz bei etwa 45 Prozent.
Hamdorfs Schwerpunkte im Holzrahmenbau liegen im Objekt- und Gewerbebau, und an Mehrfamilienhäusern, Kindergärten, Bürogebäuden, Schulen oder Flüchtlingsheimen besteht in seiner Region ein stetig steigender Bedarf. Deshalb war die Zimmerei im Jahr 2008 mit ihrer Fertigung von Holzrahmenelementen an die Kapazitätsgrenzen gestoßen. Damals produzierte man mit drei Mitarbeitern Holzelemente für etwa 6 Häuser im Jahr. „Die Nachfrage gab aber damals schon das Dreifache her“, erinnert sich Daniel Hamdorf.
Nägel mit Köpfen bei der Umstrukturierung
Statt ein oder zwei Mitarbeiter mehr einzustellen und einen neuen Arbeitstisch anzuschaffen, machte der Zimmermeister nach dem Motto „Ganz oder gar nicht“ Nägel mit Köpfen. Das hieß im ersten Schritt, dass er eine neue Halle für seine Holzrahmenfertigung auf sein Firmengelände stellte: 25 x 60 m groß, mit 7 m Hakenhöhe und einem Portalkran mit 5 t Tragfähigkeit. Außerdem investierte er in ein modernes Telecargosystem mit 2 Anhängern und 8 Wechselbrücken, um seine Bauteile zum Kunden zu bringen.
Kern der Neustrukturierung seines Unternehmens war die Anschaffung einer Weinmann-Multifunktionsbrücke mit drei Arbeitstischen, die seine Kapazitätsgrenzen schlagartig erweiterte: Mit dieser automatisierten Fertigungsanlage konnte Hamdorf nicht nur die schon vorhandene Nachfrage nach Holzrahmenelementen befriedigen, er erlebte in den Jahren danach auch einen kräftigen Auftragsschub. Heute produziert die Zimmerei jährlich Bauteile für rund 60 Holzhäuser, hat ihr Volumen im Holzrahmenbau also glatt verzehnfacht.
Dabei ist der Aufwand in der Arbeitsvorbereitung gestiegen. Diesen Effekt machen aber kürzere Montagezeiten, die durch eine Erhöhung von Bauteilpräzision und Vorfertigungsgrad möglich geworden sind, mehr als wett. Dass er damit unter dem Strich rentabler arbeitet, liegt für Hamdorf auf der Hand: Schließlich hat er das kräftige Umsatzwachstum in diesem Unternehmensbereich erreicht, ohne einen zusätzlichen Mitarbeiter einzustellen.
Fünf Tische gegen Bottlenecks & Rückstau
Die Zahl der Tische in der Fertigungslinie ist in der Zwischenzeit auf fünf angewachsen. Vier Tische hatte man von Anfang an in Betrieb: Tisch 1 ist ein Weinmann-Tisch aus der alten Fertigung, der „recycelt“ wurde und heute für die Produktion des Riegelwerks genutzt wird. Von Hand aufgelegt, mit einer Spannvorrichtung ausgerichtet und manuell genagelt, landet das fertige Riegelwerk per Hallenkran auf Tisch 2, dem ersten neuen Tisch in der Fertigungslinie.
Hier wird der Holzrahmen beplankt. Die Beplankungsmaterialien liegen direkt neben dem Tisch und werden von den Mitarbeitern ohne großen Körpereinsatz mit Plattensaugern bewegt. Die Beplankung wird anschließend von der Multifunktionsbrücke geklammert und mit Säge und Fräse bearbeitet, also zugeschnitten und mit Öffnungen für Fenster, Steckdosen, Lichtschalter etc. versehen.
Dass diese Arbeitsgänge von der Riegelwerksproduktion getrennt sind, führt bei Auftragsspitzen unter dem Strich zu kürzeren Stillstandszeiten für die Multifunktionsbrücke – vorausgesetzt, es kommt weiter hinten in der Linie nicht zu einem Bottleneck mit Rückstau.
Im nächsten Schritt gelangt das einseitig beplankte Rahmenwerk in einem Wendevorgag auf Tisch 3. Hier wird die Dämmung eingebracht, bevor das Element über einen Längsförderer zu Tisch 4 transportiert wird, der in Querrichtung verfahrbar ist. Auf diesem Tisch wird die zweite Beplankung aufgelegt, von der Multifunktionsbrücke befestigt und bearbeitet.
Anschließend wird es auf den Tisch 5 übergeben, den Hamdorf erst etwas später angeschafft hat: „Dort finden heute die Sonderbearbeitungen statt, zum Beispiel das Anbringen von Holzverschalungen, der Fenstereinbau oder der Einbau von Installationsebenen.
Außerdem dient uns der Tisch als kurzfristiges Zwischenlager für bis zu zwei Wandelemente, wenn es beim Verladen einen Engpass gibt. Bei uns wandern die Elemente vom letzten Tisch nämlich direkt auf eine Wechselbrücke.“
Mit dieser Doppelfunktion ist Tisch 5 eine wichtige Station, um den Workflow in der Halle „ein bisschen zu entspannen“ und Bottlenecks in der Fertigungslinie zu verhindern.
Qualitativer Sprung nach oben
Die Anlage wurde 2009 in der neuen Halle installiert und von den Mitarbeitern ohne große Anlaufschwierigkeiten in Betrieb genommen. Auch eine längere Optimierungsphase der Produktionsprozesse gab es in Fahrenkrug nicht. Daniel Hamdorf: „Natürlich muss man die Änderungen vorher mit den Mitarbeitern besprechen, aber viele sind naheliegend, und außerdem haben wir gute Mitarbeiter, mit denen solche Prozesse auch problemlos umzusetzen sind. Darauf bin ich schon stolz.“
„Auch Weinmann berät schon im Vorfeld sehr gut, entwickelt zusammen mit dem Kunden ein Hallenlayout und bietet für alle Beteiligten Schulungen an. Außerdem habe ich natürlich vorher bei Kollegen reingeschaut. Da sieht man schnell, worauf man bei einer automatisierten Fertigung achten muss.“
So haben sich neben der anvisierten Kapazitätssteigerung auch andere Erwartungen an die neue Produktionstechnik schnell erfüllt: „Wir wollten damals zum Beispiel auch unsere positiven Erfahrungen aus dem automatisierten Abbund in die Elementfertigung übertragen“ erinnert sich Daniel Hamdorf heute. Wobei er „positive Erfahrungen“ zunächst mit einem professionellen Qualitätsmanagement assoziiert.
In diesem Punkt ging die Rechnung für das Unternehmen voll auf: „Wir liefern unserem Kunden heute eine gleichbleibend hohe, kalkulierbare Qualität. Also einen hohen Vorfertigungsgrad in industrieller Präzision und ohne qualitative Ausreißer nach unten.“
Mehr Flexibilität und Termintreue
Ebenfalls erfüllt hat sich Hamdorfs Wunsch nach größtmöglicher Flexibilität: Wir fertigen auf der Weinmann-Anlage in Losgröße 1, können also alles liefern, was der Kunde möchte.“
Das gilt nicht nur für unterschiedliche Dämmstoffe, die das Unternehmen einlegt oder mit einer Isocell-Anlage einbläst. Es gilt für komplexe Wandkonstruktionen, anspruchsvolle Details und statisch hochbelastete Wandscheiben, wie sie im Objektbau durchaus vorkommen: „Der Kunde muss sich dabei nicht auf unseren Wandaufbau einstellen, sondern wir stellen uns auf seinen Wandaufbau ein. Ganz wie es im Handwerk sein sollte.“
Auch bei der Zeitplanung ist man in Fahrenkrug flexibler geworden. Das heißt zum Einen, dass man auch in Zeiten hoher Auslastung kurzfristig auf eng terminierte Anfragen reagieren kann. Zum anderen sind die Abläufe in der Produktion besser planbar, weshalb Hamdorf zugesagte Termine punktgenau einhalten kann: „Mir und meinen Kunden gibt das ein angenehmes Plus an Sicherheit.“
Festpreis dank klar definierten Kosten
Letzteres auch in puncto Kalkulation. Die ist für Daniel Hamdorf überschaubarer geworden, seit jedes Bauteil – auch ein kompliziertes wie z. B. eine runde Fledermausgaube – durch die automatisierte Fertigung läuft: „Die Bearbeitungszeiten lassen sich mit der automatisierten Fertigung viel exakter planen, auch komplizierte Details sind von den Kosten her viel klarer definiert. Die Probleme komplexer Bauteile lösen wir ja heute in der AV, nicht am Arbeitstisch. Das gibt mir als Unternehmer eine Kalkulationssicherheit, von der auch meine Kunden profitieren, weil ich ihnen meine Produkte zum Festpreise anbieten kann.“
Besonders im Zuliefergeschäft ist das ein gewichtiger Marktvorteil – einer der Gründe, weshalb dieser Bereich bei der Zimmerei Hamdorf seit 2009 überproportional gewachsen ist.
Kleine Betriebe, die den Holzbau als professionelles Standbein betrachten, sind in diesem Bereich ihre besten Kunden, und etwa alle zwei Wochen kommt aus diesem Kundenkreis jemand vorbei, um sich die moderne Produktionsanlage anzusehen. „Dann wird die Technik zum Marketingargument. Wenn so ein Kunde bei uns reingeschaut hat, ist ihm klar: Er kann ein Haus in ein oder zwei Tagen regendicht bekommen, wenn er alle Elemente bei mir zukauft.“
So generiert Daniel Hamdorf heute prozentual erheblich mehr Umsätze in der Firma und weniger auf der Baustelle. Alles in allem ist der Anteil der Holztafelbau-Produktion von 8 Prozent in 2008 auf aktuell 40 Prozent gestiegen.
„Rentabel“ auch für die Mitarbeiter
„Rentiert“ hat sich die Investition auch für die Mitarbeiter der Zimmerei: „Auf der Baustelle sind sie motivierter, weil die Montage auch bei komplexen Bauteilen dank höherer Präzision und einem höheren Vorfertigungsgrad schneller und reibungsloser abläuft.
Auch für die Mitarbeiter in der Produktion ist das Leben einfacher geworden, weil solche Bauteile, über die man sich früher den Kopf zerbrechen musste, jetzt unkompliziert in der Anlage mitlaufen.“
Für Hamdorf, der auch mal Geselle in der Elementproduktion war, ein sehr erwünschter Nebeneffekt: „Mir lag viel daran, dass sich durch die automatisierte Fertigung die Arbeitsbedingungen im meinem Unternehmen verbessern. Deshalb waren mir zum Beispiel auch die Plattensauger wichtig.“
Verbessert hat sich auch die Arbeitsumgebung in der Zimmerei Hamdorf. Heute arbeitet man in Fahrenkrug in einer hellen, gut ausgestatteten Halle, wovon nicht nur die Mitarbeiter profitieren, sondern auch das Unternehmen selbst. So wird sich Hamdorf auch in Zeiten der Personalknappheit etwas leichter tun, wenn er sich doch einmal auf die Suche nach neuen Mitarbeitern machen sollte.
Außerdem sieht der Zimmermeister – durchaus zu Recht – einen direkten Zusammenhang zwischen Mitarbeiterzufriedenheit und Bauteilqualität: „Von einem arbeitnehmerfreundlichen Arbeitsplatz profitieren auch wir, denn nur mit gut motivierten Mitarbeitern kann man auf Dauer Produkte in einem optimalen Qualitätsstandard produzieren.“ Ein Unternehmenskonzept mit Zukunft: Die Halle bietet bereits Raum für künftige Erweiterungen.
Quelle Bildmaterial: Hamdorf
Zimmerei Hamdorf
Handwerkliche Ausführung, Zuverlässigkeit, Qualität und gute Beratung sind die Philosophie der Firma Hamdorf. Unsere modernst ausgestatteten Fertigungshallen geben uns die Flexibilität, um uns auf Ihre Wünsche einzustellen. Handwerk mit modernster Hightech-Produktion schafft die Basis, um auch zukünftig Ihr Partner am Bau sein zu können.
Als einer der führenden Zimmereien im norddeutschen Raum, beschäftigen wir mittlerweile 46 Mitarbeiter, die einen Umsatz von ca. 6,5 Millionen Euro erwirtschaften.
Zur Website von Hamdorf