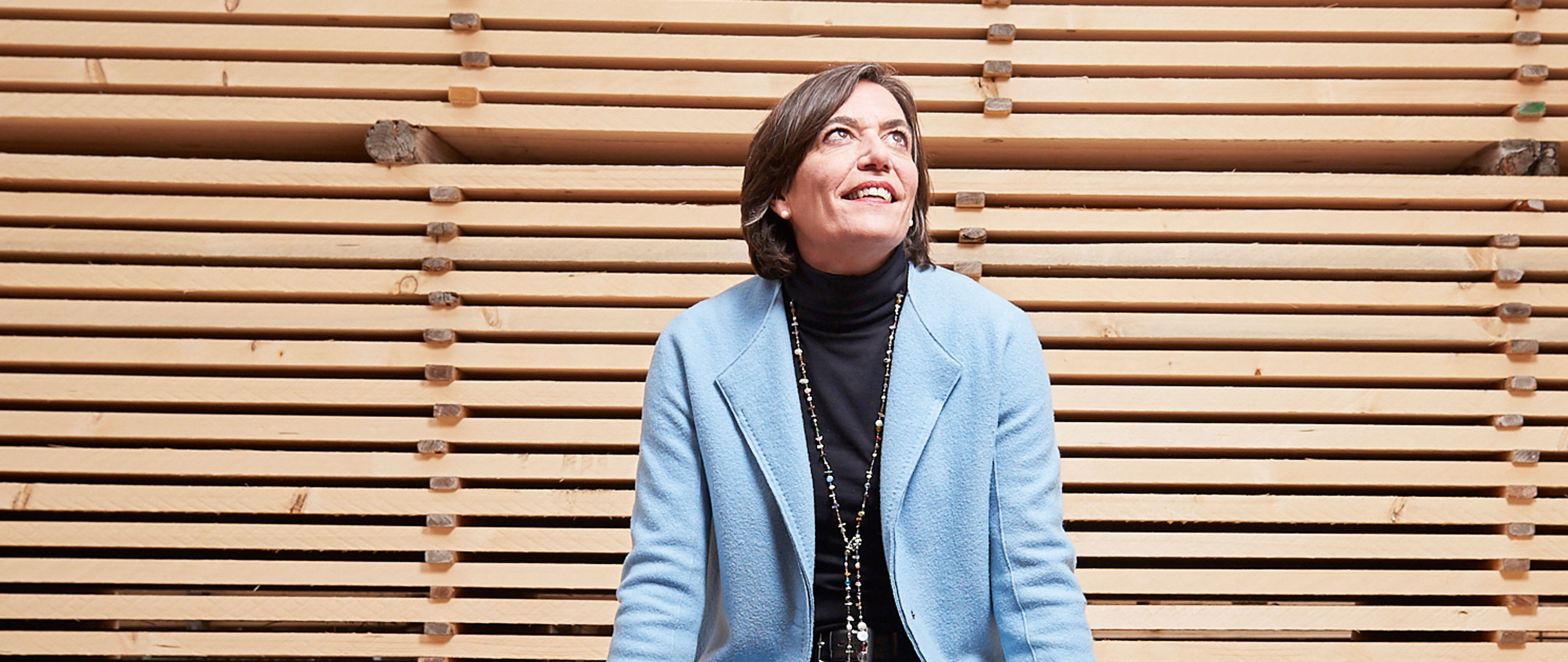
Lastwagen rangieren, Maschinen brummen, es duftet nach Fichte und Tanne. Besucher merken sofort: Es geht um Holz bei Blumer Lehmann in Gossau, einem Ort bei St. Gallen, rund 25 Kilometer südlich des Bodensees. Blumer Lehmann gehört zur Schweizer Lehmann Gruppe und ist eines der führenden Holzbauunternehmen des Landes. „Wir sind überzeugt, dass Holz der Baustoff der Zukunft ist“, sagt Katharina Lehmann, die den Betrieb seit 24 Jahren führt. Wenn die Chefin über Holz spricht, ist sie in ihrem Element. „Ich bin in der Firma aufgewachsen“, sagt sie. Seit fünf Generationen ist das Unternehmen im Besitz ihrer Familie. Ihre Vorfahren begannen 1875 mit einem Sägewerk an einem Bachlauf, später kamen Dachstühle zum Portfolio, dann Scheunen für die Landwirtschaft. „Seit rund 20 Jahren bauen wir komplette Gebäude aus Holz, darunter Mehrfamilienhäuser, Schul-, Büro- und Industriegebäude“, sagt Lehmann und ergänzt: „Wir kümmern uns um alle Arbeitsschritte – vom gefällten Baum bis zum fertigen Haus.“
Darunter sind nicht nur atemberaubende Free Form-Konstruktionen wie das Swatch-Hauptquartier in Biel oder der Apple-Store in Bangkok. Einen großen Teil des Geschäfts bringen komfortable Gebäude, die aus Holzmodulen bestehen. „Die kompletten Module fertigen wir individuell nach Wunsch der Kunden in unserem Werk“, sagt Lehmann. Mit digital gesteuerten Anlagen, welche die Elemente rasch und effizient produzieren.
Fehlersuche mit digitalen Augen
Der Prozess beginnt bei den Holzstapeln, wo ein Kran Rundholzstämme in seinen Greifarm klemmt und auf einem Förderband ablegt. Die Stämme verschwinden in der Sägerei, wo sie zerteilt werden. Drei bis vier Tage lagern die Bretter anschließend in der Trockenkammer. Häuser müssen stabil sein. Das verwendete Holz darf keine Fehler haben. Astlöcher, Risse oder Harzeinlagerungen einzeln zu suchen und herauszusägen, dauert viel zu lange. „Deshalb haben wir eine maschinelle Sortieranlage gekauft, um das Holz besser zu veredeln“, sagt Lehmann. Auf einem Förderband schießen die getrockneten Bretter durch die Hobelmaschine. Über ihnen wachen digitale Augen, die das Holz scannen. Eine smarte Software erkennt Fehler sofort und zuverlässig. Doch mehr noch: Die Maschinen von System TM sägen die Schwachstellen blitzschnell heraus. Mehr als sieben Fehler kann die Maschine pro Sekunde beseitigen. Eine weitere Maschine von System TM leimt die Teile gleich wieder zusammen. Dazu schneidet sie Zacken in beide Brettenden, die wie Schlüssel und Schloss genau ineinanderpassen. Beim Keilzinken entstehen somit standardisierte Bretter – gemacht für den Einsatz dort, wo es auf höchste Stabilität oder Ästhetik ankommt. Mehrere der so zusammengefügten Holzstücke werden in einem weiteren Arbeitsschritt quer zur Holzmaserung in Schichten zusammengeleimt oder umweltfreundlich mit harten Buchenholzstiften genagelt. Das Ergebnis sind 20 Zentimeter dicke Balken. Diesen Fertigungsschritt lässt Blumer Lehmann bei einem externen Unternehmen erledigen.
Vorgefertigte Elemente und Module
In einem weiteren Prozessschritt erfolgt der Holzrahmenbau. Mitarbeiter setzen aus Balken unterschiedlicher Länge das Riegelwerk zusammen und beplanken dieses. Dann schiebt sich die Multifunktionsbrücke von WEINMANN über die Wand – und nagelt, bohrt, sägt, fräst, markiert. In wenigen Sekunden befestigt sie die Beplankung und sorgt für die Öffnungen für Türen, Fenster und Schächte. Das halbfertige Element wird nun gewendet, die Hohlräume werden mit Dämmstoff gefüllt. Eine zweite Platte verschließt die Wand. Nach einer kurzen Endbearbeitung wird die Wand automatisch aufgestellt, dann geht es weiter ins Zwischenlager. Die Zimmerleute im Werk bauen Wände, Decken und Böden zu fertigen Modulen zusammen oder verpacken sie einzeln. Dann beginnt die Reise zur Baustelle per Lastwagen. Mithilfe eines Krans werden die Monteure die Fertigbauelemente dort aufstellen. In zwei bis drei Tagen steht das fertige Gebäude – ein Vorteil gerade in engen Innenstädten oder bei Kunden, wo es schnell gehen muss, beispielsweise bei Hotelerweiterungen. Deshalb geht Blumer Lehmann noch einen Schritt weiter. „Oft liefern wir die einzelnen Module bereits fertig ausgerüstet mit Elektroleitungen, Wasserrohren, Tapeten, Fliesen und Küchenzeile“, sagt Lehmann. Von der Firma beauftragte Sublieferanten kümmern sich noch im Werk darum. Achtsam mit begrenzten Ressourcen umgehen – darauf legt das Unternehmen Wert. Deshalb sorgt es dafür, dass nichts verkommt. „Von einem kompletten Baum können wir nur rund 60 Prozent in der Produktion nutzen“, sagt Lehmann. Was übrig bleibt, ist Restholz. Der Rundgang führt vorbei an zwei Türmen, die aussehen wie Silos. „Hier lagern wir die Holzpellets, die bei uns im Betrieb produziert werden.“ Und was passiert mit der Baumrinde? Auch dafür ist gesorgt. Sie wird zu Mulch geschreddert und geht in den Landschaftsbau. Oder wird zu Briketts verarbeitet und wie die Pellets im eigenen Kraftwerk verwertet. Ein Ökosystem, in dem nichts weggeworfen wird.
Autor: Heimo Fischer
Ein Artikel aus dem Kundenmagazin performance Ausgabe 20 | 2021 Mehr Informationen finden Sie hier.
„Wir kümmern uns um alle Arbeitsschritte – vom gefällten Baum bis zum fertigen Haus.“Katharina Lehmann, Geschäftsführerin Blumer Lehmann
Blumer Lehmann
Blumer Lehmann hat seinen Sitz in Gossau, einem Ort bei St. Gallen, rund 25 Kilometer südlich des Bodensees und gehört zur Schweizer Lehmann Gruppe. Es ist eines der führenden Holzbauunternehmen des Landes und hat sich auf Free-Form Holzbauten, Modulbau und Temporärbau spezialisiert.
Mehr Informationen finden Sie hier.