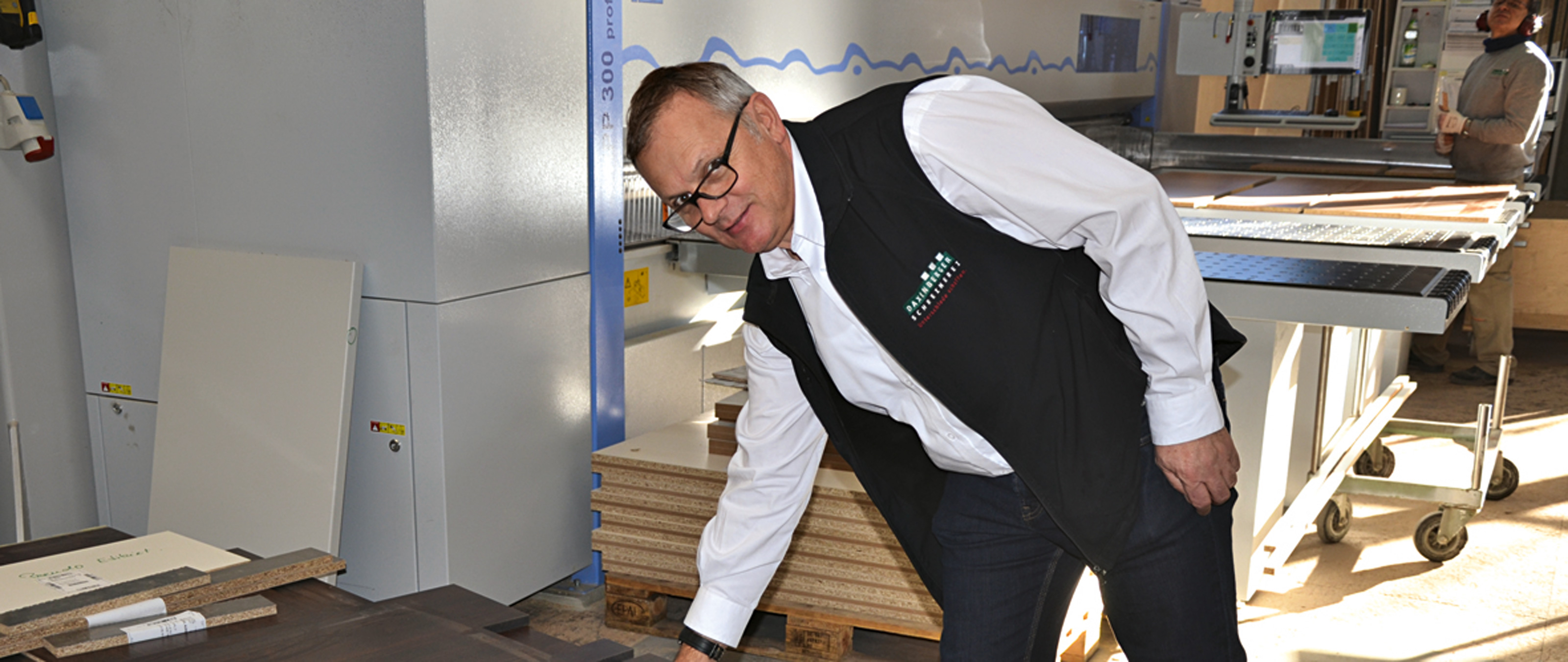
Auch wenn jeder Besucher über den Maschinenpark und die Vernetzung staunt, die bisher hauptsächlich in der Möbelindustrie zu finden war: Die Schreinerei Daxenberger ist ein echter Handwerks-Betrieb geblieben. Trotzdem dominiert im Unternehmen von Bernhard, Josef und Simon Daxenberger modernste Technik, die von einer Säge-Lager-Kombination bis zu verschiedenen Bearbeitungszentren und Software-Lösungen reicht. Die HK besuchte den Vorzeige-Schreiner in Seeon am Chiemsee.
Den Werbespruch „Wachsen mit der HOMAG Group“ haben sich die Brüder Daxenberger zu Herzen genommen. Ihre Schreinerei rüsteten sie mit modernster Technik aus: Büro-Arbeitsplätze, CNC-gesteuerte Maschinen und Software-Lösungen sind vernetzt. Barcode-Handscanner sind das Bindeglied zum Zentralrechner für jede Maschine. Das Vernetzungs-Konzept und die neuesten Maschinen kommen von der HOMAG Group. „Nur weil wir alle unsere Firmen-Abläufe vernetzt haben, sind wir kein Industriebetrieb“, räumt Bernhard Daxenberger, Schreinermeister und – wie seine Brüder Josef und Simon – Geschäftsführer der Schreinerei Daxenberger, mit einem oft gehörten Vorurteil auf. „Und wir bleiben eine Schreinerei und dem Schreiner-Handwerk mit Leib und Seele verbunden.“
Im „Bankraum“, den die Mitarbeiter eigenverantwortlich planen und für die handwerklichen Tätigkeiten einrichten durften, dominieren keine klassischen Hobelbänke, sondern hydraulische Scheren-Hubtische, die verfahrbar sind und ein Höchstmaß an Ergonomie für den Schreiner bieten. Die Erfahrungen sind so gut, dass die Daxenberger-Brüder die Anschaffung weiterer Hubtische geplant haben. Aber der „Bankraum“ weist noch eine andere Besonderheit auf, die für eine Schreinerei keineswegs normal ist: Sämtliche Energie-Versorgung erfolgt „von oben“. Steckdosen hinter Platten „verstecken“ geht nicht. Selbst Staubsauger sind „über-Kopf“ installiert, die – so sauber aufgeräumt – nirgends im Weg stehen können.
Was für den „Bankraum“ gilt, findet seine Bestätigung auch im Maschinenraum. Sämtliche Maschinen sind nach ihrer Funktion längs des Materialflusses optimal platziert: „So haben wir mehr Platz und kürzere Wege“, wie Bernhard Daxenberger erläutert. Am Anfang der Produktionslinie steht der Zuschnitt – links für Plattenmaterial, rechts für Massivholz. Dem schließt sich die einseitige Kantenanleimmaschine KR 77 Optimat von HOMAG an, die ihren Input von der Plattensäge bekommt, mit einer automatischen Teile-Rückführung ausgerüstet ist und mit einem einzigen Maschinenbediener auskommt.
Direkt danach ist ein CNC-gesteuertes Bearbeitungszentrum BOF 311 profiLine platziert, das schon die zweite Maschine dieser Art bei Daxenberger ist und die komplexen Arbeitsaufgaben beim Fräsen und Bohren bewältigt. Für die Standard-Aufgaben beim Bohren und Fräsen von Möbelteilen wurde ein WEEKE-Bearbeitungszentrum BHX 055 Optimat angeschafft, das sich bei Daxenberger bestens bewährt hat. „Diese Maschine arbeitet so effizient, schnell und präzise, dass sich ihre Investition mehr als gelohnt hat“, schwärmt Bernhard Daxenberger von der kleinen Maschine, die links des Produktionsflusses positioniert ist. Zuvor, zwischen Plattensäge und BHX, steht ein Fenster-Automat, dessen Flexibilität nicht gefordert wird, denn er ist nur mit Werkzeugen für ein einziges Profil ausgestattet. „Weil wir nur diesen Typ von Fenster bauen, was sich bewährt hat, brauchen wir an dieser Stelle auch nicht so flexibel aufgestellt zu sein wie ein Fenster-Spezialist“, argumentiert der Daxenberger-Chef. Nach zwei Schleifmaschinen schließt sich die Oberflächenbearbeitung an, die aus zwei Bandschleifmaschinen und zwei Lackierstationen besteht.
Was man bei Daxenberger nicht sieht, sind zig Transportwagen mit Bergen von Teilen, die überall, wo gerade Platz ist, in den Hallen „geparkt“ werden. Und deren Suche dann mit viel Zeitverlust verbunden ist. „Dank unserer Organisation der vernetzten Fertigung wird bei uns nichts gesucht, wir wissen immer, wo sich das zu bearbeitende Material befindet“ – in der Erklärung von Bernhard Daxenberger schwingt eine gute Portion Stolz über das Erreichte mit. Rein äußerlich ist das Barcode-Label, das an der Plattensäge ausgedruckt und auf jedes Einzelteil geklebt wird, ein ganz entscheidender Organisationsfaktor in der vernetzten Fertigung. Denn der Bar-code identifiziert nicht nur das Teil, sondern er ermöglicht auch den Zugriff auf Stückliste und Arbeitsplan. Wenn denn die Werker den Barcode lesen könnten. Dafür wiederum haben die Daxenberger-Brüder Barcode-Handscanner im Einsatz .
Aber das reichte den Daxenbergers noch nicht. Sie wollten die volle Durchgängigkeit von Rechner und Software, die Standard-Software „Schreiner-Plus“ sollte sich mit der Imos-3D-Software und den Maschinensteuerungen „verstehen“ können. Da kamen ihnen die Erfahrungen der HOMAG Group sehr entgegen, die für sich in Anspruch nimmt, Pionier der vernetzten Fertigung zu sein. Und mit Friedrich Schweiger, HOMAG-Area-Manager Bayern Südost, der über viele Jahre das Haus Daxenberger betreut und ein Vertrauensverhältnis aufgebaut hat, stand ihnen ein ehrlicher Berater zur Seite. „Uns war klar, dass der Kauf von Maschinen und verschiedenen Software-Programmen nicht ausreichend sein würde und hatten uns schon auf viel interne Arbeit eingerichtet“, plaudert Bernhard Daxenberger aus dem Nähkästchen. „Aber es hat sich gelohnt. Ich möchte nicht mehr so arbeiten wie früher.“
Heute steht am Anfang der Prozesskette eine Plattenaufteilsäge der Baureihe 3 von HOLZMA. Daxenberger hat das Modell HPP 300 profiLine gekauft, „weil wir schon gute Erfahrungen mit der Vorgänger-Maschine von HOLZMA hatten“. Diese neue Säge ermöglicht auch den Zuschnitt großer Platten von bis zu 5 600 mm Länge und lässt sich preiswert an ein Lagersystem anbinden. Darüber hinaus musste ein perfektes Handling auch mit nur einem Maschinenbediener möglich sein. Daxenberger war es außerdem wichtig, dass sich die Plattenaufteilsäge vernetzen ließ und sie den Verschnitt auf ein Minimum reduzieren konnte. Darum spielten Features wie „Resteverwaltung“, „Reste-Etikettierung“ und „Scanner-Anbindung“ eine besondere Rolle. Auch das „Dünnteile-Paket“ wird bei Daxenberger eingesetzt.
Aber erst in der Kombination von Säge und Lager lassen sich die Vorteile ausschöpfen, die sich aus optimaler Maschinen-Auslastung und minimalem Platzbedarf der bevorrateten Platten ergeben und in Zeit und Effektivität messbar sind. Dabei glänzt das Plattenlager TLF 211 von HOMAG Automation – wie es bei Daxenberger steht – durch sein Optimierungs-Potenzial: Es werden Verkehrswege eingespart und dadurch mehr Platz für Platten generiert.
Die Saugtraverse ST61 betreut den Transport innerhalb des Lagers und die Übergabe zur HOLZMA-Säge. Und die kennt dadurch so gut wie keine Leerlauf-Zeiten. Die Daxenbergers haben sich einen Wettbewerbsvorteil ausgerechnet, der allein über die Zeitersparnis entsteht, weil das automatische Flächenlager einfach schneller ist – es kennt „Suchzeiten“ nicht. So lässt sich leicht eine Steigerung der Produktivität um bis zu 40 Prozent erzielen – und das bei gleichbleibendem Personalbedarf.
So haben sich die Daxenbergers eine Amortisationszeit errechnet, die sich sehen lassen kann. Bernhard Daxenberger war vom guten Preis-Leistungs-Verhältnis überrascht und prognostiziert, „dass die Anlage in fünf Jahren bezahlt ist.“ Friedrich Schweiger, der HOMAG-Vertriebsmann geht noch einen Schritt weiter und sagt: „Die Kombination von Lager und Säge rechnet sich bereits ab 20 zu sägenden Platten pro Tag.“ Auch Bernhard Daxenberger ist überzeugt, dass die Kombination aus Plattensäge HPP 300 und Flächenlager TLF 211 auch für kleinere Schreinereien sehr interessant ist. Denn das intelligente Reste-Management senkt die Produktionskosten in jedem Betrieb spürbar. Das richtige Materialhandling ist ein Schlüssel zum Erfolg für die kosteneffiziente Fertigung, heißt es bei HOMAG. Das beginnt bei der Bestellung neuen Materials und schließt die Verarbeitung kleinteiliger Materialreste ein. Als ein Bestandteil der neuen Lagersteuerung woodStore 6 bietet HOMAG Automation mit OffCutPro das passende Modul für die Lagerverwaltung für große bis kleine Restteile.
Die computergesteuerte Schreinerei
Die Schreinerei Daxenberger wurde 1963 von Josef Daxenberger gegründet – damals natürlich noch ohne Computer. Der junge Schreinermeister startete in der Garage der Schwiegereltern mit einer Werkstattfläche von 60 Quadratmetern. Zwei Jahre später wurde der erste Geselle eingestellt, 1966 kam der erste Schreiner-Lehrling dazu. Im Jahre 1970 erfolgte der erste große Werkstatt-Neubau und nach dem letzten Anbau in Truchtlaching 1988 betrug die Nutz- und Lagerfläche 1 000 Quadratmeter. Die Philosophie des Gründers – beste persönliche Kontakte und erstklassige Arbeit – ließ die Firma weiter wachsen und erzwang so einen Neubau auf der grünen Wiese im benachbarten Seeon. Nach 18-monatiger Bauzeit erfolgte im Oktober 1996 der Umzug mit inzwischen 35 Mitarbeitern in die neue Betriebsstätte. 1997 zog sich der Gründer Josef senior zurück – und die Söhne Bernhard, Josef und Simon übernahmen die Geschäftsführung der Schreinerei. Die drei Söhne haben das Erbe weiter entwickelt und ihre Schreinerei mit modernsten Maschinen und Computer-Technik ausgestattet. Dabei legen sie großen Wert auf die Feststellung, dass ihre Schreinerei – inzwischen auf 85 Mitarbeiter angewachsen – ein Handwerksbetrieb geblieben ist. 80 Prozent des Umsatzes werden mit Privatpersonen erwirtschaftet, denen hervorragende Qualität und exklusive Schreiner-Arbeit sehr wichtig sind. Durch die Computer-Durchdringung des Betriebes und den relativ hohe Automatisierungsgrad sehen sich die drei Brüder auch bei Ausschreibungen gut aufgestellt. Das ist ihr Motto: Unterschiede schaffen. Dafür setzen sie erstklassige Materialien ein, verarbeiten diese perfekt und garantieren neben der handwerklichen Erfahrung den berühmten Daxenberger-Service.
Fotos: HK – Holz- und Kunststoffverarbeitung / Norbert Schmidt
Ein Artikel des Fachmagazins HK, Ausgabe 02/2016. www.hk-magazin.com