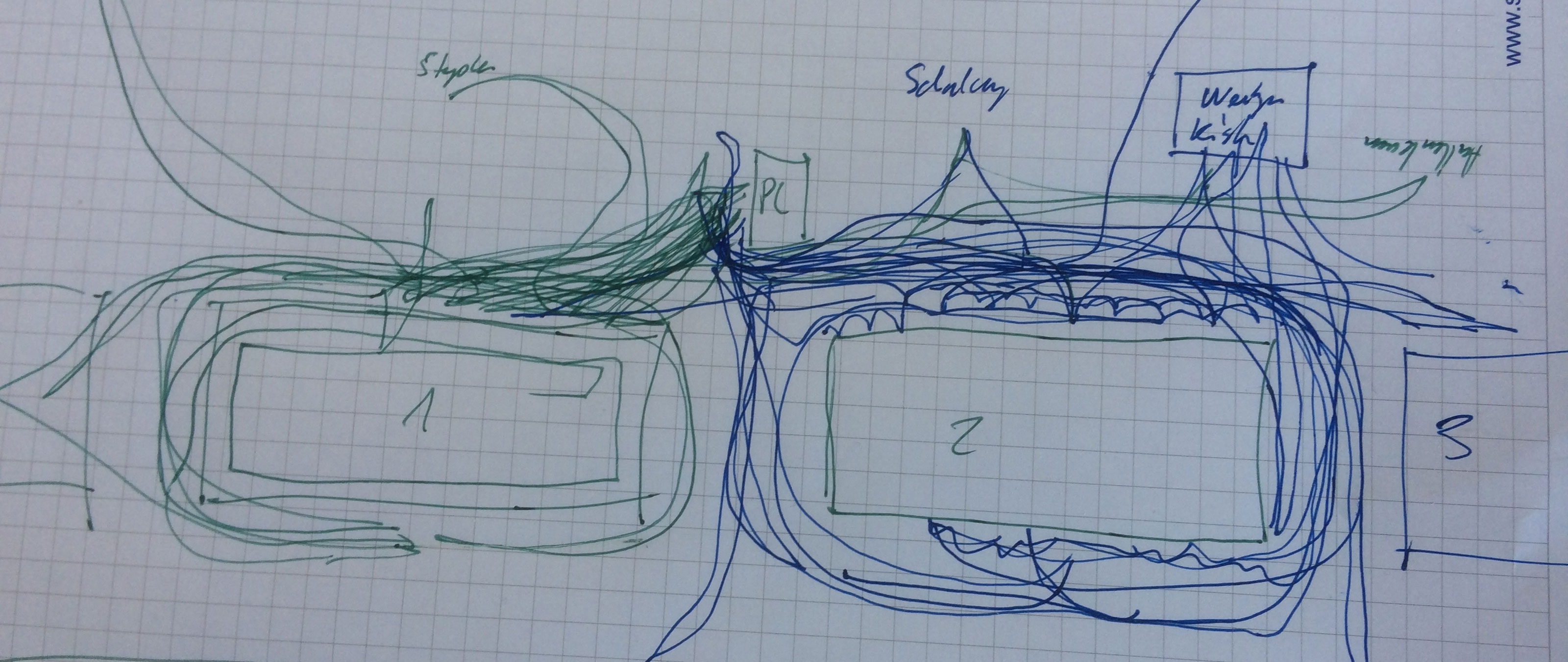
Es gibt kaum einen Berufszweig, der so viel unterschiedliches Material und in so grossen Mengen auf die Baustelle transportieren muss wie der Holzbau. Für die Elementfertiger kommt das Material zwar in zwei Stufen – zuerst in die Vorfertigung und dann auf die Baustelle –, dafür aber in kürzeren Abständen und innerhalb eines engen Zeitrahmens. Wenn dann bei Umbauten noch die Baukoordination mit weiteren Unternehmen hinzukommt, steigt die Komplexität an. Übertroffen wird das nur noch durch täglich wechselnde Einsatzpläne, die beispielsweise Krankheit, Maschinenausfällen oder anderen Feuerwehrübungen geschuldet sind. Dementsprechend kann ein Unternehmen mit der Logistik viel Geld gewinnen oder verlieren.
Logistik im Holzbau hat oft mit Rufen, Gehen und dem Hallenkran zu tun. Doch eigentlich ist Logistik die Planung, Steuerung und Optimierung des Material- und Informationsflusses, mit dem Ziel, wertschöpfend zu sein. Die Mitarbeiter sollen an ihren Arbeitsplätzen das nötige Material stets griffbereit haben und sich ganz auf die Produktion konzentrieren. Das funktioniert meist nur begrenzt, denn oftmals müssen sich die Mitarbeiter am Elementtisch auch noch um den Nachschub kümmern. Dass immer das richtige Material in ausreichender Menge bereitliegt, sollte jedoch in der Verantwortung des Logistikers liegen. Damit dieser nicht nur Feuerwehr spielen muss, sind eine entsprechende Organisation und Lagereinrichtung erforderlich.
Gehen, suchen, rückfragen
Zwar ist jedes Unternehmen, jede Baustelle und jedes Bauvorhaben anders; auch die Raumverhältnisse und die Tätigkeiten wechseln, doch es gibt viele Ähnlichkeiten. Wer in der Produktion eines Unternehmens einige Minuten stehen bleibt und einfach nur zusieht, was passiert, merkt schnell, wie viel die Mitarbeitenden gehen. Die Gehwege und Distanzen sind in der Produktionshalle meist zu lang. Viel zu oft verlassen die Mitarbeitenden ihren Arbeitsplatz und holen dieses, suchen jenes oder laufen für Rückfragen ins Büro. Im Durchschnitt legt ein Produktionsmitarbeiter pro Tag zwölf Kilometer zurück. Wer das nicht glauben mag, sollte einmal Schrittzähler verteilen! Durch die überflüssigen Wege geht viel Produktionszeit verloren. Das Gleiche gilt auch auf der Baustelle. Es würde sich also lohnen, die Gehkilometer zu halbieren.
Logistik muss gesteuert werden
Logistik hat mit Reihenfolgen, Abläufen und ganz viel mit Entscheiden zu tun. Egal ob als Logistiker, Verantwortlicher für die Logistik, Wareneingangsverantwortlicher oder als Staplerfahrer: Es ist eine Person erforderlich, die den Überblick behält, die Prozesse steuert und damit am Laufen hält. Diese Person muss auch dann vor Ort sein, wenn eine Entscheidung ansteht. Weiter muss diese Person erkennen oder wissen, wo als Nächstes Material nachzufüllen ist, wann der nächste Materialwechsel oder die Umrüstphase ansteht. Die Logistik beginnt bereits in der Phase der Planung und des Einkaufs. Viel zu häufig wird Material zu früh oder zu spät angeliefert. Abhilfe bringt hier ein Produktionsverantwortlicher, der vor Ort ist und das Material nur abruft, wenn es gebraucht wird. Der Produktionsverantwortliche macht die Vorgaben, welche Elemente am jeweiligen Tag gefertigt werden. Er kennt somit den Materialbedarf, hat die zeitliche Übersicht und das Wissen, welches Material schon bereitliegt.
Die Werkhalle ist keine Lagerhalle
Zu oft wird die Produktionshalle als Lagerhalle missbraucht. Doch direkt am Elementtisch, an dem gearbeitet wird und Flexibilität wichtig ist, sollte kein Lagermaterial stehen. Dort muss das Material fliessen – das heisst: hinstellen, verbrauchen, nachliefern. In den Produktionen, in denen sich «Berge erheben», fehlt die Übersicht. Als Faustregel gilt, dass nie mehr Material als für zwei Tage rund um den Elementtisch steht. Wenn nur schon das Lagermaterial und die nicht mehr benötigte Ware aus dem Fertigungsbereich verschwinden, ergibt sich eine übersichtliche Produktion mit kurzen Wegen.
Materialtransport in der Halle
Für die Materialbereitstellung in der Werkhalle ist der Stapler ein geeignetes Transportmittel. Doch wer hat schon rund um den Elementtisch Platz für zwei Staplergassen? Ausserdem steht der Stapler selten da, wo er gerade gebraucht wird. Also behilft man sich und holt den Hallenkran. Eine gute Lösung wären Transportrollenbahnen, die viel Zeit einsparen helfen und einen guten Materialfluss ermöglichen. Damit können beispielsweise Paletten mit Isolation und Stapel mit Gipsplatten von Hand an den Tisch geschoben werden. Und wenn die Transportrollenbahn leer ist, wird einfach der nächste Stapel nachgeschoben. Häufig werden die Arbeitsmaterialien auch an eine Ecke des Elementbautisches gestellt. Das hat zur Folge, dass die Mitarbeitenden dann über die ganze Länge der Elemente hin- und herlaufen, um beispielsweise die Gipsplatten auf das Element aufzulegen. Warum den Stapel nicht mit einem Wagen oder einer Ameise entlang dem Element fahren und die Platten einfach herunterziehen? Bei manchen Fertigungskonzepten, unter anderem wenn Plattenmaterialien vorgängig zentral zugeschnitten oder gefräst werden (Nesting), ist der Materialfluss in der richtigen Reihenfolge entscheidend. Dafür braucht es neben dem geeigneten Transportmittel auch klare Informationen für einen geordneten Ablauf. Egal wie – wenn der Logistiker das Material nicht zur richtigen Zeit an den Arbeitsplatz bringt, holen sich die Mitarbeitenden das Material und teure Wertschöpfungszeit wird verschwendet. Umso mehr, wenn durch das Fehlen eines Mitarbeiters am Elementbautisch die Gesamtleistung des Teams weiter sinkt als nur um diese eine Person.
Aufwand durch Werkslieferung
Der Preis für eine ganze Werkslieferung Weichfaserplatten ist proportional eindeutig tiefer als für eine halbe oder für einzelne Paletten. Doch nur wenige Unternehmen haben ausreichend Platz, um 32 Paletten zu lagern, ohne dass die Auswirkungen im ganzen Unternehmen spürbar sind. Das sieht in der Praxis dann so aus: Zunächst diskutiert der Projektleiter den Preisunterschied mit dem Geschäftsführer, dann folgt der Entscheid, eine ganze LKW-Ladung zu bestellen. Der Produktionsleiter sucht mit zwei Mitarbeitern auf dem ganzen Areal nach möglichen Lagerplätzen. Mit dem Stapler wird vorhandenes Material umgelagert, das erst später benötigt wird. Altes Material muss entsorgt werden, doch damit beginnen vielschichtige Abklärungen darüber, wer bestimmen soll, was weg darf. Wenn der LKW dann eintrifft, wird rasch abgeladen und der ganze Vorplatz steht voll mit Paletten. Diese werden nun an allen (un-)möglichen Plätze versorgt. Teils stehen bis zu drei Paletten übereinander mitten in der Produktionshalle. Die letzten Pakete müssen mit Hallenkran und Gurten positioniert werden. Durch die Paletten ist nun auch der direkte Weg vom Elementtisch an die Kappsäge versperrt. Auch wenn der Umweg im Durchschnitt «nur» zehn Meter beträgt, werden daraus an den nächsten Arbeitstagen unnötige Kilometer. Zusammen mit der Unterbringung der Paletten auf dem Gelände verursacht diese Bestellung einen Mehraufwand von mehreren Stunden, die dann nicht einmal dem Projekt belastet werden, sondern in den «unproduktiven Stunden» verschwinden.
In der kommenden Ausgabe von «Wir Holzbauer» wird aufgezeigt, was der Logistiker im Holzbauunternehmen braucht, damit er sein System sauber aufbauen und mehr für eine effiziente Produktion leisten kann.
Text und Foto: SCHULER (Stephan Zürcher)
Ein Artikel des Fachmagazins WirHolzbauer, Ausgabe 01/2018. Hier lesen Sie den Artikel online.