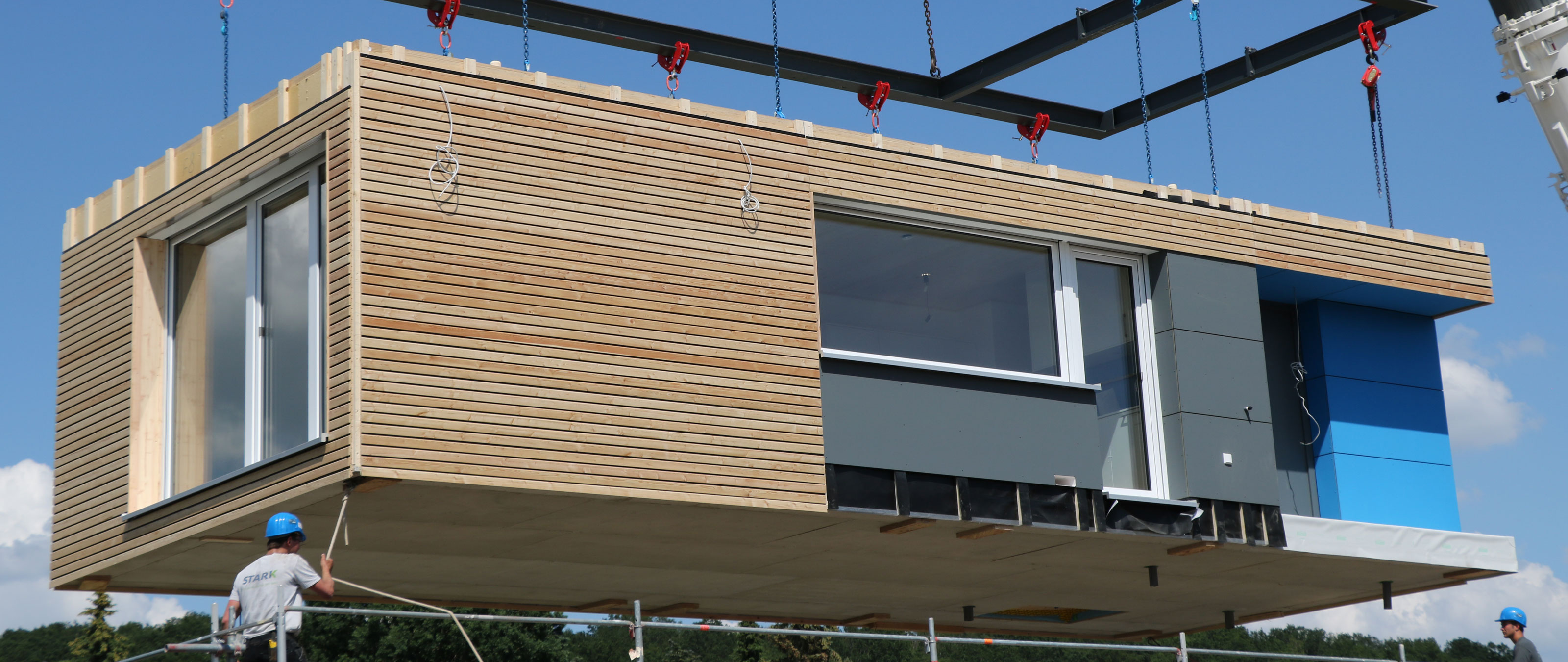
Knapp zehn Jahre nach ihrem Einstieg in den Modulbau ist die Zimmerei Stark GmbH im bayerischen Auhausen eine der ersten Adressen auf diesem Gebiet. Eine Position, die sich unter anderem darin niederschlägt, dass sie sich gerade einen Auftrag für Bundeswehrunterkünfte gesichert hat. Außer im Modulbau ist die Zimmerei mit 170 Mitarbeitern im Ein- und Mehrfamilienhausbau, in der Hauserneuerung, dem Bau von Hallen, Gewerbeobjekten, landwirtschaftlichen Gebäuden und Schäferwagen aktiv. Dabei spielt der Holzrahmenbau immer noch eine wichtige Rolle, weil er für Geschäftsführer Martin Stark vor allem bei individuellen Planungen und großen Raumvolumina entscheidende Vorteile hat. Ihre Position im Modulbau hat sich die Stark GmbH zum einen mit einem selbstentwickelten Modulkonzept erarbeitet, mit dem man bis zu fünf Module übereinander setzen kann, ohne Setzungen im Gebäude zu bekommen. Dies ist insofern bemerkenswert, als man die Module bis auf die Decke aus Holzrahmenelementen fertigt. „Dadurch profitieren wir von einem Synergieeffekt, weil wir im Holzrahmen- und im Modulbau mit einem in sich geschlossenen System arbeiten, ohne zwischen unterschiedlichen Details zu wechseln“, erläutert Martin Stark. Gefertigt werden Holzrahmenelemente und Module im Effizienhaus-55-Standard und besser.
Modulbau auch für private Bauherren
Verantwortlich für die gute Marktposition im Modulbau ist außerdem ein Geschäftsmodell, das nicht nur gewerbliche und öffentliche, sondern auch private Kunden anspricht. In Auhausen baut man deshalb nicht nur Großprojekte wie Hotels und temporäre Schul- oder Bürogebäude aus Modulen, sondern auch barrierefreie Wohnkonzepte für Senioren, „tiny houses“ als kostengünstigen Einstieg ins Wohneigentum, der sich im Lauf der Jahre an wechselnde Nutzeransprüche anpassen lässt, oder mobile Häuser für Familien, die damit rechnen, aus beruflichen Gründen ihren Wohnort wechseln zu müssen. In diesem Fall ziehen sie mit Haus und Hausrat auf ein neues Grundstück um – selbst die von Stark verlegten Streifenfundamente sind recycelbar. Inzwischen patentiert ist das „Wohnen auf Mietgrund“: Temporär nicht genutzte Grundstücke in Immobilien-Hotspots werden hier auf Zeit angemietet und mit einem Wohnhaus bebaut, was kostengünstiges Wohnen in guter Lage ermöglicht. Die Zimmerei Stark betreibt selbst ein Modul-Musterhaus auf Mietgrund am Starnberger See. Läuft die Befristung ab, wandern die Modulhäuser mitsamt Inventar stressfrei an einen anderen Wohnort. Eine weitere Besonderheit der Auhausener Zimmerei ist ihre große Fertigungstiefe: Kunden können nicht nur das Modulgebäude, sondern auch einen Großteil der Inneneinrichtung erwerben. So produziert die ins Unternehmen integrierte Schreinerei Möbel und Küchen, die zusammen mit Küchen anderer Marken, Elektrogeräten und Accessoires im firmeneigenen Möbelstudio vertrieben werden. Wer Wert auf Komfort legt oder wenig Zeit hat, kann sich bei Stark ein Modulhaus inklusive Küche, Bad, Mobiliar und Accessoires aufs Grundstück liefern lassen. Das Haus mit Küche ist für die Auhausener inzwischen quasi Standard. „Nur Gläser und Geschirr räumen wir später ein. Die hohe Servicetiefe haben wir als ländlicher Mittelständler, der viele Wünsche bedienen muss, den Großen der Branche voraus.“ All diese guten Ideen haben der Zimmerei Stark in den letzten Jahren eine stabile Nachfrage nach Modulgebäuden beschert. Im privaten Hausbau, der 30 Prozent des Gesamtumsatzes ausmacht, liegt der Marktanteil der Module bei 10 Prozent, im öffentlichen und gewerblichen Bau, wo man 2018 auch in den modularen Bau mehrgeschossiger Wohnanlagen eingestiegen ist, beträgt ihr Anteil 5 Prozent. 130 Module hat die Zimmerei in den letzten neun Jahren gefertigt und montiert. Sie rechnet für diesen Geschäftsbereich auch in der Zukunft mit einer stark steigenden Tendenz.
Tiefgreifende Umstrukturierung
Diese Entwicklung spiegelt sich nicht nur in einem modernen Modul-Musterhaus am Firmenstandort wieder, sondern auch in einer an die neuen Zielsetzungen angepassten Firmenstruktur. Erst kürzlich hat das Unternehmen eine neue Halle in Betrieb genommen, mit der es den Schritt von einer manuellen zur automatisierten Fertigung vollzogen hat. Im rechten Hallenschiff befindet sich die neue Fertigungslinie für Holzrahmenelemente, deren Kernstück eine WEINMANN Multifunktionsbrücke WALLTEQ M-380 insuFill mit integrierter Einblasplatte und zwei Arbeitstischen ist. Die Einblasplatte ist mit einer Steuerung versehen, die das vollautomatische Einblasen auch kleinerer Gefache möglich macht. Ein dritter WEINMANN Montagetisch für die Fassadenmontage und ein Arbeitstisch für Sonderelemente vervollständigen die Fertigungslinie, ein Verteilwagen übernimmt den Weitertransport fertiger Elemente zu Fassadenbau, Fenstereinbau, Zwischenlager, Verladestation und Modulbahnhof. An letzterem werden die Holzrahmenelemente per Kran aufgenommen und zu der 100 m langen Modulbahn im linken Hallenschiff weitertransportiert, auf der die Module zusammengebaut werden. Hier können die Stark-Mitarbeiter bis zu 25t schwere Module über Schienen von Hand zu den einzelnen Arbeitsstationen weiterschieben. Um die Bearbeitungstätigkeiten von den Montagearbeiten zu trennen, befinden sich der Stab- und Plattenabbund in einer separaten Fertigungshalle. Die WALLTEQ M-380 insuFill ist in Auhausen für das Befestigen der Beplankung und das Einblasen der Dämmung zuständig.
Lastenheft mit vielen Anforderungen
Die Planung und Ausstattung der Halle war das Ergebnis eines drei Jahre dauernden Vorbereitungsprozesses. „Wir haben uns dafür viel Zeit genommen, verschiedene Anlagen und Hersteller verglichen und anhand unseres Lastenheftes überprüft.“ Dabei erfüllte die Fertigungslinie von WEINMANN mit Abstand die meisten Anforderungen, zu denen unter anderem die Kombination von Elementbearbeitung und vollautomatischem Dämmen gehörte, außerdem die Vorgabe, extraschwere Elemente bis 3,5t in Dimensionen bis 3,70 x 12,00 m fertigen zu können. Auch das Hallenlayout nach Maß, die Planung des Workflows, der bewährte Verteilwagen und die Nähe zum Hersteller sprachen für den Maschinenbauer aus St. Johann-Lonsingen: „Hinzu kam eine kompetente Betreuung durch unseren Projektleiter, zu der später eine partnerschaftliche Zusammenarbeit mit den Maschinen-Monteuren kam. Im Rückblick kann ich sagen, dass wir zu 100 Prozent die richtige Entscheidung getroffen habe – vor allem, wenn ich von anderen Holzbauunternehmen höre, was bei ihnen in der Fertigung läuft oder auch nicht läuft“, zieht Martin Stark Bilanz. Die Anlaufphase der neuen Fertigungstechnik in seinem Unternehmen beurteilt er als „sehr gut. Wir haben aus dem Stand heraus produziert.“
Umfassende Digitalisierung
Um dieses Ziel zu erreichen, hat man sich in Auhausen akribisch auf die neue Technik vorbereitet. Fast zwei Jahre im Voraus hatte man ein Ingenieurbüro beauftragt, Abläufe und Details auf die neuen Maschinen hin zu optimieren. „Als die Technik in der Halle stand, hatten wir die digitalisierten Details schon auf den Rechnern.“ Aber nicht nur die Details: Für alle Wand-, Tür- und Fenstertypen ließ man in Auhausen Makros entwickeln, die man heute bei der Planung nur noch in die Dateien hineinziehen muss. Die Elementplanung ist mit diesem Schritt bereits größtenteils erledigt. Der Aufwand im Vorfeld zahlt sich deshalb heute in Zeit- und Kostenvorteilen aus. Und die Zimmerei hat noch eins draufgesetzt: „Um den Prozess von der Werkplanung über die Arbeitsvorbereitung bis in die Produktion durchgängig zu machen, haben wir als übergeordnete Prozesssteuerung die Software Granit installiert. Sie ermöglich uns zum Beispiel auch die Fertigung von Multiwänden. So können wir unseren Workflow und unsere Hängerauslastung optimieren.“ Der Verladevorgang wird bereits weitgehend digital gesteuert, Daten zu Volumen und Gewicht der Bauteile liegen bereits aus der AV vor. Und auch in den anderen Abteilungen der Zimmerei arbeitet man fast nur noch auf dem Rechner. So läuft jedes Projekt im Unternehmen mit permanent aktualisiertem Status durch den digitalen Workflow: von der Digitalisierung der Baustelle über die Vermessung mit einem Tachymeter über die Planung, Statik, Arbeitsvorbereitung und CNC-Fertigung bis hin zur Montage. Prozesse wie die Kalkulation, der Einkauf, die Nachkalkulation werden auf der Basis der erhobenen Daten weitgehend automatisch abgearbeitet. Für Martin Stark das Resultat „eines unendlichen Prozesses, in dem wir uns kontinuierlich weiterentwickeln werden.“
Höhere Qualitätbei den Arbeitsplätzen
Schon angesichts des in den letzten Jahren durchmessenen Weges könnte es einem Betrachter auf den ersten Blick schwindlig werden. Dies erging auch manchem Mitarbeiter so, als die umfassende Digitalisierung aller Prozesse im Vorfeld diskutiert wurde. „Die größte Angst dabei war, mit der schnellen Entwicklung nicht Schritt halten zu können“, erinnert sich Martin Stark. Und heute? „Ist die Skepsis von vor vier Jahren verflogen, freuen sich die Mitarbeiter über angenehme, ergonomische Arbeitsplätze in hellen Hallen mit Fußbodenheizung. Viele unserer Auszubildenden bleiben im Unternehmen, jeder zieht am gleichen Strang, jeder kommt voran und gibt sein Bestes.“ Mancher hat durch die Umstrukturierung sogar seinen Arbeitsplatz behalten, streicht zum Beispiel dank Modulbau heute Fassaden in der Halle, weil er aus gesundheitlichen Gründen nicht mehr aufs Gerüst darf. Das Versprechen, alle Mitarbeiter, die sich für das Unternehmen einsetzen, bis in die Rente zu führen, war für Martin Stark einer der Gründe, in den Modulbau einzusteigen: „So können wir Arbeitsplätze für ältere und körperlich eingeschränkte Mitarbeiter schaffen, die wir sonst vielleicht nicht halten könnten.“ Natürlich sieht der Unternehmer auch die anderen Vorteile der Modulbauweise: „Synergieeffekte und Kostenvorteile dank Wiederholung, hoher Vorfertigungsgrad, witterungsunabhängige Fertigung in hoher Qualität, kurze Montagezeiten, vor allem bei langer Anlieferung." Was er unter „kurz“ versteht, verdeutlicht Martin Stark am Schluss an einem gerade erst errichteten Zweifamilienhaus mit vier Modulen: „Die Module wurden in der Nacht zum Montag angeliefert und waren bis 11:46 Uhr montiert. Da konnten unsere Mitarbeiter den Autokran abschlagen und nach Hause fahren.“
Autor und Fotos: Dr. Joachim Mohr
Ein Artikel aus dem Fachmagazin Mikado, Ausgabe Oktober/2020. Mehr Informationen finden Sie hier.
„Dadurch profitieren wir von einem Synergieeffekt, weil wir im Holzrahmen- und im Modulbau mit einem in sich geschlossenen System arbeiten, ohne zwischen unterschiedlichen Details zu wechseln.“Martin Stark, Geschäftsführer Zimmerei Stark
Zimmerei Stark GmbH
Die im Jahre 1920 gegründete Zimmerei Stark beschäftigt mittlerweile über 170 Mitarbeiter und ist einer der größten Anbieter in dieser Region. Bei der Firma Stark wird Tradition mit modernster Technik verbunden. Dies ermöglicht ein umfassendes Leistungsangebot.
Website