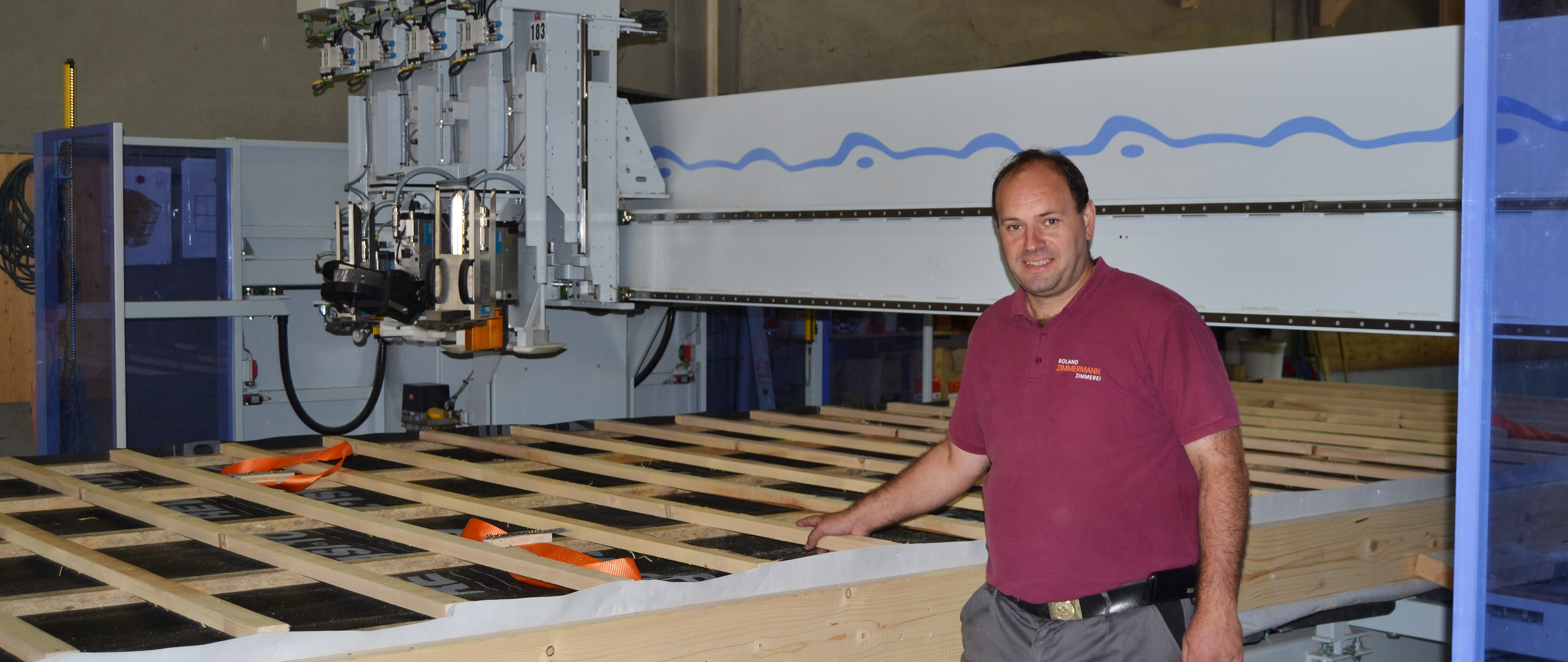
Die automatisierte Fertigungslinie, die er letztes Jahr bei WEINMANN in Auftrag gab, musste also sehr vielseitig sein. Wie vielseitig, erfuhr er, als sie Freiformen vorfertigte, bei denen seine Abbundanlage streikte.
Bereits seit einigen Jahren ist zu beobachten, wie im handwerklichen Holzbau nach dem Abbund auch die Elementierung zunehmend automatisiert wird. Dabei gibt es natürlich andere Prioritäten als im industriellen Fertigbau, wo in der Regel wesentlich höhere Stückzahlen über die Fertigungslinien laufen. Für Zimmereien steht neben einem Zugewinn an Präzision vor allem die Vielseitigkeit der automatisierten Fertigungsanlage im Vordergrund. Dies zum einen, weil möglichst alle im Unternehmen produzierten Elemente über die Linie laufen sollen, zum anderen, weil viele Zimmereien ihren Kunden keine standardisierten Bauteile, sondern ein breites Spektrum an verschieden aufgebauten Wand-, Decken- und Dachelementen anbieten. So auch die Zimmerei Roland Zimmermann in Bad Peterstal-Griesbach, die im Frühjahr 2016 in eine Kompaktanlage der Firma WEINMANN investiert hat.
Freiformen auf der Kompaktanlage
Wie vielseitig seine neue Fertigungslinie ist, wurde Roland Zimmermann erst vor einigen Monaten klar. Damals hatte er den Auftrag, für einen Kunden in Frankreich Bauteile für eine Kuppel vorzufertigen. Dabei fielen ihm in den Plänen Bauteile auf, die nicht im Auftragsvolumen enthalten waren. Nach Rückfrage in Frankreich erhielt er die Auskunft, das sei der Kuppelfuß, den solle er ebenfalls vorfertigen.
Der Kuppelfuß besteht aus acht massiven, übereinanderliegenden Holzringen, die wiederum aus jeweils 16 ineinandergreifenden Ringsegmenten bestehen. Die Radien dieser Segmente ließen sich laut Hersteller nicht auf der Abbundanlage bearbeiten, weshalb Zimmermann nach einer anderen Lösung suchen musste.
Damals fiel dem Zimmermeister seine Schulung bei WEINMANN wieder ein: „Ich hatte von der Schulung noch im Hinterkopf, dass im Software-Paket meiner Kompaktanlage ein HOMAG-Programm hinterlegt ist, mit dem sich auch Freiformen ausführen lassen.“
Nach der Kontaktaufnahme mit WEINMANN und HOMAG wurde an einer Lösung gearbeitet: „Servicetechniker beider Firmen haben das Problem für mich gelöst. Wir haben uns spezielle Fräser und ein Probeholz gekauft, HOMAG hat für uns die Fräsbahnen generiert, und am Ende haben wir den Kuppelfuß auf unserer Multifunktionsbrücke vorgefertigt.“
Flexibilität „in allen Variationen“
Nun ist es nicht so, dass Roland Zimmermann jeden Tag einen solchen Auftrag auf den Tisch bekommt. Flexibilität stand aber schon ganz oben in seinem Pflichtenheft, als er auf die Suche nach einer automatisierten Elementfertigung ging. Schließlich bearbeitet er mit seinen 10 Mitarbeitern nicht nur typische Zimmerei-Geschäftsfelder wie Dachstühle, Sanierungen, Dachumdeckungen oder Hallenbau. Er ist auch im Wohnhausbau aktiv, wo er über Mundpropaganda, Architektenausschreibungen und einen kooperierenden Bauträger an Aufträge kommt, die er in einem Lieferradius von etwa einer Stunde Fahrzeit abwickelt. Insgesamt kommen so zehn bis 15 Hausprojekte im Jahr zusammen – und das „in allen Variationen“.
Letzteres heißt nicht nur, dass er seine Wandelemente mit oder ohne Installationsebene liefert und dass die Dämmstärken und -materialien variieren. Hin und wieder verlässt der Zimmerer auch den Bereich der Holzrahmenkonstruktionen und baut mit TJI-Trägern oder mit Brettsperrholzelementen, die auf der Baustelle mit einer Außendämmung versehen werden. Bei einem Projekt fräste die WMS 150 OSB-Platten für eine Rohbau-Schalung, bei einem anderen formatierte sie Dreischichtplatten und versah sie mit mehreren Nuten, bevor sie per Container als Dachschalung nach Singapur gingen.
Der Wunsch nach Flexibilität versteht sich vor diesem Hintergrund von selbst, „und den konnte mir eigentlich nur WEINMANN erfüllen. Andere Fertigungslinien eignen sich vielleicht für eine Standard-Wandfertigung im Fertighausbau, aber individuelle Außen- und Innenwände, Dach- und Deckenelemente, Sonder- und Massivholzelemente können nur die wenigsten Hersteller über ihre Maschinen laufen lassen.“
Ganz zu schweigen von der Bearbeitungstiefe: „Wir können mit dem Flex 25 Aggregat auf unserer Maschine Massivholzelemente oder Holzfaserdämmung mit einer Schnitttiefe von bis zu 200 mm bearbeiten.“
Daneben ist die individuell konfigurierbare WMS 150 der Zimmerei mit drei Nagel- und Klammergeräten, einem Inkjet-Beschrifter und der üblichen 18,5 kW Werkzeugspindel mit 12fach-Werkzeugwechsler ausgestattet. Eine Multifuktionsbrücke mit Vollausstattung, mit der man gut für die Zukunft aufgestellt ist.
Zukunftsaspekt 1: mehr Vorfertigung
Letztere schickt sich in Bad Peterstal gerade an zu beginnen. Dies merkt man zum einen an einer stetigen Erhöhung des Vorfertigungsgrads: Lieferte man früher offene Wandelemente auf die Baustelle, sind sie heute in der Regel geschlossen. Auch Decken- und Dachelemente werden auf der Kompaktanlage vorgefertigt. Dabei übernimmt die WMS 150 unter anderem die Befestigung der Dachlattung auf den Sparren.
Damit das einwandfrei funktioniert, mussten die Zimmerer zunächst einige Details an die neue Produktionsweise anpassen: „So arbeiten wir heute zum Beispiel am Dachelementstoß mit Beisparren, weil das unter anderem das Wenden erleichtert. Auch die Dampfbremse und die Unterspannbahn in den Dachelementen wurden optimiert und an den Fertigungsablauf angepasst.“
Außerdem ergänzten die Zimmerer die AV-Parameter, damit die WMS 150 alle Daten bekommt, die sie zur Bauteilbearbeitung braucht: „Das war anfangs schon etwas Arbeit, zahlt sich auf lange Sicht aber aus, weil man so Bauteilkataloge entwickelt, mit denen sich die AV-Zeiten deutlich verkürzen.“
In diesen Bauteilkatalogen sind auch die optimalen Bearbeitungsstrategien hinterlegt. Dazu gehört zum Beispiel, dass eine Aussparung nicht nur aus einer Fräsung besteht, sondern an ihren Enden einen sauberen, rechtwinkligen Abschluss durch einen Sägeschnitt bekommt.
Roland Zimmermann: „Man muss sich also anfangs erst mal in die Arbeitsweise der Maschine und in die Funktionsweise ihrer Werkzeuge hineindenken, um optimale Ergebnisse zu erreichen. Ist der Bauteilkatalog aber erst mal erstellt, führt die Maschine alle notwendigen Fräsungen und Sägeschnitte vollautomatisch aus – etwa, wenn man in der AV ein Fenster in ein Außenwandelement integriert.“
Eingebaut werden die Fenster momentan noch von einem externen Fensterbauer auf der Baustelle. Als nächsten Schritt zur Erhöhung des Vorfertigungsgrads fasst Roland Zimmermann aber bereits den Fenstereinbau in der Produktionshalle ins Auge. Massive Wandelemente aus Brettsperrholz, deren Bearbeitung er früher zukaufen musste, will er künftig selbst auf der Kompaktanlage formatieren und mit Öffnungen für Fenster, Türen und Installationen versehen.
Zukunftsaspekt 2: Bauteile für Kollegen
Die so bearbeiteten Massiv-Wandelemente könnten dann auch als Zulieferprodukte an Zimmererkollegen gehen. Ein neues Geschäftsfeld, das durch die automatisierte Fertigung entstanden ist und das Roland Zimmermann in den nächsten Jahren entwickeln will.
Ausbauen will der Zimmerer außerdem das Zuliefergeschäft bei den Holzrahmenelementen. Hier hat man in Bad Peterstal bereits einen Kundenstamm von mittelständischen Holzbauern ohne fertigungstechnische Ausstattung, sieht außerdem dank der Kompaktanlage neue Möglichkeiten: „Zum einen hat sich unsere Schlagkraft durch die neue Technik erhöht, dass heißt, wir können diesen Kunden, die unter anderem im Raum Freiburg oder Karlsruhe sitzen, auch kurzfristige Liefertermine anbieten und Auftragsspitzen besser abarbeiten. Das ist wichtig, denn in diesem Bereich zählt vor allem der Liefertermin.
Zum anderen profitieren auch unsere gewerblichen Kunden vom höheren Vorfertigungsgrad: Wir können ihnen heute geschlossene Elemente in hoher Präzision liefern, die sich auf der Baustelle schnell und problemlos montieren lassen. Das erhöht die Sicherheit und ermöglicht kürzere Bauzeiten.“
Eine der Hürden, die seine Zimmerei auf dem Weg zu diesem Punkt genommen hat, war die externe Güteüberwachung. Seit April dieses Jahres hat man in Bad Peterstal das Ü-Zeichen – für Roland Zimmermann und seine Kunden ein weiteres Plus an Sicherheit.
Auch bei der Zertifizierung spielte die neue Produktionstechnik eine wichtige Rolle: „Während die Prüfer sich andere Firmenbereiche sehr intensiv anschauten, war die Prüfung unserer Fertigung schnell abgeschlossen. Da hat sich der Prüfer die sauberen Nagelreihen angeschaut, eine davon nachgemessen und dann seinen Haken gemacht.“ Für den Zimmerer eine Bestätigung, dass er alles richtig gemacht hat: „Schließlich habe ich auch deshalb in eine WMS 150 investiert, um in der Elementfertigung eine gleichbleibend hohe Präzision zu erreichen.“
Technik als Marketingvorteil
Diese Präzision bedeutet nicht nur mehr Sicherheit, sie ist auch ein Marketingargument gegenüber den Kunden. Schließlich bringt die automatisierte Fertigung auch einen optischen Gewinn, weil die Nagelreihen schnurgerade und regelmäßig und die Ausfräsungen in Holzfaserplatten sehr viel sauberer sind als frühere Bohrlöcher mit Handmaschinen.
Bauherren können sich deshalb jederzeit gerne davon überzeugen, wie professionell in Bad Peterstal gefertigt wird: „Davon sollte man natürlich nicht zu viel erwarten, denn unter dem Strich ist für viele Bauherren der Preis die entscheidende Größe. Aber wenn wir nahezu preisgleich mit einem Wettbewerber anbieten, haben wir hier schon ein wichtiges Alleinstellungsmerkmal. Das gilt vermutlich auch für Architektenaufträge, an die wir überwiegend über Ausschreibungen kommen.“
Ob sich die neue Fertigungstechnik auch in einem günstigeren Preis niederschlägt? „Können wir derzeit noch nicht genau sagen, da sind wir noch im Lernprozess. Klar ist, dass in der Fertigung heute nur noch zwei Mann arbeiten statt wie früher vier. Dafür haben wir aber auch mehr Arbeit in der AV. Über den Daumen gepeilt spare ich im Vergleich zur manuellen Fertigung einen Mann. Das bringt natürlich auch einen gewissen Kostenvorteil. Wie hoch der ist, müssen wir noch beobachten. Das hängt unter anderem von der Auslastung der Maschine ab.“
Anlauf ohne Schwierigkeiten
Mit dieser Auslastung ist Zimmermann momentan sehr zufrieden, sieht seine Investition inzwischen weit im rentablen Bereich. „Anfangs war das nicht unbedingt so, da waren wir oft noch mit vier Mann in der Produktion, weil wir noch nicht wussten, wie wir mit der neuen Technik umgehen sollten.“
Spielt Zimmermann damit auch auf Anlaufschwierigkeiten der neuen Fertigungslinie an? „Eigentlich nicht, die waren ziemlich gering. Wir wurden schon im Vorfeld der Investition von WEINMANN und Sema sehr gut beraten, dann waren wir auf Schulungen, und danach lief die Produktion zügig an. Und weil der WEINMANN-Mitarbeiter krank war, der uns in den ersten Tagen unterstützen sollte, haben wir schon mal ohne ihn angefangen.
Das lief alles schon sehr gut, lediglich am Anfang waren noch einige Feinanpassungen notwendig. Und wenn heute mal etwas klemmt, wird das über Hotline und Fernservice schnell wieder gerichtet.“
Auch die Mitarbeiter von Roland Zimmermann haben die neue Technik sehr gut angenommen. „Weil die Auftragslage schon damals gut war, musste keiner um seinen Arbeitsplatz fürchten. Deshalb konnten alle die Automatisierung als das sehen, was sie wirklich für sie bedeutet: eine willkommene Arbeitserleichterung. Dementsprechend begeistert wurde sie dann auch begrüßt. Für Fachkräfte und Lehrlinge sind wir dadurch deutlich attraktiver geworden.“
Insgesamt 32 Projekte haben die Mitarbeiter der Zimmerei seit Inbetriebnahme mit der Kompaktanlage gefertigt. Und in den nächsten Jahren könnte die Taktfrequenz auf der Maschine deutlich zunehmen: Vor allem im Zuliefergeschäft für andere Zimmereien sieht Zimmermann seit der Produktionsumstellung eine steigende Tendenz.
Quelle Bildmaterial: WEINMANN Holzbausystemtechnik GmbH
Ein Artikel des Fachmagazins Mikado, 9.2017. Hier lesen Sie den kompletten Artikel.