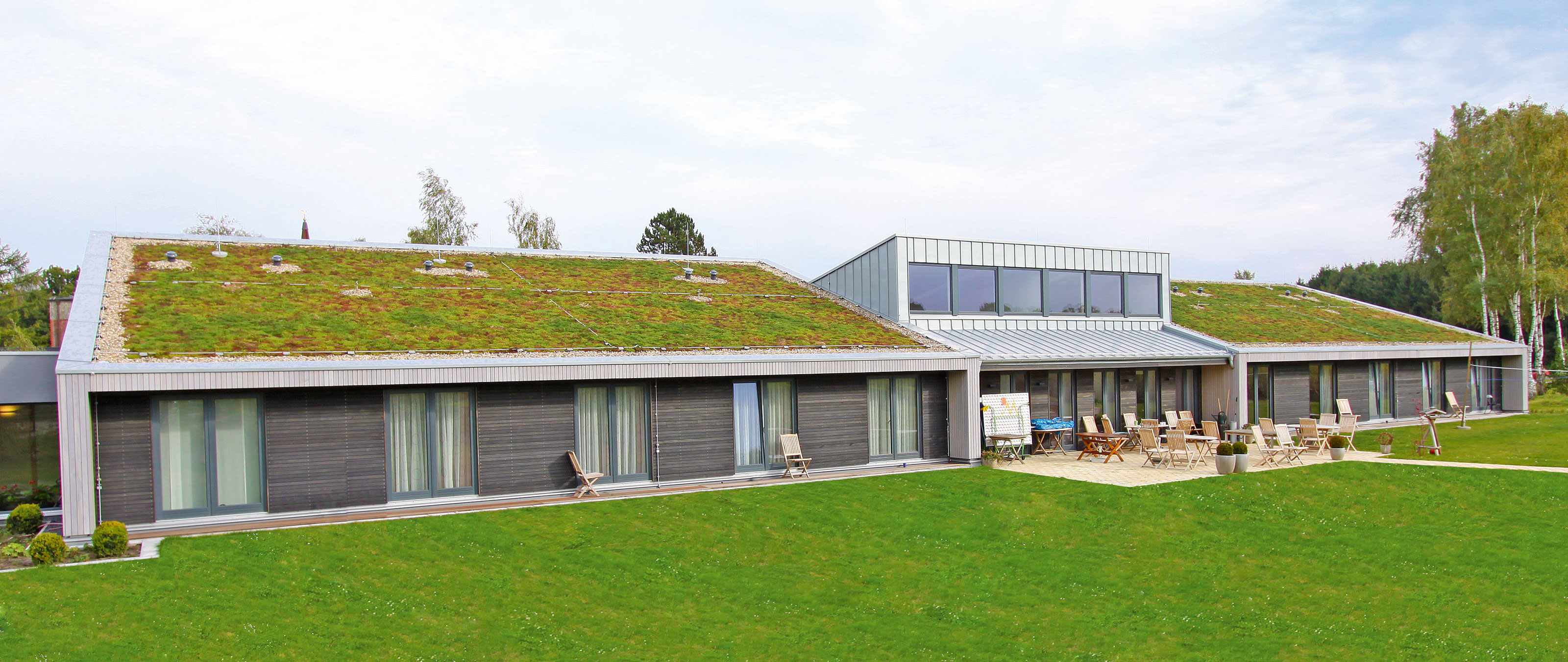
Dwa ostatnie etapy rozwoju przyniosły pełną automatyzację produkcji i przeskok w cyfrową przyszłość. Wszystkie działania w budownictwie drewnianym mają na celu rozwój — tylko w ten sposób można szybko zwiększyć udział w zamówieniach, utrzymać lub nawet poprawić pozycję na rynku oraz zminimalizować ryzyko wzrostu cen materiałów w przypadku pełnych zamówień. Z drugiej strony pojawia się coraz więcej obaw o ewentualny spadek liczby zamówień w związku z panującą pandemią. Co prawda dziś wiadomo, że prawdopodobnie ucierpi na tym głównie rynek tradycyjnej budowy masywnej, ale warto być przygotowanym na wszystko. W tej sytuacji najrozsądniejszym podejściem wydaje się być stopniowy rozwój skupiony na obecnej wielkości zamówień, dostosowanie się do sytuacji rynkowej za pomocą możliwych kroków inwestycyjnych, a także odrobina wizjonerskiej przedsiębiorczości. Aby móc w przyszłości zebrać plony, trzeba inwestować już dziś.
Dziesięć razy więcej sztuk
Dobrym przykładem takiego stopniowego rozwoju jest zakład stolarski Zimmerei Hamdorf z miejscowości Fahrenkrug położonej w Szlezwiku-Holsztynie. Skupia się on na budowie obiektów i budownictwie komercyjnym oraz na produkcji elementów drewnianych dla mniejszych firm stolarskich. Ponadto firma ta, licząca obecnie 46 pracowników, produkuje i montuje opaski do płytek kolczastych, pokrywa dachy i zajmuje się również elewacjami. Dziś mija dziesięć lat od czasu, gdy dyrektor zarządzający Daniel Hamdorf po raz pierwszy osiągnął granice swoich możliwości w zakresie produkcji elementów szkieletu drewnianego. W tym czasie produkował około sześciu domów drewnianych rocznie i chociaż w 2009 roku panował kryzys finansowy, a tradycyjna konstrukcja drewniana nie cieszyła się taką popularnością, popyt na produkty budownictwa drewnianego silnie wzrósł. Aby móc stać się częścią tych zmian, Hamdorf wybudował nową halę produkcyjną i zainwestował w trójstołowy system firmy WEINMANN. Istniejący stół roboczy WEINMANN został włączony do nowej linii produkcyjnej jako stół do produkcji szkieletu drewnianego, a nieco później dodano piąty stół. Służył jako stół buforowy oraz do obróbek specjalnych, takich jak fasady. Dzięki nowej linii produkcyjnej zakład zwiększył swoje możliwości w zakresie budownictwa drewnianego dziesięciokrotnie, czyli do 60 domów rocznie lub ich równowartości w elementach na metr kwadratowy. W ten sposób Fahrenkrug zdążył osiągnąć sukces jeszcze do końca 2019 roku. Następnie, mimo że wprowadzenie pracy dwuzmianowej zwiększyło liczbę do około 100 domów rocznie, granica wzrostu została ponownie osiągnięta. „Uważam, że dzięki wielu projektom realizowanym przez naszych klientów z sektora konstrukcji drewnianych udało się nam osiągnąć dobrą reputację w regionie” — wypowiada się Daniel Hamdorf na temat przyczyn swojego sukcesu. „Ponadto budownictwo drewniane, które charakteryzuje się wysokimi standardami jakości i dobrym bilansem emisji dwutlenku węgla, jest coraz bardziej zgodne z duchem czasu, również na północy. W związku z tym jest ono obecnie mocno ugruntowaną koncepcją wśród klientów publicznych i komercyjnych.”
Możliwość rozbudowy modułowej
W związku z dobrym rozwojem biznesu Daniel Hamdorf przewidział w 2020 roku kolejną modernizację produkcji ram drewnianych. Po konsultacji z osobami odpowiedzialnymi za przygotowanie pracy myślał przede wszystkim o automatyzacji procesu izolacji: „To był pierwszy krok. Celem była także dalsza optymalizacja procesów produkcyjnych. Chcieliśmy więc zredukować stałą pracę dwuzmianową, którą prowadziliśmy przez trzy, cztery lata, z powrotem do jednej zmiany — przy zachowaniu tej samej, a może nawet zwiększonej wydajności”. Z tą koncepcją Daniel Hamdorf skontaktował się z firmą WEINMANN i w porozumieniu z kierownikiem projektu Jörgiem Großem opracował linię produkcyjną dostosowaną do potrzeb klienta. Składa się ona z pięciu stołów roboczych, które — w przeciwieństwie do poprzedniej wersji — przejeżdżają przez wszystkie mostki wielofunkcyjne. Dwa z tych mostków są nowe: WEINMANN WALLTEQ M-310 insuFill, który dzięki w pełni zautomatyzowanemu wdmuchiwaniu materiału izolacyjnego pozwala według Hamdorfa zaoszczędzić ponad 80% czasu pracy w tym obszarze, oraz WALLTEQ M-120, który przejmuje obróbkę desek na dwóch czołowych stołach roboczych. Na obu tylnych stołach pracuje mostek wielofunkcyjny dawnego systemu trójstołowego, który otrzymał w tym celu nowe oprogramowanie. W dużej mierze zmodernizowano również istniejące stoły robocze. Zostały one wyposażone na przykład w urządzenia do transportu wzdłużnego, które w dłuższej perspektywie umożliwiają centralne sterowanie przepływu pracy (patrz poniżej). Dwa najstarsze stoły robocze zostały zastąpione nowymi nabytkami i do dziś doskonale sprawdzają się w oddzielnej produkcji elementów stropowych. Daniel Hamdorf był pod wrażeniem w szczególności tego, jak sprawnie wdrożono istniejące jednostki produkcyjne do nowej linii: „Nie spodziewałem się, że obecne oprogramowanie będzie nadal działać na naszym starszym mostku. Zarówno w tej kwestii, jak i w kwestii stołów stało się jasne, że możliwości modułowej rozbudowy maszyn WEINMANN są czymś więcej, niż tylko marketingową obietnicą”. Peryferia systemu zostały również precyzyjnie dostrojone, aby zoptymalizować przepływ materiału wokół produkcji. Tymczasem każdy stół oprócz stacji izolującej jest obsługiwany przez podnośnik płyt, dzięki czemu można go szybko umieścić na czterech stacjach i obrabiać za pomocą mostka wielofunkcyjnego. Można to robić jednocześnie na desce wewnętrznej i zewnętrznej oraz naprzemiennie na dwóch wyznaczonych stołach — bez długich przestojów mostka. Ta równoległość kilku operacji, w połączeniu ze znacznie skróconymi czasami obróbki na stacji izolacyjnej, wyjaśnia znacznie wyższą wydajność nowej linii.
Z myślą o przyszłości
Inwestując w stację kontroli produkcji Granit MES, Daniel Hamdorf wykorzystał kolejny potencjał do zwiększenia swoich wyników. „Dla mnie granit był początkowo synonimem ściany wieloelementowej” — mówi mistrz stolarski, wyjaśniając swoją decyzję inwestycyjną. „Być może istnieją inne rozwiązania w tym zakresie, ale szybko okazuje się, że zawsze są one obarczone problemami”. Zalety ścian wieloelementowych polegają przede wszystkim na skróceniu cykli roboczych: „Jeśli połączę trzy lub cztery krótsze ściany wewnętrzne w jedną ścianę wielowarstwową, nie muszę już ich pojedynczo cyklinować, lecz przechodzą one przez linię produkcyjną w jednym cyklu roboczym”, wyjaśnia kierownik projektu firmy WEINMANN, Jörg Groß. „Oszczędzam również czas przy wykonywaniu złączy ciesielskich, ponieważ ściana wieloelementowa ma ciągłą belkę górną i dolną. Gdy taki system jest dobrze wykorzystywany, można uzyskać do 20 lub 25 procent więcej mocy z linii produkcyjnej, w zależności od średniej długości ściany. Efekt ten jest szczególnie widoczny w przypadku dużych projektów z powtarzającymi się elementami. To sprawia, że granit jest również interesujący dla tych przedsiębiorstw, dla których zyski z innych modułów oprogramowania są bardziej przejrzyste”. Oczywiście istnieje również aspekt wizjonerski. Polega ona na tym, że firmy stolarskie już dziś zapoznają się z oprogramowaniem w celu nauczenia się pracy z systemem. Kiedy liczba sztuk się zwiększy, nie będą musieli wdrażać się w nowy system w stresujących warunkach. Danielowi Hamdorfowi ten tok myślenia jest również dobrze znany: „Nasza firma od dziesięcioleci stale się rozwija, ponieważ naszą dewizą jest reinwestowanie znacznej części zysku. Mój dziadek zaczynał od zera, a przekazał mi dobrze wyposażoną stolarnię. Ja również inwestuję, mając na uwadze przyszłość moich dzieci. Z dzisiejszej perspektywy może to oznaczać, że zakład stolarski Zimmerei Hamdorf znacznie się powiększy. Jeśli chodzi o grunty, mamy jeszcze sporo miejsca na nowe hale, a wtedy centralny ośrodek sterowania produkcją byłby interesującą perspektywą”. Ponadto Granit jest już częścią kompleksowego procesu digitalizacji, który przygotowuje firmę z Fahrenkrug na przyszłe wyzwania. Obejmuje to standaryzację wielu rozwiązań programowych w przedsiębiorstwie lub połączenie ich ze sobą za pomocą interfejsów w taki sposób, „aby w efekcie końcowym powstał w firmie jednolity proces cyfrowy, przez który przechodzi każdy projekt i do którego dostęp ma każdy pracownik. Granit będzie w tym procesie interfejsem do produkcji”.
Rzemiosło 4.0
A więc przemysł 4.0? W zasadzie tak, ale pomimo całej automatyzacji i cyfryzacji, zakład Zimmerei Hamdorf chce pozostać firmą rzemieślniczą. Przede wszystkim oznacza to, że nie należy oferować klientom standardowych rozwiązań, ale dostarczać każdemu to, na czym mu zależy. W produkcji chodzi na przykład o zmienną budowę ściany i zastosowane materiały — w tym przypadku nowa linia jest ustawiona w sposób całkowicie elastyczny. „Jest to oczywiście ważne również w kwestii produkcji kontraktowej” — wyjaśnia Daniel Hamdorf. „W końcu stolarz oddaje nam sporą część swojej wartości dodanej i obdarza nas dużym zaufaniem, zlecając nam wykonanie swoich elementów. Mogę również załadować ściany w sposób, który jest dla niego optymalny, i zaoferować mu ten decydujący dodatkowy element usługi, który odróżnia nas od konkurencji. Naszym celem w każdym obszarze jest to, by klient był gotów zapłacić więcej ze świadomością, że indywidualne podejście i bezpieczeństwo jest tego warte. Temat bezpieczeństwa obejmuje również fakt, że cyfryzacja i sterowanie produkcją doprowadzą również do zwiększonej planowości produkcji — ze wszystkimi dodatkowymi pozytywami, takimi jak jeszcze wyższy stopień bezpieczeństwa obliczeń i punktualność dostaw komponentów, podczas gdy jeszcze dziś można mówić o wahaniu 5–6 dni. Zanim to nastąpi w Fahrenkrug jest jeszcze kilka problemów do rozwiązania, ale pierwszy krok został już zrobiony: „Udało nam się szybko przywrócić produkcję do pracy jednozmianowej po bezproblemowej fazie przejściowej”, wyjaśnia Daniel Hamdorf. „Od tamtej pory produkujemy taką samą liczbę elementów przy czterech pracownikach, jaką wcześniej osiągaliśmy na dwie zmiany przy trzech pracownikach na zmianę. Na razie mamy redukcję kosztów urządzenia, a zastosowanie Granita w najbliższej przyszłości doprowadzi do zwiększenia liczby sztuk. W dłuższej perspektywie linia produkcyjna daje nam możliwość podwojenia liczby sztuk w ramach dwóch zmian, przy stale rosnącym popycie. Naszym celem jest wówczas produkcja 200 domów rocznie”.
Tekst: Dr. Joachim Mohr
Artykuł z magazynu mikado, wydanie lipiec/sierpień 2021 r. Więcej informacji można znaleźć tutaj.
„Byłem pod wrażeniem, jak sprawnie wdrożono istniejące jednostki produkcyjne do nowej linii.”Daniel Hamdorf, zapewnia prezes firmy Zimmerei Hamdorf
Zimmerei Hamdorf
Zakład stolarski Zimmerei Hamdorf znajduje się w miejscowości Fahrenkrug położonej w Szlezwiku-Holsztynie. Skupia się on na budowie obiektów i budownictwie komercyjnym oraz na produkcji elementów drewnianych dla mniejszych firm stolarskich. Ponadto firma ta, licząca obecnie 46 pracowników, produkuje i montuje opaski do płytek kolczastych, pokrywa dachy i zajmuje się również elewacjami.
Website