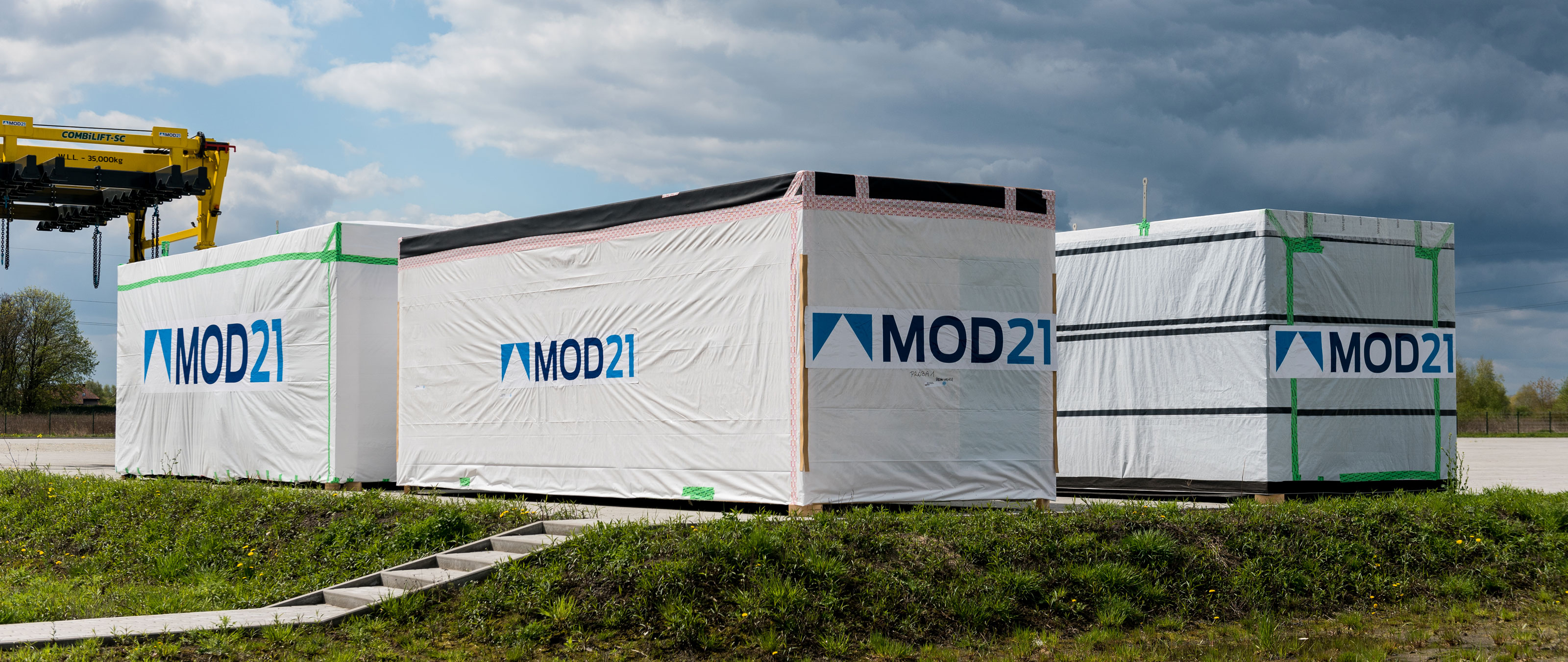
Budowa wielopiętrowych konstrukcji z drewna wiąże się z internacjonalizacją. Przejawia się to coraz większym udziałem przedsiębiorstw zagranicznych w dużych projektach, w tym głównie dużych dostawców ze Szwajcarii i Austrii. Kolejni duzi gracze na rynku budownictwa drewnianego powstają jako startupy wspierane przez inwestorów lub tradycyjne przedsiębiorstwa budowlane, które wchodzą w sektor budownictwa drewnianego.
Od budownictwa konwencjonalnego do drewnianych konstrukcji modułowych
Również MOD21 GmbH w Düsseldorfie nie jest na tym rynku nowicjuszem, ponieważ ta spółka zależna polskiego przedsiębiorstwa ERBUD SA już w 1993 r. realizowała duże projekty w regionie Düsseldorfu — wówczas jeszcze pod nazwą GWI i wyłącznie w sektorze konstrukcji stalowo-betonowych. Firma posiada wieloletnie doświadczenie również w dziedzinie stalowych konstrukcji modułowych. W 2021 r. firma z rozmachem wznowiła działalność, przy okazji zmieniając nazwę: z inicjatywy dyrektora zarządzającego ERBUDU, Dariusza Grzeszczaka, który zasłynął już szeregiem inicjatyw mających na celu transformację ekologiczną grupy, spółka przemianowana została na MOD21. Rozpoczęte inwestycje zostaną dokończone do przyszłego roku konwencjonalnymi metodami, a od 1 stycznia 2022 r. nowe projekty będą realizowane tylko w formule drewnianych konstrukcji modułowych. Jak mówi dyrektor ds. sprzedaży Marius Schneider — „Z uwagi na cele klimatyczne i zmieniające się warunki polityczne, a w szczególności propagowanie prefabrykacji seryjnej ze zrównoważonych materiałów budowlanych, nasza przyszłość leży w budownictwie drewnianym”. Przedsiębiorstwo ze zdecydowaniem i konsekwencją reaguje na zmianę sytuacji na rynku: w przyszłości — poza regionem Düsseldorfu — nawet prace ziemne, garaże podziemne itp. mają być zlecane zewnętrznym partnerom. Chociaż jako wykonawca modułowych konstrukcji drewnianych firma jest praktycznie startupem, to może korzystać ze swoich doświadczeń, referencji i kontaktów z 30 lat działalności w sektorze budownictwa nadziemnego. Ma zatem lepsze warunki startu niż gdyby była faktycznie nową firmą, zwłaszcza że klienci z sektora publicznego i prywatnego coraz częściej chcą realizować swoje projekty w formule konstrukcji drewnianych. W MOD21 zorientowano się już kilka lat temu, że niemiecki rynek otwiera się na prefabrykaty, a architekci coraz bardziej interesują się budynkami modułowymi. Marius Schneider — „Coraz więcej mówi się o tym, że budynki modułowe to nie tylko kontenery lub prowizorka, ale wysokiej jakości budynki do długotrwałej eksploatacji, po których nie widać technologii ich konstrukcji. Nie ustępują one w niczym konwencjonalnym budynkom, natomiast zapewniają stałą, wielokrotnie wyższą jakość prefabrykatów wytwarzanych w kontrolowanych warunkach”.
Wznowienie działalności na 22.000 m2 powierzchni produkcyjnej
Nawet jeśli na budownictwo modułowe przypada obecnie około 5% rynku, w Düsseldorfie widzi się znakomite perspektywy rozwoju. Dlatego podjęto decyzję o rozpoczęciu działalności w sektorze budownictwa modułowego w formule startupu i zainwestowania w niego znacznych środków finansowych. Założona w marcu 2021 r. spółka MOD21 GmbH zakupiła w Toruniu, gdzie mieści się siedziba ERBUD SA, 150 000 m2 terenu z halą mającą 14 000 m2 i budynkiem biurowym o powierzchni użytkowej 3000 m2. Po rozbudowie hali o 8000 m2 powierzchni i dobudowaniu otwartego przejścia firma dysponuje obecnie 22 000 m2 jednolitej powierzchni produkcyjnej. Starą, niższą o 6 metrów halę, wyposażono w dwie linie produkcyjne firmy Weinmann, na których będą produkowane elementy ścienne, podłogowe i stropowe. Układ przestrzenny hali został opracowany przy pomocy producenta maszyn z Lonsingen, na którego zdecydowano się, „ponieważ zaoferował nam najbardziej przekonujące i kompleksowe rozwiązanie w zakresie produkcji oraz rozmaite usługi doradcze np. w zakresie logistyki hali lub ewentualnego dofinansowania”. Linia do elementów ściennych jest wysoce zautomatyzowana i wyposażona w standardowe stacje robocze: maszynę do odwiązywania konstrukcji ciesielskich BEAMTEQ B-660 z obróbką elementów ze wszystkich stron i półautomatycznym podawaniem materiałów, stację montażu szkieletu, obowiązkowy stół odwracany z mostem wielofunkcyjnym i dwoma stołami buforowymi, na których można m.in. mocować pokrycie przeciwpożarowe bez powodowania zatorów. Linia kończy się stołem do stawiania elementów, który przekazuje gotowe elementy ścienne do wózków transportowych. Przenoszą one stojące elementy ścienne do ośmiotorowego magazynu ścian, w którym przechodzą częściowo proces finishingu z montażem okien, tynkowaniem itp. Z magazynu są transportowane za pomocą wózka transportowego i suwnicy do sekcji produkcji modułów. Ze względów ekonomicznych izolacja jest na razie montowana ręcznie, ale przewidziano już miejsce na maszynę WALLTEQ M-300 insuFill. Zrezygnowano także z użycia robotów przemysłowych, ponieważ zdaniem prezesa Theodora Kaczmarczyka przy planowanej wielkości produkcji wady tej technologii przeważają jeszcze nad jej zaletami. Na podobnie wyposażonej linii 2 są produkowane elementy podłogowe i stropowe. Na końcu produkcji podłogi są chwytane przez suwnicę i transportowane do linii modułów w nowej części hali o wysokości.
Produkcja modułów w osobnej linii
W tym miejscu są one od razu ustawiane na wózkach i poziomowane, aby montowane moduły stały pionowo. Następnie elementy są składane w modułowe pomieszczenia. Między stacjami są one przemieszczane nie na szynach, lecz na wózkach. Jak mówi prezes MOD21 Theodor Kaczmarczyk — „Daje nam to większą elastyczność, ponieważ moduły są także obracane, przemieszczane w pozycji ukośnej i zależnie od szerokości ich różną liczbę sztuk można ustawić obok siebie. Jeżeli występuje zator, gotowy moduł może nawet wyprzedzić ten, nad którym prace jeszcze trwają.” Elementy ścienne są produkowane w ciągu 29 minut, elementy podłogowe i stropowe wymagają 59 minut – różnica wynika przede wszystkim z wyższego udziału ręcznych operacji: w podłogach występują ukośne połączenia między deskami konstrukcyjnymi, które są nadal zbijane ręcznie. Przy produkcji elementów pracuje obecnie 12 osób. Modułowe pomieszczenia są gotowe — włącznie z wykonaniem elementów — w ciągu dwóch dni. Na wyposażenie wnętrza potrzebne jest jeszcze 12 dni, czyli łączny czas realizacji gotowego modułu wynosi 14 dni — włącznie z gotowymi do użytku instalacjami, szafkami, kuchenką i obiektami sanitarnymi, aż po szczotkę do toalety na uchwycie ściennym. Praca jest wykonywana głównie przez pracowników MOD21 i tylko konkretne czynności, jak dach i elewacja, które wymagają obecności na placu budowy, są zlecane podwykonawcom. Korzyść: oszczędności wynikające z przeniesienia prac podwykonawców do hali wpływają korzystnie na ogólny kosztorys. Podwykonawcy nie są natomiast jeszcze gotowi do uwzględnienia tych korzyści w swoich usługach.
Do 2026 r. nawet 100 000 m2 powierzchni zabudowanej rocznie
Na pierwszy rok działalności MOD21 założył sprzedaż i dostawę 30 000 m2 powierzchni zabudowanej i zdaniem prezesa Theodora Kaczmarczyka firma jest na dobrej drodze do realizacji tego celu. 6000 m2 jest już w produkcji, reszta jest już pipelinie, czyli biorąc pod uwagę krótki czas montażu w drewnianym budownictwie modułowym, osiągnięcie celu do końca roku jest w pełni możliwe – nawet przy obecnie dość zachowawczej postawie prywatnych inwestorów z uwagi na wzrost kosztów i stóp procentowych. Do 2026 r. wielkość produkcji ma się stopniowo zwiększać do 100 000 m2 powierzchni zabudowanej. Zakład w Toruniu ma wtedy pracować w systemie dwuzmianowym. Trzecia zmiana nie jest planowana, za to myśli się o drugim zakładzie produkcyjnym, o planach którego Theodor Kaczmarczyk rozmawiał już wstępnie z firmą Weinmann. Nowy zakład pozwoli znacznie zwiększyć wielkość produkcji ze względu na wyższy stopień automatyzacji, między innymi dzięki proponowanemu przez producenta maszyn zastąpieniu ukośnych połączeń metalowych w podłogach i stropach frezowanymi połączeniami drewnianymi. W tym zakładzie mają również być wykorzystywane roboty przemysłowe. Nowy zakład będzie zlokalizowany prawdopodobnie w Niemczech. Jest to o tyle logiczne, że MOD21 ma obecnie klientów tylko w Niemczech — rozważa się eksport do Austrii i Szwajcarii, ale polscy klienci nie są jeszcze otwarci na budynki modułowe. Decyzję o lokalizacji zakładu w Polsce podjęto zatem z innych powodów. „Mogliśmy wykorzystać zasoby naszej grupy kapitałowej” — tłumaczy Theodor Kaczmarczyk. „Poza tym ERBUD cieszy się w Polsce znakomitą reputacją jako pracodawca i nie mieliśmy żadnych problemów z zatrudnieniem”. Od strony ekonomicznej korzyści wynikające z lokalizacji są niewielkie: według Theodora Kaczmarczyka płace w Polsce są obecnie prawie na tym samym poziomie, co w Niemczech. „Dlatego właśnie młodzi Polacy wolą pracować we własnym kraju, a my sprowadziliśmy nasz zakład do nich”. Ponieważ jednak prezes uważa, że wizyta w zakładzie w celu obejrzenia nowoczesnych linii produkcyjnych i showroomu zbudowanego z przykładowych modułów ma zasadnicze znaczenie dla propagowania wizerunku firmy, MOD21 finansuje zainteresowanym podróż i zakwaterowanie.
Planowanie i wykonanie
Do wizyty firma zaprasza szczególnie inwestorów realizujących projekty, w których korzyści związane z prefabrykacją są szczególnie odczuwalne: są to m.in. placówki edukacyjne, takie jak szkoły, przedszkola i uczelnie wyższe, budynki biurowe i administracyjne, hotele lub obiekty służby zdrowia, takie jak szpitale i domy opieki, a także przybudówki i nadbudowy. Jest to związane ze znanymi już zaletami budowy drewnianego budownictwa modułowego:
Bezproblemowa realizacja, w trakcie której obecność klienta jest wymagana tylko w fazie planowania i odbioru, dzięki czemu oszczędza on na kosztach zatrudnienia
Przejrzyste zarządzanie jakością i wysoka, stała jakość budynków dzięki w znacznym stopniu zautomatyzowanym, bardzo precyzyjnym procesom produkcyjnym w kontrolowanych warunkach
Bardzo szybkie wykonanie dzięki wysokiemu stopniowi prefabrykacji i wykonywaniu prac przygotowawczych na budowie równolegle z produkcją modułów
Przekłada się to na krótki czas zamknięcia ciągów komunikacyjnych, małe uciążliwości dla mieszkańców (nadbudowy!) i możliwość montażu przedszkoli i szkół bez ryzyka w czasie wakacji
Elastyczne użytkowanie z rozbiórką modułów i odbudową w innej lokalizacji, przy czym duży budynek można na życzenie podzielić na kilka mniejszych. Demontaż jest standardowym elementem oferty MOD21, która obejmuje także formułę wynajmu.
Aby wszystko to działało, budynek musi oczywiście pasować do systemu modułowego. Dlatego MOD21 woli włączać się w projekt już na etapie planowania. Chociaż możliwy jest projekt i realizacja dowolnego rzutu poziomego, to im bardziej różni się od systemu, tym dłuższy będzie czas wykonania, a przede wszystkim tym większe będą koszty. Dlaczego planowanie realizowane we współpracy z własnymi architektami, partnerami zewnętrznymi, a także z architektami klienta, odbywa się w zakresie systemu modułowego. Po efekcie prac praktycznie nie widać modułowego pochodzenia. To zasługa elastycznych modułów o długości do 12,00 m, szerokości do 4,20 m i wysokości do 3,20 m, które są także łatwe w transporcie. W przypadku specjalnych życzeń można je łączyć pionowo i poziomo, aby uzyskać również duże sale lekcyjne, hole lub klatki schodowe o konstrukcji modułowej. Tam, gdzie jest to niemożliwe, można sięgnąć po pomoc podwykonawców.
Kalkulator CO2 oparty na wynikach badań uniwersyteckich
Swoją seryjnością i przystosowaniem do zasad zrównoważonego rozwoju oferta idealnie wpisuje się w nasze czasy, co chwaliła niemiecka minister budownictwa Klara Geywitz w trakcie swojej wizyty w toruńskiej fabryce. Do współczesnych czasów pasuje również standard ściany zewnętrznej o konstrukcji szkieletowej z izolacją 140 mm, dwiema płytami gipsowo-włóknowymi wewnątrz oraz płytą OSB ze ścianą osłonową lub ETICS na zewnątrz, która spełnia kryteria wysokich standardów energetycznych budynku. Oferta MOD21 na tym jednak się nie kończy: zainteresowani mogą za pomocą kalkulatora CO2 na stronie internetowej firmy obliczyć wielkość emisji CO2 podczas budowy ich budynku — i to rzetelnie, ponieważ algorytm został opracowany na podstawie zakrojonych na szeroką skalę przeprowadzonych na Akademii Górniczo-Hutniczej badań uwzględniających „wiele danych istotnych w projektach budowlanych”. W przypadku faktycznego projektu budowy schroniska dla azylantów w Monachium o powierzchni użytkowej 3700 m2 okazało się, że emisja CO2 jest o 97% mniejsza niż w przypadku konwencjonalnych metod budowy. „Na tym odbija się oczywiście transport samochodami ciężarowymi i dlatego już myślimy o napędzie wodorowym” — tłumaczy Theodor Kaczmarczyk. „Tego transportu nie da się jednak porównać z dojeżdżaniem wykonawców przez wiele miesięcy na konwencjonalny plac budowy”. Dla wielu klientów ten aspekt zrównoważonego rozwoju stanowi wystarczający powód do zaakceptowania nieco wyższych kosztów budowy drewnianych konstrukcji modułowych. Tym bardziej, że dodatkowe koszty kompensuje krótki czas realizacji: jeśli budowa postępuje nawet o 70% szybciej, klient oszczędza na kosztach finansowania i wcześniej może się wprowadzić lub zacząć zarabiać na wynajmie lub sprzedaży. Jeśli uwzględnimy te korzyści, to zdaniem Theodora Kaczmarczyka cena budynków modułowych jest w przybliżeniu taka sama jak budowanych innymi metodami.
Artykuł z magazynu mikado, wydanie 11/2023. Więcej informacji można znaleźć tutaj.
„Najbardziej przekonujące i kompleksowe rozwiązanie w zakresie produkcji oraz rozmaite usługi doradcze.”Prezes MOD21 Theodor Kaczmarczyk
MOD21
Przedsiębiorstwo powstało w 1993 r. w Düsseldorfie i prowadzi obecnie działalność w całych Niemczech. Jako część prowadzącej działalność w całej Europie grupy ERBUD MOD21 dysponuje znakomitą siecią kontaktów i dużym know-how w zakresie budownictwa modułowego. Nowy zakład produkcyjny został wybudowany w ciągu zaledwie 12 miesięcy. Na powierzchni 22 000 m² produkuje się dziennie około 375 m² modułów w sposób prawie całkowicie zautomatyzowany.
Więcej informacji