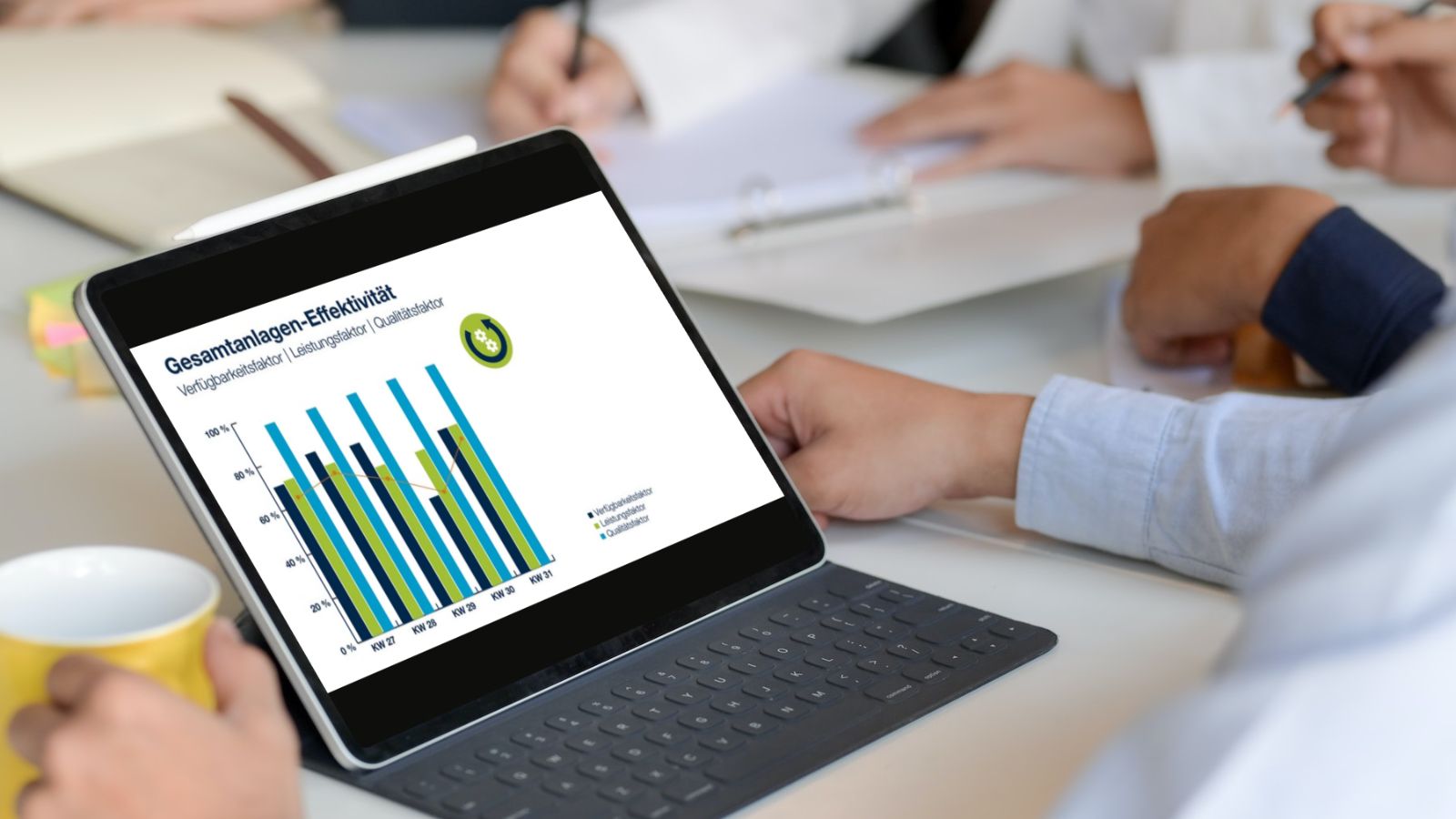
Ein Artikel aus dem HK-Magazin Ausgabe 02/2023 (Mai 2023).
Den Gesamtoutput bei gleichbleibendem Ressourceneinsatz steigern – der von Schuler Consulting und Homag entwickelte OEE-Workshop setzt sich genau das zum Ziel und bietet all jenen einen praktischen Ansatz, die die Wertschöpfung in ihrer Anlage steigern wollen. Dabei wird die Fertigung als Gesamtes betrachtet und die Einflüsse auf die Faktoren Verfügbarkeit, Leistung und Qualität analysiert. Wie eine OEE-Potentialanalyse in der Praxis aussieht, berichten Philipp Bräuer (Schuler Consulting) und Simon Liller (Homag).
Fehlerursachen erkennen und Maschinenstillstände verhindern
Es ist ein bekanntes Problem: Ressourcen wie Zeit, Fachkräfte, Maschinen, Material und Energie müssen bestmöglich genutzt werden, um dem hohen Produktionsdruck zu begegnen. OEE-Analysen helfen dabei, Maschinenstillstände und organisatorische oder unbegründete Unterbrechungen zu verstehen und zu verhindern und dadurch mit den vorhandenen Ressourcen die Effektivität der Produktion zu erhöhen. Die Gesamtanlagen-Effektivität (Overall Equpiment Effectiveness, OEE) ist eine Kennzahl, die sich aus den Faktoren Verfügbarkeit, Leistung und Qualität zusammensetzt. Diese Kennzahl beinhaltet die wesentlichen Elemente, die Einfluss auf die Produktivität und somit auf die Wirtschaftlichkeit von Prozessen und Anlagen haben. Unser Erfahrungswert zeigt: Bei langjährigen Anlagen liegt das OEE-Potential bei einer Steigerung von zehn Prozent und mehr.
Eines der wichtigsten Ergebnisse einer OEE-Potentialanalyse ist Transparenz: Warum kommt es zu Maschinenstillständen? Wo liegen die Ursachen für Fehler? Wo kommt es zu Verschwendung? Um das herauszufinden, setzen wir unterschiedliche Daten- und Prozessanalysetools nach der weltweit erfolgreichen Lean-Six-Sigma-Methodik ein. Die Einflussfaktoren auf die OEE (Verfügbarkeit, Leistung, Qualität) analysieren wir in gemeinsamen Workshops mit produzierenden Unternehmen, um Verschwendungs- und Störungsfaktoren zu identifizieren und Optimierungsmaßnahmen abzuleiten. Die erarbeiteten Lösungsansätze werden je nach Projektumfang gemeinsam mit dem Kunden umgesetzt und die Nachhaltigkeit sichergestellt. Schuler Consulting und Homag verfolgen im Bereich OEE einen partnerschaftlichen Ansatz, um durch das Zusammenspiel von Optimierungs-Know-How und Maschinenbaukompetenz das bestmögliche Ergebnis zu erreichen.
In fünf Schritten zu mehr Effektivität – Der DMAIC Zyklus
Die methodische Grundlage eines OEE-Projekts ist der „DMAIC“-Zyklus. Anhand der Lean Six Sigma Methode erarbeiten wir Optimierungsvorschläge, um die Gesamtanlageneffektivität nachhaltig zu steigern. Hierbei gehen wir in fünf Schritten vor, die der Methode ihren Namen geben: Define, Measure, Analyze, Improve und Control.
„Define“ – Wir erfassen die Ausgangssituation und machen sie messbar. In einem Workshop definieren wir gemeinsam mit dem Kunden die Projektziele und erfassen die relevanten Produktionsprozesse. Das bedeutet, dass Prozesse visualisiert und besprochen werden. Dazu führen wir Kundeninterviews mit Maschinenbediener/innen, dem Instandhaltungspersonal oder Mitarbeitenden in der Arbeitsplanung durch. Am Ende mündet alles in einem klar definierten Projektsteckbrief.
„Measure“ – In dieser Phase sammeln wir für einen bestimmten Zeitraum alle relevanten Daten zur Bestimmung der OEE und zeichnen die Prozesse auf. Dabei können sowohl historische Daten als auch neu erhobene Daten verwendet werden. Abschließend berechnen wir die aktuelle Prozessleistung. Neben der direkten Messung der Prozessleistung, das heißt der konkreten Gesamtanlageneffektivität, messen wir auch indirekte Prozessleistungen wie die Ersatzteilbewegungen, die Wartungseinsätze oder konkrete Maschinenzustands- oder Störungsdaten.
In der Analyze-Phase vollziehen wir mit Hilfe von Lean-Six-Sigma-Tools umfangreiche Daten- und Prozessanalysen. Hier analysieren wir zum Beispiel die erfassten Maschinenzustandsdaten oder Störungsmeldungen. Wir identifizieren, wie die bisherige Prozessleistung zustande kommt und erkennen Ursachen für zu häufige, wiederkehrende Störungen, zu lange unbegründete Wartezeiten oder eine zu hohe Nacharbeitsquote.
Die anschließende „Improve-Phase“ bringt die gewonnenen Erkenntnisse in die Praxis: Nun erarbeiten wir gemeinsam Lösungskonzepte für die Fertigung. Diese Lösungen erstrecken sich auf den gesamten Herstellungsprozess von konkreten Modernisierungen oder Softwareupdates über prozessuale Veränderungen im Materialfluss bis hin zu neuen Arbeitsweisen in der Arbeitsvorbereitung. Alle Lösungen werden in der Improve-Phase auf deren Wirkung im Wertstrom abgestimmt. Typische Fragestellungen sind hierbei unter anderem die Verträglichkeit mit anderen Fertigungswegen oder auch typische Hürden innerhalb von Veränderungsprozessen. Zentral ist außerdem, die erarbeiteten Optimierungsansätze auf Wirtschaftlichkeit zu prüfen und nach Möglichkeit zu testen oder zu simulieren.
In der letzten Phase, der „Control-Phase“, beginnt die Umsetzung der Maßnahmen. Dabei ist es wichtig, den Prozess genau zu überwachen und alle Anomalien zu dokumentieren. Falls die Prozessleistung abnimmt, greift ein Reaktionsplan mit vorab definierten Maßnahmen ein.
In bisherigen Projekten war eine Steigerung der Gesamtanlageneffektivität zwischen drei und fünfzehn Prozent messbar. Natürlich hängt dies immer von der Ausgangssituation ab, sodass es schwierig ist, pauschale Aussagen zu treffen. Unser Erfahrungswert zeigt, dass das OEE-Potential bei langjährigen Anlagen bei über zehn Prozent liegt. Basierend auf den Kundenanforderungen kann ein OEE-Projekt in wenigen Tagen bis hin zu mehreren Wochen dauern. Die Dauer gestaltet sich individuell. Unabhängig davon wird in jedem Projekt die Produktion im Gesamten betrachtet.
Praxisbeispiel: Arbonia Gruppe (Prüm und Garant)
Die Arbonia Gruppe ist ein Gebäudezulieferer mit Hauptsitz in Arbon (Kanton Thurgau, Schweiz) und mehreren Produktionsstandorten in Europa. Die Unternehmensgruppe umfasst zwei Divisionen: Die Division „Raumklima“ (Heizungs-, Lüftungs- und Klimatechnik) und die Division „Türen“ (Holz und Glas), zu der unter anderem die Marken „Garant“ und „Prüm“ gehören. Im Sommer 2021 wurde ein OEE-Projekt in der Division „Innentüren“ bei der Unternehmensgruppe durchgeführt.
Für die Division Türen gibt es klare Wachstumsziele in den kommenden Jahren: Durch den weiteren Kapazitätsaufbau von Produktionsanlagen sowie die Erschließung weiterer Marktanteile soll der Umsatz um bis zu 30 Prozent erhöht werden. Laut eigener Prognosen ist bereits 2023 einen Output von jährlich 3,4 Millionen Türen und Zargen bei gleichbleibender Mitarbeiterzahl möglich. Die Stellschrauben, die das Wachstum der Unternehmensgruppe ermöglichen sollen, liegen in der Fertigung: Anlass des Projekts war es, die Prozessschwachstellen und wesentlichen Einflussfaktoren auf die OEE zweier Produktionslinien für Türen zu identifizieren. Hierzu überprüfte das Team die Leistungsfähigkeit der Anlagen und deckte Verbesserungspotentiale auf.
Horst Lichter (Gesamtleiter Technik, Prüm und Garant) berichtet: „Jeder Nutzer einer Maschine oder Anlage sollte genau einschätzen können, wie der Status Quo (Leistung, Verfügbarkeit, Anlageneffektivität usw.) seiner Anlage ist. Dabei ist ein OEE-Workshop nach einer gewissen Anlaufphase mehr als nützlich. Die Aufnahme muss sehr transparent und möglichst aus neutralem Blickwinkel gemacht werde. Nur so sind die Ergebnisse repräsentativ und können für Verbesserungen genutzt werden.“
Um ambitionierte Wachstumsziele bei gleichbleibendem Ressourceneinsatz zu erreichen, ist ein hohes Engagement der Mitarbeiter gefordert. „Der Erfolg hängt von Mensch und Maschine ab“, betont Lichter. Ein neutraler Blick von außen, sei in diesem Projekt daher sehr wichtig gewesen. „Werden Ergebnisse durch eine neutrale Person ermittelt und präsentiert, werden diese sehr viel schneller akzeptiert, als wenn die Ergebnisse aus den eigenen Reihen kommen.“
Für Lichter ist eine OEE-Analyse zum etablierten Mittel geworden, um Optimierungspotentiale aufzudecken: „Ein OEE-Workshop sollte als Standardwerkzeug genutzt werden. Es gibt keine Regel, wann der richtige Zeitpunkt dafür ist. Ich denke, ein Workshop ist dann notwendig, wenn man der Meinung ist, dass man nicht mehr weiter kommt.“
Ein OEE-Workshop dient zum einen der Bestandsaufnahme: Wo steht mein Unternehmen heute? Was ist der Status-Quo? Welche Optimierungspotentiale gibt es? Im zweiten Schritt steht nach der IST-Analyse die Umsetzung der ermittelten Maßnahmen an. Damit beginnt die „eigentliche“ Arbeit für die Unternehmen selbst – und hier lauert das größte Risiko: Veränderung braucht Zeit, braucht Bereitschaft, braucht Umsetzung. Im zweiwöchigen Projekt ist das OEE-Team nach den fünf Schritten des „DMAIC“-Zyklus vorgegangen und konnte eine Liste an Optimierungspotentialen erarbeiten. Mit den Erkenntnissen aus dem Workshop ist Horst Lichter zufrieden. Es gebe eine ganze Reihe an „low hanging fruits“ und einen Abarbeitungsplan, der nun sukzessive in die Tat umgesetzt werde, so Lichter.
Dank des guten Engagements der Mitarbeiter der Arbonia-Gruppe konnte das Projekt zur vollen Zufriedenheit aller Seiten abgeschlossen werden. „Die Zusammenarbeit war von Anfang an mit ‚offenem Visier‘! Alle Beteiligten Mitarbeiter aus den verschiedensten Abteilungen haben sich eingebracht. HOMAG hat in kompetenter Weise das Coaching sowie die anschließenden Auswertungen übernommen“, fasst Lichter zusammen.
Ausblick
Eine OEE-Analyse kann sowohl als „ad hoc“-Maßnahme eingesetzt werden als auch den Beginn eines kontinuierlichen Optimierungsprozesses kennzeichnen. In beiden Fällen wird die Produktion individuell als Gesamtes analysiert. Nachhaltig und damit langfristig erfolgreicher sind unserer Erfahrung nach jene Unternehmen, die sich die kontinuierliche Optimierung ihrer Produktion auf die Fahne schreiben und täglich daran arbeiten, besser zu fertigen. Unsere klare Empfehlung lautet daher, das Thema „OEE“ nicht nur einmalig, sondern langfristig zu betrachten und sich für die Umsetzung der Optimierungsmaßnahmen Experten ins Haus zu holen.
Wer noch einen Schritt weitergehen möchte und nach einer Lösung sucht, um den gesamten Wertstrom zu optimieren, für den bietet Schuler Consulting die „Digitale Wertstromoptimierung“ an: Einen „Fährtenleser für die Produktion“ (Vgl. Ausgabe HK 05-2022). Bei der „Digitalen Wertstromoptimierung“, eine skalierbaren Beratungsleistung von SCHULER Consulting, setzt das Berater-Team ein technisches Set-Up ein, um Maschinendaten, Material- und Wertströme in der Fertigung kontinuierlich, herstellerunabhängig und digital zu erfassen. Anhand dieser „digitalen Spuren“ werden insbesondere jene Prozesse analysiert und optimiert, für die es in den Unternehmen bisher eine unzureichende Datenbasis gibt. Durch regelmäßige Optimierungsworkshops, in denen auch die Methoden aus OEE-Workshops eingesetzt werden, können Unternehmen langfristig den Gesamtoutput ihrer Fertigung steigern.
Autoren:
Philipp Bräuer arbeitet im Team Industrie 4.0 von Schuler Consulting. Zu seinen Kernaufgaben gehören Fabrikplanungen und Fertigungsoptimierungen. Der gelernte Schreiner, Holzingenieur und REFA-Fachmann ist bei OEE-Workshops in der Prozessanalyse und -optimierung tätig.
Simon Liller ist Produktmanager Service Solutions und arbeitet im Bereich Life Cycle Services der Homag. Der Produktmanager ist ausgebildeter Lean-Six-Sigma Green und Black Belt und in OEE-Projekten in der Industrie tätig.