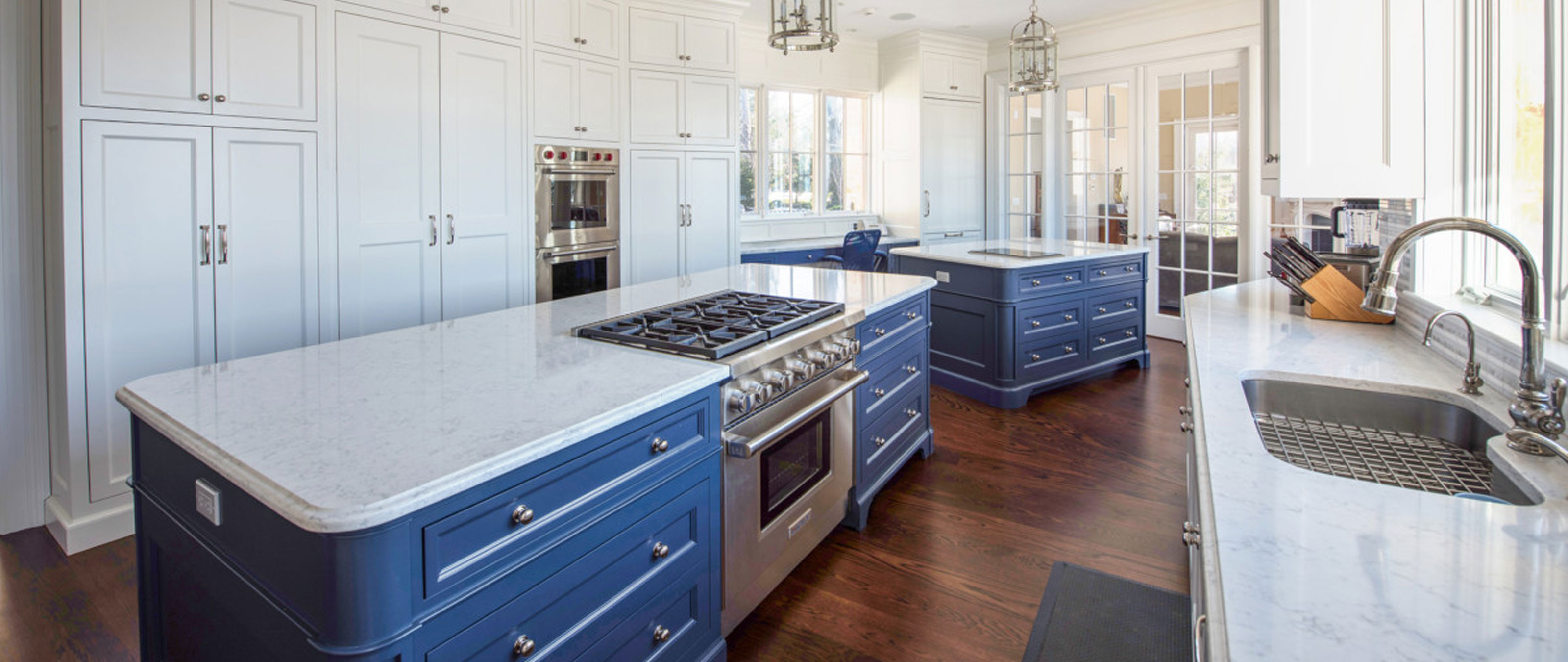
Seit mehr als 100 Jahren steht das Unternehmen Ciuffo Cabinetry für elegantes, italienisches Design und hochwertige Qualität. Angefangen mit der Herstellung von Holz-Schnitzereien, welche noch heute in den Kirchen New Yorks zu finden sind, kann das Unternehmen auf eine bewegte Geschichte zurückblicken. Die italienischen Einflüsse auf Gestaltung und Konstruktion niemals verloren, stellt die Familie Ciuffo heute in fünfter Generation mit etwa 50 Mitarbeitern exklusive Küchen und Wohnmöbel her.
Die steigende Nachfrage nach hochwertigen, individuellen Küchen war für das Unternehmen Ciuffo Cabinetry am kleinen, beschaulichen Standort auf Long Island vor den Toren New Yorks nicht mehr zu bewältigen. Die Produktion war am Limit und die beengten Platzverhältnisse erschwerten Materiallogistik und Produktionsprozesse. Dem familiengeführten Unternehmen war schnell klar: „Wir wollen wachsen“.
An den Erweiterungsgrenzen des bisherigen Standorts angekommen, begann also die Suche nach einem neuen Produktionsgebäude – nicht ganz einfach auf einer Insel, welche sich bei wohlhabenden und prominenten Persönlichkeiten größter Beliebtheit erfreut. Trotz hoher Investitionskosten sollte auch das neue Produktionsgebäude in unmittelbarer Nähe zum Haupt-Absatzmarkt des Unternehmens, nämlich New York City, liegen. Die gesamte Auftragsabwicklung der exklusiven Produkte bis hin zur Montage erfolgt bei Ciuffo aus einer Hand, da sind kurze Wege zum Kunden Pflicht. Um das neue Produktionsgebäude optimal nutzen zu können entschied sich Ciuffo für die Unterstützung durch SCHULER Consulting und fand den idealen Partner, um den Entwicklungsprozess und den Umzug in das neue Produktionsgebäude zu begleiten.
Der Umzug an einen neuen Standort sollte, neben der geplanten Kapazitätssteigerung, auch als Chance für einen digitalen Wandel dienen. Das bisherige IT-Konzept war in die Jahre gekommen und der Flut an Aufträgen nicht mehr gewachsen. Die Fehlerquote in der Produktion durch mangelnde Informationen war hoch, weshalb sich die Berater neben der strategischen Produktionsplanung auch den Prozess- und Informationsflüssen innerhalb des Unternehmens widmeten und gemeinsam mit dem Unternehmen ein ideales und skalierbares IT-Konzept für den neuen Produktionsstandort entwickelten.
In der Arbeitsvorbereitung und Auftragsabwicklung bot sich zunächst ein gewohntes Bild, wie es häufig bei handwerklichen und mittelständischen Möbelproduzenten vorzufinden ist:
Eine isolierte CAD/CAM-Lösung, viele Excel-Listen und Unmengen an Papier dominierten die Auftragsabwicklung. Eine effiziente Auftragsabwicklung war, aufgrund wenig standardisierter Prozesse, stark abhängig vom entsprechenden Sachbearbeiter. Dies machte sich, speziell bei den komplexen und individuellen Konstruktionen durch eine hohe Fehlerrate und Verzögerungen im Produktionsprozess bemerkbar. Die fehlende Materialbeschaffungslogik führte zu großen Material- und Auftragsbeständen in der Produktion, was zeitweise erhebliche Probleme in der Intralogistik des Unternehmens erzeugte.
Nach dem Zuschnitt war keine eindeutige Zuordnung der Bauteile zur entsprechenden Baugruppe oder gar zur Auftragsposition möglich und bei der End-Montage entstanden lange Suchzeiten und Fehlteile, was Output und Effizienz negativ beeinflusste. Nicht selten mussten ganze Kommissionen aus dem Produktionsprozess ausgeschleust werden, weil Baugruppen, Zukaufteile oder Nachfertigungsteile nicht rechtzeitig bereitgestellt wurden. Um diese Fehler zu vermeiden und die Effizienz zu steigern musste also zunächst einmal definiert werden, welche Daten überhaupt an welcher Stelle der Produktion benötigt werden.
Mit der Bottom-Up-Methode wurden aus dem Endprodukt und den eingesetzten Technologien in der Produktion die Anforderungen an die IT-Landschaft und den Informationsfluss ermittelt. Dabei werden am Point of Manufacturing die notwendigen Daten für die einzelnen Fertigungsschritte definiert und analysiert in welcher Form und an welchem Ort diese Daten und Informationen benötigt werden. Ausgehend von dieser Analyse werden die Daten schrittweise auf die einzelnen Prozessebenen transformiert. Auf diese Weise können detailliert die Anforderungen an das Prozess- und Datenmodell ermittelt werden.
Diese Ergebnisse der Bottom-Up-Methode waren unerlässlich, um eine Softwareauswahl auf den einzelnen Prozessebenen vollziehen zu können. Die so gewonnenen Ergebnisse dienten also zuerst einmal zur Erstellung eines Lastenhefts.
Den Datenursprung bildet immer die Auftragserfassung, wo die Informationen in einer definierten Form und vollständig vorliegen müssen, um den Kundenauftrag in allen Merkmalen definieren zu können. Innerhalb der Arbeitsvorbereitung werden diese Informationen dann angereichert und in Produktionssprache übersetzt.
Für eine effiziente und fehlerfreie Produktion der komplexen und individuellen Küchen spielt also die gründliche Arbeitsvorbereitung eine wichtige Rolle für den nachhaltigen Erfolg, die Verringerung der Fehlerquote, sowie eine Steigerung der Transparenz innerhalb der Produktion. Die Anreicherung der Informationen aus dem Kundenauftrag muss nach einem standardisierten Schema und nach Möglichkeit mit geringem manuellen Aufwand erfolgen. Ein strukturiertes Datenmodell und die Definition von Standardartikeln erleichtert hier nicht nur die Arbeitsvorbereitung, sondern auch die Produktionsprozesse durch die Schaffung wiederkehrender Vorgehensweisen.
Durch das traditionelle Design in Rahmenbauweise entstehen bei den Produkten von Ciuffo Cabinetry nicht nur komplexe Berechnungen bei der Langteilgenerierung, sondern auch aufwändige Baugruppen wie beispielsweise profilierte Rahmentüren aus Massivholz oder Blend-Rahmen, welche sich über mehrere Korpen erstrecken.
Viele Kranzprofile, Lichtleisten und Blenden müssen automatisiert berechnet und mit Aufmaß für die Profilierung versehen werden. Auch hier kann mit der Etablierung von Standards eine erhebliche Verringerung der Komplexität erreicht werden.
Ziel der Arbeitsvorbereitung bei Ciuffo Cabinetry ist die effiziente Erstellung eines „digitalen Zwillings“ der komplex aufgebauten Küchen, von welchem alle notwendigen Fertigungsinformationen, Maschinenprogramme und Prozessparameter automatisiert abgeleitet werden können. Jede einzelne Baugruppe soll in Ihren Merkmalen vollständig definiert sein und die zur Produktion notwendigen Informationen sollen zur richtigen Zeit und am richtigen Ort in einer sinnvollen Form zum Mitarbeiter transportiert werden können.
Notwendige Maschinenprogramme und Zuschnittpläne müssen vollständig und vor Allem fehlerfrei automatisiert ausgegeben und zentral für die entsprechenden Anlagen bereitgestellt werden. Ciuffo setzt hierbei im Zuschnitt konsequent auf Nesting. Künftig sollen aus einem Flächenlager zwei Nestinganlagen beschickt werden, eine davon mit der Möglichkeit zur Bearbeitung mit 4,5-Achsen. Dadurch kann ein Großteil der Bauteile bereits beim Nesting komplett bearbeitet werden, obwohl hier durch die genutete Korpusverbindung komplexe Bearbeitungen entstehen.
Die hierfür notwendigen Zuschnittpläne werden automatisiert aus den einzelnen NC-Programmen, welche vom CAD/CAM-System bereitgestellt werden, generiert. Die Optimierung beinhaltet dabei auch alle Informationen für die Etikettierung und Nachverfolgung der Bauteile. Durch die Generierung einer eindeutigen Teilenummer ist das von SCHULER designte Teileetikett der Schlüssel zu allen weiterführenden Informationen dieses Bauteils.
Ebenso befinden sich wichtige Fertigungsinformationen auf dem Teileetikett. Eindeutig definierte Nummernkreise sorgen für eine fehlerfreie und zuverlässige Zuordnung der Bauteile zum zugehörigen Fertigungsauftrag.
An definierten Stellen in der Produktion erhalten die Produktionsmitarbeiter durch Infoterminals Zugang zu ggf. notwendigen Zusatzinformationen, wie bspw. Baugruppenzeichnungen, welche automatisiert vom CAD/CAM-System erzeugt und zentral bereitgestellt werden.
Ciuffo Cabinetry geht mit dem Umzug in das neue Produktionsgebäude und der Implementierung des neuen IT-Konzepts einen großen Schritt in Richtung Digitalisierung. Das Augenmerk liegt auf der Standardisierung in der Arbeitsvorbereitung und dem Aufbau eines durchgängigen Datenmodells. Das Unternehmen ist diesen Weg mit Unterstützung gegangen und nun auf dem besten Weg New York City weiterhin mit hochqualitativen Küchen aus einer vernetzten Fertigung zu versorgen.
Wichtig bei der Digitalisierung einer Fertigung ist das Erkennen des Potentials schrittweiser Veränderungen bis hin zur digitalen Produktion. Nur wer seine Prozesse kennt und analog effizient ist, der kann auch digital und die Vorteile smarter Technologien künftig gewinnbringend nutzen.
Autor: David Strom, SCHULER Consulting GmbH
Ein Artikel des Fachmagazins HK, Ausgabe 1/2019.