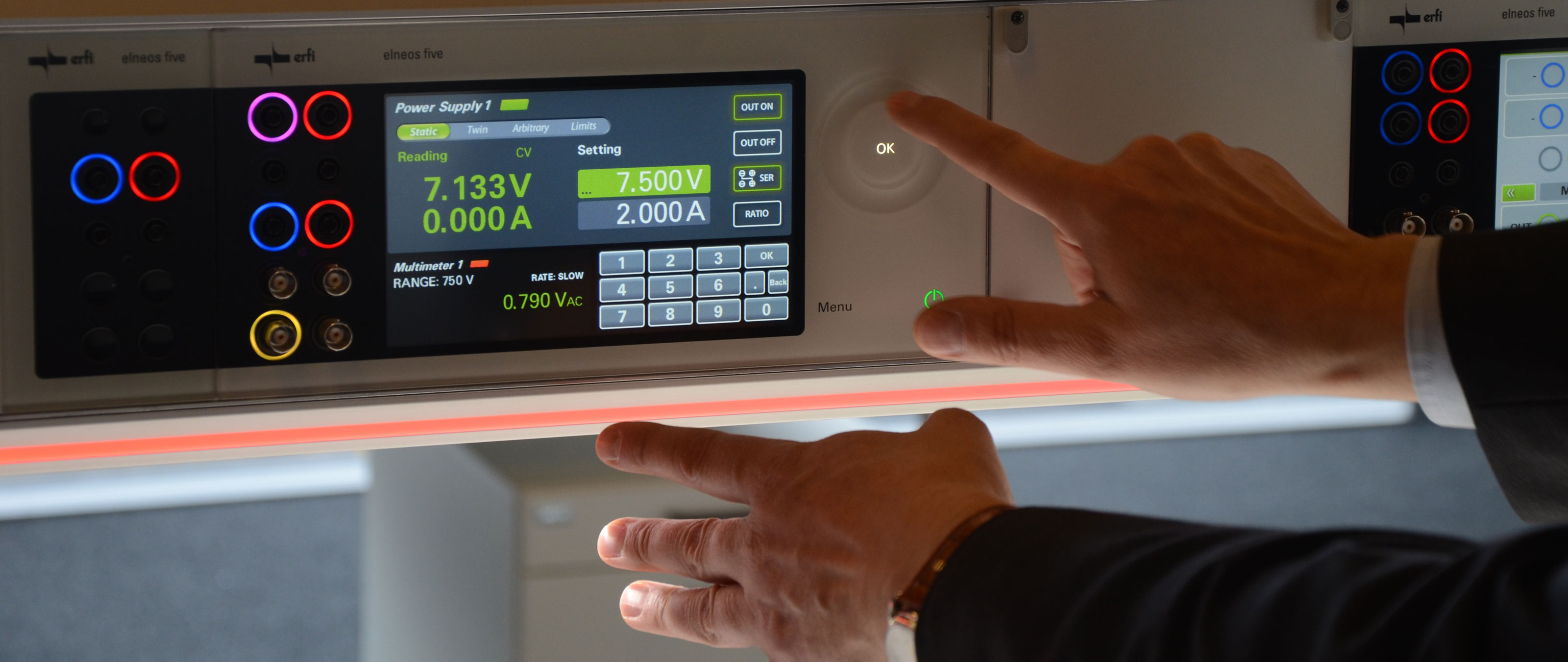
Вначале клиент намеревался только заменить кромкооблицовочный станок и установить новое программное обеспечение. Но уже на этапе планирования стало ясно, что проект станет более масштабным. Ответственные лица компании Ernst Fischer GmbH (Erfi) выбрали комплексное решение. Теперь все деревянные элементы для рабочих столов и шкафов, изготавливаемых этим специализирующимся на производстве электроники предприятием из Фройденштадта создаются на автоматизированной производственной линии HOMAG. Система уже отвечает всем требованиям Индустрии 4.0 и скоро будет готова к подключению к системе tapio.
«Надо было срочно что-то делать», — говорит Андреас Фишер, младший руководитель Erfi, описывая ситуацию на производстве, где все работы выполнялись на деревообрабатывающих станках с ручным управлением. «Мы больше не могли отвечать требованиям рынка — не могли обеспечить разнообразие модификаций и одновременное производство и единичной, и серийной продукции». Компания, изготавливающая электронное лабораторное оборудование, сборочные рабочие станции, измерительные и контрольные приборы, а также испытательные системы, на 100% выполнила рекомендации HOMAG и оснастила производство новейшим технологическим оборудованием. Компании из Фройденштадта удалось сделать огромный шаг — от отдельных станков к объединенной системе — при соблюдении всех принципов и требований Индустрии 4.0.
Станки объединенной системы удалось расположить в имеющемся цеху оптимальным образом. При взгляде на автоматическую линию подачи деталей посетитель сразу понимает, что речь идет о производстве с высоким уровнем автоматизации. В начале линии на форматно-раскроечном станке SAWTEQ B-300 (HPP 300 profiLine) выполняется раскрой плит, загрузка заготовок в который выполняется из системы штабельного хранения STORETEQ S-500 (TLF 411). Дисковая пила возвышается над рабочим столом на 95 мм, что позволяет выполнять раскрой как отдельных плит, так и пакетов. Таким образом, станок способен с минимальными затратами раскраивать большое количество заготовок. Дополнительные опции обеспечивают повышение эффективности и экономию материала. Расположенный перед раскроенным станком этикетировщик для плиточных заготовок наклеивает этикетки на еще не обработанную плиту, что дополнительно ускоряет процесс раскроя. На каждую заготовку наклеивается этикетка со штрих-кодом, которая обеспечивает идентификацию детали на протяжении всего процесса от раскроя до сборки. Между этапами раскроя и облицовки кромок разрезанные детали помещаются на сортировочный накопитель SORTEQ R-200 (TLB 321), который вмещает до 1200 деталей различного размера.
Облицовка кромок производится на многофункциональном участке нанесения кромочного материала, где для производства деталей с «нулевым швом» с объемом партии, равном одному изделию, используется laserTec – Next Generation. Для обеспечения гибкости производства в этой системе применен односторонний кромкооблицовочный станок EDGETEQ S-810 (K 610). Метод поочередной обработки сторон позволяет добиться высокой производительности даже при производстве небольших партий с постоянно меняющимися размерами. Современный уровень развития технологий позволяет переоснастить агрегат во время краткого перерыва между обработкой двух заготовок. Благодаря системе подачи детали транспортируются в продольном и поперечном направлении под требуемыми углом и с соблюдением необходимых размеров. Мощный фуговальный агрегат с высокоточными гидравлическими инструментами, позволяющими избежать возникновения вырывов, обеспечивает точность форматной обработки при поточном режиме работы. На этапе склеивания возможна обработка двенадцати различных кромок в автоматическом режиме без ручного вмешательства. Лазерный агрегат, в котором используется новая диодная технология, оптимизирован по мощности, а благодаря простой конструкции очень надежен и занимает меньше места, чем лазерный агрегат предыдущего поколения. Кроме того, для приклеивания кромок может использоваться полиуретановый клей, выполняющий высокие требования к устойчивости к нагреву и влаге.
Система возврата с интегрированным поворотным модулем с высокой эффективностью обеспечивает непрерывный поток материалов. Обработанные заготовки автоматически сортируются: все прямоугольные детали возвращаются на сортировочный буферный склад, после чего автоматически направляются в обрабатывающий центр DRILLTEQ H-600 (BHX 560) для сверления и фрезерования. Детали произвольных форм распознаются на выходе из зоны обработки кромок и с помощью робота-манипулятора направляются на производственный участок с ЧПУ и роботом-манипулятором для дальнейшей обработки.
Основным элементом участка с ЧПУ является обрабатывающий центр CENTATEQ P-500 (BMG 512) модульной конструкции, конфигурируемый в соответствии с пожеланиями и запросами клиента. Ответственные за производство сотрудники Erfi считают, что наиболее важным достоинством BMG является гибкость. Так, в качестве фрезерного шпинделя был выбран 5-осный шпиндель Drive-5C+. Консольный стол с высокоточными линейными направляющими и надежным закладочным механизмом с двумя пневматическими цилиндрами упрощает перемещения заготовок, сверлильная головка Multi Processing Unit, поворачивающаяся на 360 градусов и позволяющая позиционировать любой из шпинделей под произвольным углом. Это также касается цепного устройства смены инструмента на 72 места, гарантирующего высокую скорость смены, возможность использования большого количества инструментов и агрегатов, а также гибкость в эксплуатации. Поскольку заказчик указал на необходимость обеспечить одинаково высокое качество обработки как прямых, так и изогнутых кромок, для обработки фасонных деталей была выбрана система laserTec. Поскольку продолжительность обработки при этом значительно увеличивается, функции по транспортировке деталей выполняются промышленным роботом с 5-осями. В результате оператор получает возможность управлять несколькими станками одновременно.
Робот сразу привлекает внимание всех входящих в производственный цех Erfi. Он наиболее явно свидетельствует о высокой степени автоматизации производства. При этом автоматизация начинается на гораздо более раннем этапе — этапе объединения подготовительных данных заказа, данных системы CAD/CAM и управления спецификациями. Благодаря системе управления производством ControllerMES HOMAG для каждой детали составляются программы ЧПУ и производственные данные, которые затем заблаговременно передаются на станки. Здесь каждой детали присваивается уникальный идентификационный номер, который будет действителен до момента окончательной сборки. «Система управления производством ControllerMES от HOMAG представляет собой платформу, которая позволяет организовать и оптимизировать автоматизированные и выполняемые вручную производственные процессы», — рассказывает о новых технических возможностях Петер Битцер, IT-специалист и системный администратор Erfi.
«Модульная система обеспечивает надежную поддержку производственного процесса Erfi — с момента конфигурирования и оптимизации производственных данных и планирования производства и до проверки после завершающего монтажа», — добавляет Харальд Зибер, старший менеджер по продажам компании HOMAG Systems. «Таким образом, программное обеспечение создает условия для изготовления многовариантной продукции в рамках индивидуального заказа с помощью объединенной системы». Одновременно ПО обеспечивает прозрачность производственного процесса, предоставляя информацию о статусе каждой детали, благодаря чему степень готовности каждого заказа можно проверить в любой момент. В результате контроль и управление процессом производства становятся еще более эффективными. Проблемные ситуации распознаются на раннем этапе. В случае повреждения штрих-код позволяет обеспечить изготовление замены заранее, а не только после обнаружения дефекта во время сборки. Особенностью ControllerMES является возможность объединения производственных заказов. «Таким образом, в режиме предварительного просмотра можно выбрать так называемые "возможные детали" и объединить их с "обязательными деталями" по текущим заказам для составления оптимальной схемы раскроя с минимальным количеством отходов», — описывает преимущества Петер Битцер.
В этом случае слово «экономичность» не способно в полной мере описать преимущества ControllerMES — система не просто сокращает затраты, она инвестирует в будущее. Уже сейчас заметно повышение производительности, обеспечиваемое снижением расхода материалов, времени простоя и непроизводительных операций, а также увеличение скорости производства. Модульная стандартная программа допускает возможность гибкой настройки, расширения и адаптации при вводе новых процессов, а также возможность обновлений системы. И именно на этот факт уже обратило внимание руководство Erfi, которое намерено внедрить систему управления производством ControllerMES и на участках изготовления дополнительных деталей и электроники. Поскольку система подключена к tapio, первой в мире цифровой платформе для деревообрабатывающей промышленности (см. HK 6/17), цифровые приложения, например MachineBoard, позволяют запросить информацию о текущем статусе станка, просмотреть сообщения о неисправностях или ошибках с помощью смартфона. Система, в свою очередь, передает на смартфон оператора важные сообщения, например, о сбоях. В этом аспекте организация производства компании Erfi также полностью соответствует критериям Индустрии 4.0.
Ein Artikel des Fachmagazins HK, 01/2018. Источник фотоматериалов: Magazin HK. Hier lesen Sie den Artikel auf hk-magazin.com.
Видеоролики
Please confirm that when you use YouTube, data such as your IP address, browser identifier and similar may be transmitted to Google.
» Политика конфиденциальности
Industry 4.0 at erfi Ernst Fischer GmbH