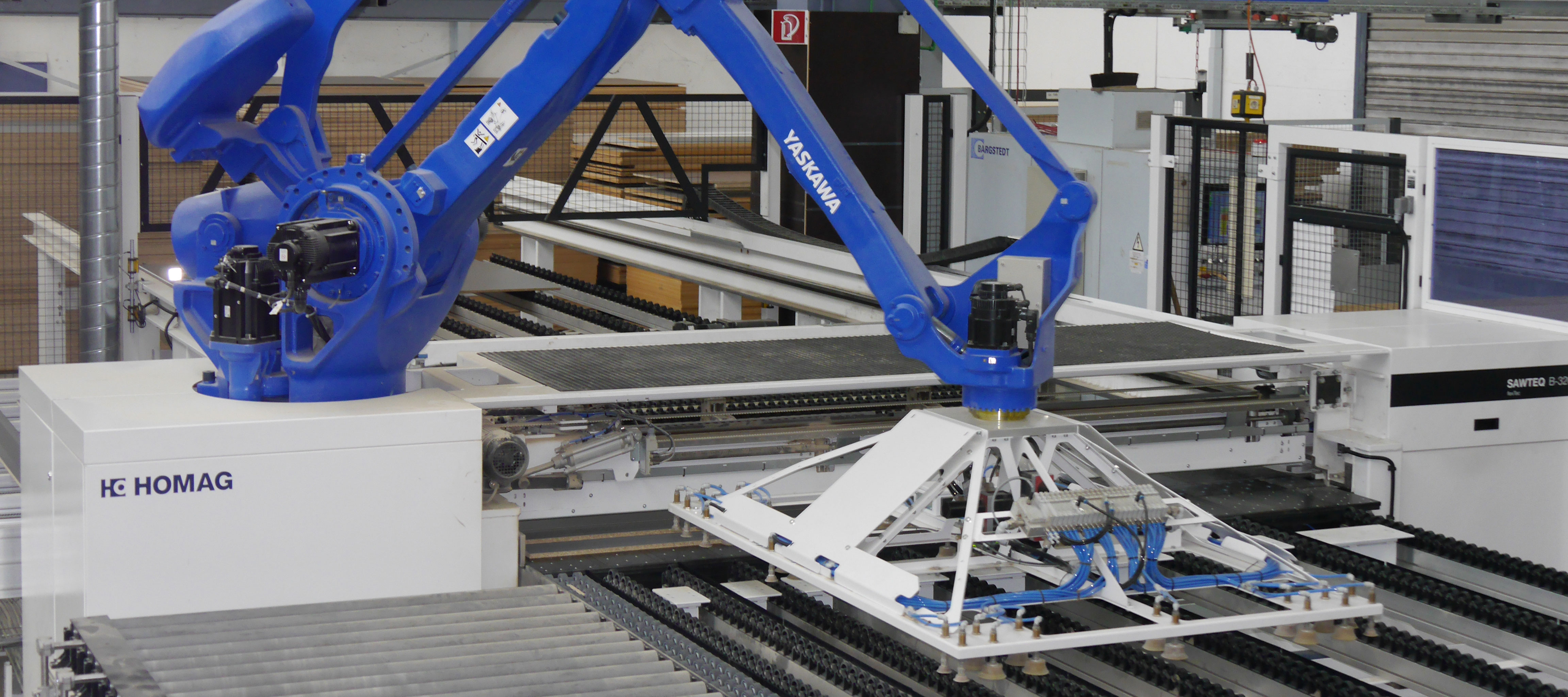
Rapidità e flessibilità rivestono un'importanza fondamentale per i responsabili di Duravit. Per questo motivo, l'azienda produttrice di mobili per il bagno ha acquistato dalle tecnologie di sezionatura per pannelli di Homag due impianti di sezionatura identici con alimentazione robotizzata, che vengono alimentati con materiale grezzo prelevati da magazzini automatici di pannelli. Grazie all'impiego dei robot industriali, Duravit raggiunge così quasi il 100% di disponibilità. HK ha visitato l'azienda nello stabilimento di Schenkenzell.
Ulrich Weber, ingegnere e direttore dello stabilimento di produzione di mobili di Duravit AG a Schenkenzell, nella Foresta Nera, descrive così la sua sede di lavoro: "Abbiamo in produzione circa 87.000 pezzi, più 20.000 pezzi sezionati che devono immediatamente passare in produzione. Infatti non abbiamo alcun deposito per i pezzi dei mobili: ogni pezzo in produzione appartiene a una commessa", quindi la sua grandezza non fa alcuna differenza. In realtà, nel processo di produzione automatico sono presenti due magazzini, ma si chiamano polmoni di deposito e di smistamento. Entrambi garantiscono che nella linea di squadratura vi sia il minor numero possibile di modifiche e che durante la sezionatura sia possibile portare a termine in modo ottimale gli schemi di taglio. Nel complesso, Duravit ha sviluppato 20 criteri e li ha memorizzati nel sistema di controllo della produzione per ottenere la massima efficienza possibile.
Ulrich Weber è entrato a far parte dell'azienda produttrice di mobili per il bagno nel 1993 e ha contribuito in modo significativo allo sviluppo dello stabilimento, che fino al 1992 era una fabbrica di tessuti. L'azienda produttrice anche di sanitari in ceramica desiderava aumentare il grado di integrazione verticale e includere nella propria gamma di prodotti anche mobili per il bagno e lavabi sottopiano. Weber, in quanto giovane direttore di stabilimento, era fin dall'inizio intenzionato a creare un flusso di produzione ottimale. Con il suo team è riuscito a farlo.
Chi oggi visita lo stabilimento di mobili Duravit di Schenkenzell non può credere ai propri occhi, perché si trova davanti a uno stabilimento di produzione simile a quelli dell'industria automobilistica. L'intera produzione è organizzata in modo completamente automatico ed è protetta da recinzioni alte due metri, con ponti pedonali che impediscono ai visitatori o agli operatori di interferire con il flusso di produzione. "Grazie all'elevato grado di automazione abbiamo anche ottenuto un miglioramento della qualità, poiché i componenti non sono quasi più soggetti a danneggiamenti", spiega Ulrich Weber. Tutto parte dalla sezionatura. Sono presenti due impianti di sezionatura identici, ciascuno costituito da una "Sawteq B-320 Flextec" con movimentazione robotizzata e collegato all'intera produzione organizzata in modo industriale tramite trasportatori a rulli e nastri trasportatori. Entrambe le "sezionatrici robotizzate" sono alimentate da due magazzini orizzontali contenenti materiali per pannelli organizzati in modo caotico e controllati in modo computerizzato. Questi magazzini corrispondono al nuovo "Storeteq S-500" Homag.
Il secondo magazzino orizzontale è situato in un capannone adiacente e ha un terzo in più di capacità di stoccaggio. Tramite un carrello elevatore, i pannelli grezzi vengono trasportati in base alle necessità al magazzino 1 e qui vengono ricevuti dal dispositivo di controllo computerizzato.
Nel magazzino orizzontale avvengono sia l'immagazzinamento sia lo smistamento e il trasferimento alle sezionatrici, che sono state concepite come celle di sezionatura per il taglio individuale di singoli pannelli e per la produzione su commessa. Le commesse dei clienti vengono raggruppate dal controllo della produzione in base al tipo di materiale al fine di creare la minore quantità possibile di scarti di taglio. Dopo l'esecuzione degli schemi di taglio corrispondenti, i pezzi che non devono essere bordati passano direttamente all'accatastamento. Invece, i componenti che necessitano di bordatura vengono immagazzinati temporaneamente nel "Sorteq H-600", un deposito che funge da polmone di disaccoppiamento, e vengono trasferiti mediante un trasporto intermedio adeguato alle necessità verso la bordatrice monolato "Edgeteq S-800". In questo modo è possibile guidare in successione, su commissione, pezzi di dimensioni diverse.
Il dispositivo di ritorno "Loopteq C-500" è realizzato come linea a "O" in cui i componenti vengono completamente bordati in uno, due o tre passaggi. Successivamente i componenti passano allo smistatore quadruplo "TLB 210" o direttamente all'accatastamento. La stazione di deposito con accatastamento robotizzato garantisce il trasferimento dei componenti di un lotto di smistamento nella sequenza prestabilita. Inoltre, a seconda della funzionalità i componenti vengono trasportati verso centri di finitura che eseguono lavori di fresatura, foratura o sezionatura in modo specifico per i componenti. Una parte dei pezzi viene inoltre verniciata, con applicazione di colori personalizzati in base al cliente. In questo caso, in particolare, i vantaggi della produzione su commissione sono evidenti.
I robot giocano un ruolo significativo per il successo di tutta la linea di produzione, poiché grazie alla tecnologia del vuoto spostano i pannelli in modo delicato. Inoltre, grazie alla precisione dei movimenti garantiscono il massimo livello di qualità. Con i collaudati robot industriali, le interruzioni di produzione seguono pressoché esclusivamente le indicazioni prestabilite con una disponibilità quasi pari al 100%. A ciò si aggiunge un tasso di errore estremamente ridotto.
La stampante per etichette con scanner di controllo integrato, una per ogni impianto, contrassegna tutti i pezzi in modo completamente automatico incollando l'etichetta del codice a barre sul pezzo tagliato poco prima esca dall'impianto. Nella fattispecie, le etichette contengono tutte le informazioni per le finiture successive.
Con una potenza fino a 1.500 pezzi per turno, i costi unitari della produzione in lotto 1 vengono notevolmente ridotti. Non immediatamente evidente allo sguardo dei visitatori nei processi di produzione è la potenza dei computer, che lavorano in modo silenzioso e affidabile nella rispettiva scatola nera. In questo modo l'impianto Homag, collegato al sistema di gestione "Controller MES", consente di raggiungere gli obiettivi degli utilizzatori. In effetti, il "Controller MES" gestisce le commesse dei clienti e della produzione provenienti dal sistema di pianificazione di Duravit riproducendo i dati sui sistemi di comando delle singole macchine di finitura.
Ulrich Weber racconta così la sua esperienza: "Ciò che durante il colloquio di vendita viene descritto come semplice, nella pratica è molto diverso. "A chiunque voglia creare un impianto di questo tipo consiglio di tenere in considerazioni gli aspetti tecnico-informatici". Per Ulrich Weber, gli investimenti nelle due "segatrici robot" e nella linea di squadratura automatica non devono essere effettuati con un semplice calcolo dell'ammortizzazione. "Perché non abbiamo solo comprato macchine, abbiamo anzi realizzato un cambio di sistema e ci siamo attrezzati per il futuro", aggiunge Weber. Naturalmente, il responsabile dello stabilimento conosce in prima persona il valore rappresentato dal risparmio di un collaboratore nel calcolo dell'ammortizzazione. Ma come si fa trasformare in cifre tempi di consegna più brevi, maggiore qualità e flessibilità e un'elevata disponibilità degli impianti?
A questa domanda Ulrich Weber non risponde, ma sta già esplorando una nuova sfera di attività. Intende ridurre gli scarti di taglio sulle sue "segatrici robot". "Ogni punto percentuale corrisponde a 50.000 euro", conclude con scaltrezza.
«Grazie all'elevato grado di automazione abbiamo anche ottenuto un miglioramento della qualità, poiché i pezzi non presentano quasi più danneggiamenti»Ulrich Weber, direttore dello stabilimento di produzione di mobili di Duravit AG a Schenkenzell