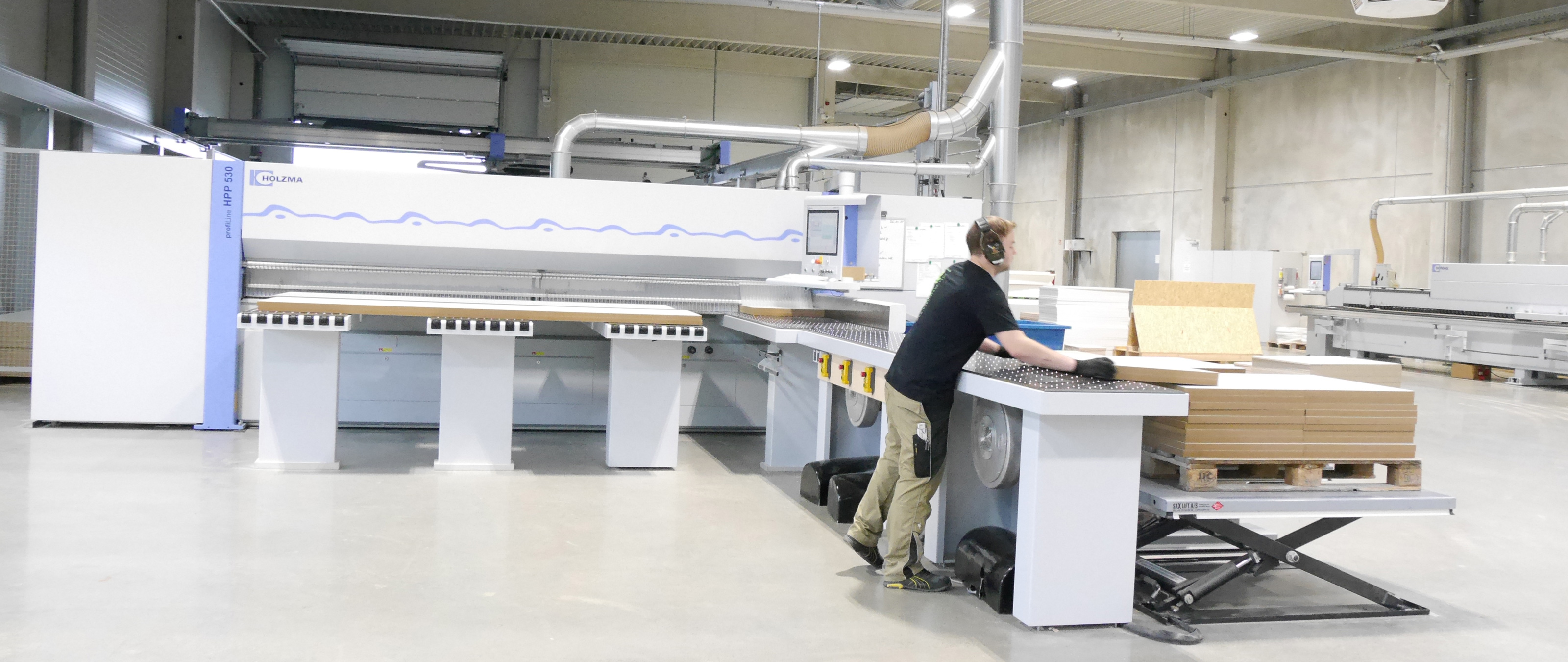
«Больше не нужно наклоняться»
Не важно, надо ли распилить одну панель или сто, твердый пенопласт или пару листов слоистого пластика высокого давления: для обслуживания производственной ячейки, состоящей из пилы и системы складирования производства Holzma и Homag Automation, в компании Popp достаточно одного человека. Ему не надо наклоняться или переносить тяжести.
Клеменс Симон, работник компании Popp из Форххайма, легко справляется с распиливанием сразу двух плит из МДФ толщиной 22 мм и размером 4100 x 2800 мм каждая. При работе с более крупными партиями он разрезает пакеты толщиной до 115 мм, состоящие из пяти или шести плит. Программа позволяет пиле HPP 530 profiLine компании Holzma разделить пакет на четыре-пять полос длиной 4100 мм и шириной от 300 до 500 мм.
Компания Schreinerei Popp поставляет серийную и штучную продукцию промышленным предприятиям, университетам, муниципалитетам, домам престарелых и частным клиентам. Предприятие известно производством серийной продукции из древесных и высокотехнологичных материалов для медицинской техники. Кроме того, Popp специализируется на трехмерном фрезеровании. Сегодня Франк и Соня Гепперт руководят предприятием, основанным прадедушкой Франка в 1905 году. Предприятие, когда-то представлявшее собой обычную столярную мастерскую, постепенно превратилось в поставщика промежуточной продукции для других промышленных компаний. На предприятии занято 60 сотрудников, два года тому назад высокотехнологичное производство было перенесено на новую площадку площадью 6000 м². Производство разделено между цехом деревообработки и обработки пластмасс.
Толкать, а не поднимать
Трех-четырех ударов о край мусорного контейнера Клеменсу Симону хватает, чтобы измельчить и выбросить обрезки, а пакет нарезанных полос он передает вперед на длинные столы, расположенные перпендикулярно линии раскроя. Кажется, ему не приходится при этом напрягаться. Ведь стол станка и продолжающие его дополнительные столы оснащены системой шариковых воздушных форсунок. Подача воздуха через форсунку для формирования воздушной подушки начинается, когда пакет нажимает на шарик. Пока Клеменс Симон продолжает нарезку, автоматическая система штабельного хранения TLF 411 производства Homag перемещает материал для следующего пакета к задней части пильного станка, на загрузочный выравнивающий стол. После того, как разрезана последняя полоса, и извлечены все обрезки, Клеменс Симон поворачивает и передвигает одну полосу за другой к угловой линейке и в правые захваты толкателя.
Пильный станок с программным управлением делит полосу в продольном направлении. С каждым ходом пакет нарезанного материала перемещается на передний стол. Клеменс Симон должен рассортировать его для последующей обработки и разделить на три штабеля. Эта работа также не кажется сложной. Стол с воздушной подушкой перед угловой линейкой удлинен примерно на 4 м. За ним расположены подъемные столы для отдельных штабелей. Верхняя плита автоматически размещается на пару миллиметров ниже уровня стола. Клеменсу Симону не приходится поднимать пакет плит, и он легко передвигает его к соответствующему штабелю.
Теперь ячейка выходит из режима серийного производства и выполняет нарезку для единичного изделия. Изготавливается специальная многослойная структура с основой из высококачественного твердого пенопласта и покрытием из слоистого пластика высокого давления, предназначенная для медицинского прибора. Пильный станок и система складирования легко справляются и с этими материалами.
«Все цели достигнуты»
До того, как предприятие в 2013 году переехало из Байерсдорфа в Форххайм, сотрудникам приходилось выполнять раскрой на пиле Holzma примерного такого же размера, и эта работа требовала значительного физического напряжения. Тогда, как и сегодня, раскрой производился оперативно, и ежедневная норма составляла примерно 30 плит. После переезда Гепперты решили освободить своих сотрудников от необходимости поднимать плиты и приобрели ячейку раскроя. Кроме состоящей из пильного станка и системы складирования ячейки в цехе установлены четыре обрабатывающих центра, кромкооблицовочный станок и автомат вставки шкантов, все — производства Homag Group. Франк Гепперт считает, что инвестиции себя оправдали: «Мы выполнили задачи, которые ставили перед собой при приобретении оборудования: Больше не нужно наклоняться, горбиться или разыскивать нужные детали. Там, где раньше двое работали восемь часов подряд, сейчас один человек справляется всего за семь часов. Кроме того, ячейка раскроя может обрабатывать все используемые нами материалы. Остатки не представляют для нас проблемы: мы производим серийную продукцию и можем полностью раскраивать любые плиты».
Опубликовано в DDS, январь/2016. Holzma благодарит ответственного редактора Георга Молински. Мы также благодарим нашего клиента Popp GmbH & Co. KG.
Источник изображений: DDS/Георг Молински
«Мы выполнили задачи, которые ставили перед собой, когда принимали решение о приобретении оборудования: Больше не нужно наклоняться, горбиться или разыскивать нужные детали. Там, где раньше двое работали восемь часов подряд, сейчас один человек справляется всего за семь часов. Кроме того, ячейка раскроя может обрабатывать все используемые нами материалы. Остатки не представляют для нас проблемы: мы производим серийную продукцию и можем полностью раскраивать любые плиты.»Франк Гепперт, управляющий Popp GmbH & Co. KG