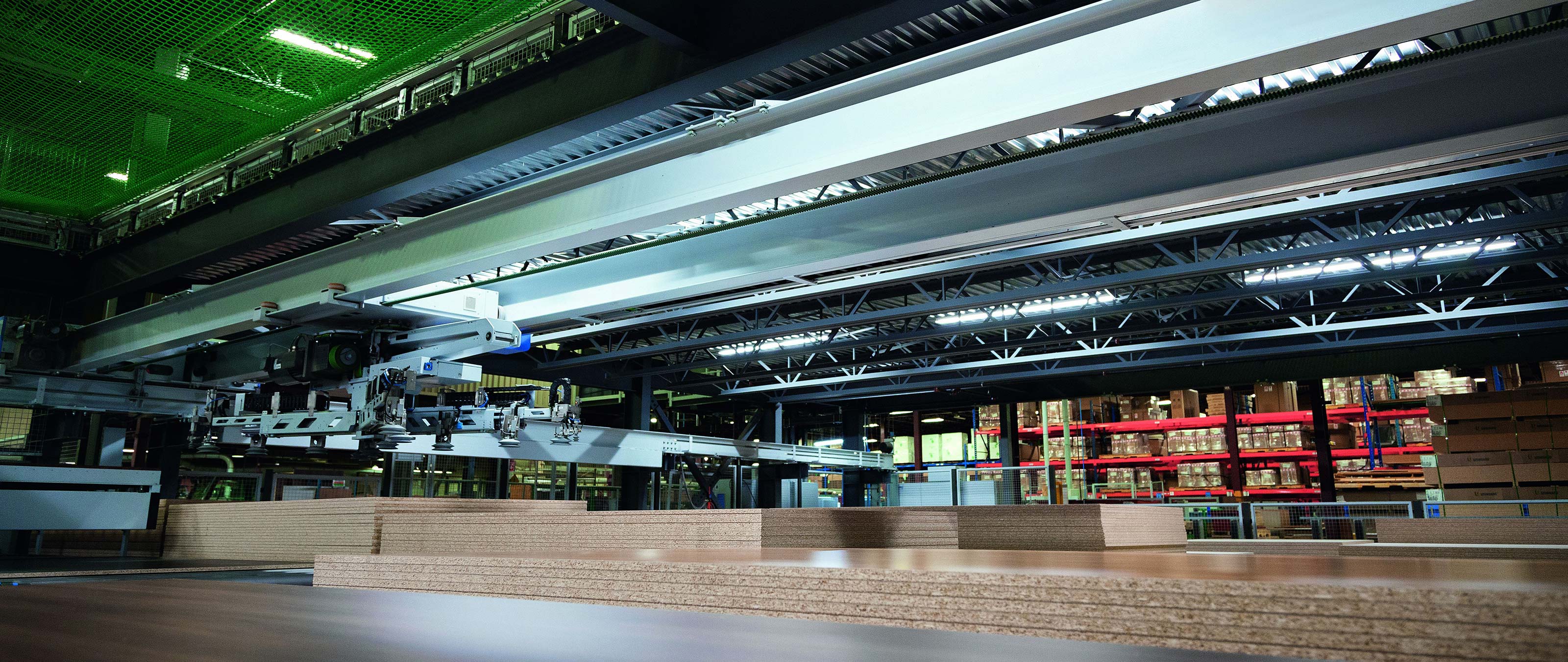
Der kanadische Büromöbelhersteller Artopex setzt auf die neuesten Trends – nicht nur bei Schreibtischen, Schränken und Stühlen.
Hinter dem Sicherheitszaun stapeln sich hunderte Holzplatten mit buntem Dekor. Ein Vakuumgreifer flitzt über dem Lager hin und her. Er weiß genau, wo die gesuchte Platte liegt, senkt sich auf sie herab und legt sie auf eine Förderstrecke. Kurz darauf frisst sich die Säge ins Holz und schneidet die Platte in mehrere Teile. Aus ihnen werden Möbel, die schon Tage später in einem nordamerikanischen Büro stehen werden. Das hochmoderne 2-Etagen-Flächenlager und die vollautomatische Roboter-Säge bilden die erste erfolgreiche Etappe einer großen Ersatz- und Erweiterungsinvestition, mit welcher der kanadische Büromöbelhersteller Artopex die HOMAG Group beauftragt hat. Über zwei Jahre hinweg wird sie am Standort Granby bei Montreal die alten Produktionsanlagen schrittweise durch eine vollautomatische Fertigung ersetzen.
Hilfe vom digitalen Zwilling
Die Experten aus Deutschland werden bis 2019 alle Maschinen so anliefern und aufbauen, dass die Fertigung nicht unterbrochen werden muss. Ein Eingriff so komplex wie eine OP „am offenen Herzen“. Einen ungewollten Stillstand der Fertigung darf es auf keinen Fall geben. Das wäre ebenso fatal wie kostspielig. Die HOMAG Group kennt sich aus mit solchen Einsätzen. „Perfekte Planung und viel Erfahrung sind erforderlich“, sagt Wolfgang Kläger aus dem technischen Vertrieb der Business Unit „Systems“. Jeder einzelne Lieferschritt der gestaffelten Implementierung steht lange vorher fest und wird geprobt, bis er reibungslos funktioniert. Das geschieht auch mithilfe eines 3-D-Simulationsmodells, das die neue Fertigungsstraße virtuell nachbildet. An diesem digitalen Zwilling laufen zahlreiche Tests ab. Der wichtigste betrifft das Fertigungsleitsystem controllerMES. In dieser Softwareplattform der HOMAG Group laufen im Realbetrieb alle Fäden des vernetzten Produktionsprozesses zusammen. Sie befiehlt jeder Maschine, was sie zu tun und zu lassen hat. Anhand der integrierten Reporting-Funktionen kann sie kontrollieren, ob ihre Anweisungen befolgt werden.
Vertrauen in die HOMAG Group
Angesichts dieser Vorkehrungen bleibt Denis Bergeron gelassen. Er arbeitet seit vielen Jahren mit der HOMAG Group zusammen. „Ich weiß, dass ich mich bei der Umsetzung auf sie verlassen kann“, sagt der Vizechef von Artopex. Er ist ein Wegbegleiter des Unternehmers Daniel Pelletier, der den 38 Jahre alten frankokanadischen Familienbetrieb 1993 übernommen hat. Heute arbeiten bei Artopex an fünf verschiedenen Standorten 650 Personen. Sie entwerfen und bauen hochwertige Büromöbel: Schreibtische, Aufbewahrungsmöbel, Industriestühle, weiche Sitzmöbel, Akustikplattensysteme und Trennwände. Die Möbel haben ihren eigenen Stil. Leichte Formen, helle Farben und Individualität prägen das Sortiment. „Wir wollen die Bedürfnisse unserer Kunden genau erfüllen“, sagt Bergeron. In modernen Unternehmen machen Designer oft strenge Vorgaben, um den Bürolandschaften ein eigenes Profil zu verleihen. Bei Artopex kann deshalb jedes einzelne Stück individuell und trotzdem wie am Fließband gefertigt werden.
Pioniere aus Tradition
Schon Ende der 90er Jahre kaufte Artopex bei der HOMAG Group ein Flächenlager mit zwei integrierten Sägen – damals eine Sensation in Nordamerika. Ein paar Jahre später stellte Artopex auf eine Kleinserienfertigung in Losgröße 1 um. Elektronisch gesteuert wissen seitdem alle Maschinen, wie sie ein Teil individuell bearbeiten müssen. Ganz früh kaufte Artopex dafür ein Bearbeitungszentrum sowie eine Kantenleimmaschine, die mit der Bohrtechnik verkettet war. „Wir wollten immer Vorreiter in Sachen Technologie sein“, sagt Bergeron.
Im Jahr 2014 hatten die Anlagen ihren Dienst lange genug versehen. Bergeron dachte über eine neue Fertigung nach. Den Anstoß gab eine Technologie-Tour, die er mit der HOMAG Group in Europa machte. Eine Woche lang standen diverse Fabrikbesuche auf dem Programm – immer mit der neuesten Technologie. Die Vertreter von Artopex waren begeistert. Daraufhin traf der Vorstandsvorsitzende Daniel Pelletier die Entscheidung, eine vollautomatische Fertigung zu bauen. Die sollte vor allen Dingen schneller sein als die bisherige. Seine Bedingung: Bis zu 4000 Teile am Tag sollten geschnitten, formatiert, mit Kante versehen und gebohrt oder gefräst werden können. Das macht bei Vollauslastung bis zu vier Teile pro Minute. Ein Spitzenwert.
Nichts für schwache Nerven
Gleich nach Ende der Reise begann die Planung. Die lokale Vertriebsgesellschaft HOMAG Canada und der technische Vertriebsmann Kläger setzten das Projekt gemeinsam mit Artopex in die Spur. Die insgesamt fünf Implementierungsabschnitte sollten sich über zwei Jahre erstrecken – bei laufender Produktion. Im ersten Schritt sollte das neue vollautomatische Flächenlager entstehen und an die Säge angebunden werden. „Gemeinsam mit dem Kunden sind wir durch die Fabrik gegangen und haben überlegt, wohin wir welche Teile der Anlage während der Implementierung schieben dürfen, damit die laufenden Maschinen weiterproduzieren können“, sagt Kläger. Nichts für schwache Nerven. Das neue Material muss abgelegt und so sortiert werden, dass jedes Teil sofort verfügbar ist, wenn es gebraucht wird. Stahl, Kabel, Werkzeuge – das macht Tonnen an Gewicht. Beim Rundgang stieß Kläger auf eine Ablagefläche für Platten, die nicht mehr gebraucht wurde. Hier ließ sich das neue Flächenlager einrichten und mit den Sägen verketten. „Diese erste Etappe ließ sich relativ einfach umsetzen“, sagt Kläger. Flächenlager und Säge sind seit Ende 2017 in Betrieb. Jetzt folgen die nächsten Schritte.
Schritt für Schritt zur neuen Fabrik
Bis Herbst 2018 wird ein Entkopplungspuffer eingegliedert. Er ist ein wichtiger Bestandteil der Fertigungsstraße – die zugeschnittenen Teile legen dort sozusagen eine Pause ein. Fehlt es an Nachschub aus dem Lager, kann die Produktion trotzdem weitergehen. Ebenfalls bis Herbst soll die Kantenbearbeitungsanlage stehen. Kanten sind das Aushängeschild für gute Möbel. In den Fugen darf sich kein Schmutz sammeln. Die Maschinen der HOMAG Group positionieren die Kanten in der passenden Farbe am richtigen Teil. Ein Laserstrahl bringt das Kantenband zum Schmelzen, bevor es mit der Platte verpresst wird.
Anlagen zur Kantenbearbeitung können ungewöhnliche Formen bearbeiten – aber es gibt Grenzen. Sollten Möbelkunden sich ein völlig ausgefallenes Design wünschen, übernimmt die Kanten bei Artopex ein elektronisches Bearbeitungszentrum der HOMAG Group, das für kompliziertere Aufgaben ausgelegt ist und seinen Platz neben der Fertigungsstraße finden wird.
Vernetzt bis zum Kunden
Ab Herbst 2018 kommt die Bohrtechnik hinzu, dann der Sortierpuffer im Frühjahr 2019. Er bringt die bearbeiteten Teile abschließend in die richtige Reihenfolge für die vorhandenen Montagebänder. Im fünften Schritt folgen eine weitere Säge und eine zweite Kantenbearbeitung. Dadurch wird die Produktionsleistung noch einmal verdoppelt und die Bereiche Zuschnitt und Kantenbearbeitung werden redundant gehalten. Artopex hat schon Pläne für die Zeit nach dem Umbau: Das Unternehmen überlegt, die Fertigungsstraße zu verlängern. Vernetzte Maschinen sollen
die Teile künftig auch verpacken. Diese müssen anschließend nur noch auf Lastwagen verladen und dann beim Kunden zusammengesetzt werden. „Die vollautomatische Fertigungsstraße ist dann komplett“, sagt Denis Bergeron. „So wird Artopex noch lange Vorreiter in Sachen Technologie bleiben.“
Der digitale Zwilling
Digitale Zwillinge kommen in der Maschinenbaubranche immer häufiger zum Einsatz. Dabei handelt es sich um virtuelle Maschinen, die vor dem Bau einer realen Maschine als deren Abbild erstellt werden. Der Zwilling wird in Form einer echtzeitfähigen, sogenannten „Hardware in the Loop“-Simulation ausgeführt. Diese macht es möglich, schon vor dem Bau sämtliche Funktionen der Maschine an ihrem digitalen Zwilling abzuprüfen.
Weitere Vorteile des Zwillings: Durch eine realitätsnahe Abbildung komplexer Materialflüsse kann er zur Optimierung von Anlagen genutzt werden, aber auch zum risikolosen Test weiterentwickelter Software. Durch den Einsatz des Systems über den ganzen Lebenszyklus einer Maschine könnten zukünftig im Servicefall Probleme nachgestellt und so schneller gelöst werden.
„Ich weiß, dass ich mich bei der Umsetzung auf die HOMAG Group verlassen kann.“Denis Bergeron, Vice President, Artopex Inc.