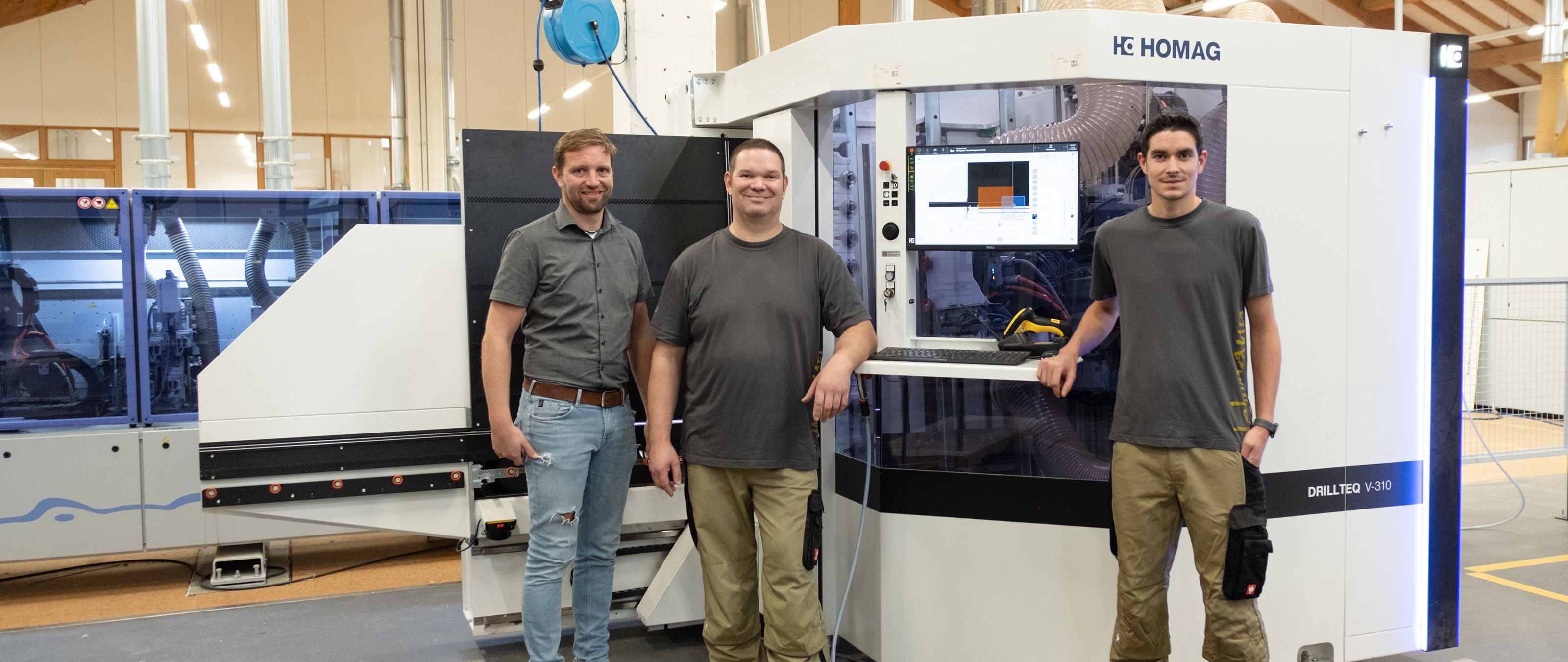
4050 m² of operating space, 65 employees, more than 70 years of experience: the Lehmann workshop has grown continuously but at the same time, has its roots firmly in the carpentry sector. Since 1951, the classic carpentry workshop has become a modern family business for high-quality and made-to-measure interior fittings in the private sector, gastronomy and in public sector properties—and the company in the Black Forest is also internationally active in area of store design and fittings. The integrated production depth makes the company particularly strong—from veneer manufactured in-house to the solid wood warehouse.
However, the greatest strength of the company located at Zell am Harmersbach is doubtless, as the employees confirm, the family-like atmosphere. Many have been trained within the company and, as a result, there is a high level of staff retention. Despite its size, the carpentry business can therefore operate in an agile fashion in the same way as a small business. The customers appreciate this, too. It results in a high degree of commitment and delivery reliability, not to mention the quality of the craftsmanship with design attributes. At any time, owner Stefan Lehmann can rely on his employees, and that is important to him. It means they can realize challenging projects as well: "We're not afraid of anything, we've managed everything up to now."
In addition to the company's own design department and the construction team, this is ensured above all by the expertise in project management and the excellently equipped workshop. When it comes to the machine pool, the Lehmann workshop relies on HOMAG whenever possible. After all, according to CNC expert Ingo Giesler, operation of HOMAG machines has been ingrained over the years, and the quality of the machines is beyond any doubt. That is why the company wanted a HOMAG machine when purchasing a stationary CNC processing center intended to relieve the burden on the horizontal CENTATEQ. The problem at the time was that HOMAG did not actually have a machine in its portfolio that could meet the desired processing spectrum over the 12 square meters available.
Perfect timing
Foreman Christoph Lehmann and CNC specialist Ingo Giesler had already decided on another machine. There was no space available for a second CENTATEQ and the requirements were not suitable for a small DRILLTEQ. Fortunately, the DRILLTEQ V-310 was still looking for a pilot workshop. Foreman and users were immediately convinced. And that is still the case. In the meantime, the V-310 has been in operation for several months, right next to the horizontal machine. What makes foreman Christoph Lehmann particularly happy: "It has hardly any flaws for a pilot machine. And if something doesn't work, Mr. Rasche from HOMAG solves all the problems."
Together with the experts from HOMAG Bohrsysteme, Christoph Lehmann developed the perfect machine configuration, which requires only a few manual interventions in day-to-day operation. If manual intervention is necessary, this is done with minimal effort, confirms Martin Brucher. This is an enormous advantage in peak times: trimmers can be used on both processing centers, and an urgent job can be processed in parallel.
Ingo Giesler and his CNC colleague Martin Brucher also appreciate the ability to drill very small parts. This is an enormous time saving because in the past, temporary solutions were always required. This processing is made possible by the collet chuck system, which also saves resources. It means that vacuum suction units do not have to be set, which is very time consuming. Another advantage of the machine is that parallel series of holes can be drilled at high speed thanks to the split-head Clamex combination.
Positive feedback from all employees
Even though the machine is already working perfectly, the company from the Black Forest is working together with HOMAG on further improvements. A mini mitering revolution is already in the starting blocks. It is no wonder that it is not only the foremen, operators and managing directors who are satisfied with the machine. The other carpenters in the workshop also appreciate this space-saving miracle. After all, thanks to this machine, waiting times on the CNC are a thing of the past.
“If it weren’t for the V-310, we would either still not have a second CNC, or it wouldn’t be a HOMAG.”Ingo Giesler, CNC Specialist Lehmann Joinery
Manfred Lehmann Innenausbau GmbH
4,050 m² of operating space, 65 employees, more than 70 years of experience: the Lehmann workshop has grown continuously but at the same time, has its roots firmly in the carpentry sector. Since 1951, the classic carpentry workshop has become a modern family business for high-quality and made-to-measure interior fittings.
More information