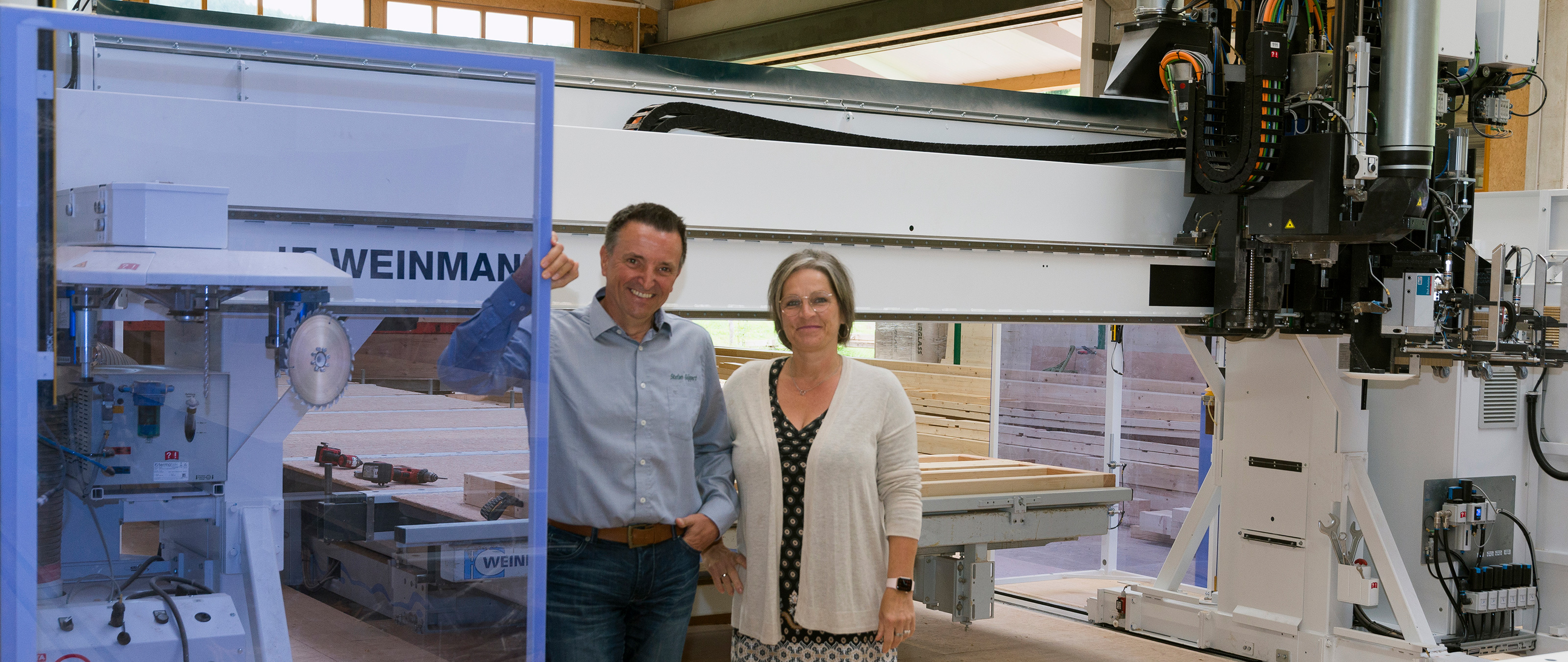
W chwili obecnej duże zainteresowanie zautomatyzowaną technologią produkcji dotyczy również małych przedsiębiorstw z sektora drzewnego. Jeżeli w istniejącej hali jest zbyt mało miejsca, a rozbudowa nie jest możliwa, może to stać się wyzwaniem dla projektantów. Przy tym nie chodzi tylko o zintegrowanie potrzebnych maszyn z układem hali. Jeszcze bardziej interesujące może być pytanie, który obszar produkcji ma być w ogóle zautomatyzowany.
Rozbudowa w dwóch sekcjach
Właśnie przed takim pytaniem został postawiony na początku ubiegłego roku Stefan Göppert. W pierwszym etapie budowy rozbudował swoją halę do wymiarów 15 x 35 m, a następnie zainwestował w nowy budynek biurowy. A to po dłuższym okresie ożywienia, któremu założona przed 20 laty firma Elztal Holzhaus GmbH zawdzięcza znaczny rozwój: „W ciągu ostatnich dziesięciu lat podwoiliśmy liczbę produkowanych elementów i obroty, dzięki czemu obecnie jesteśmy przedsiębiorstwem zatrudniającym około 50 pracowników, które buduje około 15 domów jednorodzinnych rocznie”. Sektor budownictwa jedno- i dwurodzinnego stanowi około 70% obrotów przedsiębiorstwa. Ponadto przedsiębiorstwo jest także aktywne w miejskim i rzemieślniczym budownictwie drewnianym (ok. 20%) i jako GU przeprowadza renowacje budynków energetycznych (ok. 10%). Obszar działalności sięga od granicy Szwajcarii po rejon Karlsruhe/Stuttgartu. Współpraca z różnymi architektami pozwala na indywidualne planowanie, co sprawia, że buduje się praktycznie niepowtarzalne obiekty. Konstrukcja zapewniona jest w ramach ekologicznych elementów MHM, BSP lub samodzielnie wytworzonych ram drewnianych. Te ostatnie stanowią największą część (80%). Wszystkie elementy są przewidziane do przygotowania pracy na czterech stanowiskach, co umożliwia zachowanie szczegółów.
Stół do produkcji
Rozwój działalności z pewnością umożliwiłby dalszy wzrost przedsiębiorstwa, ale podstawowa część przedsiębiorstwa zajęła już większość firmowej posesji. Jasne było, że można było zautomatyzować tylko jedną część procesu produkcyjnego. W zasadzie Stefan Göppert odpowiedział już na podstawowe pytanie: Nowa hala była przeznaczona na linie produkcyjne z zakresu prac ciesielskich. Tak by pozostało, gdyby właściciel na początku 2020 roku nie poświęcił czasu na krytyczną analizę procesów produkcyjnych.
„Szybko przyszła mi do głowy myśl, że zatory występują tylko w strefie ręcznej produkcji elementów. To był nasz problem, a nowa maszyna do odwiązywania konstrukcji ciesielskich nie mogła zatem zwiększyć naszej wydajności. Wręcz przeciwnie, spowodowałaby ona jeszcze większe przestoje przy stole produkcyjnym”. W trakcie letniej przerwy w 2020 r., Stefan Göppert rozważał zautomatyzowanie produkcji elementów i kontaktował się z różnymi producentami oraz oglądał urządzenia produkcyjne różnych marek. W listopadzie po rekordowo szybkim procesie decyzyjnym zamówił w firmie WEINMANN Holzbausystemtechnik GmbH w Lonsingen kolejny stół stolarski i WALLTEQ-340. Zainstalowany już w 2015 roku stół montażowy firmy WEINMANN można było bez problemu zintegrować z nową linią.
Stoły do stawiania elementów i dźwig halowy
„Zdecydowałem się na ten most wielofunkcyjny głównie ze względu na wymiennik narzędzi. Za jego pomocą można wymieniać tarcze piły, które podczas przycinania płyt pilśniowych powodują powstawanie niewielkich ilości wiórów”.
W trakcie intensywnych konsultacji z firmą WEINMANN ustalono najlepsze rozmieszczenie stołów stolarskich. Aby optymalnie wykorzystać dostępne miejsce, oba stoły montażowe zostały dodatkowo wyposażone w funkcję ustawiania z ogranicznikiem w odbiciu lustrzanym. Do transportu pośredniego wykorzystywany jest dźwig halowy. „Pozwala to nam na obracanie na wąskiej osi. W ten sposób, mimo ograniczonej przestrzeni, udało nam się zwiększyć nasze moce produkcyjne i poprawić jakość produkcji”.
Bardziej ergonomiczna praca
W celu ułatwienia pracy swoim pracownikom zainwestowano dodatkowo w dwa podnośniki płyt. „Często jesteśmy w ruchu w klasie budynku 4, gdzie na zewnątrz stosuje się poziom ochrony przeciwpożarowej z płyt Fermacell o grubości 15 mm. Ich układanie jest to bardzo obciążająca dla kręgosłupa, chciałem zaoszczędzić tego moim pracownikom. W związku z tym nowa technologia została dobrze przyjęta, zwłaszcza że strefa prac ciesielskich też coś na tym zyskała: „Jeśli dziś układamy i sklejamy płyty Fermacell, to przepływ pracy jest o wiele bardziej płynny niż wcześniej”. Przy stołach produkcyjnych Stefan Göppert świadomie ustawił dwóch starszych pracowników z działu montażowego, „aby utrzymać tych doświadczonych pracowników do czasu przejścia na emeryturę dzięki nowemu interesującemu zadaniu i ergonomicznemu środowisku pracy”.
Około 30% szybciej
W ramach przygotowań do nowych zadań obaj pracownicy pojechali na szkolenie do Lonsingen: „Mogli oni dalej bez przeszkód pracować na nowym stanowisku zaraz po dostarczeniu linii produkcyjnej w czerwcu 2021 roku” – część procesu opieki, w ramach którego cieśla zawsze najlepiej konsultował się i dostarczał dobrych pomysłów wyglądał następująco: „Jak mogliśmy umieścić dźwig, podnośnik płyt i nowy odciąg bez kolizji w niezbyt wysokiej hali”. Również jego wnioski po uruchomieniu są pozytywne: Już dziś widać, że „w produkcji mamy do czynienia z oszczędnością czasu rzędu 30%. W związku z tym mamy jeszcze perspektywy na przyszłość: Dzięki większej liczbie pracowników moglibyśmy znacznie zwiększyć liczbę produkowanych elementów, a przy zoptymalizowanej logistyce również produkować na linii elementy dachowe i stropowe”. Nieco łatwiejsza będzie sytuacja dzięki uproszczeniom w zarządzaniu jakością: „Z jednej strony linia produkcyjna daje nam wyraźny wzrost precyzji, co jest dla nas ważnym powodem inwestowania w automatyzację, a z drugiej strony ułatwi dokumentację dla kontroli przeprowadzanych z zewnątrz, ponieważ wszystkie ważne dane są dostępne automatycznie w maszynie”. W ostatecznym rozrachunku oznacza to wzrost jakości, który jest równie ważny dla wszystkich zleceniodawców. „Właśnie jesteśmy na etapie składania wniosków o większy obiekt w Karlsruhe, nawet była już delegacja, która chciała obejrzeć zakład. Daje to pewność, że zainwestowaliśmy w jakość i wartość naszych produktów”. Perspektywa w Schuttertal jest odpowiednio pozytywna. Stefan Göppert przewiduje wzrost zamówień pomimo trudności związanych z pozyskiwaniem drewna.
Tekst: Dr. Joachim Mohr
„Z jednej strony linia produkcyjna daje nam wyraźny wzrost precyzji, co jest dla nas ważnym powodem inwestowania w automatyzację, a z drugiej strony ułatwia dokumentację dla kontroli przeprowadzanych z zewnątrz, ponieważ wszystkie ważne dane są dostępne automatycznie w maszynie.”Stefan Göppert, prezes firmy Elztal Holzhaus GmbH
Elztal Holzhaus GmbH
Od momentu założenia w 2001 r. rodzinna firma Elztal Holzhaus GmbH zajmuje się wysokiej jakości, produkowanymi na indywidualne zamówienia drewnianymi domami z wykorzystaniem ekologicznych rozwiązań. Stolarnia z siedzibą w Schuttertal-Schweighausen specjalizuje się w budowie „pod klucz” budynków mieszkalnych, komercyjnych i komunalnych. Około 50 pracowników rocznie wytwarza około 15 domów.
Więcej informacji można znaleźć tutaj.