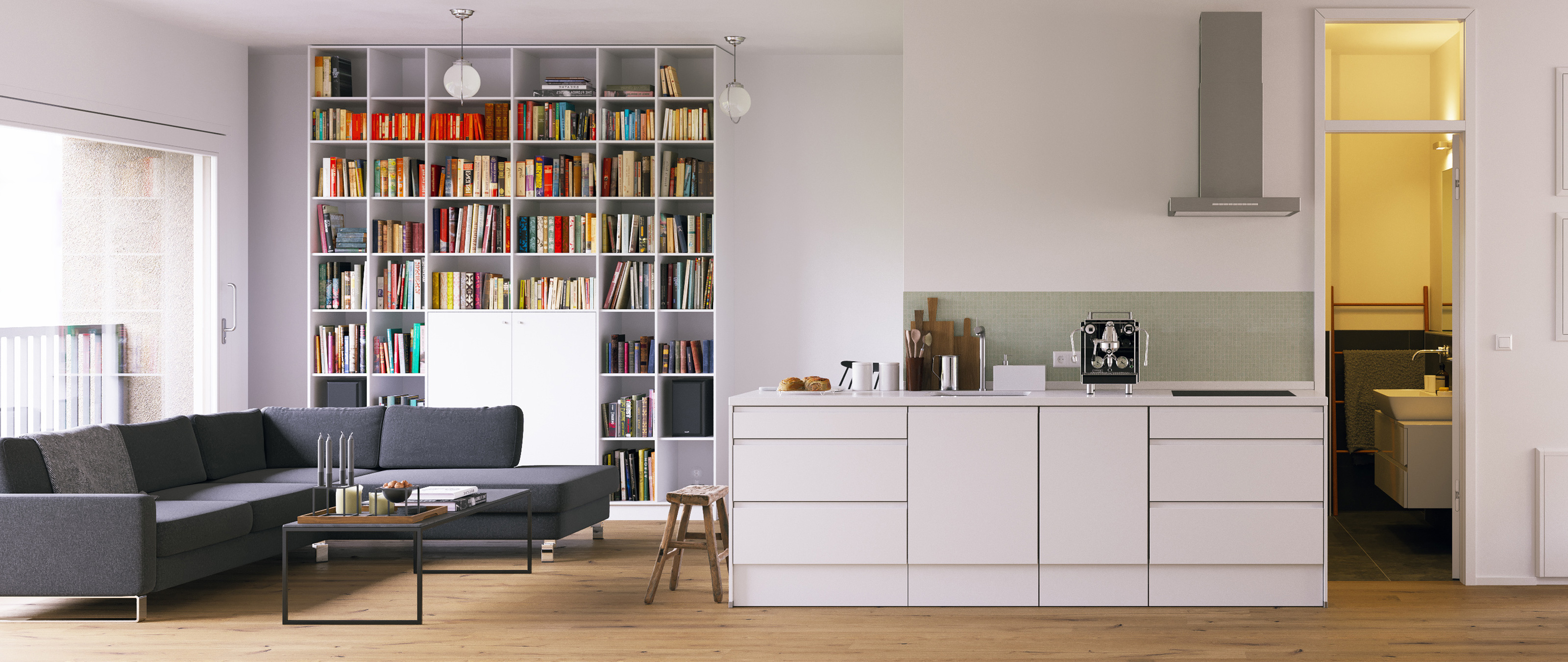
There are three huge trucks parked up there of a kind you will hardly ever catch a glimpse of out on the road.
A walk through the production halls of the coach builder based in Rheinmünster close by Baden Airpark is even more jaw-dropping.
What are produced here are bespoke truck trailers designed for wide-ranging different purposes but all with one thing in common. They are all about creating the greatest possible amount of space and functionality within the confines of the maximum admissible dimensions for road travel: 14 m in length, 2. m in width and 4 m in height. The motor racing world accounts for around 60% of the company’s business, for instance in the form of transport vehicles to accommodate F1 racing cars which include a control center and multifunctional living accommodation for the drivers. The other 40% of the company’s business supplies bespoke vehicles for roadshows, mobile labs, TV broadcasting, equestrian sports teams and also luxury mobile homes. Since May 2012, the interior fittings for the vehicles have been produced using a HOMAG BAZ 322 processing center with DRIVE+ -axis spindle.
"No two customers tick the same ": broad customer spectrum
The impressive aspect of Bischoff + Scheck’s work is that every single component of their vehicles is individually manufactured – right down to the three axles for the chassis. It takes an enormous amount of expertise and sound specific knowledge to address the special needs of customers from wide-ranging different branches of industry. This is why Directors Bernd Bischoff and Volker Scheck see their company’s role neither as that of a classical furniture maker nor as just an auto maker or metalworking firm. As Bernd Bischoff explains: "Most customers come to us with only a vague idea of what they want. There are no two customers who tick the same. We then make suggestions about how their concept could look. We complete the entire project in-house – from planning, through design and production to the completed turn-key vehicle. We have to be extremely flexible, as the needs and expectations of our customers are paramount. And we are also used to customers requesting changes.” From acceptance of order to handover of the finished vehicle generally takes four to five months. Around 2 – 30 completed trucks a year roll out of the factory gates in Rheinmünster – and all of them involve the combined efforts of different trades. Each individual new truck produced is a masterpiece in its own right.
Behind these special products is a special team
The Bischoff + Scheck team comprises around individuals working in the sales and development + design departments, the steelworking and metalworking shops, the chassis construction and vehicle electrics/hydraulics departments. Added to these is a further 2-strong team in the electrical department, who are employed in separate premises by the company’s subsidiary. Another 1 – 20 staff members are only rarely to be seen at the company headquarters: They are on the road tending to the vehicles shipped around the whole of Europe, providing customers with a perfect support service.
"What we provide is an all-round carefree package"
"Alongside the entire project completion from the initial idea through to handover, we offer customers all-round support including a rigging and de-rigging service”, explains Bischoff. “In the Formula One world, for instance, at the start of the season we hand over a ready-to-use vehicle almost every week. Our service team then takes charge of each transfer between races during the season. In practical terms, this means de-rigging after the Belgian Grand Prix in Spa, transferring the vehicles to Monza in Italy, and setting up the vehicle on site ready for the racing team to use when they arrive.” Once we have delivered something to the customer, it has to work. When the season gets under way, there is no time window left for snagging lists or additional modifications.
"Our vehicles are working tools with a great visual impact"
The focus is different for every project and every client. A promotional vehicle clearly has a presentation role to fulfill and also has to comply with certain standards. Other vehicles such as mobile labs or medical units concentrate far more on providing maximum internal functionality. The important thing which applies to every type of vehicle is that it can be moved and set up using a minimum of manpower and that the maximum dimensions for road transport are adhered to. “Our customers see these vehicles first and foremost as a working tool – but one which needs to make a striking impact at the same time. As soon as the vehicle is constructed, there are no end of possibilities. For instance it can be widened, lengthened or extended outwards and upwards", says Bischoff.
Wanted: Efficiency, flexibility, quality
The variety of needs expressed by Bischoff + Scheck customers is matched by the enormous flexibility of the company’s dedicated team. The manufacturing sequence is organized as a parallel process between design and production. Since 2003, the firm has worked in 3D with Autodesk Inventor and the PDM system Productstream. Right from the start, each individual component has been separately designed and attached to its own bill of material. This applies to everything from furniture carcases to steel frames.
This was the reasoning behind investing in the new HOMAG processing center, as Bischoff explains: “We used to outsource a lot of parts, even ordering unique one-off components from joineries. However, this not only restricted our flexibility, it also meant high expenditure on items of only minimal intrinsic value. We only worked with standard joinery machines in our own workshops. The BAZ 322 is actually rather outsized for our premises, but we needed a highly flexible machine capable of covering a wide range of processing operations. We were looking for an all-round solution which would cover all panel component processing operations and deliver complete ready-to-assemble components straight from the machine. We don’t have time for laborious reworking!”, explains Bischoff. "We are always chasing strict deadlines, particularly for our motor racing clients. Efficient working is essential. What we manufacture has to be reproducible!” Alongside achieving flexibility and continuity from design to production and installation, improving and maintaining quality were also key objectives.
With this investment, Bischoff + Scheck has also benefited in another key area: staffing bottlenecks and shortages of skilled labor have always something of an issue in the region around Rheinmünster. Now with the BAZ, the company is able to cover many of the work stages which would otherwise have to be performed by additional specialist workers.
Found: CNC and edge banding in one
Initially Bischoff + Scheck considered purchasing a second-hand -axis machine. At the HOMAG Treff, the coach builders then discovered precisely the machine they had been looking for, which has since changed the complete work flow at Bischoff + Scheck. “We saw the edge banding unit for the processing center at the HOMAG Treff. One thing was clear: This machine would allow us to perform the complete processing sequence we needed for edge banding – as well as panel processing. For us, attaining our long-term objective and maximizing our possibilities are key. The new BAZ simply has greater application scope to offer, which more than justifies the higher investment we had to find for the new machine from HOMAG. We would certainly take this decision again”, says Bischoff.
Wood, aluminum, acrylic? Anything goes with the BAZ!
The new BAZ 322 processing center with -axis spindle DRIVE+ is used to produce all the furniture and elements destined for the interior fittings of these high-tech vehicles. Practically everything is possible in terms of processing. Equipped with powerClamp collet chucks for narrow parts, a 72-slot chain changer, V21 H4 drilling head and camera system, the joinery specialists at Bischoff + Scheck are able to put just about any idea into practice. Maximum flexibility is also offered in terms of the different materials which can be processed. The processing center copes easily with every type of material, from plastic-coated or veneered multiplex panels, solid wood, sandwich materials, plastics, aluminum profiles, acrylic to HPL and many more. Customary chipboard panels never make an appearance in this workshop. At the moment, the Bischoff + Scheck production halls are busy producing a rolling biometric lab for the Fraunhofer Gesellschaft which is destined for use in Africa. It is equipped with a high-security lab for handling highly infections pathogens. Its mission: to combat diseases such as AIDS and tuberculosis locally, where their dissemination is most prolific but where there is little or no existing medical infrastructure available. Dibond aluminum composite panels are used for the internal cladding. These are also processed at Bischoff + Scheck using the BAZ.
Zero CNC experience
When the decision was made in favour of the new machine, none of the team working at Bischoff + Scheck had any experience with CNC – let alone -axis technology or an edge banding unit. “All we did was to send some of our existing team to training courses without any prior experience”, recalls Bischoff. “One of the joiners was moved to the design department, and is now responsible for the woodworking field without the vehicle interiors team. He is not only involved in the design process and drawing up bills of material, but also in the generation and preparation of processing programs”, continues Bischoff.
Another very useful addition is the use of woodMotion. This software allows joiners to simulate the production process from the comfort of the office. In summary: “To date, our experience has been one hundred per cent positive. We have not had any crashes and have produced practically no scrap. Although the time spent in the office has increased, the change has most certainly paid off”, according to Bischoff.
An end to collisions with woodMotion
woodMotion provides a graphic depiction of the workpiece processing operations. The software generates a virtual workpiece reflecting what the machine “would have produced” with the generated program. This allows the programmer to quickly recognize whether it can really be run correctly without problems on the machine. woodMotion works on the basis of a virtual machine simulated on the office computer for CNC control. This means that a real CNC control system is run on the PC which simulates not only pure processing operations but also tool changes, inward and outward movements, and acceleration and braking processes. Even error messages which typically occur only during real operation at the machine can be predicted and displayed in advance. Another benefit is the integrated collision monitoring facility, which detects any collisions between tools, suction cups and consoles during the simulation.
From dream to reality
Bischoff + Scheck offers a practically unique service in its role as complete supplier. As Bischoff explains: “We do not have any comparable competitors in Germany. We offer a unique service in this country. Across the whole of Europe there are only around five companies offering anything comparable – but we are the only ones to offer such a wide and complete spectrum on this scale.” The origins of the company also make for interesting reading. Both Directors have their roots in the special-purpose vehicle and coach building sector: Bischoff on the production side, Scheck specializing in sales. 1 years ago, both dreamt about pursuing a new challenge. “We are passionate about building vehicles to an exemplary standard of quality, and in the motor racing sector particularly the most stringent standards apply. No two vehicles we produce are ever the same. This is a field in which we envisage true scope for further development. We have turned this dream into a reality over a period of 1 years in what we think must be a fairly unique success story”.
Just driving into the yard at Bischoff + Scheck is an amazing experience. There are three huge trucks parked up there of a kind you will hardly ever catch a glimpse of out on the road.
A walk through the production halls of the coach builder based in Rheinmünster close by Baden Airpark is even more jaw-dropping.
What are produced here are bespoke truck trailers designed for wide-ranging different purposes but all with one thing in common. They are all about creating the greatest possible amount of space and functionality within the confines of the maximum admissible dimensions for road travel: 14 m in length, 2. m in width and 4 m in height. The motor racing world accounts for around 60% of the company’s business, for instance in the form of transport vehicles to accommodate F1 racing cars which include a control center and multifunctional living accommodation for the drivers. The other 40% of the company’s business supplies bespoke vehicles for roadshows, mobile labs, TV broadcasting, equestrian sports teams and also luxury mobile homes. Since May 2012, the interior fittings for the vehicles have been produced using a HOMAG BAZ 322 processing center with DRIVE+ -axis spindle.
"No two customers tick the same ": broad customer spectrum
The impressive aspect of Bischoff + Scheck’s work is that every single component of their vehicles is individually manufactured – right down to the three axles for the chassis. It takes an enormous amount of expertise and sound specific knowledge to address the special needs of customers from wide-ranging different branches of industry. This is why Directors Bernd Bischoff and Volker Scheck see their company’s role neither as that of a classical furniture maker nor as just an auto maker or metalworking firm. As Bernd Bischoff explains: "Most customers come to us with only a vague idea of what they want. There are no two customers who tick the same. We then make suggestions about how their concept could look. We complete the entire project in-house – from planning, through design and production to the completed turn-key vehicle. We have to be extremely flexible, as the needs and expectations of our customers are paramount. And we are also used to customers requesting changes.” From acceptance of order to handover of the finished vehicle generally takes four to five months. Around 2 – 30 completed trucks a year roll out of the factory gates in Rheinmünster – and all of them involve the combined efforts of different trades. Each individual new truck produced is a masterpiece in its own right.
Behind these special products is a special team
The Bischoff + Scheck team comprises around individuals working in the sales and development + design departments, the steelworking and metalworking shops, the chassis construction and vehicle electrics/hydraulics departments. Added to these is a further 2-strong team in the electrical department, who are employed in separate premises by the company’s subsidiary. Another 1 – 20 staff members are only rarely to be seen at the company headquarters: They are on the road tending to the vehicles shipped around the whole of Europe, providing customers with a perfect support service.
"What we provide is an all-round carefree package"
"Alongside the entire project completion from the initial idea through to handover, we offer customers all-round support including a rigging and de-rigging service”, explains Bischoff. “In the Formula One world, for instance, at the start of the season we hand over a ready-to-use vehicle almost every week. Our service team then takes charge of each transfer between races during the season. In practical terms, this means de-rigging after the Belgian Grand Prix in Spa, transferring the vehicles to Monza